In the mining and mineral processing industry, ore handling or ore preprocessing, which may account for 30-60% of the total delivered price of raw materials, usually covers the processes of transportation, storage, feeding, and washing of the ore en route to, or during, its various stages of treatment in the mill.
Since the value of minerals is dependent on their quality, clay and other deleterious materials need to be removed at the processing plant prior to the downstream process.
Ore entering the mill from the mine (run-of-mine ore) normally contains a small proportion of material that is potentially harmful to the mill equipment and processes. For example,
- In the crushing stage, large pieces of iron and steel broken off from mine machinery can jam in the crushers and even cause damage to the crusher machines.
- In flotation processing, wood is a major problem as this is ground into a fine pulp and causes choking or blocking of screens, etc. It can also choke flotation cell ports, consume flotation reagents by absorption and decompose to give depressants, which render valuable minerals unfloatable.
- Clays and slimes adhering to the ore are also harmful as they hinder screening, filtration, and thickening, and again consume valuable flotation reagents.
So all these must be removed as far as possible at an early stage in treatment. Hand sorting from conveyor belts has declined in importance with the development of mechanized methods of dealing with large tonnages, but it is still used when plentiful cheap labor is available, such as artisanal miner or small-scale miner.
Methods to remove iron and steel
Crushers can be protected from large pieces of “tramp” iron and steel by electromagnets suspended over conveyor belts. These powerful electromagnets can pick up large pieces of iron and steel traveling over the belt and, at intervals, can be swung away from the belt and unloaded. Guard magnets, however, cannot be used to remove tramp iron from magnetic ores, such as those containing magnetite, nor will they remove non-ferrous metals or non-magnetic steels from the ore.
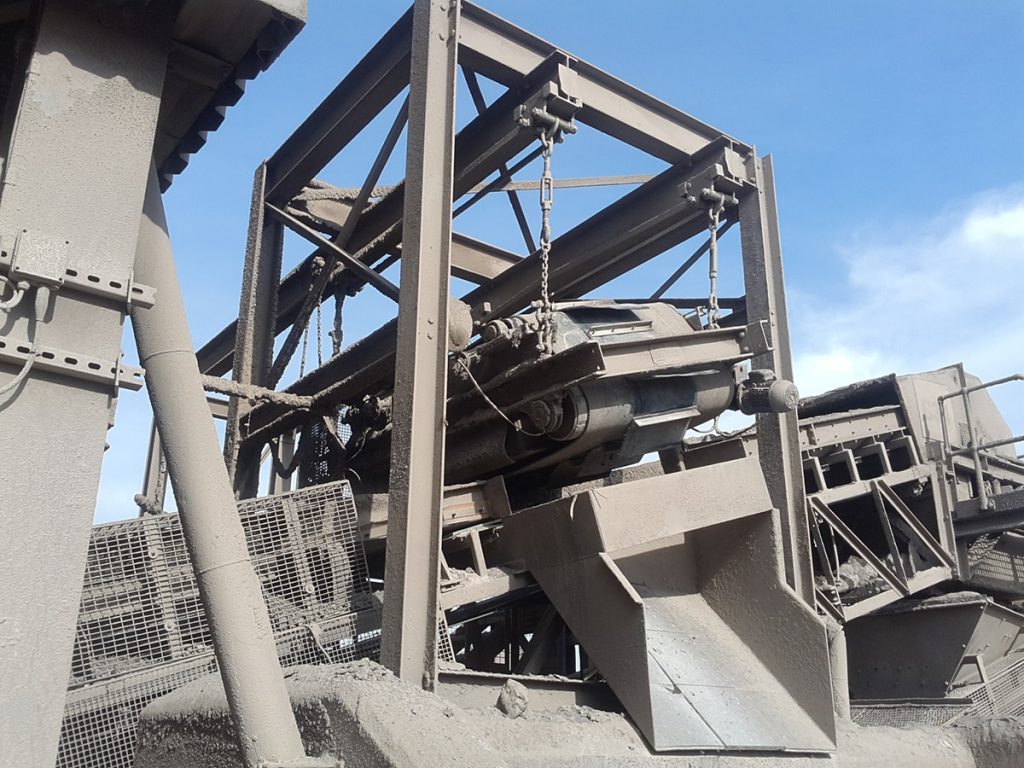
Metal detectors, which measure the electrical conductivity of the material being conveyed, can be fitted over or around conveyor belts. The electrical conductivity of ores is much lower than that of metals and fluctuations in electrical conductivity in the conveyed material can be detected by measuring the change that tramp metal causes in a given electromagnetic field. When a metal object causes an alarm, the belt automatically stops and the object can be removed.
It is advantageous with non-magnetic ores to precede the metal detector with a heavy guard magnet which will remove the ferromagnetic tramp metals and thus minimize belt stoppages.
Methods to remove wood from flotation processing
Large pieces of wood which have been “flattened out” by passage through a primary crusher can be removed by passing the ore feed over a vibrating scalping screen.
And the working principle is very simple but efficient, the apertures of the screen are slightly larger than the maximum size of particle in the crusher discharge, allowing the ore to fall through the apertures and the flattened wood particles to ride over the screen and be collected separately.
