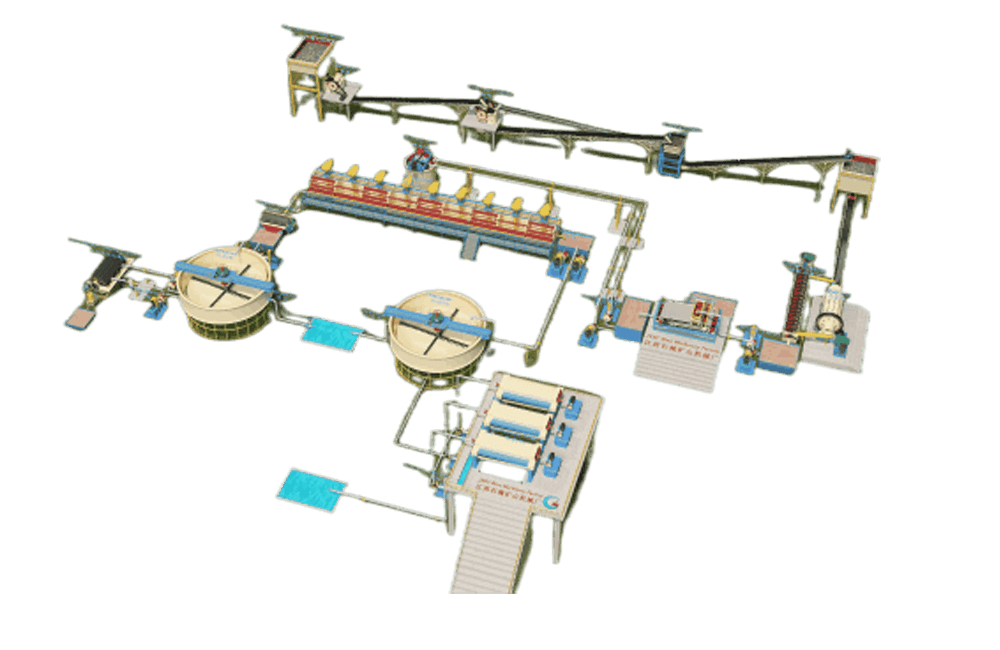
Feldspar Processing Plant
Feldspar is an aluminosilicate mineral containing calcium, sodium, and potassium. There are many kinds of it, such as orthoclase (potassium feldspar), albite, anorthite, micro plagioclase, etc. Mainly contains iron minerals; its impurities include clay, quartz, mica, garnet, beryl, etc.
Feldspar processing plant usually using magnetic, gravity separation, flotation and combined processes.
Feldspar benefication Process
The iron mineral will affect the color of the feldspar concentrate and reduce the quality. Therefore, iron removal from feldspar is an important link by beneficiation. The methods of feldspar ore beneficiation can be processed differently according to the characteristics of the ore and requirements.
1. It should adopt strong magnetic separation process for weakly magnetic minerals such as iron oxide, mica and garnet in potassium feldspar ore.
2. When the iron-containing impurities in potassium feldspar are pyrite, mica, or iron-containing alkali metal silicate minerals such as garnet and tourmaline, or potassium feldspar with non-magnetic impurities, the flotation process is often used to clean up.
3. Potassium feldspar containing fine-grained or iron-stained impurities refractory to separation should be processed by combined flotation-magnetic separation, scrubbing-magnetic separation-flotation and other combined processes.
feldspar ore process
- High-quality feldspar produced in pegmatite: hand selection – crushing – wet grinding – classifying.
- Feldspar in weathered granite: washing – crushing – grinding – classification – flotation (removal of iron and mica or separation of feldspar and quartz).
- Feldspar in fine crystal rock: crushing – grinding – screening – magnetic separation.
- Feldsparous placer: washing mud – screening or flotation to separate quartz.
Feldspar Processing plant
1. Feldspar flotation + Magnetic separation process
Raw feldspar ore information: contains iron, calcium, mica, and other impurities, so the feldspar ore dressing process including magnetic separation, flotation or gravity separation, so as to remove iron, mica and other impurities to obtain high-grade feldspar.
1. Crushing section: Utilize coarse jaw crusher, fine jaw crusher and vibrating screen to form a closed crushing circuit, so as to make 200mm rock ore down to 20mm.
2. Grinding section: Utilize ball mill and spiral classifier to form closed grinding circuit, so as to achieve more than 90% discharging size 200mesh(0.074mm).
3. Magnetic separation: Low intensity plate magnetic separator can remove magnetite(Fe3O4), and high intensity magnetic separation can remove hematite, limonite, ilmenite(Fe2O3)
4. Flotation separation: The flotation machine is used to remove impurities in the feldspar ore further, so as to obtain high-grade feldspar concentrate.
5. Dewatering process for concentrate: Use a slurry pump to send concentrate to the thickener, the overflow of thickener goes to a clear water pond, and the underflow goes to disc filer machine for dehydration. After being dehydrated by a disc filter machine, the moisture concentration is less than 10%.
6. Tailing dry discharging process: All tailings are first pumped to cone thickener for adjusting the suitable concentration, the overflow of cone thickener go to recycled clear water pond, and the underflow go to plate filter press for dehydration, finally the moisture of tailing is less than 10%, this is dry stacking tailings process.
2. feldspar Grinding + Magnetic Separation plant
The feldspar separation plant details equipment and process as follows:
Jaw crusher
- Ball mill
- Spiral classifier
- High-intensity magnetic separator
- Trommel scrubber
1. Crushing stage: The raw ore is roughly crushed by the jaw crusher, and then sent to the fine jaw crusher by the belt conveyor for secondary crushing. Thus, it makes sure the particle size of the material entering the grinding section is qualified;
2. Grinding stage: The crushed material enters the powder silo, and is sent to the ball mill and classifier to form closed-circuit grinding, and the coarse particles are returned to the ball mill for secondary grinding;
3. Magnetic separation: The material enters the high-intensity magnetic separator for separation. The trommel scrubber then washed the soil to obtain qualified feldspar powder, which is then transported to the finished product warehouse by the belt conveyor.
Contact Us Now
Please fill out the information below for the quotation price and engineer’s help. We will reply ASAP!
Notice:
- We do not recruit, don’t offer jobs, and are not interested in investments or partnerships.
- We provide mineral processing equipment and solutions; not buy and sell mineral /ore /materials.
- We value your privacy and keep your information safe.