JXSC Mining Machinery offered this Alluvial Deposits Diamonds Mining Plant for washing & separating diamond from kimberlite rocks and other allivial diamond ores.
kimberlite diamond ores processing
Over thousands of years, the kimberlite rocks gradually reaches the Earth’s surface is eroded and weathered by wind, rain, rivers and streams.The eroded kimberlite bears rough diamonds, which are carried downstream. The first diamonds discovered in South Africa were from alluvial deposits.
Today, industrial alluvial diamond mining involves building a large wall to collect the water in one area. Diamonds are often found in the gravel layer, which collects under layers of other material, such as mud, clay and underwater plant-life. Once the gravel is collected, it is hauled to the surface and prepared for processing.
Alluvial Deposits Diamonds Mining are recovered from ore in 5 stages:
Stage 1 – Crushing
Once the diamond bearing ore and gravel is collected, it is transported to a primary crusher. The primary crusher is responsible for reducing the size of the ore into smaller, more manageable pieces or chucks measuring no larger than 150mm. A secondary crusher, known as a roll-crusher, may also be used to reduce the size of the ore even further.Stage 2 – Scrubbing
In this stage, the ore are scrubbed to remove loose excess material and is screened. Material smaller than 1.5mm is discarded because it is too costly to extract diamonds from such a small piece of ore.Stage 3 – Cyclonic separation plant
During this stage the diamond bearing ore is mixed with a solution of ferrosilicon powder and water, which is measured to a specific relative density. This solution is fed into a cyclone, which tumbles the material and forces a separation. Materials with a high density sink to the bottom, which results in a layer of diamond rich concentrate.Stage 4 – Recovery
Here, the diamond rich concentrate is put through a series or processes involving magnetic susceptibility, X-ray luminescence and crystallographic laser fluorescence that are calculated based on the specific properties of diamonds. These processes are designed to separate the rough diamond from any other heavy density materials collected by the cyclonic separation plant. For example, diamond’s fluorescence when exposed to an X-ray. Sensors detect flashes of light emitted by the diamond and sends a signal to a microprocessor that fires a blast of air at the diamond, which spits it into a collection box.
Concentration is performed by combining dense medium separation (DMS) with XRT (transmitted X-ray), pulsed X-ray, mineral jigs according to application and condition
- Stage 5 – Cleaned, weighed and packaged.
The diamonds collected in the recovery process are cleaned in an acid solution, washed, weighed and packaged in sealed containers for transport. In accordance with the Kimberley process, these containers are sealed with a tamper resistant seal, numbered on site, and a certificate of origin is issued.
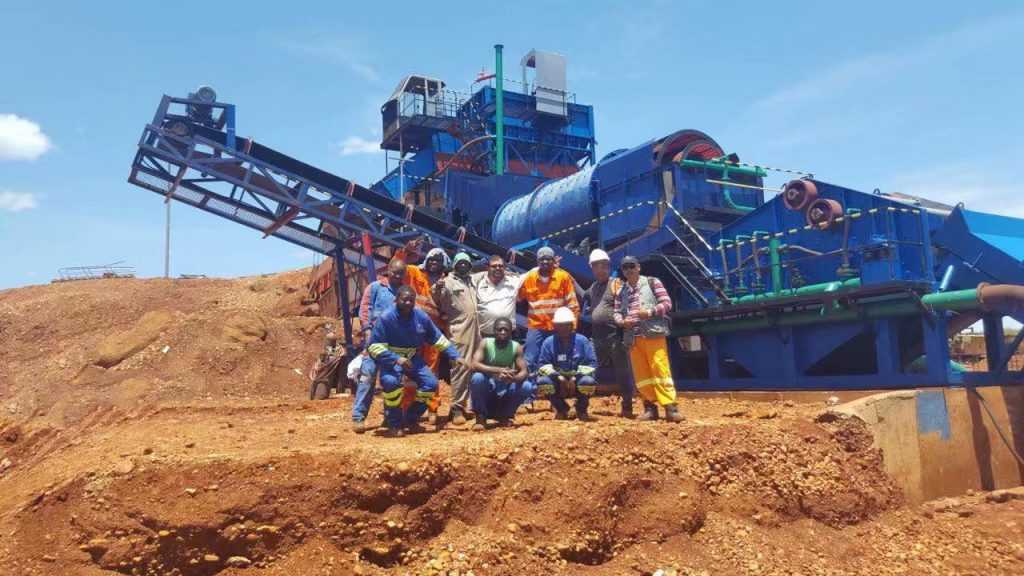
Processing of diamond ores begins with crushing. Typically, an ore is crushed initially to below 250 mm by means of a gyratory crusher and then to 75 mm using a cone crusher. The final stage of crushing is done by means of a high-pressure roller mill to further reduce the size below 25 mm. The incremental size reduction is helpful for minimizing the possibility of breaking diamonds inadvertently. The crushed ore is scrubbed in a tumbler in the presence of water, while the fines generated during crushing and scrubbing are removed by screening typically at 2 mm. The crushed ore in the range of 2–25 mm size is sent to heavy-media cyclones, with the diamond-rich underflows going to X-ray sorters to recover diamonds. The reject streams from the X-ray sorters are then sent to grease tables (or belts), in which diamonds are retained on the grease table as they are selectively attracted to the grease via hydrophobic interaction while hydrophilic gangue minerals flow through.
