Electrostatic Separator
Capacity: 1-2T/H
Feeding: 0.1-3mm
Uses: magnetite, ilmenite, rutile, monazite, zircon, etc
product display
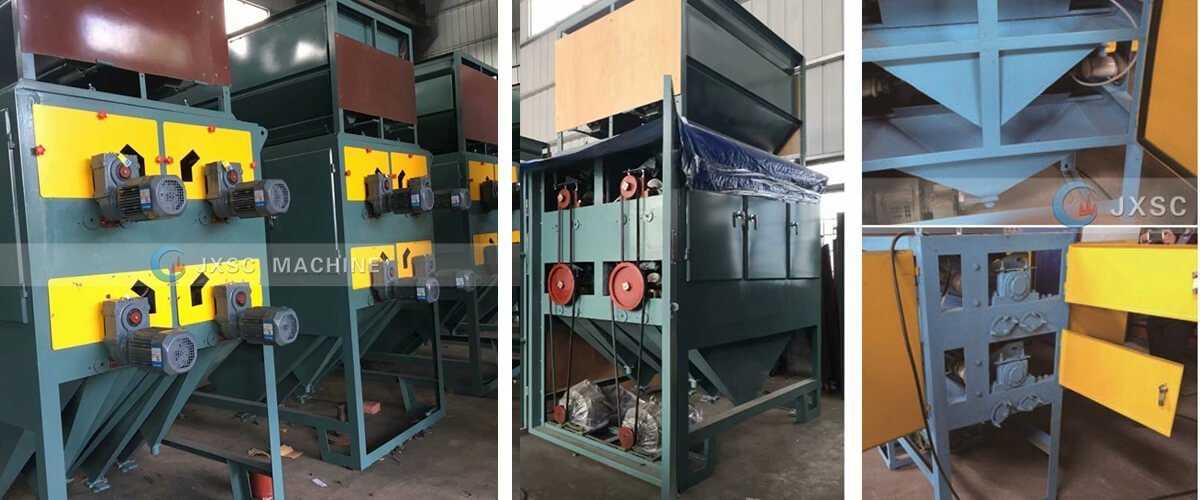
Overview
Electrical separation is a physical beneficiation method that utilizes the different electrical properties of various minerals and materials for separation. The commonly used electrical separation equipment is a drum-type electrical separation machine.
https://www.youtube.com/watch?v=kac-rcHPzcI
The most suitable granularity of the selected materials for the drum-type electric separator is 0.1-1mm. The selected materials need to be dried, because moisture will reduce or disappear the electrical difference between conductor and non-conductor minerals. The nature of the selected materials is different, and the conditions for electrical selection should also change accordingly. Therefore, in actual production, the voltage, motor position, drum speed, and ore plate position should be adjusted at any time.
models & specifications
Technical parameter Structure Application Technical parameter
Structure
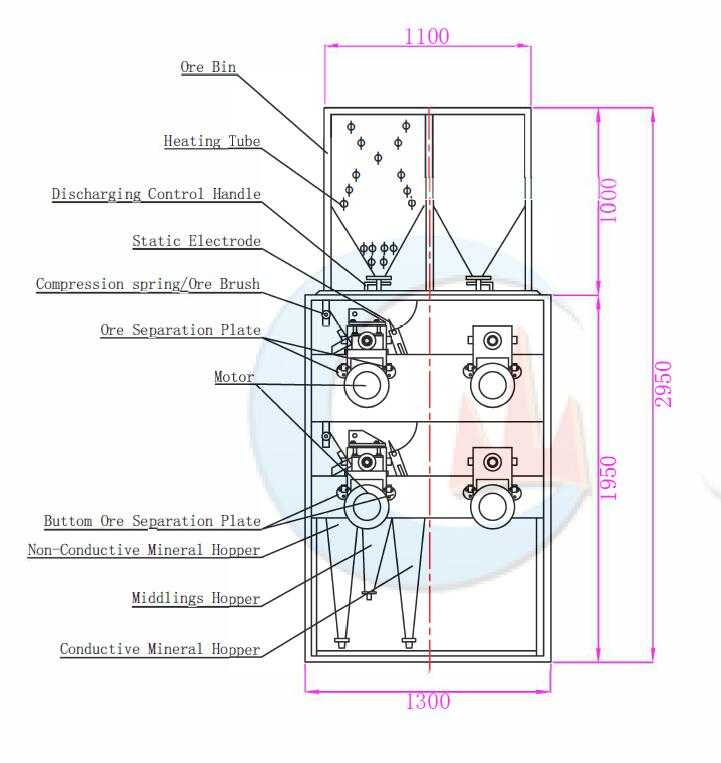
Application
At present, electrical selection is widely used in the following areas:
1. Sorting of non-ferrous and rare metal minerals
These two types of minerals are often firstly subjected to gravity separation or other beneficiation methods to remove a large amount of gangue minerals or surrounding rocks to obtain a certain grade of coarse concentrate, which is then selected by electric separation or in combination with magnetic separation to make useful minerals are separated from each other.
Such as the separation of white tungsten and cassiterite;
After the gravity sorting of seashore ore or land sand ore, different heavy minerals such as magnetite, ilmenite, rutile, monazite, zircon, and phosphorite are sorted;
Separation of tantalum-niobium ore and garnet, tourmaline, quartz, feldspar, mica, etc.
2. Sorting of ferrous metal ore
A small number of iron ore, manganese ore and chromium ore directly use electrical separation, most of which are only used in the concentrating process. Electric separation has a special effect on the removal of silicate minerals (such as quartz, etc.) from iron concentrate, manganese ore and chrome ore.
After the separation of these ores, an additional stage of electrical separation is carried out for beneficiation, which not only can further improve the grade of concentrates, but also greatly reduce the content of silica, which will reduce the coke ratio in iron making, save energy, and improve the blast furnace.
3. Selection of placer gold
Placer gold is also gravity separated to obtain heavy minerals, usually including gold, magnetite, ilmenite, and a small amount of quartz, etc. This heavy mineral is combined with magnetic separation and electrical separation for selection. When magnetic separation is used to remove magnetic minerals, and then electrical separation is used to select gold, gold concentrate with high grade and high enrichment ratio can be obtained, which is much superior to the general beneficiation method or mercury mixing method.
4. Sorting of non-metallic minerals
Such minerals include graphite, asbestos, diamond, apatite, coal, potassium salts, quartz and feldspar.
5. Classification of various solid materials
Including all kinds of metals and non-metals and other solid materials, in industrially developed countries, the particle size requirements of chemical raw materials, coatings, metal powders and corundum powders in metallurgy are very strict, when these materials can not use the wet classification method, electric classification has become the most feasible method, and can overcome a series of difficulties caused by wet classification and save the necessary series of concentration, filtration and drying equipment.
6. Recovery of non-ferrous metals from various solid materials or waste materials
Recovery of non-ferrous metals from various types of cutting waste and plastics; recovery of coal and spherical particles and fly ash of aluminosilicate produced in combustion from coal-fired power plants and other chimney ash.
Application & solution
The jaw crusher is usually used as the primary crusher which is fed with blasted rock material. The main crusher must have a large inlet opening because the size of the blasted material can vary greatly. The secondary crusher is usually cone crusher or gyratory crusher, and the third and final crushers are mainly cone crushers. In cases where very high cubicity is required, if the rock is particularly difficult to form, the final crusher may become an impact crusher.