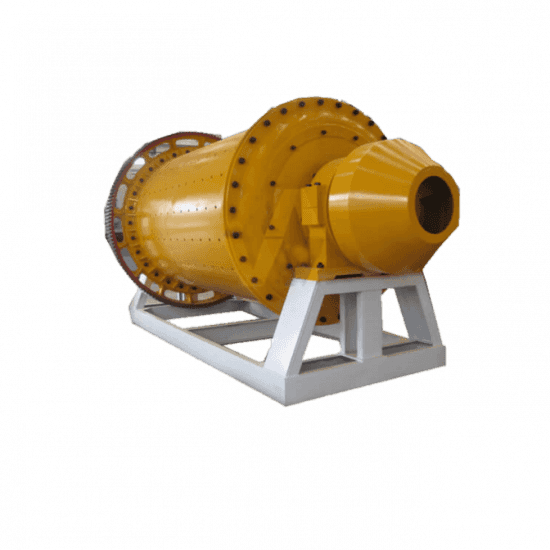
Ball Mill
ball mills designed for long life and minimum maintenance. grinding ores and other materials typically to 35 mesh or finer in a variety of applications, both in open or closed circuits.
product hightlightOur grinding ball mill features and advantages
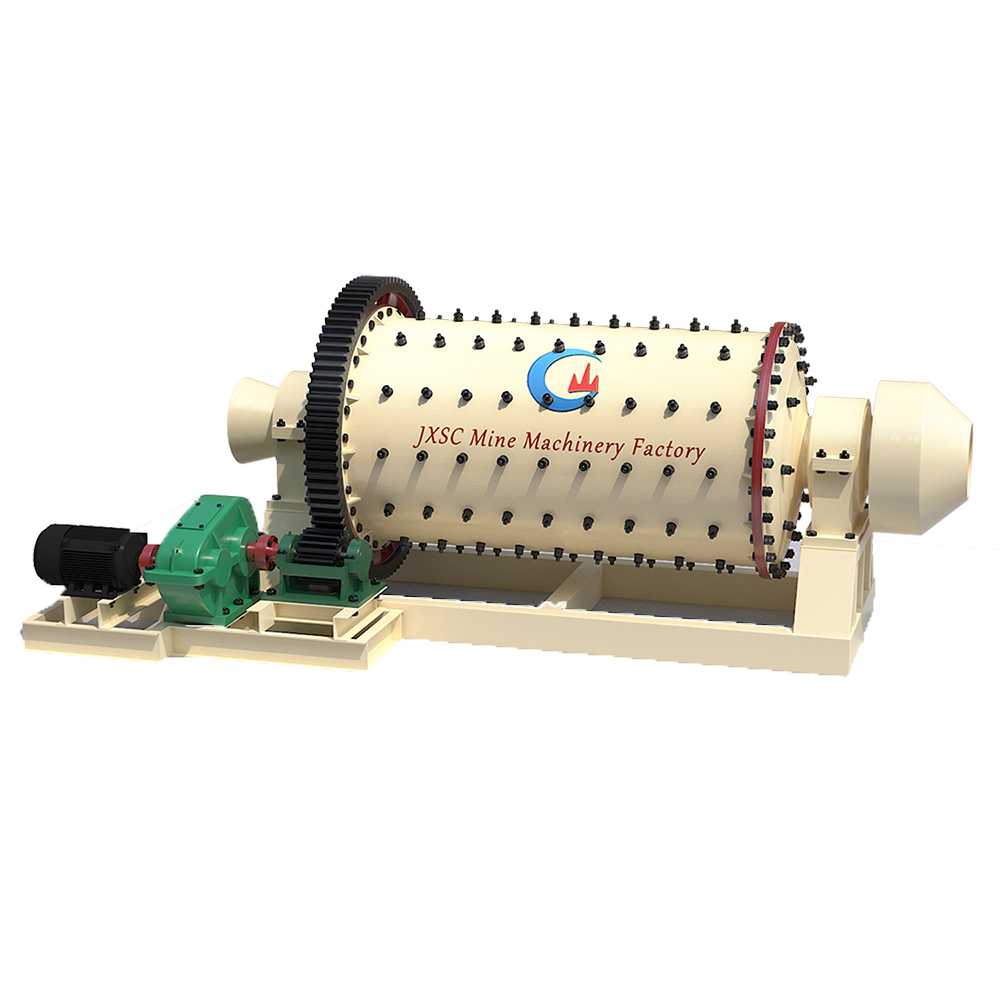
Feature 01Long life and minimum maintenance
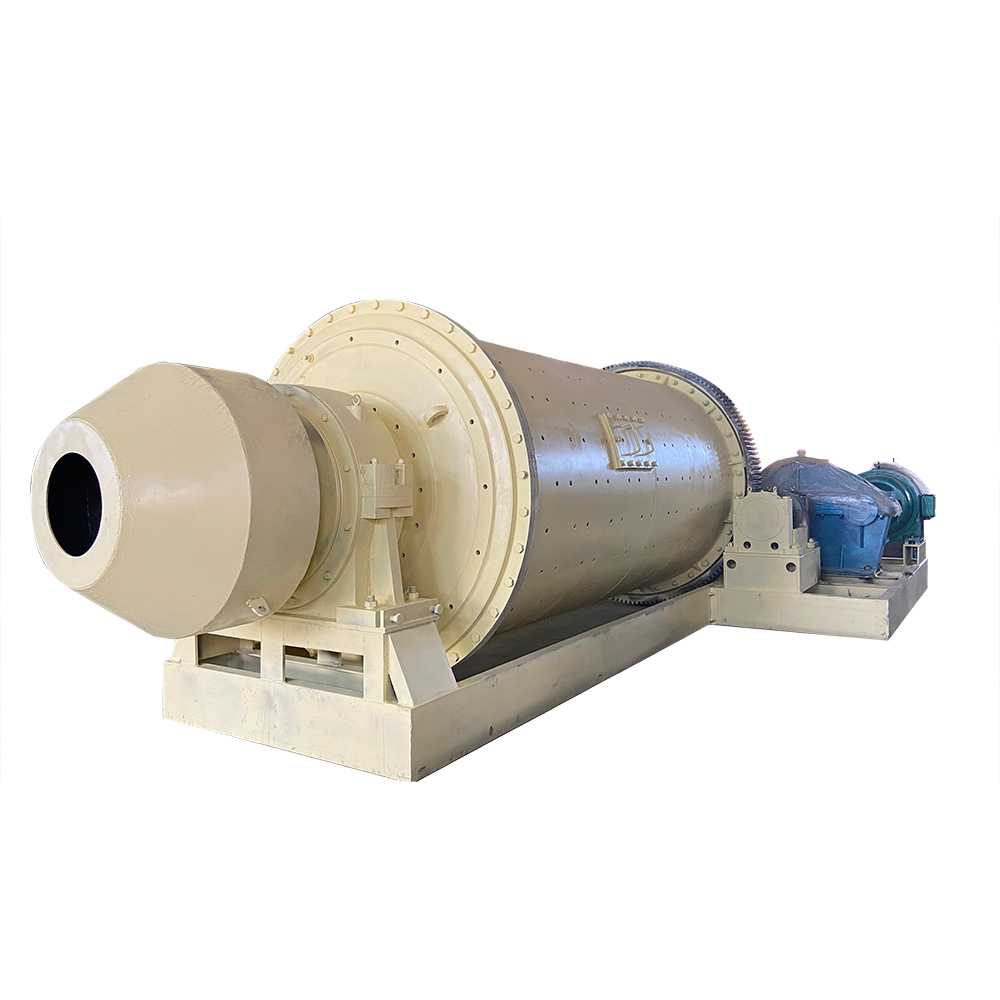
Feature 02High efficiency and energy saving
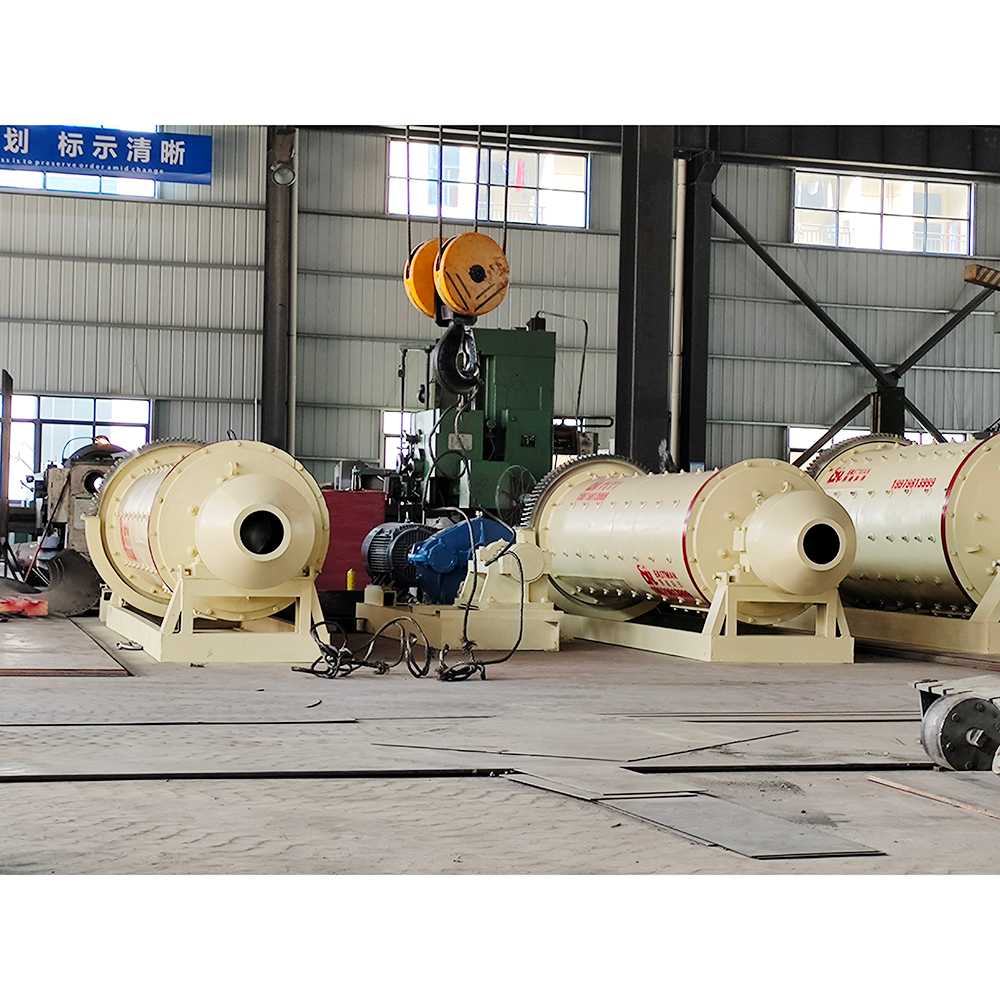
Feature 03Big grinding processing capacity
