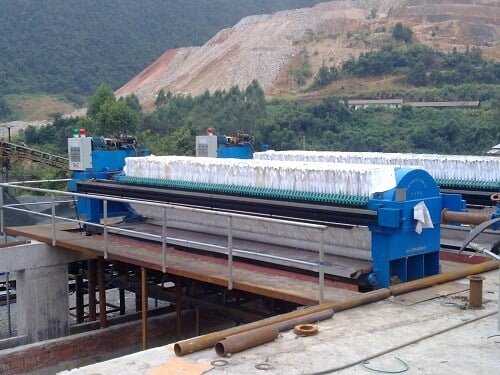
tailings Processing
Tailings refer to the parts of the beneficiation operation with lower useful target components, which are no longer suitable for separation under the current economic conditions. With the development of social economy and sorting technology, useful components in tailings can be further recycled. At the same time, the other components in the tailings are not completely useless waste materials. According to their nature and composition, they can be comprehensively utilized to achieve no waste discharge. This is a common requirement for full resource utilization and environmental protection. Email Us Chat Online
Tailings are misplaced resources, and their harmfulness is caused by improper handling by people. The hazards of tailings are mainly reflected in the harmfulness of elements and solid wastes. The harmfulness of the elements is reflected in the flotation reagent ions and other ions in the tailings entering the surrounding environment with water flow, air and other media, causing serious environmental pollution ; Tailings are the main component of industrial solid wastes. The accumulation of large amounts of them leads to land encroachment, vegetation destruction, land degradation, desertification, dust pollution, water pollution and other problems. At the same time, the accumulation of tailings is also a hidden danger of landslides and other geological disasters.
From the perspective of protecting the environment and making full use of resources, people have put forward requirements for tailings reuse and tailless emissions. The general idea of the comprehensive utilization of tailings is: 1. Based on the analysis of tail mineralization, re-election of tailings with re-election value; 2. Simple processing of the tailings after re-election Use construction materials or tailings to fill the mined-out area; 3. Finish the tailings to produce high-value building decoration materials; 4. Use ecologically restored tailings as ecological restoration materials.
Tailings are misplaced resources, and their harmfulness is caused by improper handling by people. The hazards of tailings are mainly reflected in the harmfulness of elements and solid wastes. The harmfulness of the elements is reflected in the flotation reagent ions and other ions in the tailings entering the surrounding environment with water flow, air and other media, causing serious environmental pollution ; Tailings are the main component of industrial solid wastes. The accumulation of large amounts of them leads to land encroachment, vegetation destruction, land degradation, desertification, dust pollution, water pollution and other problems. At the same time, the accumulation of tailings is also a hidden danger of landslides and other geological disasters.
From the perspective of protecting the environment and making full use of resources, people have put forward requirements for tailings reuse and tailless emissions. The general idea of the comprehensive utilization of tailings is: 1. Based on the analysis of tail mineralization, re-election of tailings with re-election value; 2. Simple processing of the tailings after re-election Use construction materials or tailings to fill the mined-out area; 3. Finish the tailings to produce high-value building decoration materials; 4. Use ecologically restored tailings as ecological restoration materials.
Tailings processing methods
The main treatment process of tailings at this stage:
The tailings consolidation discharge, tailings dry pile, and tailings filling are the main tailings treatment processes at the present stage. The first treatment process is more traditional tailings discharge technology, and it is still used by most of the dressing plants at this stage, but this tailings treatment method has problems of ecological damage and high maintenance costs. Therefore, at this stage, people have proposed a tailings disposal technology with a small footprint, a low degree of environmental disruption, and safe and efficient tailings disposal. In tailing filling, tailings are used as filling materials for the filling of mined mines, which solves the problem of shortage of filling materials and avoids the pollution of the tailings to the environment.
Tailings consolidation discharge
The concentrator will simply concentrate the water-bearing tailings obtained and then discharge them directly into the tailings pond through the pipeline. For the remaining water in the tailings, select the recycling or discharge through osmosis purification in the surrounding waters according to the design of the plant selection process.
