In recent years, the demand for high-quality sand has increased significantly due to the widespread use of high-quality sand in various industries such as construction, glass manufacturing, and water treatment. Therefore, sand washing plants are essential to produce clean and usable sand. However, traditional sand washing processes often need to improve in effectively separating impurities in sand grains.
The main function of the sand washing plant is to remove impurities in the sand and improve its quality for different applications. One of the key steps in the process is magnetic separation. Therefore, the high-efficiency magnetic separation process has become a promising solution in sand washing plants. This innovative method uses powerful magnets to attract and extract iron-bearing minerals and other magnetic particles from a mixture of raw materials. By integrating this process into their operations, sand making plant operators can achieve superior levels of purification while maximizing product capacity.
Magnetic Separation Importance In sand Washing Plant
In traditional magnetic separation methods, weak magnets attract and separate iron particles from sand. However, this approach could be more efficient due to insufficient magnet power. The magnetic separation process helps improve the quality of the final product by removing unwanted contaminants such as clay, silt and other organic matter. By implementing a highly efficient magnetic separation process, sand washing plants can significantly increase production and reduce water consumption.
- Improve the quality of sand and gravel: The magnetic separation process can effectively remove iron minerals, magnetic impurities and other substances containing metal elements in the sand and gravel. These impurities reduce the quality of the sand and may negatively affect subsequent use. Through magnetic separation, the purity and quality of sand can be greatly improved.
- Increase the added value of products: magnetic separation can separate valuable magnetic minerals (such as iron ore) in sand and gravel, and these minerals can be sold as independent products or further processed and utilized. By extracting magnetic minerals, sand washing plants can increase the added value of products, thereby increasing profits.
- Reduce environmental impact: Magnetic separation is a physical separation process that does not require chemicals or other pollutants. Compared with other treatment processes (such as flotation, chemical treatment, etc.), the magnetic separation process has less impact on the environment, which helps to reduce the discharge of wastewater and waste and protect the environment.
- Improve production efficiency: The magnetic separation process can realize automatic operation with high efficiency and rapidity. It can quickly separate magnetic impurities and automatically collect and remove them, reducing manual operation and processing time. This can greatly improve the production efficiency of the sand washing plant and reduce production costs.
- Reduce equipment wear: Magnetic separation can effectively remove metal impurities in sand and gravel, avoiding equipment wear and damage by metal particles. Metallic impurities can lead to equipment failure, increased downtime and repair costs. Through the magnetic separation process, these problems can be reduced and the service life of the equipment can be extended.
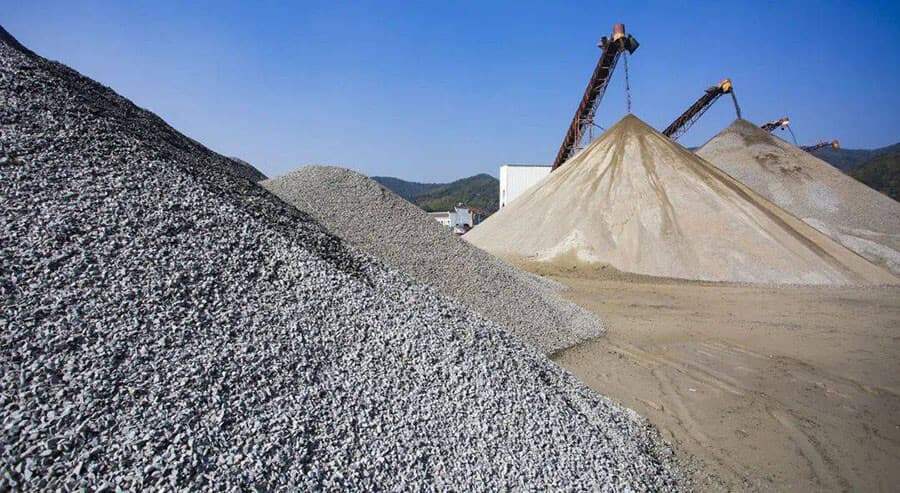
Sand Washing Plant
The magnetic separation process of the sand washing plant separates the sand containing ferromagnetic substances through magnetic separation equipment. The following are the main steps of the magnetic separation process in sand washing plant:
- Crushing: The original sand ore is preliminarily crushed through crushing equipment (such as jaw crusher, cone crusher, etc.) so that the particle size is suitable for subsequent magnetic separation equipment.
- Washing: Send the crushed sand ore to washing equipment (such as sand washing machine, screening machine, etc.), and remove the soil, impurities and other non-magnetic substances through the washing and screening of water flow to obtain magnetic Sand mines of minerals.
- Magnetic separation: Transport the washed sand ore to magnetic separation equipment, usually using a magnetic separators. A strong magnetic field is set inside the magnetic separator, and the magnetic minerals are attracted to the magnetic roller or plate by the magnetic force’s action, while the non-magnetic substances are excluded.
- Separation: After magnetic separation, magnetic minerals are separated to form magnetic separation products. The grade and recovery rate of magnetic separation products can be controlled by adjusting the magnetic roller or magnetic plate.
- Iron removal: Since some iron impurities may be adsorbed together during the magnetic separation process after the magnetic separation, the product must be iron-removed to remove iron impurities and improve the ore quality.
The specific process may vary due to different ore properties and process requirements, so in practical applications, certain adjustments and improvements may be made to the process.
Using magnetic separation in sand washing plants can improve product quality, purity and production efficiency, while achieving resource recovery and environmental protection. These advantages make magnetic separation a commonly used process in sand washing plants. It effectively removes unwanted iron particles from the sand, improving the final product’s quality and purity. This not only improves the overall performance of the sand in various applications, it also reduces the risk of contamination and increases the efficiency of downstream processes. JXSC sand washing plant can significantly improve the purity of ore sand, with zero discharge, no waste, no pollution, high production capacity, and low unit energy consumption. Please contact us online sustom sand washing plant including silica sand, beach sand, kaolin,etc. It also can be applied to various large-scale sand making production lines.