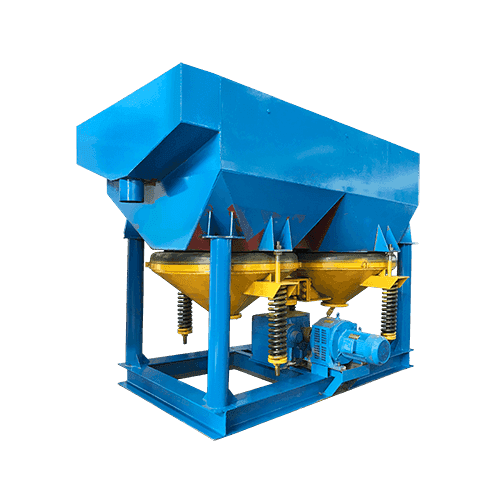
Mineral Jig Concentrator
The mineral jig has been widely used in recovering valuable heavy minerals such as gold, platinum, tin, tungsten and lower density minerals, gemstones such as diamond and sapphire from alluvial or placer deposits. Jigs have also been widely used in hardrock mill applications for recovering of coarse heavy minerals liberated in open or closed grinding circuits.
Feeding: 2~18mm
Capacity: 1-20 TPH
Application: alluvial gold, coltan,tin, etc
The mineral jig has been widely used in recovering valuable heavy minerals such as gold, platinum, tin, tungsten and lower density minerals, gemstones such as diamond and sapphire from alluvial or placer deposits. Jigs have also been widely used in hardrock mill applications for recovering of coarse heavy minerals liberated in open or closed grinding circuits.
Products display
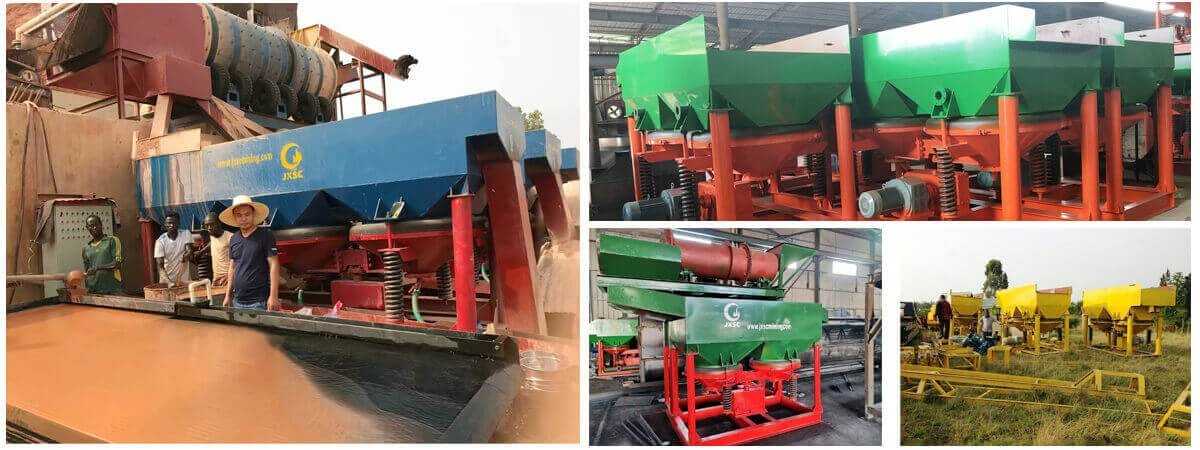
Overview
A jig is a device that drives pulses of water upwards through a thick bed of settled sediment in order to keep it loose and agitated. This achieves gravitational separation by allowing the denser minerals to sink easily and quickly through the lighter minerals. A typical jig consists of a water-filled tank known as a jig-cell, with a horizontal jig screen (‘mesh’) near the top, upon which sediment is able to settle as the jig bed. Pulses of water are injected from below, through the jig screen. Each pulse causes the jig bed to be watercharged, loose and agitated, permitting denser minerals to fall to the bottom of the jig bed. The jig screen traps gold nuggets, but the smaller gold falls through the jig screen and to the bottom of the hutch (water tank) to accumulate as a concentrate. The concentrate is bled off continuously through a spigot (‘tap’) in the base of the hutch, as shown below:
A feature of jigs is that the composition of the jig bed can be carefully designed by placing a layer of coarse dense particles known as ‘ragging’ on the jig screen. These may include steel balls or a suitable heavy mineral such as hematite Fe2O3. By this means, only very dense grains will penetrate through the ragging and fall through the jig-screen. Grains of lower density (e.g. quartz SiO2
) above the ragging.