During the transportation of tailings slurry, the ore sand is very serious to the wear of pipes, bends, valves, tailings pumps and other components. The wear and damage of the tailings transportation system not only affects the normal production of the processing plant, but also the tailings leakage will cause serious damage to the environment damage. JXSC has made breakthrough progress in the research of mine wear-resistant materials. The wear resistance of its wear-resistant rubber has reached 128%, which is about 10 times that of ordinary rubber. It is more wear-resistant than alloy in the colloidal state. The high-efficiency wear-resistant hydraulic cyclones, sieves, valves and other products manufactured by it have been widely used in the tailings discharge process of the dressing plant, which perfectly solves the problem of mine wear resistance.
As a traditional tailings treatment process, tail discharges have become increasingly prominent as the comprehensive utilization of resources and environmental protection requirements have increased. First, the useful components in the tailings cannot be recycled under the current economic conditions. With the development of technology and economy, their recycling is possible in the future, and secondly, other components in the tailings can also be used for other Use, so this treatment process caused a waste of resources. The construction of the tailings pond not only takes up a lot of cultivated land and destroys vegetation, but also all kinds of harmful ions in the tailings enter the surrounding environment with the water flow, causing serious pollution to the water body and suddenly. Improper maintenance of tailings ponds is likely to produce dust during dry climates, dam breaks during floods and heavy rains, and geological disasters such as debris flows, which pose a serious threat to the lives and property of surrounding residents.
Tailings dry piling
Tailings pile is a new technology for tailings treatment that has emerged in recent years. It refers to the process of tailing slurry after multi-level concentration and dehydration, and then using tailings tailings vibration dehydration and other high-efficiency dehydration equipment to form a small water content, easy precipitation and solidification And the slag piled up on the site is sent to the tailing pond for storage by means of belt conveyors or cars.
Common tailings dry discharge process:
Tailings processing related machine
Hydrocylone Vacuum disk filter Filter press Dewatering screen
Thickener + cyclone + belt filter: This equipment combination and process flow are suitable for the treatment of medium and coarse-grained tailings, which can be continuously produced. However, in the production and operation process, the power consumption is large, the cost is high, and the investment is large.
Thickener + ceramic filter: This process and equipment combination is suitable for the dewatering of medium-fine-grained tailings, but it has certain difficulties in the dewatering of coarse-grained and -0.037 mm particle size accounted for 80% of the pulp. The process can realize continuous production and the water content of dehydrated products is low. However, its equipment investment is relatively high, and the ceramic plate is easy to block, so it is generally used for the dehydration of concentrate.
Thickener + box filter press or vertical filter press: This process is suitable for the dehydration of medium and fine-grained materials. It can still be used when the -0.037 mm particle size accounts for 95%. Among them, the filter cloth and pump flow parts are vulnerable parts, which need to be replaced on time. Vertical filter presses are expensive and have a low moisture content, which is often used for concentrate dehydration.
Cyclone + thickener + multi-frequency sieve: This process is a combination of a new type of dehydration equipment and dehydration process, which can almost complete the dehydration operation of all mineral materials within 80% of -325 mesh. This solution has the characteristics of small investment and low operating cost. Its operating cost is 1/2 of the ceramic filter, belt filter, and chamber filter press. There are almost no wearing parts in the process. The high-frequency fine sieve screen adopts a built-in wear-resistant urethane combination screen, and its life is 3-10 times higher than that of the traditional metal screen. For very fine-grained materials, thickener + multi-frequency sieve + filter press can be used to complete the dehydration operation.
Among them, the high-efficiency multi-frequency dewatering screen is excited by dual vibration motors, and the structure is sturdy and compact, free from the shortcomings of the traditional eccentric vibrator, such as large structure, oil leakage, large wear, large noise, and inconvenient maintenance. The side body shield of the mine dewatering screen is bonded with wear-resistant rubber to ensure that the dewatering screen will not be deformed and broken by abrasion, and reduce the pollution of iron to the material. In addition, the mine dewatering screen uses a built-in wear-resistant urethane combination screen. Its life is 3-10 times higher than that of the traditional metal screen. It avoids the direct collision between the metal frame of the screen and the ore, reducing noise. Reduce the heavy feeling of metal screen.