In most cases, the materials smaller than 2 mm are disposed of without further processing due to the lack of appropriate separation methods. In some plants, the 2 mm material is screened at 0.5 mm, and the 2 + 0.5 mm fraction is subjected to flotation.
However, it has been a challenge to recover small diamonds by flotation for two reasons. One is the difficulty in floating diamonds as large as 2 mm using conventional flotation machines. In general, mineral flotation is effective in the narrow particle size range of 0.1–0.25 mm. The other is that the dissolved species present in the aqueous phase of kimberlite ore slurry tends to reduce the hydrophobicity of diamonds, while the flotation of coarse particles requires stronger collectors that can increase the hydrophobicity beyond the level that is required for the flotation of smaller particles.
Equipment Lists for diamond wash plant
Diamond Washing Trommel
Mobile Trommel Wash Plant
Diamond Jig Separator
High-frequency Vibrating Screen
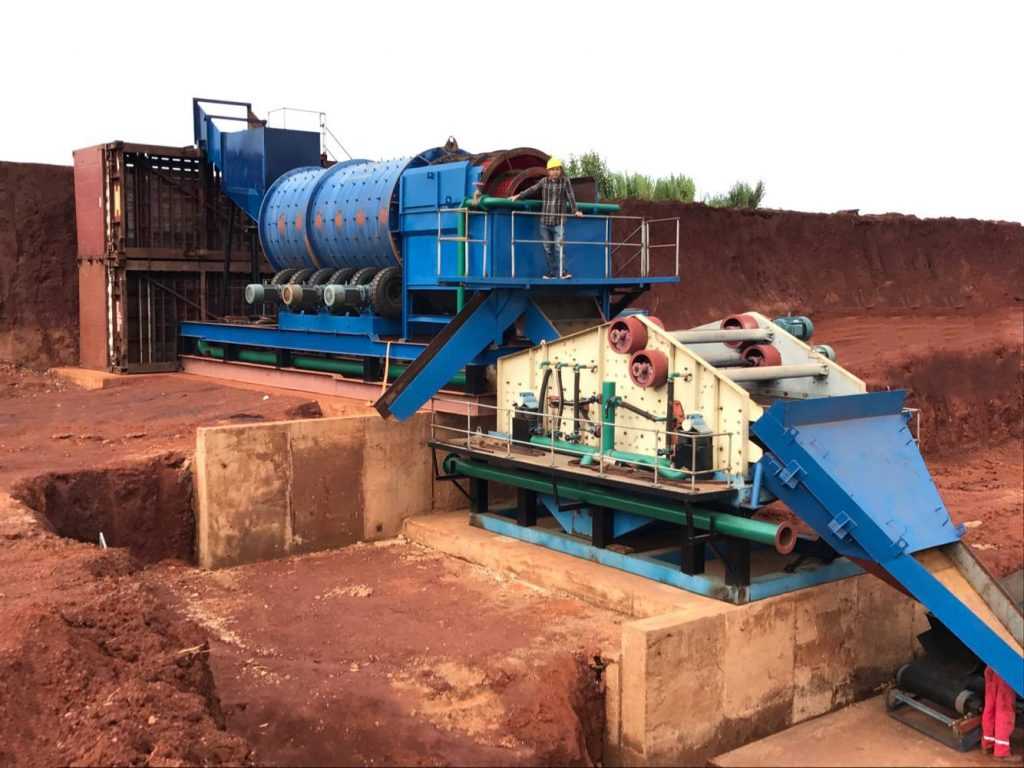
- Feed Hopper
Raw kimberlite ore may containing sticky clay firstly is fed into our hopper by the wheel loader truck or a conveyor belt.
The inner wall of JXSC’s hopper is lined with 10mm wear-resistant steel, which can greatly prolong the service life.
