Lead-zinc ore is a polymetallic mineral rich in elemental lead and zinc, mainly in lead-zinc sulfide and lead-zinc oxide ore. Among them, lead-zinc sulfide ore is an easy-to-select ore; lead-zinc oxide ore is a difficult-to-select ore. Due to the increasing global demand for lead-zinc mineral resources, both lead-zinc ores are valuable for mining.
In the mineral processing, lead-zinc ores are mainly flotation methods. According to the selectivity of the ore, the flotation methods of lead-zinc sulfide ores and oxide lead-zinc ores are different. At present, lead and zinc are mostly obtained through sulfide separation. However, with the development and utilization of resources, the easily separated lead-zinc sulfide ore resources are gradually depleted, and the mining of lead-zinc oxide ores is gradually eliminated.
Compared with lead-zinc sulfide ore proceesing, lead-zinc oxide ore has a more complex composition, more associated minerals, finer embedded particle size, is prone to produce slime, and contains a large amount of soluble salts. Many reasons lead to difficulties in the flotation treatment of lead-zinc oxide ores.
Lead-zinc Sulfide Ore Flotation
In the beneficiation process, the sulfide lead-zinc ore is mainly flotation. Among them, the proportion of zinc ore in most lead-zinc ore is higher than that of lead ore. Therefore, the “suppressing zinc and floating lead” method is generally adopted in the actual process. The common flotation processes of lead-zinc sulfide ore are mainly priority flotation, mixed flotation, equal flotation, fractional-speed branch flotation, and separation potential flotation.
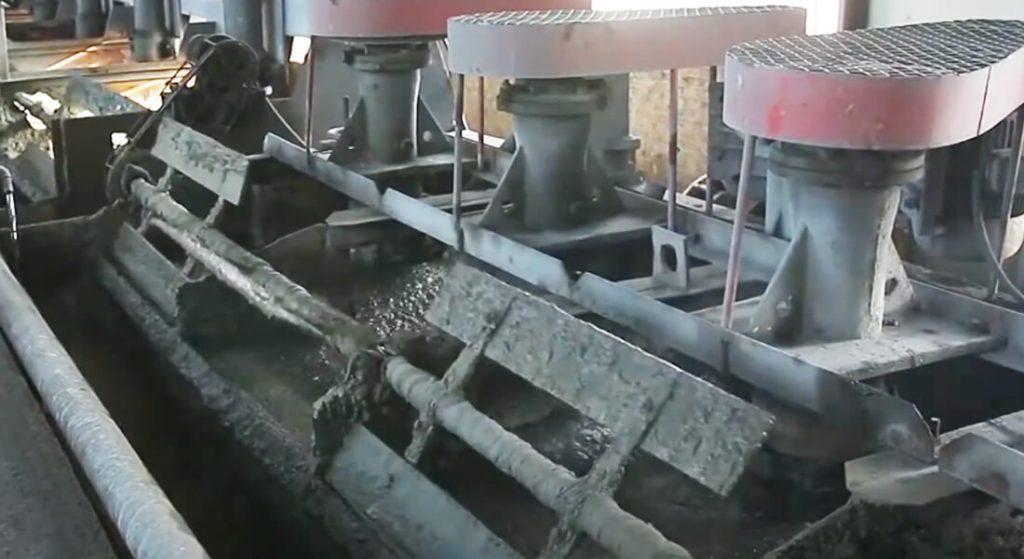
Lead-zinc Sulfide Ore Flotation
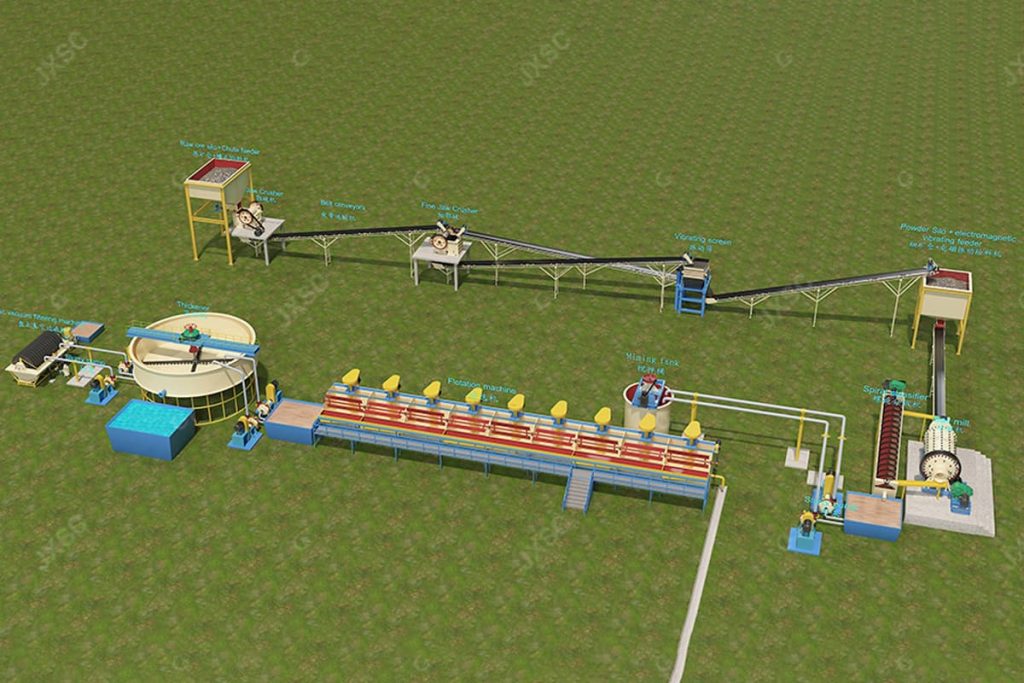
This setup is sulfide rock lead-zinc processing plant , suitable for processing Sulfide rock Gold, Copper, Silver, Zinc, Lead, Fluorite ore,ect. Has high recovery ratio for sulfide type minerals. Usually can reach about 85-90% depends on material conditions.
