Rock Crushing Equipment
Mineral Processing » Equipment » Crushing Equipment
JXSC is a leading manufacturer of rock crushing equipment. We provide fixed and mobile types rock crushers including jaw crushers, cone crushers, impact crushers, hammer crushers, roll crushers, VSI sand-making machines, glass bottle crushers, etc.
Rock crusher Application:
- Quarry stone crushing: cobblestone, basalt, limestone, granite, talc, river pebbles, dolomite, marble, quartz stone, etc.
- Mine rock ore crushing: iron ore, copper ore, gold, lead-zinc, coal, manganese ore, silica sand, etc.
- Solid waste recycling and crushing stage: tailings, slag, construction waste, etc.
Fixed Rock Crusher For Sale
Rock crushing equipment and crushers are essential for construction, mining and mineral processing. Its main function is to produce sand for road construction or concrete aggregate. It can crush various materials, including granite, limestone, basalt, river pebbles, gold ore, copper ore, and other stone or ore crushing plants. In addition to having quality and durable rock/stone crushers, JXSC manufacturers prioritize optimal customer service. Contact us for factory direct price!
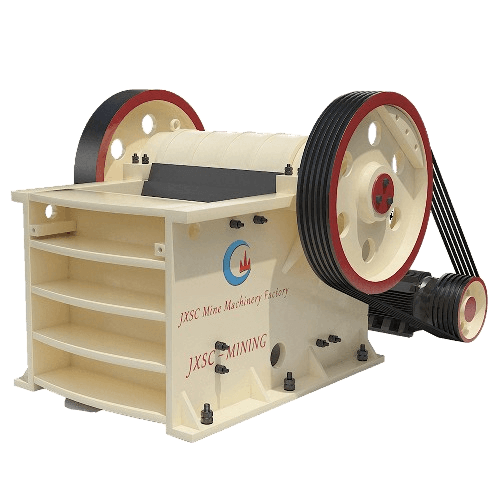
PE Jaw crusher
Capacity: 1-1120t/h
Feeding size: <1200mm
Application: Primary crushing, which is the first step coarse crushing in mineal processing.
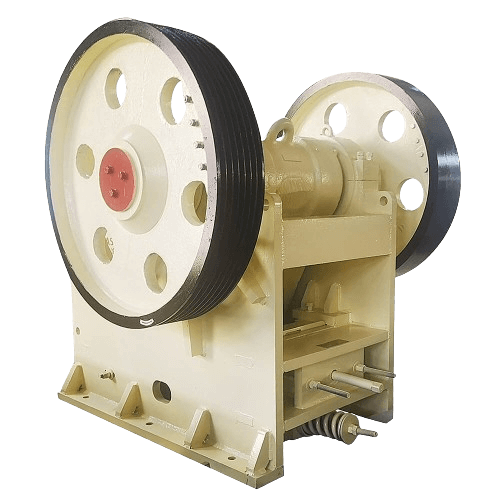
PEX jaw crusher
Capacity: 1-120t/h
Feeding size: <300mm
Application: Secondary crushing, medium crushing and fine crushing.