- Vibrating Feeder
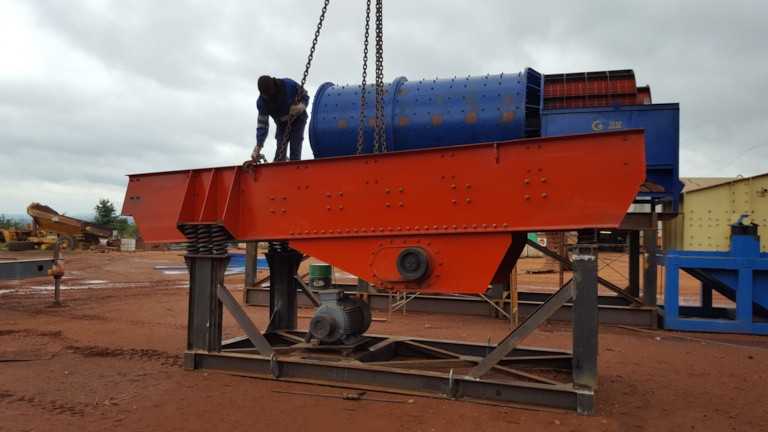
Then the feeding materials will work through a vibrating feeder, this can control the feeding material size below 150mm. It adopts replaceable wear-resistant grizzly bar, and also lined with 10mm thick wear-resistant steel.
As for the discharge trough part, the angle of the waste stone discharge device can be adjusted, the guide groove is made of rail steel, and the inner wall of the discharge chute is lined with wear-resistant steel.
The vibrating feeder belt is covered to make it safe and reliable. The double eccentric shaft vibration exciter inside, have a stable amplitude, which can provide good continuity and adjustable excitation force. And the top of the feeder is equipped with a water spray system and a booster pump.
This wash plant is also equipped with a steel stair aisle, makes it convenient for operation and maintenance.
You may notice that the inner wall of the feed tank is equipped with 10mm thick hardox 400 wear-resistant steel lining
as well as the other parts of inner pipes. Those help to extend the machine’s service life.
- Trommel Scrubber Washer
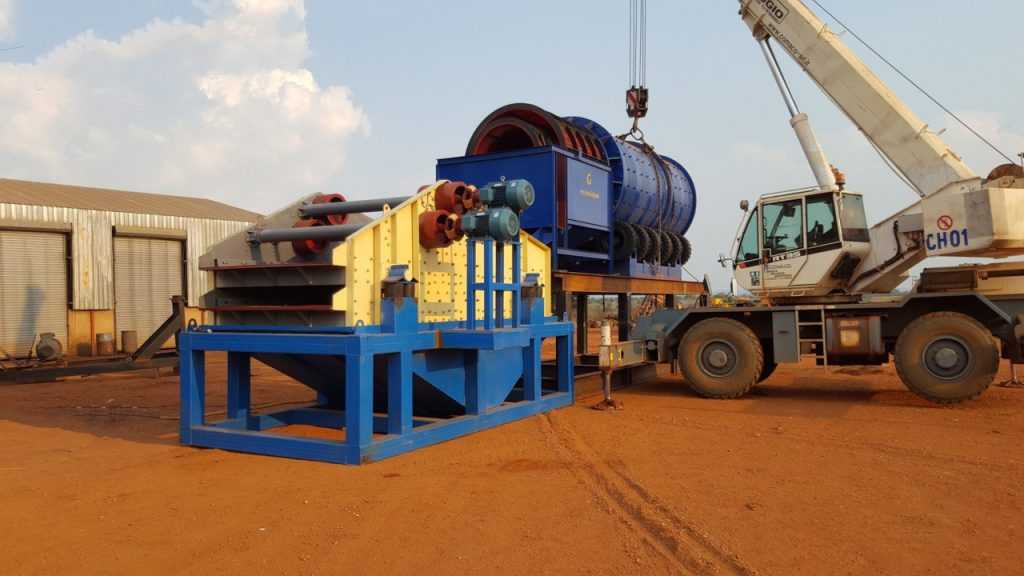
Diamond Trommel Washing Scrubber is the core parts of this diamond washing machine. It can significantly help remove water-soluble clays, deleterious materials and coatings providing a cleaner product. Our trommels washing screen are notable for its economy and efficiency, whether it is used in cleaning sand, gravel, or washing crushed stone and various ores. What’s more, It can process fine and coarse feed simultaneously,
Our machine adopts the latest cutting edge design. The outer screen is divided into two halves, And they are tightly connected by bolts. The trommel screen inside built with a robust cylinder design, those screen panels are very easy to replace, and you can choose from urethane, rubber, punch plate, or wire cloth media.
