Centrifugal concentrators are often associated with efficiently separating fine particles of minerals, making them valuable tools in mining and mineral processing. Not only does it provide an efficient and cost-effective way to recycle fine gold particles, but it also provides a sustainable solution to minimize environmental impact. It is capable of handling large amounts of material while maintaining high efficiency.
However, many may not realize that centrifugal concentrators can also effectively separate tailings – the waste material left after extracting the desired minerals. This breakthrough enables mining operations to minimize waste and recover added value from tailings. Using centrifugal concentrators to separate tailings, mining companies can extract any remaining traces of valuable minerals from the waste before discarding them. Not only does this reduce environmental impact by minimizing the amount of waste material, but it also provides potential economic benefits by maximizing resource recovery. Additionally, using centrifugal concentrators to separate tailings helps improve water management practices at mine sites because it reduces the amount of material that needs to be stored and disposed of.
Introduction and application of centrifugal concentrator
Centrifugal concentrators are often key equipment in the mining industry, using centrifugal force to separate and concentrate valuable minerals from other substances. It can efficiently process large quantities of ore and recover fine particles. Its high efficiency and continuous operation capabilities make it a cost-effective solution for mineral processing plants, especially gold processing plants. The centrifugal concentrator uses centrifugal force to concentrate heavy materials, allowing for higher recovery rates and reduced chemical use compared to traditional methods such as cyanide leaching or amalgamation.
Application: Tailings centrifuge also has a wide range of applications. It can recover heavy metals in tailings and separate light and heavy metals. Tailings with differences in specific gravity can be separated and enriched. It can be recycled for precious metals with high enrichment ratios. It’s widely used in tin, gold, lead-zinc, or other tailings plants. The centrifuge is placed in front of the flotation machine on the production lines of many mineral processing plants. It is now more popular. The tailings centrifuge is placed before the flotation machine to recover single and wrapped heavy metals with high specific gravity differences. The effect is good; the recovery rate is high.
Working Principle
The centrifugal acceleration generated by the drum rotation is basically to dozens of times the acceleration due to gravity, which strengthens the gravity separation process, so it is an efficient fine-grained tailings gold separation equipment. During operation, the drum rotates at a certain speed, and the slurry is fed into the inner wall of the drum through the ore feeding device. When the slurry rotates at high speed with the drum, the higher-density mineral particles are subjected to a large centrifugal force. They are eventually deposited on the inner wall of the drum to rotate with them. In contrast, the lighter particles are pushed to the outer wall and rotate at a certain helix angle during the rotation. It moves from the feeding end to the ore discharge end along the slope of the drum and is finally discharged into tailings. On the other hand, heavier particles move towards the center, resulting in efficient separation.
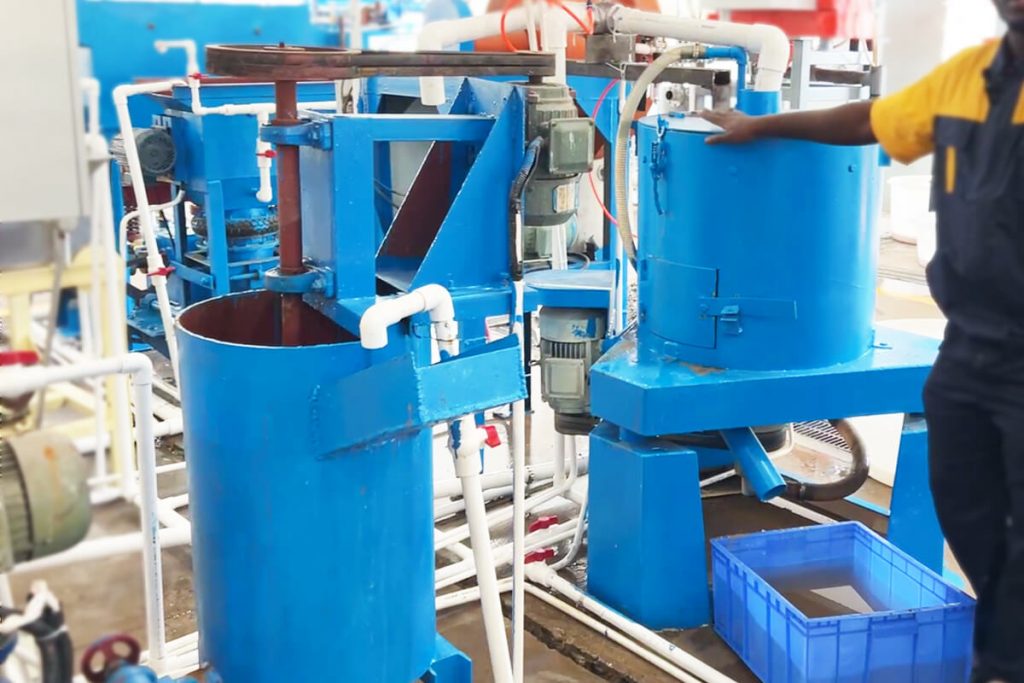
The importance of tailings reseparation
Tailings separation presents several challenges that require innovative solutions for effective management. The main challenge lies in the complex composition of tailings, which often contain a mixture of fine particles and chemical compounds. It makes it difficult to separate valuable minerals from the waste, leading to environmental problems and resource waste. Among them, the large amounts of tailings generated by mining operations increase the difficulty of efficient separation processes. Also, proper tailings separation can contribute to sustainable mining practices by mitigating the long-term environmental liabilities of improperly managed mine waste.
However, introducing centrifugal concentrators revolutionized this process by providing a more efficient and cost-effective solution. Using centrifugal force to separate valuable minerals from less desirable components quickly makes the extraction process more precise and thorough, significantly reducing the amount of useful material lost in tailings. It can handle various granularities from fine to coarse without compromising efficiency. Furthermore, with its compact design and minimal energy requirements, centrifugal concentrators offer a sustainable solution for processing tailings while minimizing environmental impact.
Centrifugal concentrator for separating gold tailings
Centrifugal concentrators have become an integral part of the gold mining industry, particularly in separating gold tailings streams. These highly efficient machines use centrifugal force to separate particles based on density, making them ideal for processing and recovering fine gold particles from tailings.
- First, after the ore is crushed and ground, the material reaches a certain size of fine particles. Usually, they can also be put into a mixing barrel to mix the tailings and water evenly into a slurry and then sent to the centrifugal concentrator. Here, high-speed rotation forces heavier particles, such as gold, outward toward the walls, while lighter particles are pushed toward the center. This separation mechanism effectively concentrates gold from surrounding waste materials.
- As the concentrated gold particles gather at the periphery of the concentrator, precise regulation and control mechanisms ensure that only pure gold remains while impurities are discharged. The final step involves further processing to extract pure gold from this concentrated material.
The centrifugal concentrator separation method uses advanced technology and optimized operating parameters to provide an efficient solution for recovering valuable gold from tailings, with environmental and economic benefits. Separating gold tailings using centrifugal concentrators combines innovative engineering with strategic processing steps to achieve maximum extraction efficiency. This approach facilitates responsible waste management and brings new opportunities for sustainable resource use in mining operations.
Centrifugal concentrators can effectively separate valuable minerals from tailings. When the equipment rotates at high speed, it generates a large centrifugal force, strengthening the gravity selection process and enabling better recovery of fine mineral particles. Its presentation successfully handles the full recovery of fine particles, and therefore, it is now widely used to separate tungsten, tin, iron, and other ore slime tailings. Each type of tailings has different properties. JXSC tailings-specific centrifuge is used in various processing plants. It is best to choose according to the situation of the tailings.