Wet Pan Mill
Capacity: 0.5-6t/h
Feeding: <30mm
Discharge: 0.074-0.6mm
Products display
Overview
The wet mill is the full name of the wet pan grinding mill. According to the different applications, it is divided into the gold mill, amalgam mill, iron mill, and electric mill;
According to the different structure, it is divided into single pan mill, double pan mill and three pan mill.
It is used for grinding operations of various ferrous metals, non-ferrous metals and non-metallic minerals, as well as grinding, beneficiation and processing operations of rare and precious metals gold and silver. Wet pan mill is the optimal first grinding equipment for the majority of small-scale beneficiation plants, alternative equipment for ball mills.
https://www.youtube.com/watch?v=ryVR1et6gHM
Working principle
The electric motor transmits the power to the reducer. Under the drive of the reducer, the rolling wheel obtains the driving force and rotates counterclockwise along the horizontal direction of the horizontal axis.
The added ore material is subjected to squeezing force from the weight of the wheel in the mill, and the huge friction force generated by the wheel during rotation and rotation of the wheel and the grinding disc is completely crushed after repeated extrusion, kneading and grinding.
specifications
Parameter Replacement Structure Parameter
Replacement
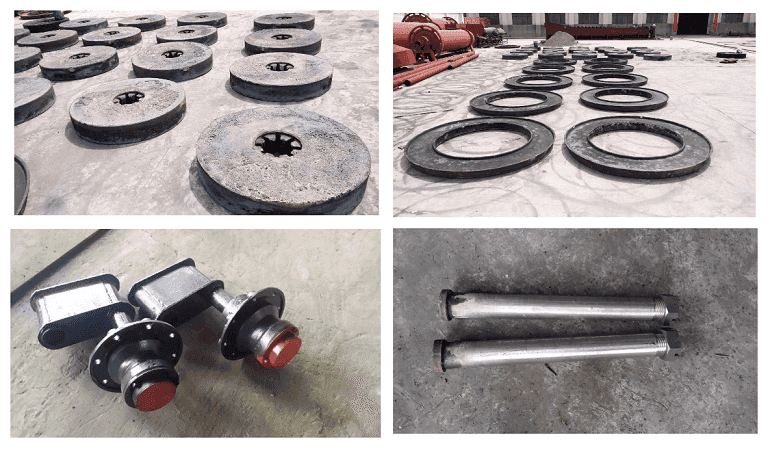
Structure
The equipment is mainly composed of power plant, frame, water basin, rolling wheel, rolling plate and other components.
After grinding and crushing, the monomers dissociate the fine mineral particles, and are brought to the upper surface of the liquid in the mixed slurry, and are discharged through the overflow discharge port provided on the water basin to enter the next process.
Coarse-grained minerals are settled on the bottom of the grinding disc, and continue grinding and crushing until the fineness reaches the standard.
The sieve installed at the discharge port of the water basin can strictly control the classification particle size to avoid the phenomenon of excessive crushing of minerals or uneven particle size, and create good conditions for subsequent operations.
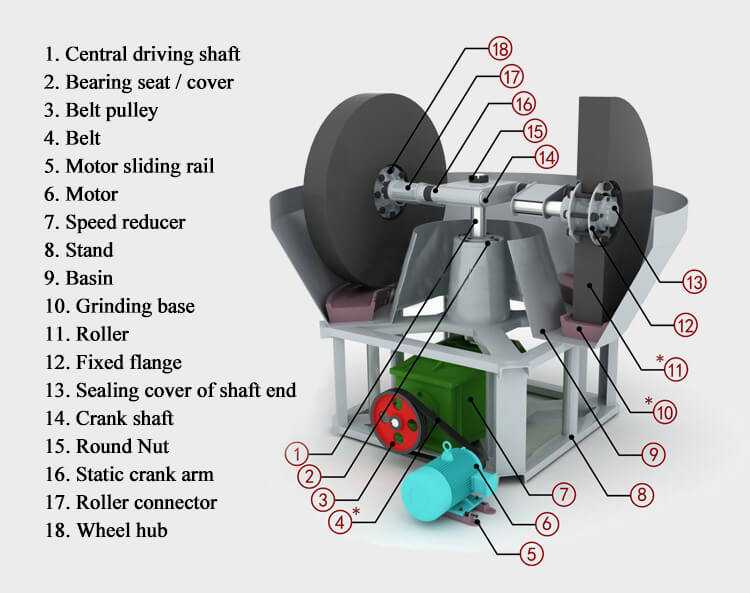
Why Choose US
JXSC Wet Pan Mill VS Other Pan Mills
#1 Roller and Base
JXSC
1. Good raw materiel (Mn,Iron).
2. Weight reach 1.5 t each (wheel), 1.2t (base)
3. No sand holes.
4. Smooth surface.
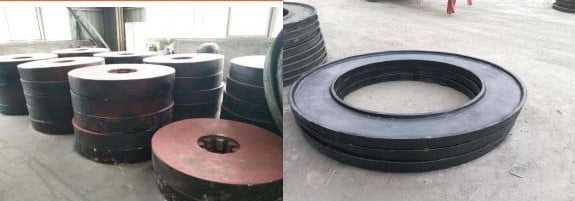
Others
1. Low-quality raw material.
2. Many sand holes which lead to mercury and
gold missing.
