Mining Dewatering Equipment
In mineral processing flow, the concentrates and tailings produced by different of treating methods must be dewatered, so these pulps products can convert to a transportable state. We provides mining and mineral dewatering machines including dewatering screen, thickener, rotary dryer, filter press, disc vacuum filter, belt pressure filter, etc.
Mining Dewatering Equipment for sale
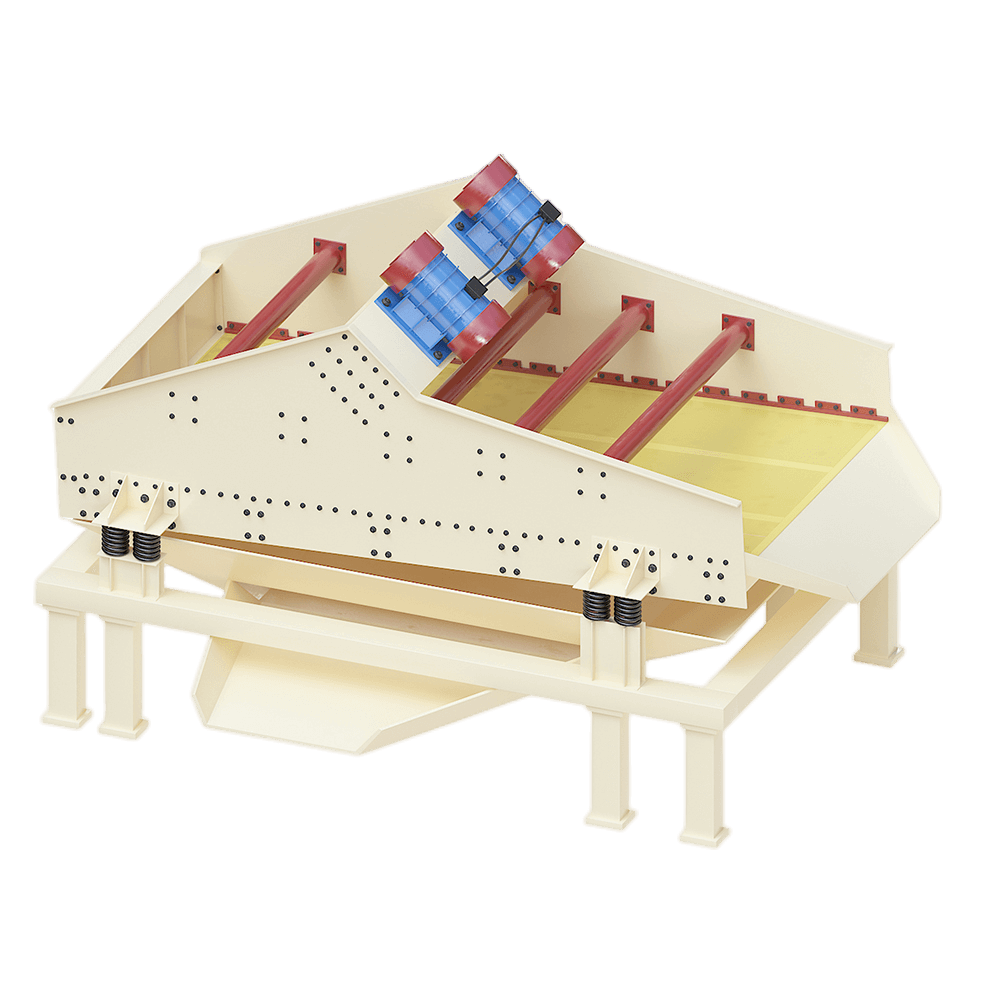
Dewatering screen
Capacity: customizable, 5-250 tph
screen sieve
Material: PU, PE, and others materials
Screen size: 1.6–10.8 mm
Advantages:
high dewatering rate, low noise
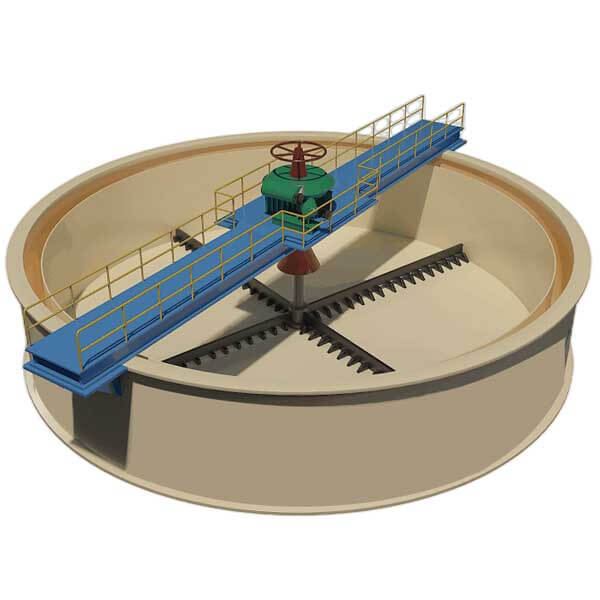
Thickener
Capacity: 1.3-1140 t/24h
Application: dewatering process of concentrates and tailings in the mineral processing plant. It is specifically designed for the beneficiation industry and tailing processing.