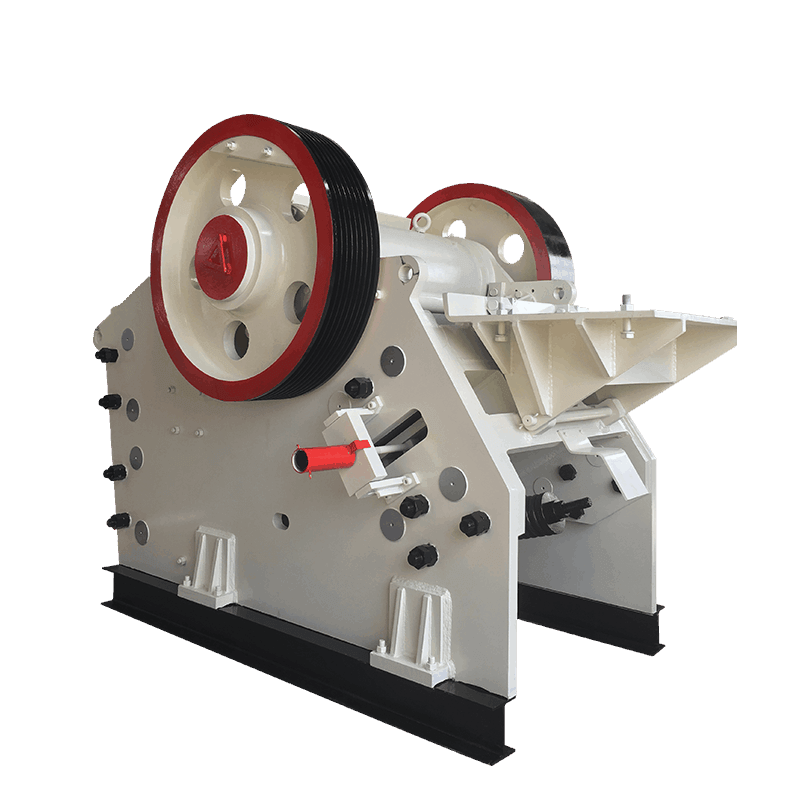
Eupropean type jaw crusher
Capacity: 55-675t/h
Feeding size: <150mm
Application: such as crushing rocks, ores, slag, concrete, construction waste, etc
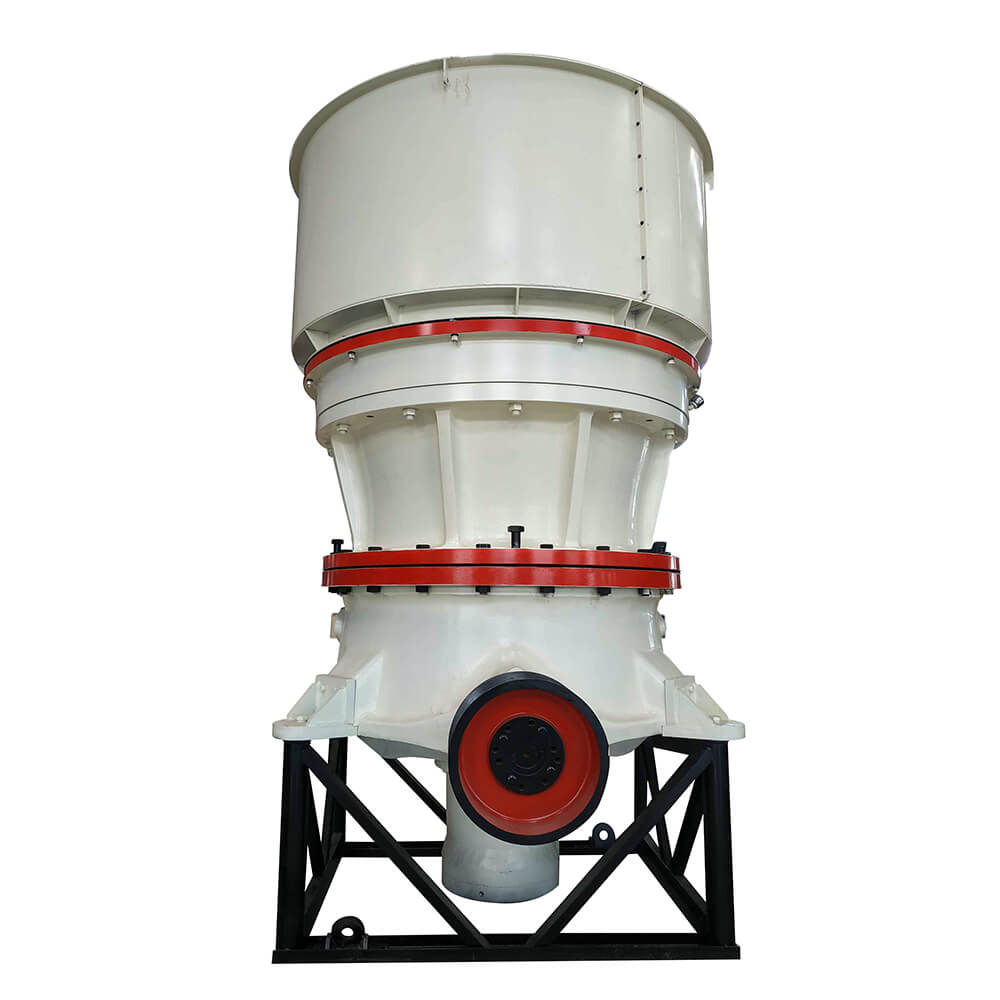
Single cylinder cone crusher
Capacity: 35-175t/h
Feeding size: <220mm
Application: Ideal for secondary and tertiary crushing applications.
