For centuries, jigging has been a workhorse of the mineral processing industry. Recently, it has also found its way into the recycling industry, and the increasing concerns related to water usage has led to a renewed interest in dry jigging. However, the current scenario of increasing ore complexity and the advent of smart sensor technologies, such as sensor-based sorting (SBS), has established increasingly challenging levels for traditional concentration methods, such as jigging.
Against this background, the current review attempts to summarize and refresh the key aspects and concepts about jigging available in the literature. The configuration, operational features, applications, types, and theoretical models of jigging are comprehensively reviewed. Three promising paths for future research are presented:
(1) using and adapting concepts from granular physics in fundamental studies about the stratification phenomena in jigs;
(2) implementing advanced control functions by using machine vision and multivariate data analysis and;
(3) further studies to unlock the potential of dry jigs. Pursuing these and other innovations are becoming increasingly essential to keep the role of jigging as a valuable tool in future industry.
1. Introduction
Jigging is one of the oldest methods of ore treatment and remains one of the workhorses of the mining industry. Until recently, it was, together with dense medium separation (DMS), the main (when not the only) choice for pre-concentration and concentration of coarse-sized ores and coals. Jigging has also currently exceeded the limits of mineral processing, having found applications in different recycling industries, and growing concern related to water usage has led to a renewed interest in the use of dry jigging.
On the other hand, the current scenario of decreasing ore grades and the recent developments in sensor-based sorting (SBS) technologies have established increasingly challenging levels of operational efficiency. With compact installation units, dry operation, and the ability to deal with ores of complex mineralogy, like rare earth bearing minerals, SBS technology has the potential to replace jigs in many of its traditional applications, particularly those involving coarse particle treatment. The scenario is in some ways analogous to the beginning of the 20th century when the advent of magnetic separation and froth flotation partially replaced gravity concentration processes. Breakthroughs and innovations in the understanding, design, and optimization of jigs should be sought in order to keep the technique competitive.
2. Jigging: Concepts and Development
Gravity concentration methods aim to create conditions in which particles of different densities, sizes, and shapes may move relative to each other when under the action of gravity or centrifugal forces, originating multiple bands containing the light and dense materials. When the relative interparticle movement manifests itself in the form of vertical expansions and contractions of a particle bed caused by a pulsing fluid, the gravity concentration operation in question is known as jigging. Although its origin possibly dates back as far as Classical Antiquity, the first remarkable description of jigging appeared only in the 16th century in De Re Metallica, the well-known seminal work by Agricola. In this, the first jigs are depicted as perforated baskets (the “jigging sieve”) containing the mixed ores that were manually and repeatedly dipped into a water tank, after which stratified layers of ore were removed by hand. Until the advent of the industrial revolution, modifications in jigging devices were limited to a little more than the inclusion of levers for using larger baskets. The emergence of hydraulic systems like the piston pump and the plunger pump, with or without seals, are regarded as decisive for the introduction of mechanically pulsated jigs, giving rise to the basic configuration of modern jigs.
Hydraulic Jigs
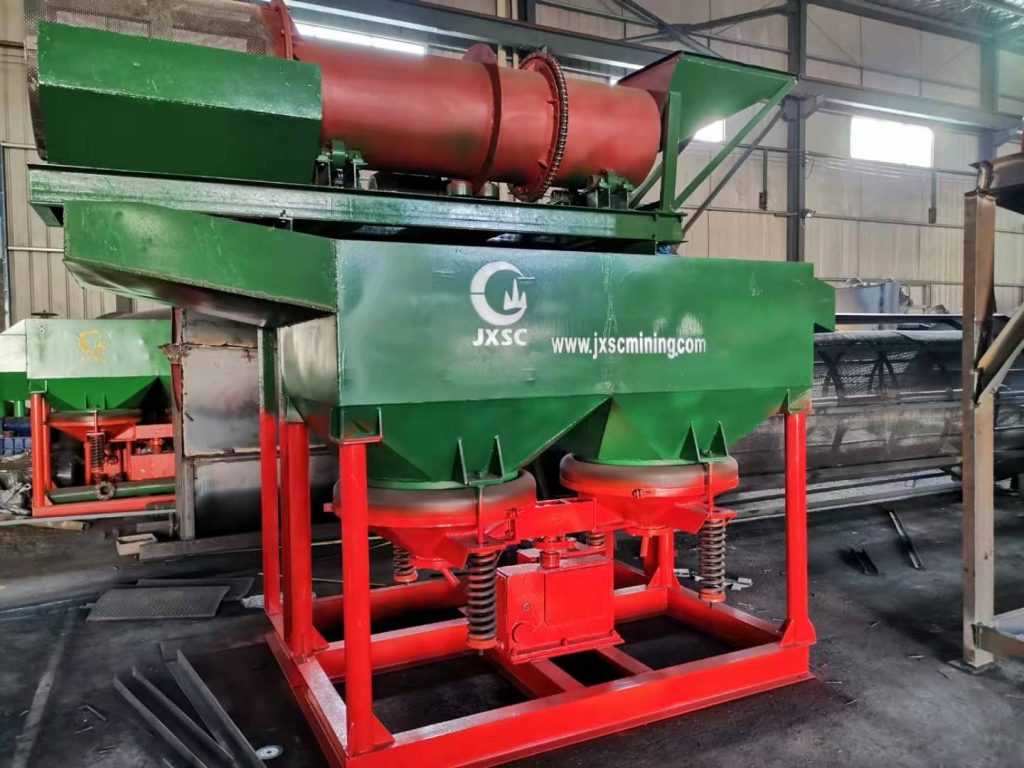
In modern water jigs, the original basket was replaced by a compartmentalized vessel equipped with a sieve (or screen) to support the particle bed, mechanical pulsation devices were introduced, and operation became continuous. The general scheme of most industrial jigs consists of a container divided into two compartments, one of them corresponding to the separation chamber where feed particles are located on a supporting sieve and through which the water performs its oscillatory motion. The other compartment contains the mechanism that drives fluid pulsation responsible for moving the bed during its passage by the jig. The pulse wave can be produced either mechanically through a plunger or by the pulsation of water or air that is intermittently fed into the jig vessel by using a special valve. In some types of jig, the relative motion between particles and water is obtained through the vertical displacement of the supporting sieve.