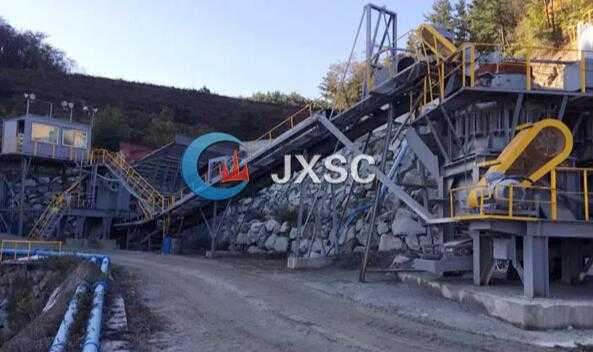

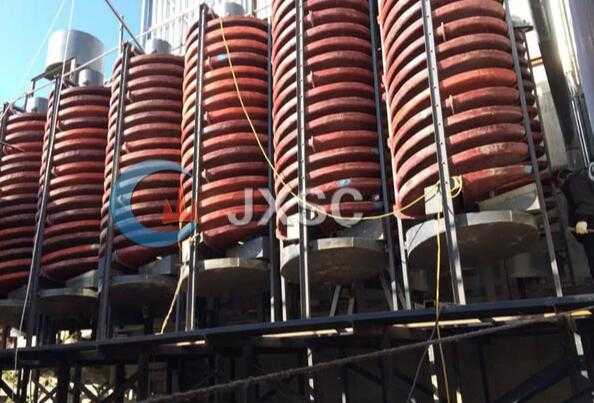
tungsten Processing
Tungsten is a rare metal with high melting point or refractory rare metal in the field of metallurgy and metal materials. Tungsten and its alloys are one of the most important functional materials in modern industry, national defense, and high-tech applications. They are widely used in aerospace, atomic energy, shipping, automobile industry, electrical industry, electronics industry, chemical industry, and many other fields.
tungsten ore beneficiation process
Classification-shaker-centrifugal concentrator
With the development of the times, the single shaker process cannot meet the requirements of efficie. The grading-shaker-centrifugal concentrator process divides the fine mud into two grades of +0.037mm and -0.037mm after concentration, +0.037mm grain grade is recovered with a shaker, and -0.037mm grain grade is selected with a centrifugal concentrator. The total recovery rate can reach 47% to 60%. Compared with the shaker process, the grading-shaker-centrifugal concentrator process strengthens the recovery of a 0.037 mm particle size, and the operation is simple and the indicators are stable.
Gravity-flotation process
After the concentrated mud is concentrated, it is pre-concentrated with a centrifuge, and then the sulfide ore flotation is performed on the coarse concentrate of the centrifuge, and the tungsten ore is enriched with a shaker for the tailings. The advantage of this process is that the centrifuge is used for pre-selection, and a large amount of gangue minerals can be discarded first, which not only greatly reduces the amount of ore feeding into subsequent operations, but also plays the role of desilting and pre-enriching fine mud, which improves the ore feeding grade.
Strong magnetic separation-flotation process
The tungsten ore has weak magnetic properties. Using this point, the tungsten fine mud that has been decontaminated and concentrated can be discarded by strong magnetic rough separation first. The strong magnetic separation coarse concentrate can be desulfurized and floated before using fatty acids, light fatty acids and water glass. Wait for the selection. This process can obtain fine mud concentrate with higher grade (W0350%), and the recovery rate can reach 54%-65%. In recent years, the strong magnetic separation-flotation process has been widely used in many tungsten separation plants. Through the experiment, the strong magnetic separation-flotation process was introduced in the tungsten fine mud treatment process to change the original single re-separation process. After being put into production, the grade of tungsten fine mud concentrate was increased by 10% and the operation recovery rate was increased by 30%. Compared with the full flotation process, the strong magnetic separation-flotation process can greatly reduce the amount of reagents, and has the advantages of short process and simple operation. Its disadvantage is that most of the sulfide ore is discarded with strong magnetic separation tailings. It is suitable for processing ores with high content of sulfide ore and scheelite.
Desulfurization-centrifugal concentrator-flotation
In this process, the tungsten fine mud is first desulfurized, and then the coarse concentrate is centrifuged with a centrifugal concentrator. The obtained coarse concentrate is desulfurized again and then enters tungsten flotation or strong magnetic separation. The recovery rate of the obtained tungsten fine mud concentrate is generally about 65% . In 2006, the recovery rate of the tungsten fine mud concentrate operation of a certain processing plant reached 66.87%, which was at the leading level in the same industry in China. Although this process can obtain a higher recovery rate of tungsten fine mud, the process is more complicated and requires higher flotation process. In addition, the efficiency of the centrifugal concentrator is lower than the shaker.