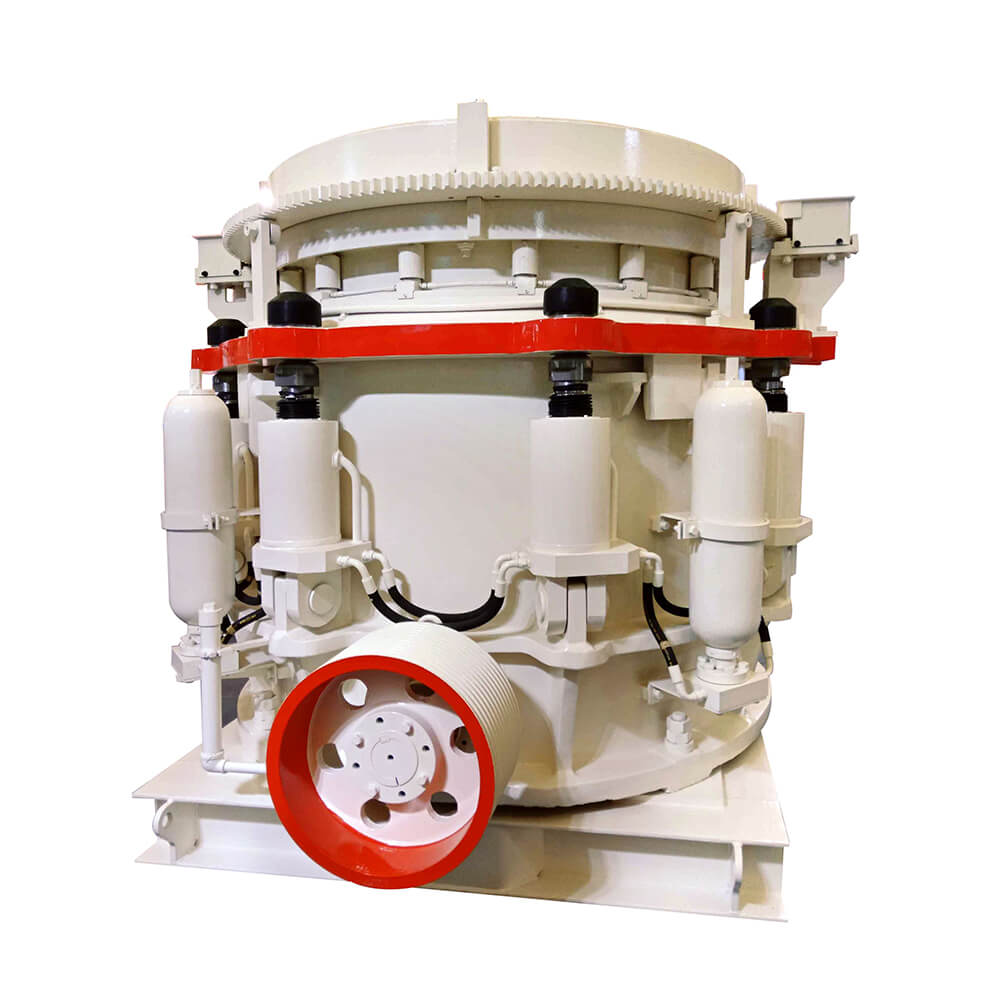
Multi-cylinder cone crusher
Capacity: 90-1200t/h
Feeding size: <353mm
Application: Excellent in crushing large-scale materials such as granite and basalt.