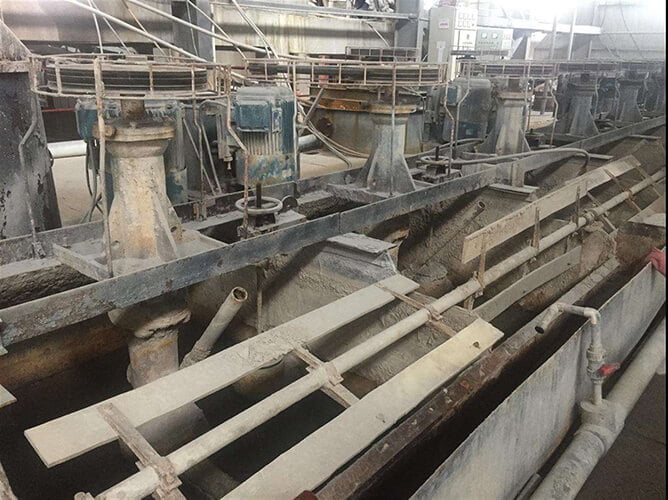
Wood can be further removed from the pulp discharge from the grinding mills by passing the pulp through a fine screen. Again, while the ore particles pass through the apertures, the wood collects on top of the screen and can be periodically removed.
Use washing to remove very fine harmful particles
Washing of run-of-mine ore can be carried out to facilitate sorting by removing obscuring dirt from the surfaces of the ore particles. However, washing to remove very fine material, or slimes, of little or no value, is more important. Washing is normally performed after primary crushing as the ore is then of a suitable size to be passed over washing screens. It should always precede secondary crushing as slimes severely interfere with this stage.
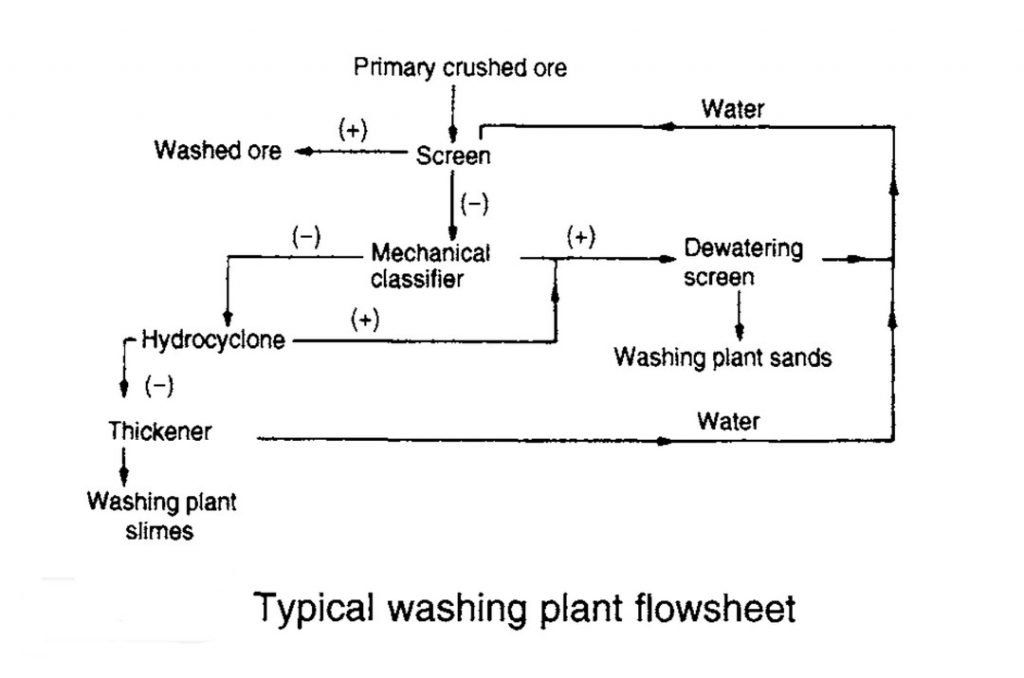
The ore is passed through high-pressure jets of water on mechanically vibrating screens. The screen apertures are usually of similar size to the particles in the feed to the grinding mills, the reason for which will become apparent. In the circuit shown in the above picture, material passing over the screen, i.e. washed ore, is transported to the secondary crushers. Material passing through the screens is classified into coarse and fine fractions by a mechanical classifier or hydrocyclone or both. It may be beneficial to classify initially in a mechanical classifier as this is more able to smooth out fluctuations in flow than is the hydrocyclone and it is better suited to handling coarse material.
The coarse product from the classifier, designated “washing plant sands”, is either routed direct to the grinding mills or is dewatered over vibrating screens before being sent to mill storage. A considerable load, therefore, is taken off the dry crushing section. The fine product from classification, i.e. the “slimes”, may be partially dewatered in shallow large-diameter settling tanks known as thickeners and the thickened pulp is either pumped to tailings disposal or, if containing values, pumped direct to the concentration process, thus removing the load from the grinding section.
In the circuit flowsheet shown, the thickener overflows are used to feed the high-pressure washing sprays. Water conservation in this manner is practised in most mills. The wood pulp may again be a problem in the above circuit, as it will tend to float in the thickener, and will choke the water spray nozzles unless it is removed by retention on a fine screen.
Sometimes these impurities can be removed by washing, but other times a more aggressive approach is required to work the deleterious material free.
Use Scrubbing to produce a high-quality, silt-free mineral product
In some situations, the deleterious materials maybe can’t be removed with just washing, so further scrubbing processing is needed in order to make those materials released from mineral products.
Scrubbing is more intense processing and requires more energy than washing. During the scrubbing process, minerals are freed, or separated, from deleterious materials by agitation with water and then thoroughly flushed away from the desired product to a settling pond or water treatment process.

In conclusion
With the development of modern metallurgy and beneficiation, more and more refined operations are implied in mineral beneficiation, the deleterious materials are harmful to downstream mineral processing and cause many problems and even damage your profits. Therefore, desirable aggregates and minerals should be clean and free of impurities that can cause problems that affect their performance. And ore handling and preprocessing have become more and more important parts of mineral processing.