The drive part is powered by a group of model K127 reducer, and each reducer is equipped with 2 renewable tires. Units integrate abrasion-resistant steel or thick rubber liners, are secured into the scrubber drum to prevent wear and drum leakage. All the seams on a solid shell scrubber are welded to withstand the continual shock loading.
The outside water supply pipe for trommel scrubber is high-quality Q235 steel material, it has a big flow capacity and withstands high pressure. The continuous lifting and dropping action combined with water helps to abrade, scrub, and break down soluble contaminants. Optional trommel screen extensions can be added to provide rough product separation,
screening and dewatering capabilities.
- High-frequency Vibrating Screen
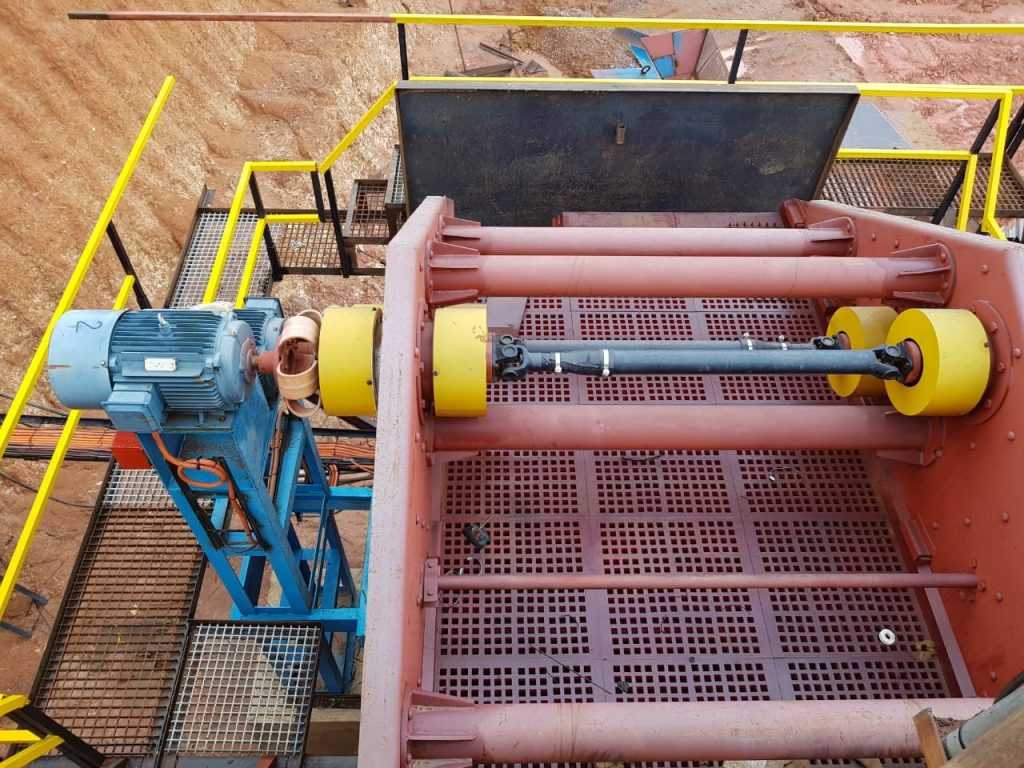
High-Frequency Vibrating Screening is another important part, it is used to separate material according to its size. Material is typically fed to a single-, double- or triple-deck screen to make the required sizes. The main water pipe of the vibrating screen adopts flange joint,
which can easily connect the external water pipe with the machine.
Through spray high-pressure water, it separates and washes material to obtain a good sieving effect. The material must go through or over a specified size to end up in the right pile. Unlike the crushers, Vibratory Screens cannot produce the material; they can only size material that is already reduced to the product sizes.
Under the screen slurry tank, there is a flange connector, it is convenient to connect the vibrating screen and pipe, and the tank lining with 4mm thick rubber plate, making it more wear resistance. The tank is also equipped with a discharge chute and access door, which can be opened for maintenance.
The driving shaft of the vibration screen, is made of high-quality DIN C45 Steel material. Material is typically fed to a single-,
double- or triple-deck screen to make the required sizes.
- Conveyor Belt
The final parts are the conveyor belt, the conveyor belt is at the heart of your operations and the key to its profitability. JXSC offers a comprehensive range of conveyor belts, designed for high performance, cost-effectiveness, and safety.
With our high-quality belt component, you can easily customize your output routing ways.