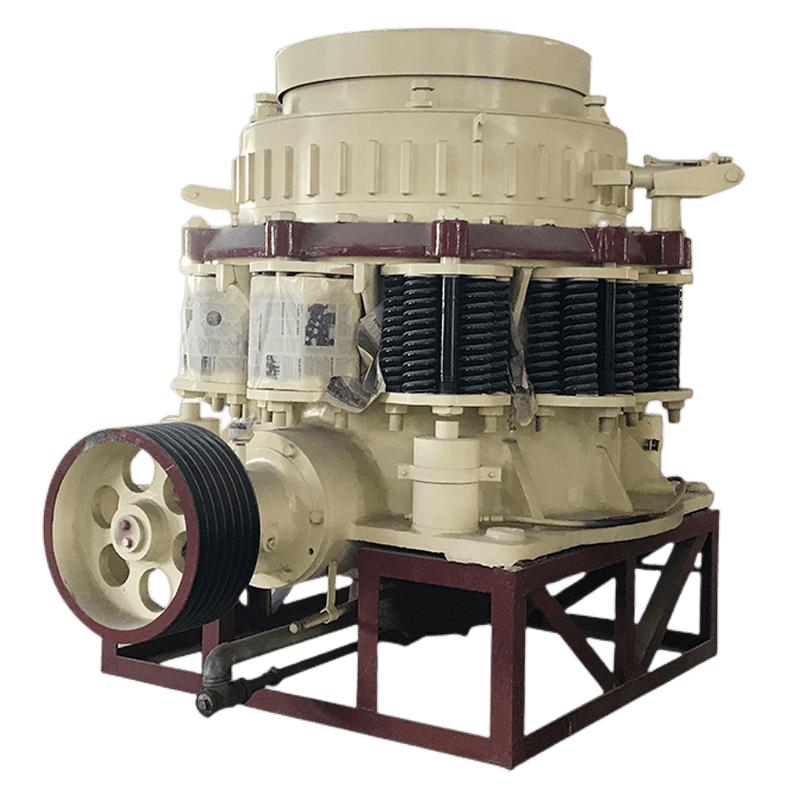
Symons cone crusher
Capacity: 27-1450t/h
Feeding size: <425mm
Application: Crushing materials ranging from hard rocks to ores and minerals.
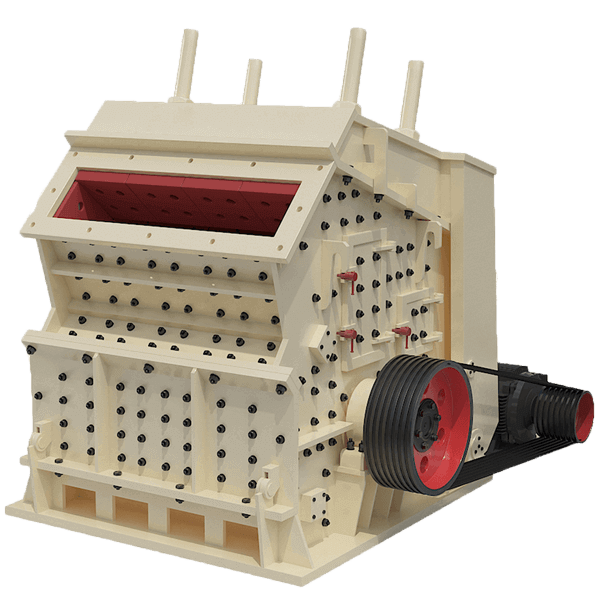
Impact Crusher
Capacity: 30-500t/h
Feeding size: <700mm
Application: Suitable for crushing medium hardness and low abrasive materials to produce coarse aggregate.