Products display
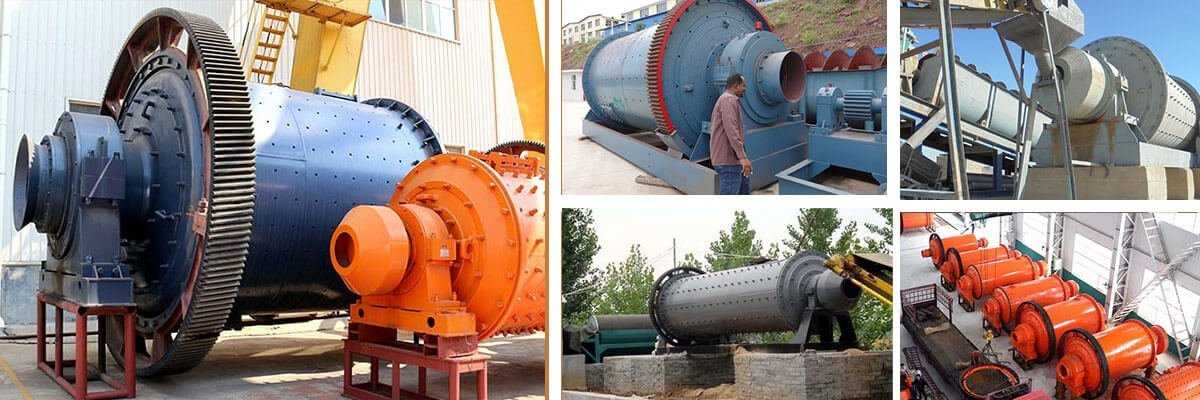
Overview
The ball mill is a tumbling mill that uses steel balls as grinding media. Ball mills can be used in wet or dry systems for bulk and continuous milling, and are most widely used in small or large-scale beneficiation plant.
