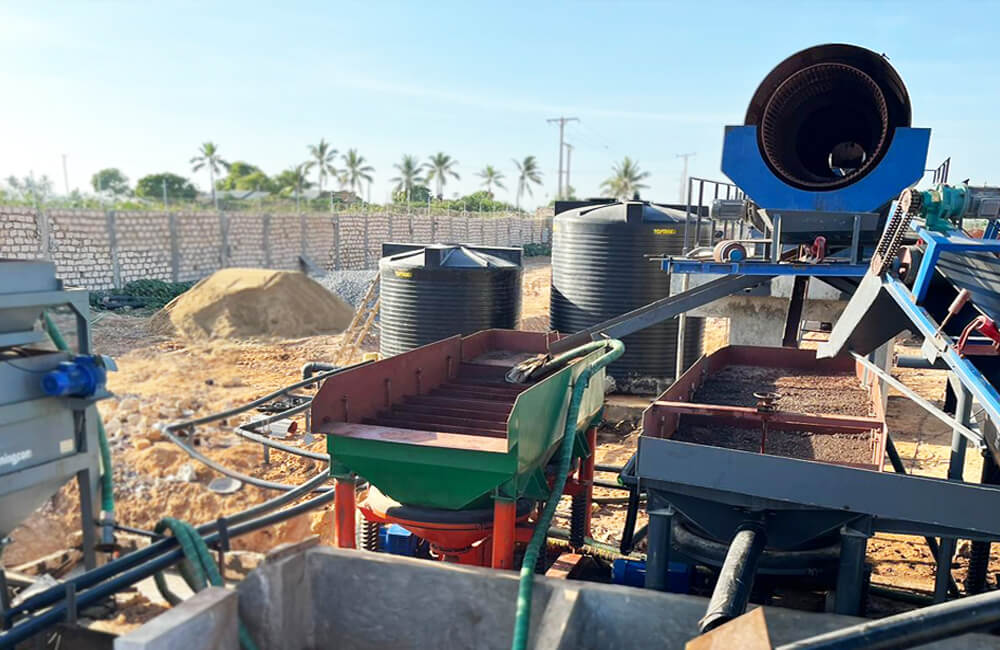
Manganese Ore processing
JXSC manganese ore process and equipment can separate various components of ore, including crushing, washing, screening, gravity separation, magnetic separation and flotation processes, etc. After beneficiation, the ore becomes more valuable and can be used in various industries such as steelmaking and alloys.
Application: beneficiation of the manganese oxide ore, carbonate manganese ore, manganese-containing iron ore and multi-metal composite manganese ore.
manganese Beneficiation Process
Manganese ore beneficiation is extracting valuable minerals and removing impurities from manganese ore. It usually includes crushing, grinding, washing, gravity separation, flotation or magnetic separation to improve the grade and concentration of manganese. The manganese ore process is used to beneficiate manganese oxide and carbonate ore.
- Pre-separation: usually includes crushing and grinding to reduce the size of the ore particles; sometimes a washing process is also used to effectively remove impurities such as soil and clay adhering to the surface of the manganese ore.
- Gravity separation: A method of using gravity differences to separate and enrich manganese minerals in ores; usually suitable for situations where the density difference between manganese minerals and waste rocks is large. Its equipment includes jig separators, shaking tables, spiral chutes, etc.
- Magnetic separation: It mainly separates the manganese iron oxide. Manganese minerals are attracted to magnetic fields, while impurities are not.
- Flotation process: Flotation separates manganese ore by adding chemicals to make the surface of manganese ore particles hydrophilic or hydrophobic. It mainly beneficiates manganese ores containing non-metallic impurities such as silicates.
The actual process flow may vary depending on the composition and characteristics of the ore. Usually, the combined beneficiation process is used for manganese ore processing plant to maximize the mineral grade and recovery rate.
manganese ore Processing plant
1. Rock Manganese Ore Processing
This setup is for the rock manganese ore processing plant, main equipment and flow including:
- Jaw crusher
- Cone crusher
- Vibration screen
- Ball mill
- Slurry pump
- Spiral chute
- Double drum magnetic separator
- The raw bin+vibration feeder for feeding materials to the jaw crusher automatically, you only need to load the materials to the raw bin by truck or excavator or else as you want.
- The jaw crusher is for crushing the raw ore to small pieces, then to the cone crusher to get the fine sizes. The vibration screen for separating the size +20mm back to the cone crusher, 0-20mm will sent to ball mill by electromagnetic feeder.
- The ball mill is for grinding the 0-20mm materials to 0-1mm, then using the slurry pump to transport the 0-1mm materials to the spiral chute to separate the heavy minerals.
- The double drum magnetic separator is for separating the manganese from other heavy minerals, making the manganese concentrate to a higher grade.
2. Alluvial & Rock Manganese beneficiation
This is a setup of alluvial & rock manganese ore process plant, the main equipment including:
- Trommel scrubber
- Vibrating screen
- Impact crusher
- Belt conveyor
Capacity: washing 100 TPH, crushing with 200 TPH
1. Washing part: The vibrating feeder feeds the raw material into a trommel scrubber for scrubbing and washing the clay.
2. The output from the scrubber goes to a vibrating screen directly for screening. The vibrating screen with 4-layer decks for separating different products: 5mm, 20mm, 30mm and 80mm.
3. Crushing part: The vibrating feeder feeds the raw material around 200mm into an impact crusher for less than 80mm crushing.
4. The output from the crusher also goes to a vibrating screen for screening. The overscreen of more than 80mm particles goes back to the impact crusher again for crushing.
The capacity for this process plant can be customized as per requirement and mine situation.
Contact Us Now
Please fill out the information below for the quotation price and engineer’s help. We will reply ASAP!
Notice:
- We do not provide jobs and have no interest in investment or partnerships.
- We provide mineral processing equipment and solutions; not buy and sell mineral /ore /materials.
- We value your privacy and keep your information safe.