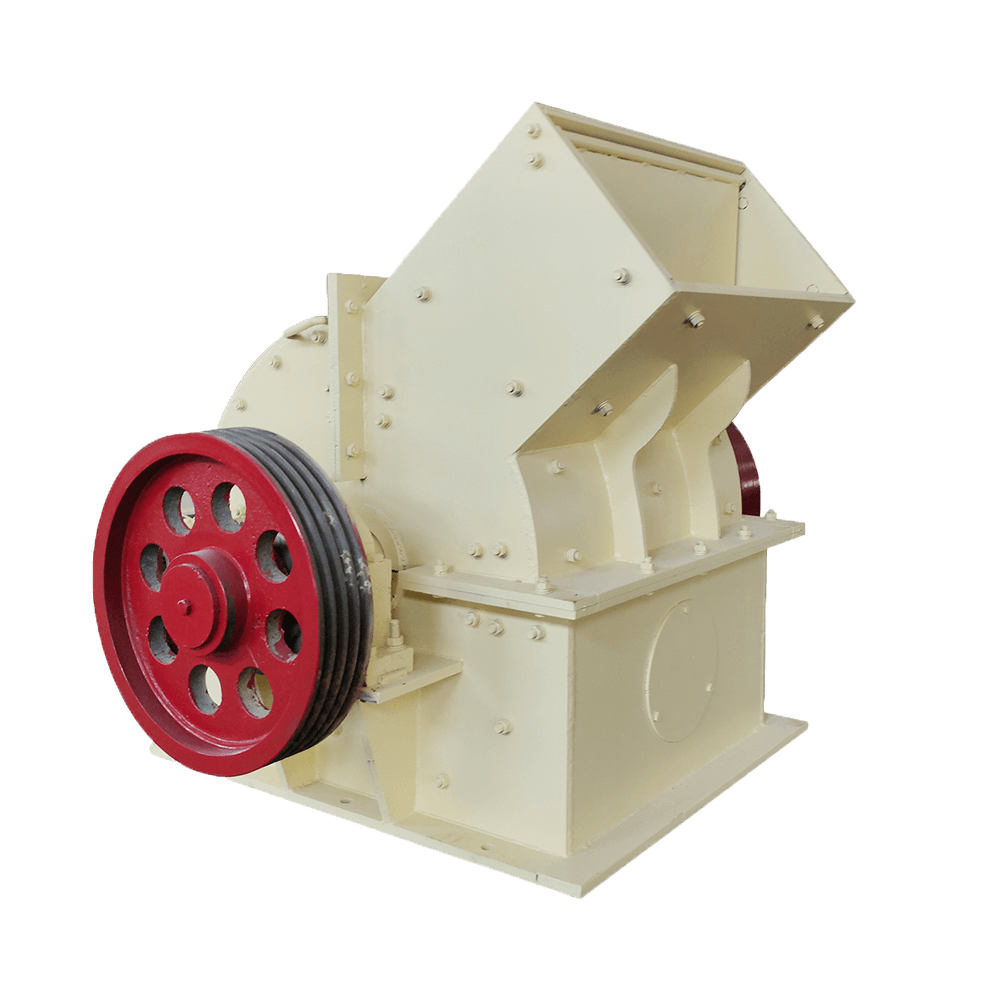
Hammer Crusher
Capacity: 1-110t/h
Feeding size: <10-35mm
Application: Suitable for crushing medium hard materials such as limestone, gold, copper, iron ore, marble.
