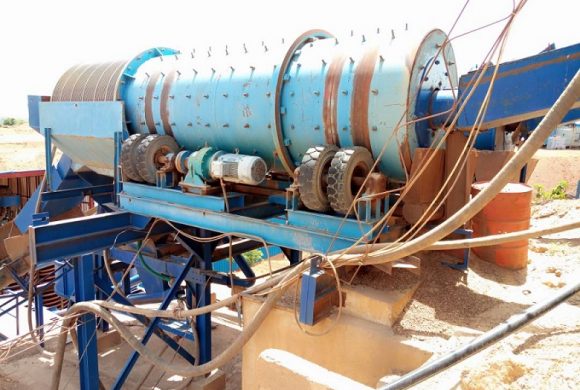
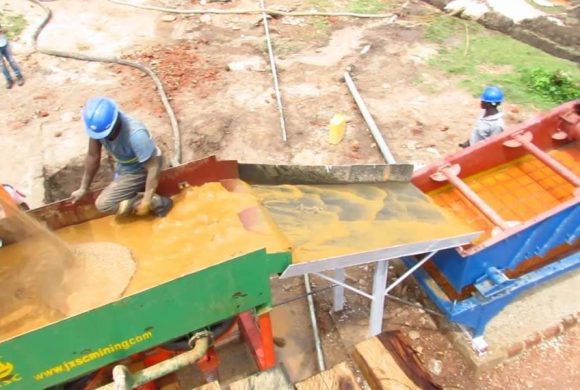
Tin Ore Processing
Tin(Cassiterite) ore processing refers to the process of extracting tin from ore. Gravity separation, magnetic separation and flotation are mainly used to grade tin concentrate and remove other impurities.
In order to achieve high efficient, low-cost beneficiation flow, JXSC will custom process and equipment according to ore characteristics.
Tin ore beneficiation process
The tin(Cassiterite) ore beneficiation plant can be main completed by crushing, screening, washing, gravity separation and magnetic separation. The specific process and equipment need to be determined according to the nature and characteristics of the ore.
1. Crushing and grinding: The original tin ore is crushed and ground to refine it into an appropriate particle size for subsequent sorting operations. Equipment such as jaw crushers and ball mills are usually used.
2. Beneficiation: Through the sorting operation, the tin ore after crushing and grinding is separated into ores of different grades and qualities. The commonly used sorting methods include gravity separation, flotation and magnetic separation.
- Gravity separation: use the density difference of different minerals in the ore to separate the ore by gravity.
- Flotation: Using the difference in hydrophilicity and hydrophobicity between ore and water, ore is separated by bubble adsorption and buoyancy.
- Magnetic separation: For tin ores containing magnetic minerals, using the sensitivity of certain minerals in ore to magnetism, magnetic minerals are separated from non-magnetic minerals through the action of a magnetic field.
- Electric separation: For tin ores containing minerals with different electrical properties, further separation of tin minerals can be achieved by adjusting the electric field strength, current density and processing time.
3. Concentration and dehydration: Concentration is carried out by thickening equipment to increase the solid content of the pulp, which is convenient for subsequent processing and transportation. It is then dehydrated to remove excess water. Commonly used dehydration equipment includes filters, filter presses, etc.
Tin ore processing plant
1. Alluvial Tin Ore Mining plant
This system is a fully set 120tph alluvial tin ore mining process plant setup:
- Vibrating feeder
- Trommel screen
- Belt conveyor
- Jig separator
- Shaking table
- Three discs magnetic separator
Raw ore conditions in this tin project are as follows:
- Raw ore doesn’t contain sticky clay, just alluvial loose soil;
- Tin concentrate size in alluvial ore is 0-5mm;
- The maximum feeding size of raw ore is 150mm;
- Feeding capacity is 120 tons per hour.
1. Use a high-pressure water gun to break up the raw materials on the vibrating feeder (with an 80mm grid). Material over 80mm will be removed and transported to the waste dump. Materials that meet the size enter the hopper through the vibrating feeder, and then enter the drum screen evenly.
2. The trommel screen has two layers of mesh. The inner mesh is a 30mm bar steel mesh, and the outer mesh is a manganese steel mesh with a pore size of 5mm. Among them, materials larger than 5mm are screened out and transported to the waste pile. Materials smaller than 5mm are pumped to the distributor together with sand.
3. Materials smaller than 5mm in the distributor enter 6 4m2 jig concentrators (15-20TPH) for primary separation of tin concentrate.
4. The tin concentrate comes from six 4m2 jigs and enters three 2m2 jigs (5-10TPH) by gravity to select the tin concentrate.
5. The tin concentrate in three 2m2 jigs enters six shaking tables by gravity, mainly to further refine the tin concentrate and improve the grade of the finished product.
6. The shaking table produces three outputs: tin concentrate, middlings and tailings. The medium may also contain some tin. In order to improve the recovery rate, all medium ore are sent to three shakers (second stage) for reprocessing.
7. All tin concentrates coming out of the shaking table are finished products, and their tailings enter the tailings pond.
8. After the tin concentrate is naturally dried, it is sent to a three-disk magnetic separator for dry separation to remove tin, iron, coltan and other weak magnetic minerals.
2. Hard Rock tin ore processing plant
This is a complete 5TPH rock tin ore processing plant process designed by JXSC. The details are as follows:
1.Crushing & Screening
There is a smaller hopper above the jaw crusher and a chute feeder below the hopper. The stone is evenly fed into the jaw crusher and then screened with a vibrating screen. Materials larger than 5mm enter the next double-roller crusher through the belt conveyor for fine crushing. The output materials will be transported to the vibrating screen for re-screening.
2.Gravity separation
Material smaller than 5 mm is conveyed to the jig. The concentrate <2mm below the screen of the jig separator is directly transported to the distribution tank by the slurry pump, and then enters the shaking table for separation to obtain high-grade tin concentrate.
3.Tailings processing
The customer requires the use of dewatering screens and the recovery of jig tailings water. The dehydrated waste sand is transported away by a belt conveyor.
Related Equipment
Contact Us Now
Please fill out the information below for the quotation price and engineer’s help. We will reply ASAP!
Notice:
- We do not provide jobs and have no interest in investment or partnerships.
- We provide mineral processing equipment and solutions; not buy and sell mineral /ore /materials.
- We value your privacy and keep your information safe.