The hammer head is one of the core components of the hammer crusher. It is arranged on the hammer shaft of the crusher rotor to hit the material to crush it.
It should to choose the most suitable hammer crusher head according to the different types of crushed materials. The following first briefly introduces the characteristics and classification of the hammer heads.
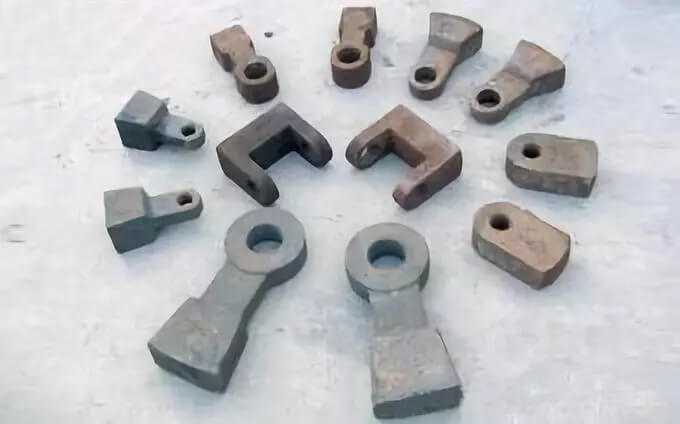
How many types of hammer head?
1. Forged hammer
Forged crusher hammer head is suitable for crushing pebbles, coal gangue, limestone, etc. The hammer head of the forging crusher adopts high-quality train wheel steel material (65Mn, good impact resistance, strong toughness, good wear resistance, not easy to break)
The metal blank is repeatedly forged by forging machinery to deform it to obtain a certain mechanical performance, certain shape and size, and then undergo a special quenching heat treatment method to ensure that the hammer head’s working area has high hardness and high wear resistance.
Forging can eliminate defects such as as-cast looseness during metal smelting and optimize the microstructure. At the same time, due to the preservation of complete metal flow lines, the mechanical properties of forgings are generally better than castings. Forged hammers are favored by users because of their low price, economy and durability.
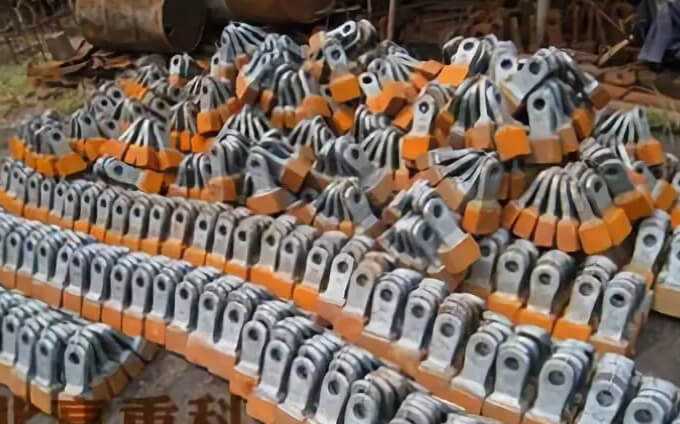
2. High manganese steel hammer head
Alloyed high manganese steel wear-resistant hammer, reliable quality, wear resistance is three times that of traditional high manganese steel. The hammer head of this crusher is widely used in the large-scale limestone crusher supporting the domestic new dry cement production line. With the continuous development of wear-resistant materials, high manganese steel has gradually become unsuitable for the development of modern foundry industry.
It is replaced by chromium-molybdenum alloy steel, high chromium cast iron and nickel hard cast iron. But the high toughness of high manganese steel is unmatched by other wear-resistant materials. High manganese steel crusher hammer head has good toughness, good manufacturability and low price. Its main feature is that under the action of greater impact or contact stress, the surface layer will quickly produce work hardening, and its work hardening index is 5 higher than other materials 5-7 times, the wear resistance is greatly improved.
However, the hammer head of the high manganese steel crusher has higher requirements for the overall performance of the crusher. If the physical impact force is not enough or the contact stress is small in actual work, the surface cannot be quickly worked hardened, so that the wear resistance cannot be exerted. Sex. Therefore, it is hoped that customers should choose according to the actual parameters of the equipment before use, and if necessary, the equipment can be modified to maximize economic benefits.