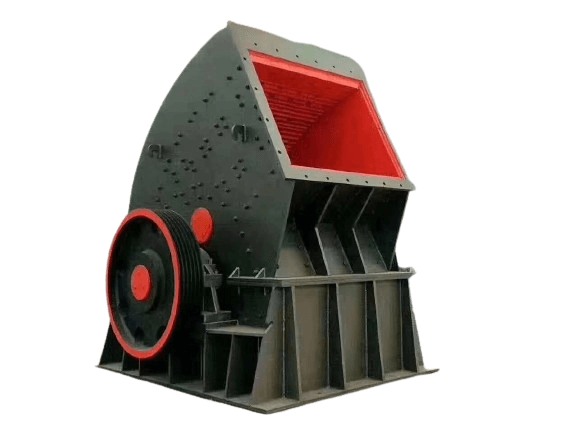
heavy hammer crusher
Capacity: 50-1200t/h
Feeding size: <400-1200mm
Application: Capable of crushing highly abrasive materials with high moisture content, such as granite and quartz.
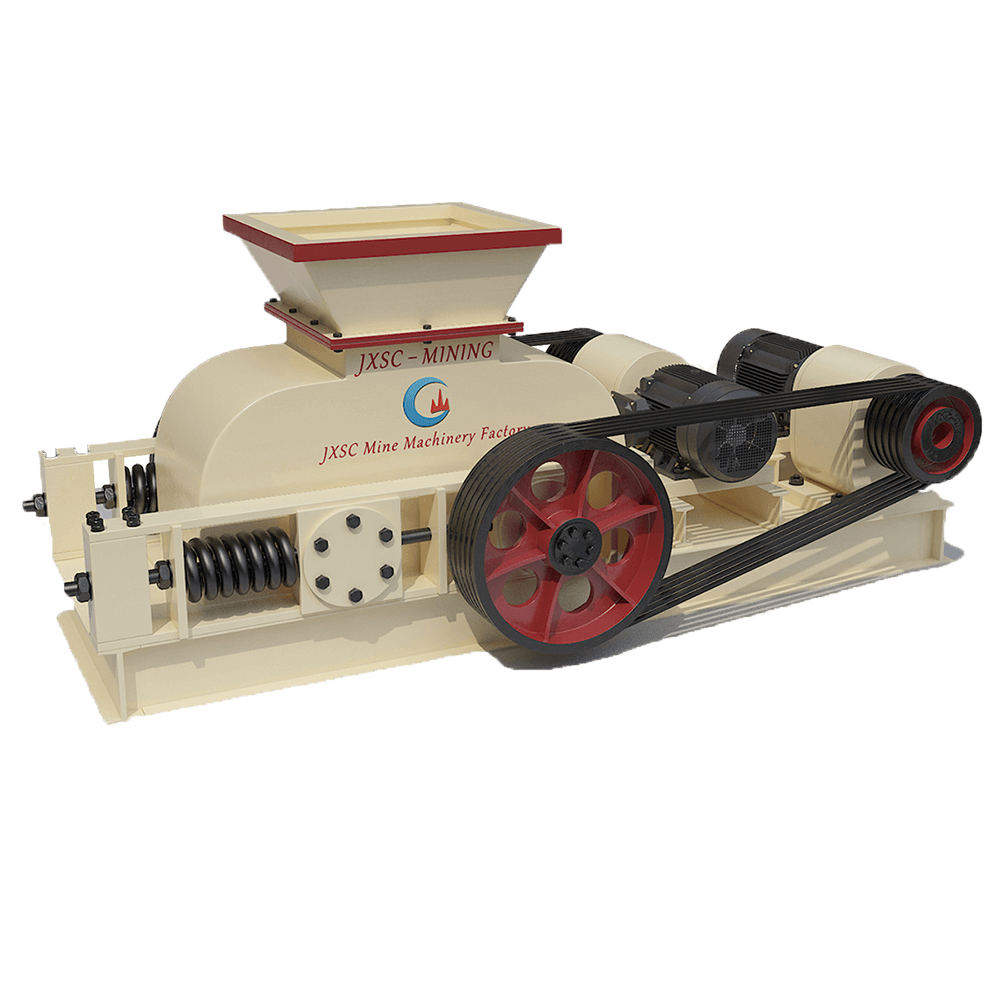
Spring roller crusher
Capacity: 1.5-70t/h
Application: Suitable for crushing medium to hard materials such as coal and limestone.
