Antimony is a non-renewable strategic mineral resource and an indispensable and important raw material for modern industrial development. With the high-intensity resource mining in recent years, the consumption of antimony resources is too large. Antimony beneficiation methods are important to improve the recovery rate of antimony ore.
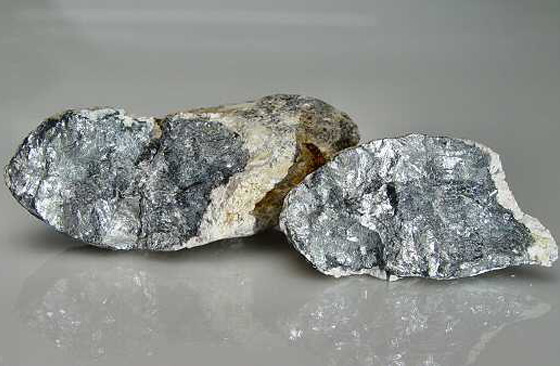
Antimony is a scarce resource. It is a silver-gray metal. It is an acid-resistant substance at room temperature. Its specific gravity is 6.68, its melting point is 630.5 °C, and its boiling point is 1590 °C. It is brittle and has no ductility. It is a poor conductor of electricity and heat. It is not easy to be oxidized at room temperature and has corrosion resistance. The main function of antimony in alloys is to increase hardness, and is often referred to as a hardener for metals or alloys. Antimony and antimony compounds were first used in wear-resistant alloys, printing type alloys and the arms industry. With the development of science and technology, it has been widely used in the production of various flame retardants, enamels, glass, rubber, coatings, pigments, ceramics, plastics, semiconductor components, fireworks, medicine and chemical products.
Antimony beneficiation Methods
Hand Separation
The antimony ore hand-selection process is carried out by using the difference in color, luster and shape of the antimony-containing minerals in the antimony ore and the gangue. Although this method is primitive and labor-intensive, it still has special meaning for antimony ore beneficiation. Since antimony deposits are often produced in the form of coarse single crystals or massive aggregate crystals, hand-selecting can often get high-grade bulk antimony concentrates, which are suitable for the technical requirements of vertical roasting furnaces in antimony metallurgical plants. In addition, manual selection can reduce the production cost and energy consumption of beneficiation, so it is widely used in various areas.
Gravity separation
Gravity separation is one of the most economical, ideal and effective antimony beneficiation methods. It can also be used as a pre-enrichment operation for flotation, reducing the burden on grinding equipment and improving the efficiency of the process flow.
The embedded particle size of antimony ore is generally coarse, and the specific gravity of antimony crystal is much larger than that of the associated gangue. Therefore, the gravity separation method is an ideal method to treat antimony ore. The primary condition for gravity beneficiation is monomer dissociation. For antimony ore beneficiation, the degree of monomer dissociation between antimony ore and waste rock directly affects the effect and beneficiation index of gravity separation. It is necessary to crush or even grind the antimony ore to break the conjoined structure and dissociate the antimony ore from the waste rock monomer. The higher the degree of monomer dissociation, the higher the beneficiation effect and recovery will be. The antimony ore gravity separation equipment mainly refers to the jig separator, and sometimes the shaker table is also used. The re-election cost is low, and a large amount of qualified coarse-grained concentrate can be sorted out in a relatively coarse-grained range, and a large amount of gangue can be discarded.
Flotation Separation
Flotation is the most important extraction method for antimony deposits. Antimony sulfide deposits are easy-to-float deposits, and flotation methods are mostly used to improve the crystal position of the ore. In the meantime, stibnite often uses lead salts as activators first, and also uses copper salts or both lead salts and copper salts, and then uses collectors for flotation. Commonly used collectors are butyl xanthate or a mixture of shale oil and ethyl thiazide, and the foaming agent is pine oil or No. 2 oil. Antimony oxide ore is classified as refractory ore. Flotation is the main beneficiation method for obtaining powdered antimony concentrate, and flotation is included in almost all beneficiation processes. The types of ores used for processing are: mono-antimony sulfide ore, sulfide-oxidized mixed antimony ore, tungsten antimony gold polymetallic sulfide ore, antimony arsenic gold sulfide ore, tin, lead, antimony, zinc polymetallic sulfide ore, antimony, lead , zinc, mercury polymetallic sulfide ore and arsenic, antimony, gold polymetallic sulfide ore, etc., now take the single sulfide ore of mine and the beneficiation of tin, lead-zinc, antimony polymetallic ore as examples to illustrate the single Flotation process for antimony sulfide ores and complex antimony sulfide ores.