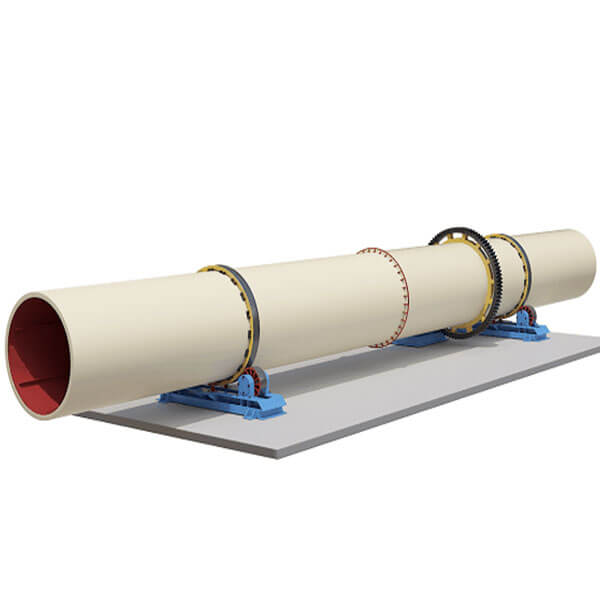
Rotary dryer
Capacity: 0.8-40 tons/hour
Suitable materials: drying powder, lump, granular materials such as coal slime, ore powder, slag, sludge, clay, fly ash, etc.
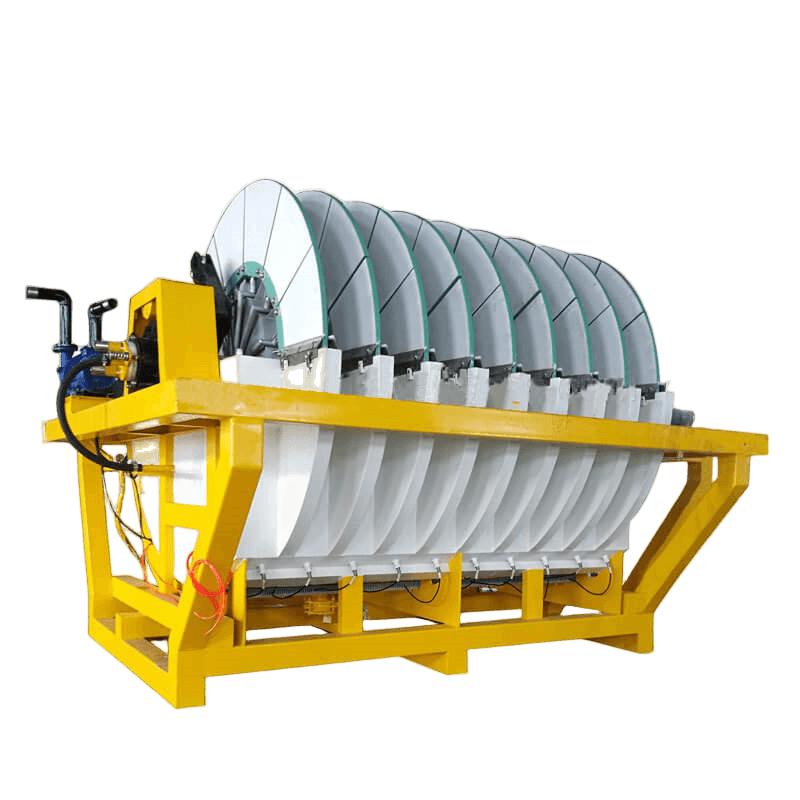
Disc Vacuum Filter
Capacity: 0.85-1.2 t/h·m² (Different material processing capacity is different)
Application: It is suitable for fine material filtration and dehydration of fine tailings and non-ferrous metal concentrates in mineral processing plants, etc.
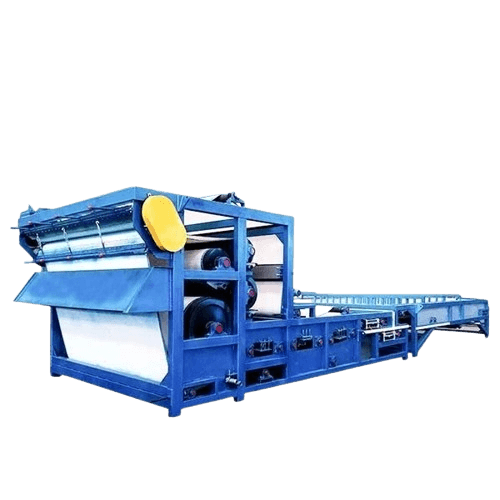
Belt pressure filter
Capacity: 0.5-30TPH
Slurry feed concentration: 3-8%
Application: dehydration and solid-liquid separation operations such as tailings mud, mineral processing wastewater, sand washing mud, sand plant sludge, etc.
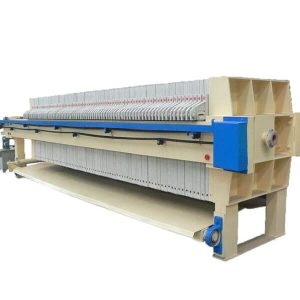
plate Filter press
Filter area: 50-500 m²
Cake thickness: 30 mm
Application: Dehydration of sludge in sewage treatment plants; used to separate solid minerals and water in slurry, such as gold, coltan, tin, tungsten, iron tailings processing.
Contact Us Now
Ask us about mineral processing configuration and equipment quote! (No job, No investment)
Notice:
- We only provide mineral processing equipment and solutions; not buy and sell minerals/ ores/ materials.
- We do not recruit, don’t offer jobs, and are not interested in investments or partnerships.
- We value your privacy and keep your information safe.