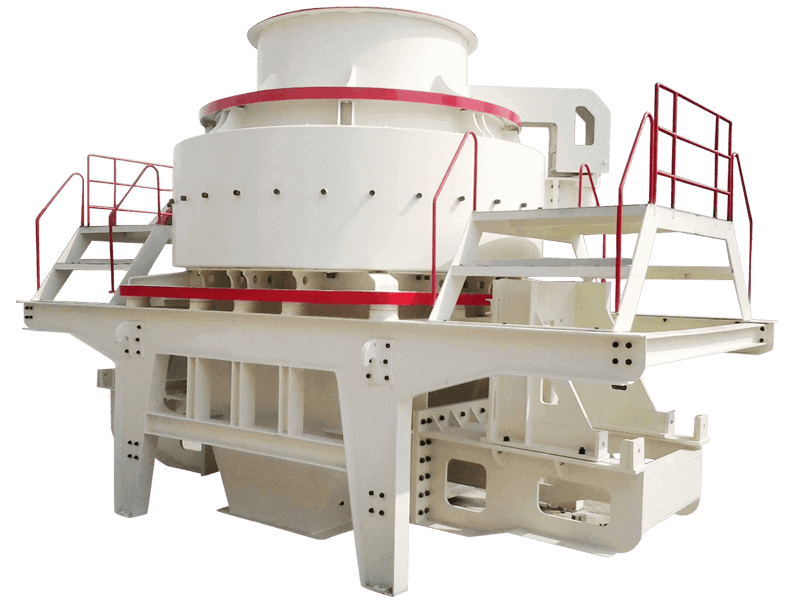
VSI Sand Making Machine
Capacity: 20-180m³
Application: Produce high quality sand for construction projects: hard and abrasive materials such as granite, basalt, iron ore; limestone and river pebbles.
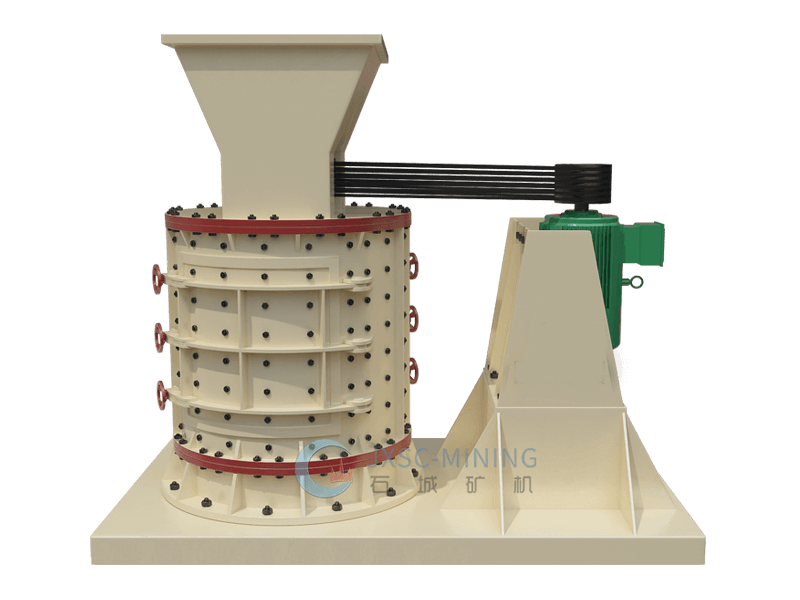
vertical shaft compound crusher
Capacity: 5-200t/h
Application: Crush various types of hard and abrasive rocks, and can effectively crush and shape limestone, coal, quartz, granite.
