The Concept Of Magnetic Separation
Magnetic separation is a beneficiation method that uses the difference of mineral magnetism to separate different minerals in a non-uniform magnetic field.
The magnetic separation method is usually used for the beneficiation of metal ores. The use of magnetic separation for non-metallic minerals is to remove magnetic impurities from non-metallic minerals, so as to achieve the purpose of selecting non-metallic minerals.
With the development of high gradient magnetic separation, magnetic fluid beneficiation, superconducting strong magnetic separation, the application of magnetic separation method is more and more in-depth and extensive.
Influence Of Mineral Magnetism On Magnetic Separation Process
Mineral magnetism has a great influence on the magnetic separation process. The magnetic susceptibility of the mineral particles in the magnetic product determines the selection of the magnetic field strength of the magnetic separator (magnetic field or strong magnetic field).
According to the difference of the specific magnetic susceptibility of various minerals, magnetic separation is carried out by magnetic separators with different magnetic field strengths, which are generally divided into three categories: strong magnetic minerals, medium magnetic minerals, weak magnetic minerals.
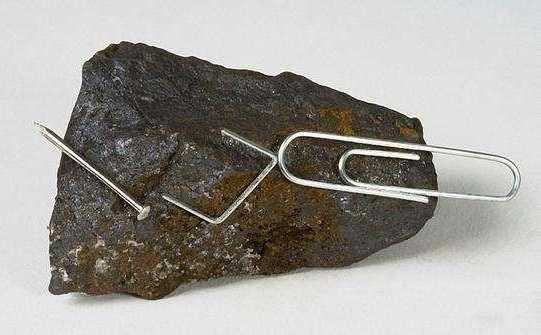
- Strong magnetic minerals, specific magnetic susceptibility greater than 3000×10-9m3/kg · such as magnetite, pyrrhotite, etc., can be effectively separated from gangue minerals by weak magnetic separation equipment.
- Medium magnetic minerals with a specific magnetic susceptibility of 500-3000×10-9m3/kg, such as semi-phantom hematite, some ilmenite, chromite, etc., are separated by medium magnetic field magnetic separation equipment.
- Weak magnetic minerals, with a specific magnetic susceptibility of 15 to 500×10-9m3/kg, such as hematite, limonite, iron carbonate, ferromanganese, hard manganese, rhodochrosite, rutile and some ilmenite, etc. , Recovered by strong magnetic separation and other methods, the specific magnetic susceptibility is less than 15 × 10-6 cm 3 / gram for non-magnetic minerals, such as quartz, feldspar, fluorite and so on.
When fine-grained or fine-grained magnetite or other strong magnetic minerals (such as ferrosilicon, maghemite, and pyrrhotite) enter the magnetic field of the magnetic separator, they form magnetic chains or magnetic beams along the lines of magnetic force. The demagnetization coefficient of a fine flux linkage is much smaller than that of a single particle, while its magnetic susceptibility or magnetic induction is much higher than that of a single particle. The magnetic chain formed in the magnetic field of the magnetic separator has a good effect on the addition and collection of fine magnetic particles, especially during wet separation. This is because the magnetic susceptibility of the magnetic linkage is higher than that of a single magnetic particle. In the direction of the region where the magnetic field is relatively strong, the water medium is favorable for the movement of the magnetic linkage. Still, on the contrary, it is less than the resistance of the single-particle.
Production practice has also proved that magnetite particles rarely appear as single particles during the magnetic separation process, and most of them exist in the form of magnetic chains or magnetic clusters.
The formed magnetic link has an adverse effect on the quality of the magnetic product, because the non-magnetic particles, especially the fine non-magnetic particles, are mixed into the magnetic link and the grade of the magnetic product is lowered.
In the magnetic separation of weak magnetic ores or minerals, in addition to the magnetic susceptibility of the particles, the remanence and coercivity of the particles also play an important role. It is precisely because of their existence that the strong magnetic ores or concentrates that have passed through the magnetic field of the magnetic separator or magnetization equipment often preserve their magnetization after coming out of the magnetic field. As a result, the fine and microfine particles form magnetic clusters or flocs. This property is used in desliming to accelerate the settling of strongly magnetic ore particles. For this purpose, the pulp is magnetized in a special magnetizing device or directly magnetized by a magnetic field in a desliming device (such as a magnetic washing tank) before desliming.
The side effects of magnetic agglomeration not only affect the quality of products, but also in the grinding and classification of intermediate products of magnetic separation. When adopting the separation process in the grinding stage, because a part of the magnetic chain or magnetic agglomerate enters the overflow of the classifier, the classification particle size becomes coarse, which affects the classification effect of the second-stage grinding and classification operation, and reduces the classification index. Therefore, before the second-stage grinding and classification operation, a demagnetization device to destroy the magnetic agglomeration of the pulp should be installed for the ferromagnetic materials (intermediate products) that have previously passed through the magnetic field of the magnetic separation equipment or the magnetization equipment. Demagnetizing the fine magnetic concentrate before filtration can reduce the moisture of the filter cake and improve the processing capacity of the filter.
The small ratio formed when the fine-grained or fine-grained weak magnetic ores or minerals enter the magnetic field of the magnetic separator shall not be lower than 4-5. Below this value, the magnetic product will contain more conjoined organisms. If the magnetic field force distribution of the magnetic separator (groove roll magnetic separator) is more uniform, the weak magnetic ores can be selected under the condition that the ratio of the specific magnetic susceptibility of the separated components is small (2.5 or 3).
When magnetite is oxidized, its magnetism weakens, and the deeper the oxidation, the greater the weakening of magnetism. Magnetite ore with magnetite ratio m Fe / T Fe ≥ 85% can be treated by magnetic separation method, and good separation efficiency can be obtained; mixed ore with m Fe / T Fe = 15% to 85% should be combined with other separation by magnetic separation Method; Hematite ore with m Fe / T Fe ≤ 15% should be treated by magnetic separation combined with other separation methods or single flotation method.