What is gold tailing?
In the mining industry, tailings are the materials left over after the process of separating the valuable fraction from the uneconomic fraction (gangue) of an ore. Tailings are distinct from overburden, which is the waste rock or other material that overlies an ore or mineral body and is displaced during mining without being processed.
In short words, tailings are ground up rock minus the gold. Rocks mined from underground which contain gold are called ore.
Processing involves crushing the ore into sand to liberate and recover the gold. What’s left over is called gold tailings.
Beneficiation and reprocessing gold tailings
Nowadays, more and more mining companies are figuring out ways to turn tailings to profits with novel reprocessing technologies to extract valuable metals from the waste. Tailings reprocessing is gaining more and more traction both for economic and environmental reasons. Here are some example include:
- DRD Gold, one of the first South African companies to abandon traditional mining to focus on extracting gold from tailings. New technology allows it to recover up to 40% of the gold left in particle form in tailings. DRD Gold extracted 33,600 ounces of gold, worth nearly US$40 million, in the last quarter of 2013.
- Mintails, a mine tailings processor, has developed new technology to process 350,000 tons of slimes from its extensive tailings resources. It expects to recover 58 kg of gold per month, and has enough slimes to last until 2025.
Our Study on gold tailing reprocessing
First, the collected ore samples are sent to the spiral chute, and then the samples are processed. Generally, they are processed into three types, such as medium ore, coarse sand, and fine mud, and then the coarse sand is selected. The inlay of gold, minerals and pyrite is very close, and the gold content of the ore sample is relatively small, about 0.13g per ton. Recycling of its metal substances.
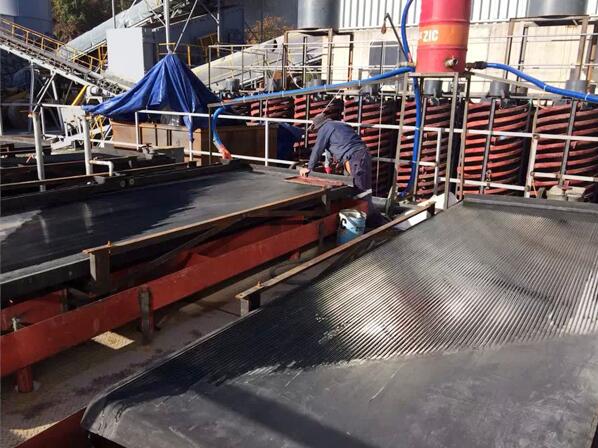
The most indispensable part of the ore process engineering is the shaking table operation, so that the recovered products can not only be applied to metal ores or gold mines. After the shaking table and other processes, the gold content of the gold grade can reach per ton of gold ore, and the survival rate in the spiral chute will be between 0.09%, which means the survival rate of the ore sample will be 1.3% for the tailings of the concentrator. %, but most of its production is lower-grade metal concentrate obtained by using a shaker. The daily productivity in the concentrator can reach 1,000 tons of ore production, and then 30 grams per ton of concentrate can be obtained after processing by the shaking table process. The two are incorporated into the leaching system, which can effectively recycle and utilize the two, and can also process them again.
- Strong magnetic iron removal process for beneficiation
The medium ore produced in the process of processing through the spiral chute is very rich in iron, sulfur and other substances, which are not suitable for use as raw materials for ceramic production, so there is some gap from the technical standards of ceramic production. It is necessary to further remove iron minerals and sulfur minerals. Since iron minerals, sulfur minerals, etc. have their own forms, various removal schemes and process treatments can be adopted. One of the methods is to grind them, and then adopt weak magnetic screening. After screening, they can be Placed at the stage of the flotation process.
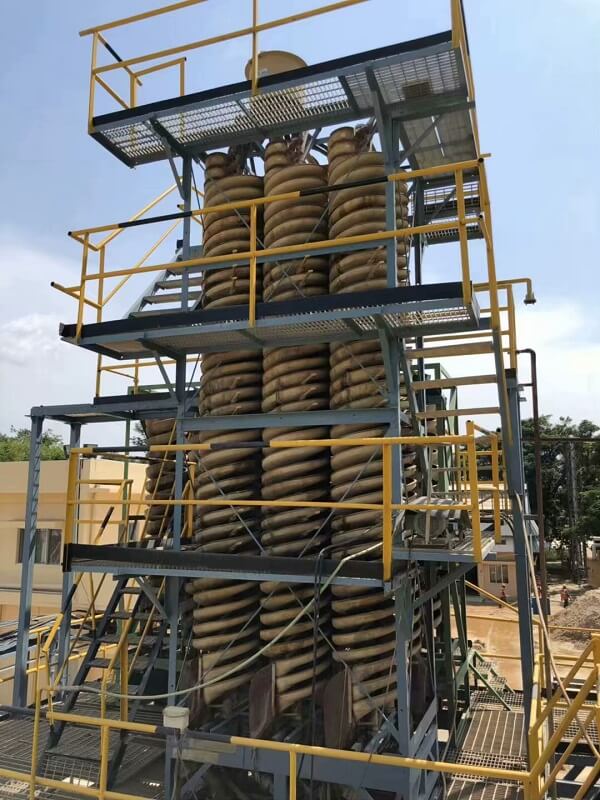
Another way is to select it by strong magnetic screening, and give flotation after strong magnetic selection. After the whole process is completed, iron minerals and sulfur minerals can be removed. By comparing the two methods, strong magnetic screening is obviously much cleaner than weak magnetic screening, so most companies will choose the second method. The medium ore produced after the spiral chute treatment can be applied to the stencil medium. Although the tooth plate medium is more commonly used, it is not as effective as the stencil medium. The magnetic induction intensity used in iron removal is about 1.8T. This iron removal operation can effectively improve the work efficiency of the operation.
- Desulfurization process test
After the strong magnetic treatment, there are even some residual sulfur impurities. The sulfur impurities contain pyrite. After the strong magnetic treatment, the reverse flotation technology can be used to remove the pyrite. This technology is mainly Reverse flotation is used to remove feldspar. If only xanthate is simply added, the sulfur cannot be removed. Therefore, some butyl xanthate can be appropriately added for flotation. Only in this way can the sulfur be removed. Good removal.
In general, the more common dispensing method is 500 grams of lime per ton, 200 grams of copper sulfate, 300 grams of collector, BK413 is generally selected as the collector, 30 grams of butyl xanthate and 27 grams of foaming agent.
- Applied Effects
It can be seen from the above process application and analysis that the ore samples existing in the tailings of gold beneficiation are processed by the spiral chute, and the combination of the two technologies of strong magnetic and shaking table technology can effectively obtain the content of iron and sulfur. Relatively low feldspar powder. Among them, the shaking table tailings can be carried out by underground filling. In the various operations of the process, fine mud, etc. will be transported to the tailings dam through pipelines, and the remaining feldspar powder can be used for the production and production of ceramics middle.
Why is tailing raise great concert nowadays?
The environmental concerns associated with mining are well known nowadays, since tailing can be dangerous sources of toxic chemicals, such as heavy metals, sulfides and radioactive content. Once those waste and tailing did not receive a responsible process or leak outside, they may cause serious environmental disasters. Because of these and other environmental concerns, such as groundwater leakage, toxic emissions, or bird death, that is why the first UN-level standard for tailing management was established to mitigate these risks in 2020.
The good news is that there are a wide range of methods for recovering economic value, containing or otherwise mitigating the impacts of tailings. From tailings to treasure and make money from tailing reprocessing has be proved as a sustainable business.