The feed can be dry with a water content of less than 3% to minimize the coverage of the ball, or it can be a slurry with a water content of 20-40%. The ball mill can be used for primary or secondary grinding applications. In the primary application, they receive feed from the crusher, and in the secondary application, they receive feed from the rod mill, autogenous mill or semi-autogenous mill.
working principle
Main parts
The mill includes motor, reducer, slow drive, power distribution control cabinet, feeding device, main bearing, rotary part, discharging device, transmission part, lubrication system (mainly including high-pressure pump station and low-pressure thin oil station) and other parts.
The main working part of the ball mill is a rotary cylinder mounted on two large bearings and placed horizontally. The cylinder body is divided into several compartments by a partition plate, and a certain shape and size of grinding body is installed in each compartment. The grinding bodies are generally steel balls, steel forgings, steel rods, pebbles, gravel and porcelain balls. In order to prevent the barrel from being worn, a liner is installed on the wall of the barrel. The length of a cylindrical shell is usually 1–1.5 times the diameter of the shell.
The grinding elements including grinding media and material in the ball mill move at different speeds. Therefore, the collision force, direction and kinetic energy between two or more elements vary greatly in the ball charge. Friction and wear or friction and collision energy all act on the particles. These forces come from the rotating motion of the ball and the particle motion in the mill and the contact area of the collision ball.
specifications
Model | Shell rotation speed (r/min) | Ball load (t) | Feeding size (mm) | Discharging size (mm) | Capacity (t/h) | Motor power (kw) | Weight (t) |
Ø 900*1800 | 36-38 | 1.5 | < =20 | 0.075-0.89 | 0.65-2 | 18.5 | 4.6 |
Ø 900*3000 | 36 | 2.7 | < =20 | 0.075-0.89 | 1.1-3.5 | 22 | 5.6 |
Ø 1200*2400 | 36 | 3 | < =25 | 0.075-0.6 | 1.5-4.8 | 30 | 12 |
Ø 1200*3000 | 36 | 3.5 | < =25 | 0.074-0.4 | 1.6-5 | 37 | 12.8 |
Ø 1200*4500 | 32.4 | 5 | < =25 | 0.074-0.4 | 1.6-5.8 | 55 | 13.8 |
Ø 1500*3000 | 29.7 | 7.5 | < =25 | 0.074-0.4 | 2.0-5.0 | 75 | 15.6 |
Ø 1500*4500 | 27 | 11 | < =25 | 0.074-0.4 | 3.0-5.0 | 110 | 21 |