3. Low working efficiency.
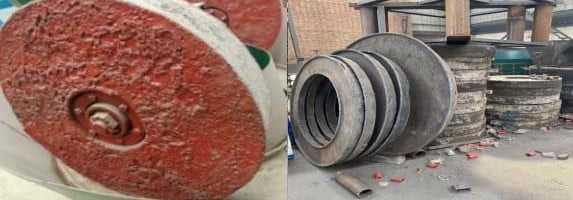
#2 Basin
JXSC
1. Thickness: National standard 6mm.
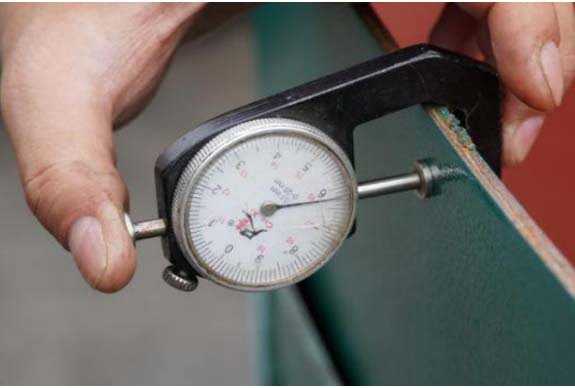
Others
1. Thickness:3mm
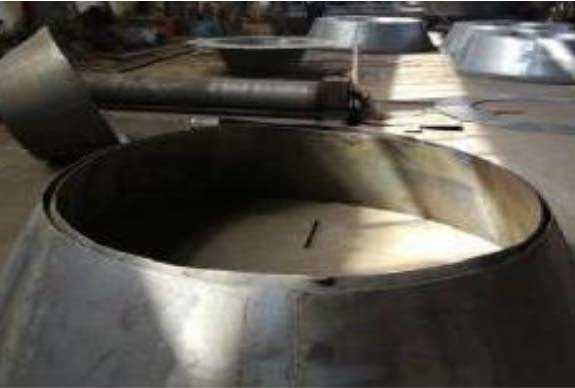
#3 Welding
JXSC
1. Carbon dioxide arc welding:Double-side welding can get through parent metal easily and increase intensity, no slurry leak age from the joint;
2. Electric-charge able liquid helps avoid iron liquid scattering around when welding and makes the outlook perfect.
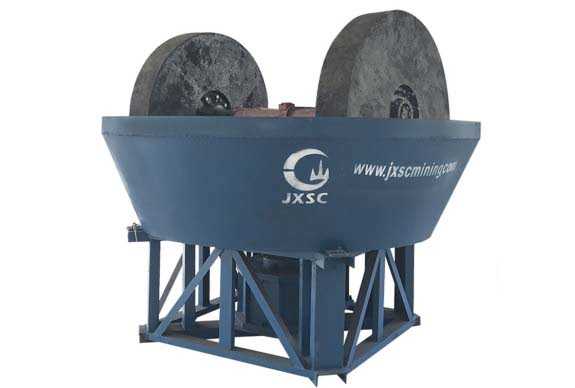
Others
1. Manual welding:low temperature; uneven welding seam; One-side welding;
2. Without using electric-chargeable liquid, scattering
liquid makes the plate surface uneven.
3. Low temperature;uneven welding there is slurry leakage from the joint.
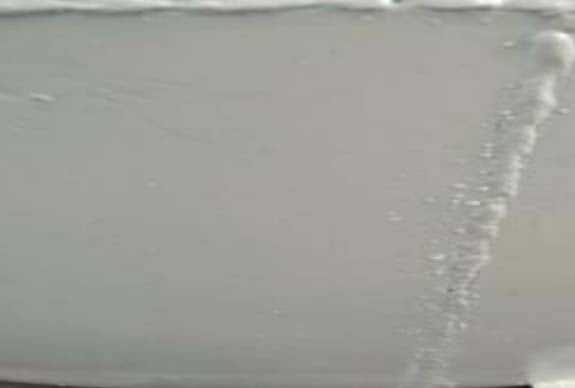
#4 Electric motor
JXSC
1. The stator coil is with long service life. pure copper wire
2. The motor is equipped with imported bearing, which has good mute effect and normal operation at high speed and high temperature.
