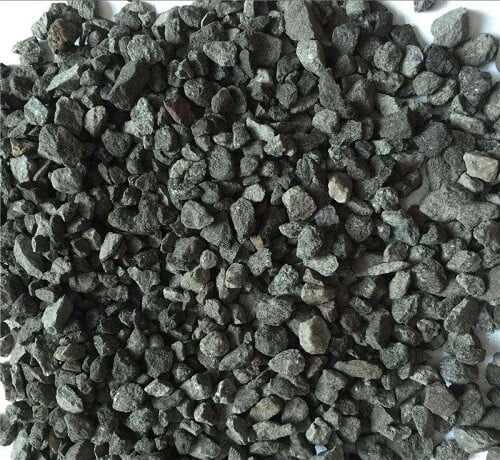
Magnetite Processing
Magnetite is mostly granular aggregates with strong magnetism and wide distribution. According to the different types of iron-bearing minerals, magnetite can be divided into single magnetite and mixed ore. In general, single magnet ore is often selected by weak magnetic separation method, and multi-metal magnet ore and mixed ore are usually combined process of multiple beneficiation methods. Email Us Chat Online
Magnetite beneficiation
Single magnetite
Most of the iron minerals in a single magnetite are magnetite. Because the single magnetite is simple in composition, strong in magnetism, and easy to grind and sort, the weak magnetic separation method is often used for selection.
◆ When the particle size of grinding is greater than 0.2mm, most iron ore magnetic separation plants often adopt a process of grinding and magnetic separation;
◆ When the grinding particle size is less than 0.2mm, the two-stage grinding-magnetic separation process is used;
◆ If qualified tailings are separated in the rough grinding stage, the magnetite magnetic separation plant should adopt the stage grinding-magnetic separation process;
◆ For dry and water-scarce areas, the magnetite ore dressing plant may consider using dry grinding-dry magnetic separation process;
◆ For the depleted magnetite-rich ore or magnetite-rich ore, the gangue can generally be removed by dry magnetic separation process, and then the lump-rich ore is obtained, and then the concentrate is obtained through the grinding-magnetic separation process.
In order to obtain high-grade concentrate, magnetite concentrate can be treated by reverse flotation or high-frequency fine screen. In addition, in order to further improve the recovery rate, processes such as tailings gravity separation may also be considered to further recover magnetic minerals.
Polymetallic magnetite beneficiation
The gangue containing polymetallic magnetite often contains silicate or carbonate minerals, associated with cobalt pyrite, chalcopyrite and apatite, etc. Generally, the combined process of weak magnetic separation-flotation is used, that is, weak magnetic separation process recovers iron, and flotation process recovers sulfide or apatite.
In general, the combined processes of weak magnetic separation-flotation process of polymetallic magnetite can be divided into weak magnetic separation-flotation and flotation-weak magnetic separation, the difference of which lies in the different direction of the continuum of magnetite and sulfide.
For the weak magnetic separation-flotation process flow, the contiguous body mainly enters the iron concentrate; for the flotation-weak magnetic separation process flow, the conjoined body mainly enters the sulfide concentrate. Therefore, under the same grinding particle size, the first float and then magnetic process process can obtain iron concentrate with lower sulfide content and sulfide concentrate with higher recovery rate.
Magnetite-Hematite beneficiation
According to the types of iron-bearing minerals, common iron ore can be divided into magnetite, hematite, vanadium-titanium magnetite, limonite, siderite and mixed ore consisting of two or more of these iron bearing minerals. Among them, magnetite-hematite is a common mixed ore, and its beneficiation usually adopts a combined process flow composed of multiple beneficiation methods.
Single Magnetite-Hematite
The single magnet-hematite is mostly fine-grained; the gangue mineral is mainly quartz, and some of it contains iron silicate. The proportion of magnets in the ore is gradually increases from the surface of the deposit to the deep part. The following two beneficiation methods are commonly used for selection:
Weak magnetic separation, gravity separation/flotation/strong magnetic separation
The combined process of using weak magnetic separation to recover magnetite and then gravity separation, flotation or strong magnetic separation process to recover weak magnetic iron mineral.
Production practice shows that for the weak magnetic separation-flotation process, the flotation method can be placed after the weak magnetic separation according to the nature of the ore and the actual conditions of the beneficiation plant, so as to ensure stable production indicators and save costs.
Polymetallic magnetite
The iron minerals in polymetallic magnetite are mainly magnetite and hematite or siderite, medium and fine-grained; gangue minerals are mainly silicate and carbonate minerals or fluorite, etc., and the accompanying components include apatite , pyrite, chalcopyrite and rare earth minerals.
The sorting of polymetallic magnetite is relatively complicated. Generally, the combined process consisting of weak magnetic separation and other mineral separation methods is used, that is, the weak magnetic separation method is used to recover the magnetite first, and then the gravity separation, flotation or strong magnetic separation method is used to recover weak magnetic iron minerals, and the associated components are final recovered by flotation.
The above is the common magnetite beneficiation method. For magnetite beneficiation, it is recommended to tailor the process to suit your own through the beneficiation test, and rationally select the appropriate magnetite beneficiation method according to the final beneficiation test report.