For complex polymetallic minerals containing antimony, multiple heavy non-ferrous metal sulfides are often associated: arsenic-containing sulfide minerals such as arsenopyrite FeAsS, realgar AsS, orpiment As2S3; lead-containing sulfide minerals such as galena; zinc-containing sulfide minerals such as sphalerite ; Cinnabar and other mercury-containing sulfide minerals and so on. Sometimes there are also oxide minerals with great economic value, such as cassiterite, scheelite, etc.; there are also precious metal minerals such as natural gold. Therefore, it is necessary to consider the comprehensive recovery of filtration during beneficiation.
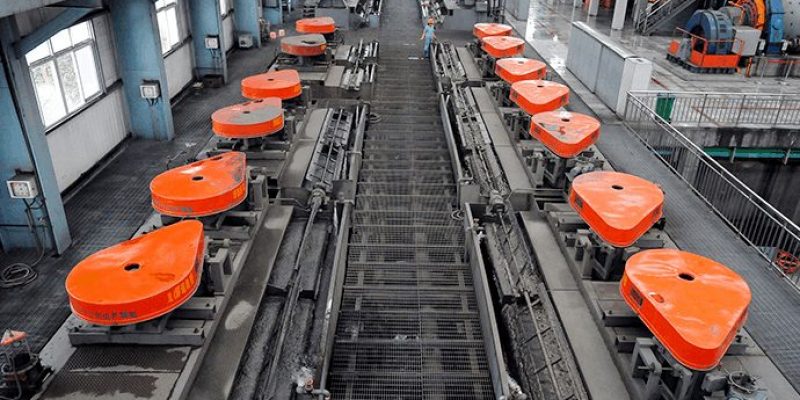
How to improve the recovery rate of antimony ore beneficiation?
1. The flotation reagent system is the key to improving the level of mineral processing technology, mainly to find a cost-effective collector for antimony oxide ore, which must be achieved through mineral processing experiments.
2. Under the existing process flow structure and conditions, strengthen the operation management and adjust the process conditions to adapt to the changes in the properties of the raw ore. Strict management of each link is required. The control of ball milling operation conditions is the key to reducing the cost of beneficiation and improving the flotation effect. The method of adding chemicals can be considered to increase the efficacy and reduce the consumption of chemicals by adding water. Increase the concentration of roughing and reduce the concentration of beneficiation to ensure the recovery rate of roughing and improve the grade of concentrate. It is also necessary to adjust the pH value of the pulp to ensure the selective flotation of useful minerals;
Antimony processing plant
There are many varieties of antimony ore, including antimonite, antimonite, antimony, antimony ochre, etc. Depending on the properties of the ore, the optional beneficiation processes include manual selection, gravity separation and flotation. The density, color and metallic luster of stibnite are significantly different from those of gangue minerals, and the floatability is relatively good. Therefore, good results can be obtained regardless of single flotation or re-selection combined with hand-selection. At present, flotation is the main beneficiation method for stibnite. Gravity separation is mainly used for the beneficiation of antimony oxide ore and the separation of coarse stibnite. Therefore, the beneficiation process of single antimony sulfide ore includes single flotation process and gravity separation-flotation combined process. This is the antimony flotation plant flowchart:
The specific process flow needs to be designed according to the nature and characteristics of the ore. This process flow is a general process flow and is universal. The specific mineral processing process needs to provide antimony ore samples from the customer to determine the best mineral processing solutions. The selection of suitable antimony ore beneficiation equipment can better improve the flotation effect and enhance the economic benefits of the enterprise. JXSC has been engaged in metal beneficiation plant for more than 38 years.