Ø 1500*5700 | 28 | 12 | < =25 | 0.074-0.4 | 3.5-6 | 130 | 24.7 |
Ø 1830*3000 | 25.4 | 11 | < =25 | 0.074-0.4 | 4.0-10.0 | 130 | 28 |
Ø 1830*4500 | 25.4 | 15 | < =25 | 0.074-0.4 | 4.5-12 | 155 | 32 |
Ø 1830*6400 | 24.1 | 21 | < =25 | 0.074-0.4 | 6.5-15 | 210 | 34 |
Ø 1830*7000 | 24.1 | 23 | < =25 | 0.074-0.4 | 7.5-17 | 245 | 36 |
Ø 2100*3000 | 23.7 | 15 | < =25 | 0.074-0.4 | 6.5-36 | 155 | 34 |
Ø 2100*4500 | 23.7 | 24 | < =25 | 0.074-0.4 | 8-43 | 245 | 42 |
Ø 2100*7000 | 23.7 | 26 | < =25 | 0.074-0.4 | 8-48 | 280 | 50 |
Ø 2200*4500 | 21.5 | 27 | < =25 | 0.074-0.4 | 9-45 | 280 | 48.5 |
Ø 2200*6500 | 21.7 | 35 | < =25 | 0.074-0.4 | 14-26 | 380 | 52.8 |
Ø 2200*7000 | 21.7 | 35 | < =25 | 0.074-0.4 | 15-28 | 380 | 54 |
Ø 2200*7500 | 21.7 | 35 | < =25 | 0.074-0.4 | 15-30 | 380 | 56 |
Ø 2400*3000 | 21 | 23 | < =25 | 0.074-0.4 | 7-50 | 245 | 54 |
Ø 2400*4500 | 21 | 30 | < =25 | 0.074-0.4 | 8.5-60 | 320 | 65 |
Ø 2700*4000 | 20.7 | 40 | < =25 | 0.074-0.4 | 12-80 | 400 | 94 |
Ø 2700*4500 | 20.7 | 48 | < =25 | 0.074-0.4 | 12-90 | 430 | 102 |
Ø 3200*4500 | 18 | 65 | < =25 | 0.074-0.4 | —– | 800 | 137 |
Talk with JXSC’s mining experts to get more help, fell free to conslution!
Structure

Replacement
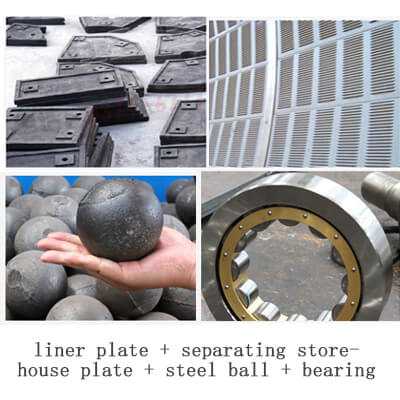
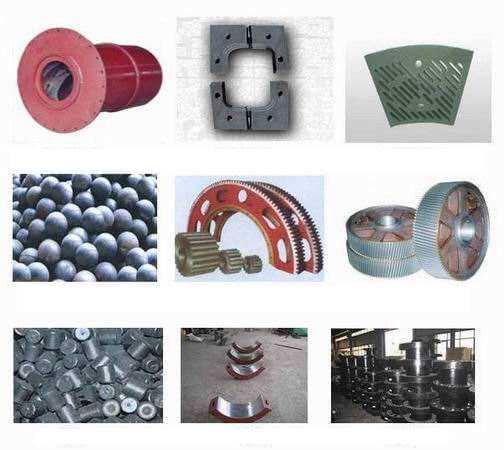
Features
- High chromium cast ball
High chromium cast ball is an alloy white cast iron ball with high chromium content (more than 10% Cr), which is wear-resistant, heat-resistant and corrosion-resistant, and has considerable toughness. The martensitic matrix high-chromium cast iron ball surface hardness HRC can reach 58-66
. The wear resistance of high chromium cast iron balls is 8 to 12
times that of ordinary carbon steel balls
- Liner plate
The cylinder is lined with high-manganese steel lining and multi-element alloy wear-resistant lining, which has good impact resistance and wear resistance.
- Wide applicability and high capacity
- Maintain a certain capacity for a long time to achieve the durability of the specified grinding fineness (add balls regularly to compensate for its wear)
- Reliability and safety, easy maintenance.
- The machine runs smoothly and works reliably. The internal structure can be adjusted according to customer requirements.
- Suitable for batch grinding, continuous grinding, open circuit grinding and closed circuit grinding, suitable for all kinds of hardness materials.