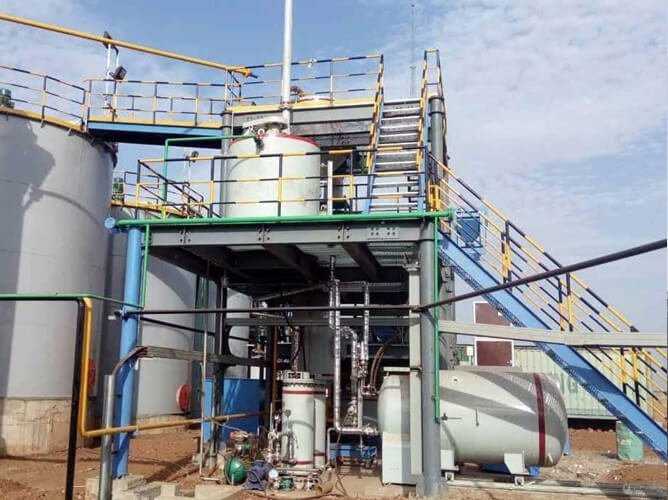
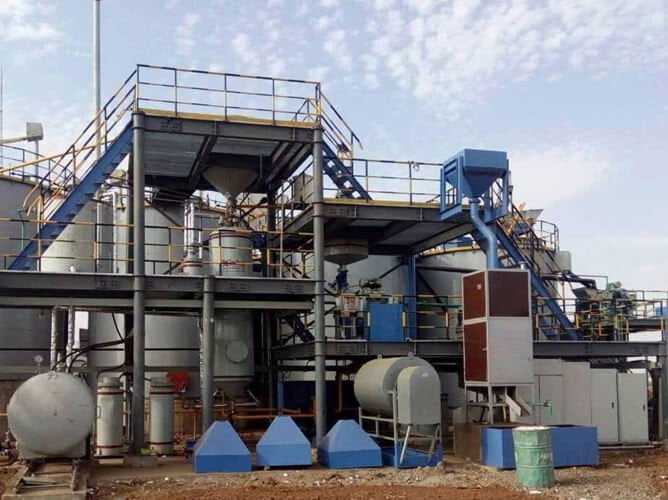
manganese Processing
Manganese is widely distributed in nature, and almost all kinds of ores and silicate rocks contain manganese. In modern industry, manganese and its compounds are widely used in various economic fields, of which the iron and steel industry is one of the most important fields. The amount of manganese used is as high as 90%-95%, which is mainly used as a deoxidizer and desulfurizer for iron and steelmaking.
manganese ore
Manganese oxide ore
Manganese oxide ore is mainly composed of secondary manganese oxide ore of weathered deposits, in addition to some primary and secondary manganese oxide ore of sedimentary and hydrothermal deposits. The manganese minerals in the manganese oxide ore are mainly dolomite, pyrolusite and hydromanganese ore; the gangue minerals are mainly silicate and carbonate minerals, often accompanied by iron, phosphorus and nickel, cobalt and other components.
Manganese carbonate ore
The manganese minerals in sedimentary manganese carbonate ore mainly include rhodochrosite, calcium rhodochrosite, manganese-containing calcite and rhodochrosite; gangue minerals include silicate and carbonate minerals, often accompanied by impurities such as sulfur and iron. The ore is generally more complex, and the particle size of the manganese mineral inlay is as fine as micrometers, which is not easy to dissociate, and it is often difficult to obtain a higher concentrate grade.
manganese beneficiation
Because most manganese ores are fine-grained or fine-grained, and there are a considerable number of high-phosphorus ores, high-iron ores and symbiotic (associated) beneficial metals, it is very difficult to classify. At present, the commonly used manganese ore beneficiation methods include physical beneficiation (washing and screening method, gravity separation method, strong magnetic separation method, flotation method, combined beneficiation method), chemical beneficiation (leaching method) and special beneficiation (fire method enrichment method) ).
Washing and screening
Ore washing mainly uses mechanical scrubbing machine to separate the ore from the mud. Commonly used equipment includes ore washing sieve, cylindrical ore washing machine and trough ore washing machine. Usually, the ore washing operation is accompanied by the sieving operation. Directly flush the water on the vibrating screen or send the ore (net ore) obtained by the ore washing machine to the vibrating screen for screening. Screening can be used as an independent part to separate products of different particle sizes and grades for different uses.
Gravity separation
At present, the gravity separation method is only suitable for sorting manganese ore with a simple structure and coarser particle size, especially manganese oxide ore with a higher density. Commonly used gravity separation methods include heavy-medium beneficiation, jig beneficiation and shaker beneficiation.
The beneficiation process of manganese oxide ore is generally to crush the ore to 6-0mm or 10-0mm, and then to classify, coarse grade particles are sent to jig sorting, and fine grade particles are sent to shaker for sorting.
Strong magnetic separation
Manganese minerals are weak magnetic minerals (specific magnetization coefficient X=10×10-6~600×10-6cm3/g), can be effectively recovered in a strong magnetic field magnetic separator with a magnetic field strength of Ho=800-1600kA/m (10000-20000oe), and the grade of manganese can generally be increased by 4-10%.
Because the magnetic separation method has the characteristics of simple operation, easy control, and strong adaptability, it is widely used in the selection of various manganese ores, and various new coarse, medium, and fine-grained strong magnetic machines have also been successfully developed.
Magnetic-flotation
The strong magnetic-flotation method has good adaptability. The strong magnetic separator not only effectively removes the slime, but also improves the selection grade of flotation. Strong magnetic-flotation desulfurization can directly obtain comprehensive manganese concentrate products.
Sodium petroleum sulfonate instead of oxidized paraffin soap as collector can make the ore pulp sort at neutral and normal temperature, saving medicine consumption and energy consumption.
Leaching
Generally, manganese ore leaching methods include direct leaching, roasting leaching and biological leaching. Among them, the direct leaching method includes the hydrosulfite method, sulfur dioxide method, ferrous sulfate method and so on.
Taking the leaching method of sulfur dioxide for manganese as an example, the manganese ore is slurried, and sulfur dioxide gas is introduced, and the manganese oxide in the ore is converted into MnSO4 and MnS2O6. Lime milk is added to the filtrate to produce manganese hydroxide precipitation, and solid manganese hydroxide is obtained after filtration. This method is suitable for processing low-grade, inlaid fine-grained manganese oxide ores.
The above are common manganese ore beneficiation methods. In actual production, most of the manganese carbonate ore beneficiation methods use strong magnetic separation, heavy medium beneficiation method and flotation method.
The manganese oxide ore is mainly adopts gravity separation method, and the ore washing-heavy separation-reduction roasting-magnetic separation-heavy separation process flow is mostly used. Of course, it is often necessary to combine two or more beneficiation methods for refractory manganese ore.