models & specifications
Model | Jig Area (m2) | Stroke (R/Min) | Feeding size (mm) | Hutch Water ( T/H) | Pressure Water (kg/cm2) | Capacity;(T/H) | Power;(KW) | Overall dimensions (mm) | Weight (T) |
---|---|---|---|---|---|---|---|---|---|
JT0.57-1 | 0.57 | 60-160 | <6 | 1-2 | ≥0.3 | 1-2.5 | 1.5 | 1560x820x1550 | 0.612 |
JT1-1 | 1.04 | 60-160 | <10 | 2-3 | ≥0.3 | 4-10 | 2.2 | 1322x1190x1915 | 0.9 |
JT2-2 | 2.28 | 60-160 | <10 | 2-4 | ≥0.3 | 8-15 | 3 | 3225x1550x2150 | 1.637 |
JT4-2 | 4 | 50-125 | <10 | 4-8 | ≥0.1 | 8-16 | 7.5 | 4240x1990x2750 | 4.6 |
JT4-2A | 4 | 50-125 | <10 | 4-8 | ≥0.1 | 8-16 | 8 | 4240x1990x2750 | 4.6 |
JT5-2 | 4.86 | 80-120 | <10 | 4-10 | ≥0.1 | 10-20 | 7.5 | 3940x2006x2580 | 4.6 |
Replacement
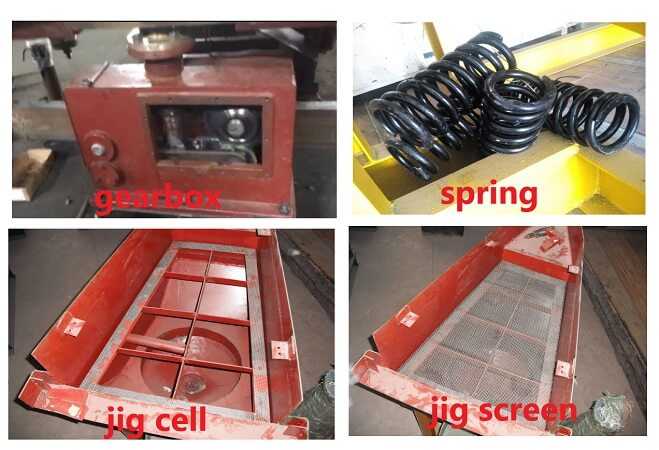
Structure
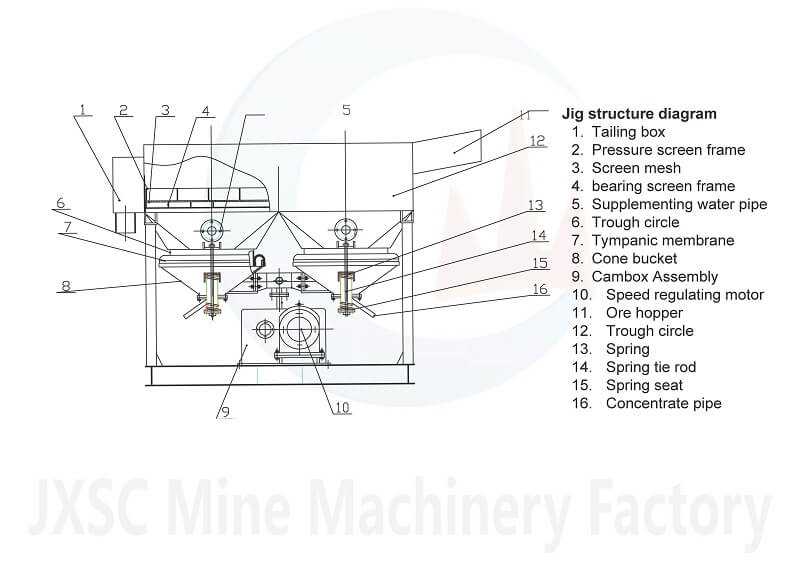
Features
• Low water consumption when compared with most centrifugal concentrators.
• A high degree of recoveries – recover 0.5% to 30% concentrate, increasing recovery rate.
• Wide feed and particle size recovery – feed size up to 30mm, which reduces the step of prescreening the feed. Improve the potential for gravity recovery and avoid excessive grinding
• efficient – low operating costs, low water consumption.