Complete plant mainly include material feeding hopper, chute feeder, Primary Jaw crusher, fine jaw crusher, vibration screen, belt conveyor, vibration feeder, storage bin, Ball mill, spiral classifier, mixing tank, flotation machine, slurry pump, thickener , disc vacuum filter machine.
Full processing plant includes four system:
–Crushing System: Chute feeder is for feeding raw material to primary jaw crusher stably and evenly, it can feed 0-300mm materials, if bigger size and capacity , can use grizzly vibration feeder. Then primary jaw crusher crush large ore to smaller size, about 0-80mm. Output send to fine jaw crusher to crush again to below 25mm particles. But there still has some +25mm particles , so better send to vibration screen to sieving out 0-25mm go to ball mill grinding system.and +25mm go back to fine crushing again.
The feeding size of ball mill can be smaller , the smaller ,the better, grinding efficiency will much higher. So sometimes , will have 3 stages crusher in crushing system to make smaller feeding size for ball mill (0-5mm or 0-8mm or 0-10mm).
–Grinding System: the 0-25mm material will firstly go to a storage bin before feed to ball mill, so the crushing system can work separated from grinding system as long as has stock enough 0-25mm in storage bin. Then feed the 0-25mm material by swing feeder or electromagnetic vibration feeder to ball mill through belt conveyor. The ball mill is for grinding material to small fine powder, because flotation process need 200mesh material, need work together with spiral classifer to reach 200mesh output from overflow of classifier, the underflow coarse particles will go back to ball mill grind again, to be closed-circuit. So from this grinding system will get 200mesh slurry.
-Flotation System: the 200mesh slurry will be firstly sent to mixing tank by slurry pump ,to make sure material is mixed completely, then from mixing tank go to flotation machines, need to add different chemicals in flotation machine to separate out different minerals, the flotation process has primary selection, secondary selection and final selection, this is for increase minerals grade to maximum after process. If need higher grade, then need to flotate more times. Will get each minerals concentrate ore after flotation system.
-Concentrate ore filtering system: after get the minerals concentrate ore from flotation system, for the high grade minerals, such as copper, fluorite, use the thickener to concentrate, make higher density, then send to disc vacuum filter machine to filter water, and get more dry concentrate minerals. Then can dry in the sun or by drying machine to get complete dry minerals concentrate ore.
This sulfide ore flotation processing plant is high effective to recovery sulfide minerals, suitable for processing Sulfide rock gold, copper, fluorite ore, etc. The plant design can be customized as per rock minerals conditions, capacity can be small,medium and big as per request.
Lead-zinc sulfide ore flotation regulator
One of the most critical aspects of lead-zinc sulfide ore processing is using flotation reagents to separate the valuable minerals from the gangue effectively. Three key reagents that play an essential role in this process are xanthate, dithiophosphate, and thiocarbamate.
- Xanthate is widely used due to its strong ability to capture sulfide minerals, especially lead and zinc.
- Meanwhile, dithiophosphates are effective in selectively promoting the flotation of lead minerals relative to zinc.
- Finally, thiocarbamates have excellent selectivity for zinc minerals compared to lead and are particularly suitable for reducing the zinc content in the final concentrate.
When applied strategically in lead-zinc sulfide ore processing, these three flotation agents have distinct advantages. Their different affinities for specific mineral components allow for precise control of separation efficiency, resulting in higher-quality concentrates and increased overall recovery. By understanding these reagents’ unique properties and behavior, mineral processing engineers can tailor their use to optimize flotation performance while reducing cost and environmental impact.
The flotation process of lead-zinc sulfide ores provides a promising method for extracting valuable metals from complex ore deposits. By using a variety of reagents and flotation techniques, high recoveries and concentrate grades can be achieved. JXSC supports customized lead-zinc ore processing plants and equipment, contact our professional engineers for consultation and quotation!