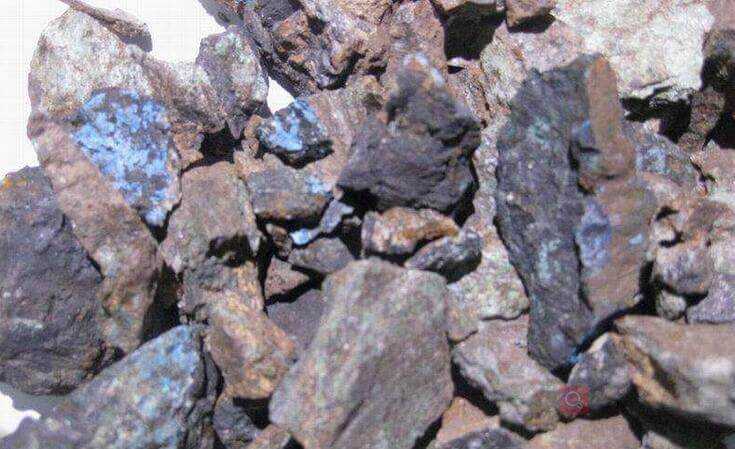
Copper Processing
Commonly used beneficiation methods include gravity separation, flotation, magnetic separation, electrical separation and chemical beneficiation. Even the same type of copper ore, it is necessary to design the most appropriate process according to local conditions, and cannot be copied completely.
Copper ore beneficiation
Commonly used beneficiation methods include gravity separation, flotation, magnetic separation, electrical separation and chemical beneficiation.
Gravity separation
The gravity separation method sorts minerals according to their relative density (usually called specific gravity). Mineral particles with different densities are subjected to the action of fluid power and mechanical force of various mineral processing equipment in the moving medium (water, air and heavy liquid), resulting in suitable loose stratification and separation conditions, so that the mineral particles of different densities are separated.
Currently, gravity separation is only used to select copper ores with coarser inlays, and is especially suitable for copper oxide ores with higher density. Commonly used gravity separation equipment includes heavy medium beneficiation, jig and shaker.
Flotation
The flotation method is based on the difference in the physical and chemical properties of the mineral surface, processed by the flotation agent, and the mineral is selectively attached to the bubbles to achieve the purpose of separation. The beneficiation of non-ferrous metal ores, such as copper, lead, zinc, sulfur, molybdenum, etc., is mainly treated by flotation; some ferrous metals, rare metals, and some non-metallic ores, such as graphite ore, apatite, etc. are also used for flotation Law selection.
Magnetic separation
The magnetic separation method is based on the different magnetic properties of minerals. Different minerals are subjected to different forces in the magnetic field of the magnetic separator, so as to be sorted. It is mainly used for sorting ferrous metal ores (iron, manganese, chromium), but also for sorting non-ferrous and rare metal ores.
Electric separation
The electrical separation method is based on the difference in mineral conductivity. When the mineral passes through the high-voltage electric field of the electric separator, due to the different conductivity of the mineral, the electrostatic force acting on the mineral is also different, so that the mineral can be separated. The electrical separation method is used for the separation of rare metals, non-ferrous metals and non-metallic ores. At present, it is mainly used for separation and beneficiation of mixed coarse concentrates, such as separation of scheelite and cassiterite, beneficiation of zircon, and beneficiation of tantalum and niobium ore.
Chemical beneficiation
Chemical beneficiation is a mineral processing process based on the difference in the chemical properties of minerals and mineral components, using chemical methods to change the mineral composition, and then enriching the target components by other methods. For example, leaching copper ore containing malachite with dilute sulfuric acid changes the mineral composition, that is, malachite becomes a copper sulfate solution, and then replaces copper ions in the solution with iron filings to obtain metallic copper.
Copper Processing flow
Copper beneficiation technology basically includes crushing, grinding, grading, sieving, sorting, drying and other processes. Each process is connected by a conveyor to ensure the integrity of the connection between the various processes.
1. Copper smelting
Copper concentrate is the primary mineral material for copper smelting, and its smelting methods include fire method and wet method. At present, the fire method is the main method, and the wet method is in the experimental discussion period.
2. Washing and screening
Ore washing equipment uses water flushing and mechanical scrubbing to separate the ore from the mud. Commonly used ore washing equipment include ore washing screen, cylinder trommel scrubber washing machine and trough type washing machine.
Ore washing work is often accompanied by sieving, such as flushing directly on the vibrating screen for cleaning or sending the ore (net ore) obtained by the ore washing machine to the vibrating screen for sieving. The sieving can be used as an independent work, separating the different sizes and grades of copper concentrate commodity supply with different uses.