Mobile Crusher For Sale
We also provide mobile/portable stone crushers. They are divided into wheel-type and crawler-type crushing plants, including mobile jaw crushers, cone crushers, impact crushers, vibrating screens, etc. The equipment provides efficient, low-cost. Usually the jaw crusher can be equipped with a vibrating screen or a belt conveyor to form a small portable crushing plant. It also supports customized mobile jaw crushers, impact crushers, cone crushers, sand making machines, etc.
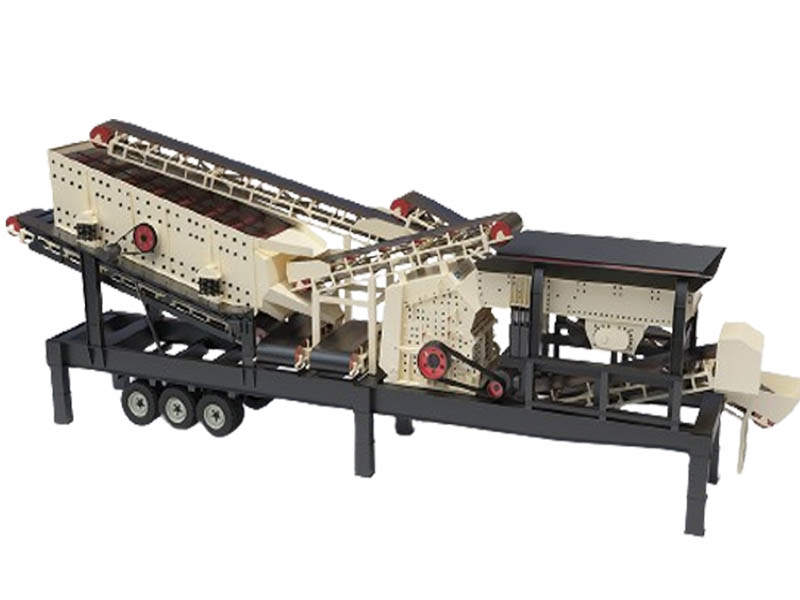
Mobile Crusher
Capacity: 1-450 t/h or customizable
Main equipment: vibrating feeder + rock crusher + vibrating screen
Application: It is widely used in mining crushing plants, sand-making production, and construction waste recycling.
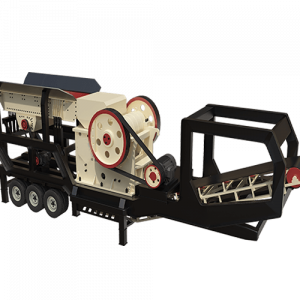
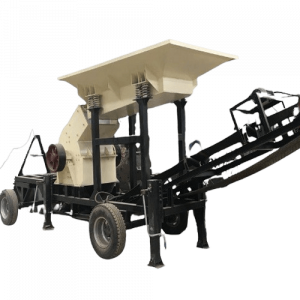
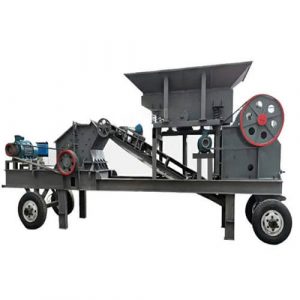
Why Choose JXSC Rock Crushing Equipment
- Highly automated design
- High efficiency production
- Wide range of applications
- High strength and durability
- Controllable and flexible
- Low energy, Large capacity
- High-precision Crushing
- Factory Price & Customizable
Related Products
Contact Us Now
Please fill out the information below for the quotation price and engineer’s help. We will reply ASAP!
Notice:
- We do not provide jobs and have no interest in investment or partnerships.
- We provide mineral processing equipment and solutions; not buy and sell mineral /ore /materials.
- We value your privacy and keep your information safe.