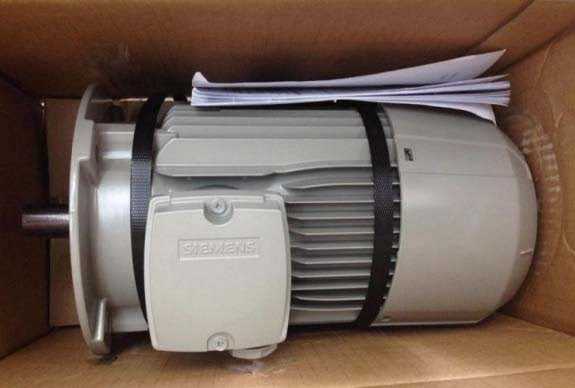
Others
1. The stator coil is made of aluminum wire with copper plating, which has a short service life.
2. Ordinary bearing noise, coil is easy to be heated, would affect the operation.
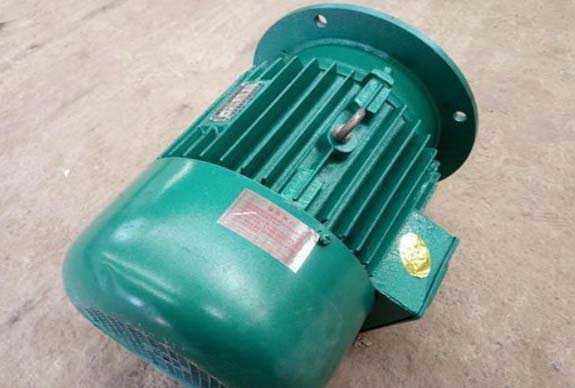
#5 Bear
JXSC
ZWZ bear
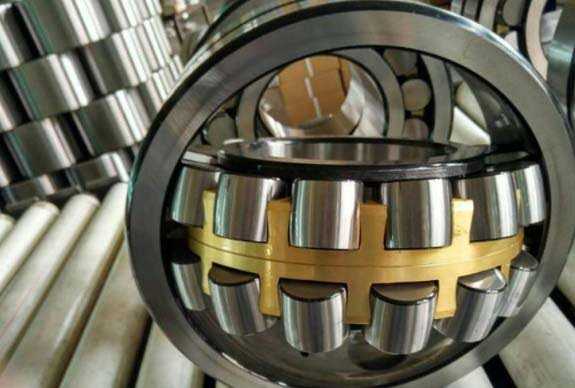
Others
Common bear
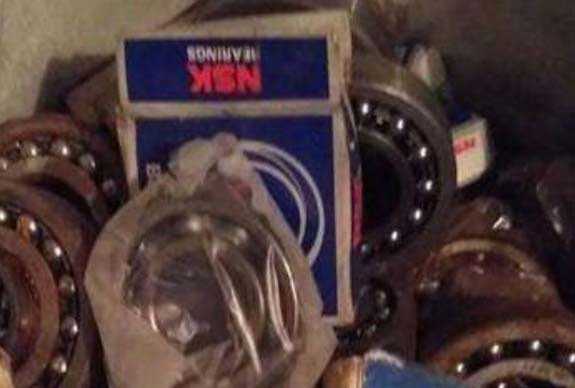
#6 Painting
JXSC
1. Porcelain glazed paint with once bottom painting and once surface painting
2. More waterproof, effectively prevent rust
3. Professional color palette, so that customers have more choices.
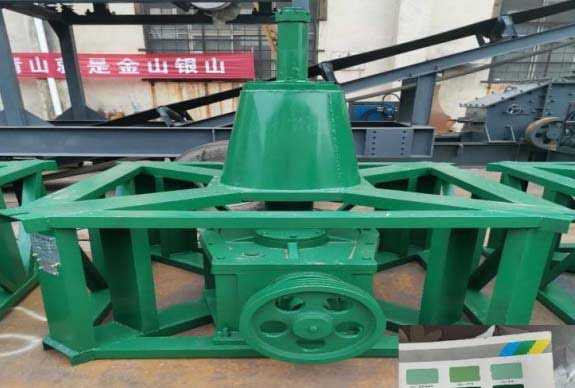
Others
Ordinary paint, easy to rust
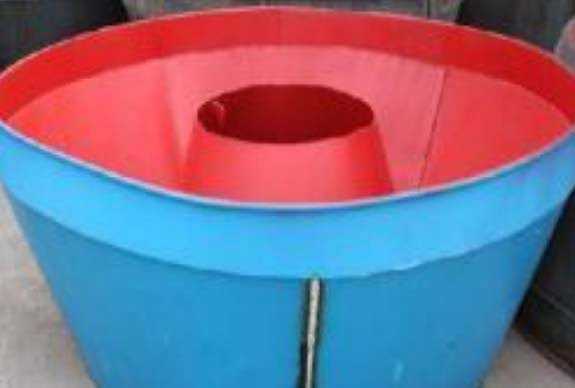