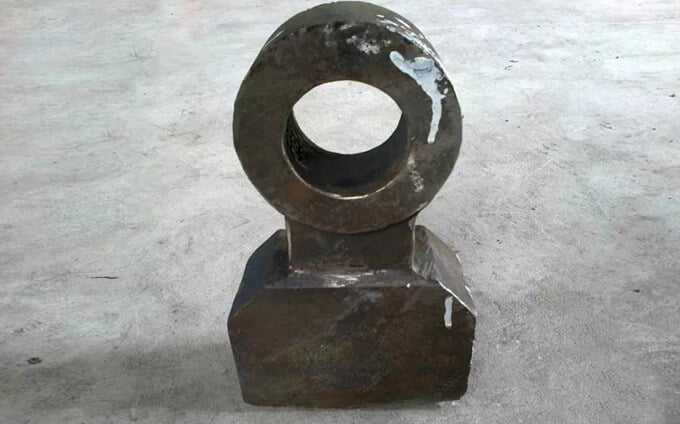
3. High chromium alloy hammer head
The high chromium alloy crusher has excellent hammer head hardness and is a high-quality wear-resistant material. It has been widely used in the third generation of sand making machines and impact crushers. However, the high chromium alloy has poor toughness. In this case, it is prone to breakage. High chromium composite hammer head, that is, the hammer handle uses high manganese steel, and the hammer head working area uses high chromium alloy. The two are combined, so that the hammer head has high hardness, and the hammer handle has high toughness. The advantages of the materials overcome the shortcomings of a single material and meet the performance requirements of the hammer. Especially suitable for crushing high hardness materials, such as quartz stone, basalt, etc. However, the traditional manufacturing process is complicated, the process requirements are stricter, and the price is higher.
4. Hard alloy hammer
Compared with other materials, cemented carbide hammers have higher hardness, bending strength and impact, thermal fatigue resistance, good thermal hardness, and low cost. It solves the cracks, desoldering and collapse of high manganese materials. Problems such as mouth, falling blocks, etc.
1. Ultra-high wear resistance, more than 20 times that of high manganese steel hammers.
2. It has good resistance to mechanical shock and thermal shock.
3. It has a wide range of applications and can basically be adapted to all crushing industries.
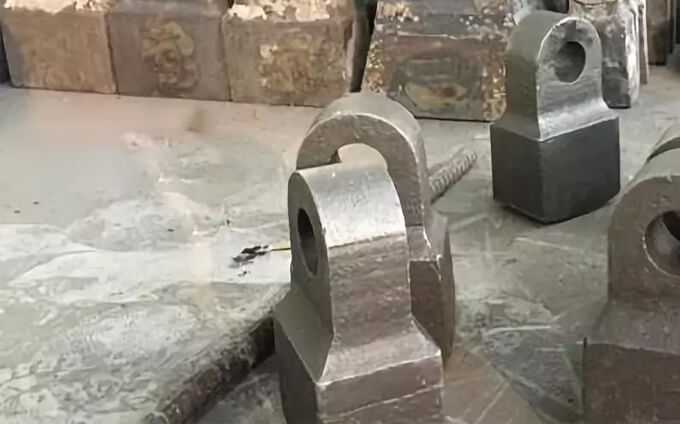
5. Bimetallic hammer head
The hammer head of the crusher which is poured by two different metal liquids is a bimetal hammer head. The bimetal hammer head ensures the toughness of the hammer handle part, and the hammer head part also has hardness and wear resistance.
The temperature of the bimetal hammer head during quenching is very important. Generally, the appropriate quenching temperature is selected according to the thickness of the part wall. The higher the quenching temperature, the higher the hardenability. Therefore, a reasonable setting must be made in the production of the hammer head casting and heat treatment process.
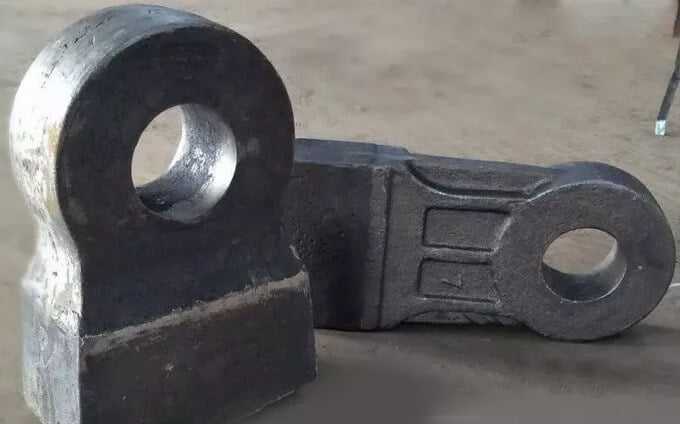