What is heavy minerals
Heavy minerals usually refer to minerals with a density greater than a certain threshold (2.89 or 2.90g/cm3) in sediments. These refer to rocks or ores that have been weathered and have relatively high density. Heavy minerals usually accumulate in the sandy layers of nearby riverbeds, lakeshores, and beaches. Industries such as mining and mineral processing rely on these minerals for a variety of applications, including construction materials, electronics, and even cosmetics.
The high density of these minerals makes them stand out compared to surrounding materials. It mainly contains ilmenite, zircon, rutile, garnet, tourmaline, monazite, etc. These minerals are commonly found in sand, but usually in low amounts (less than 1%). Sometimes, it’s concentrated on beaches or river bottoms, forming beautiful and unusual sand patterns. The composition of these sand samples varies widely. The most common components are garnet, magnetite, ilmenite, and epidote; most heavy mineral sand samples also contain quartz. Many heavy mineral sands are of great economic value and can be beneficiated to meet industrial requirements.
Analysis of gravity separation
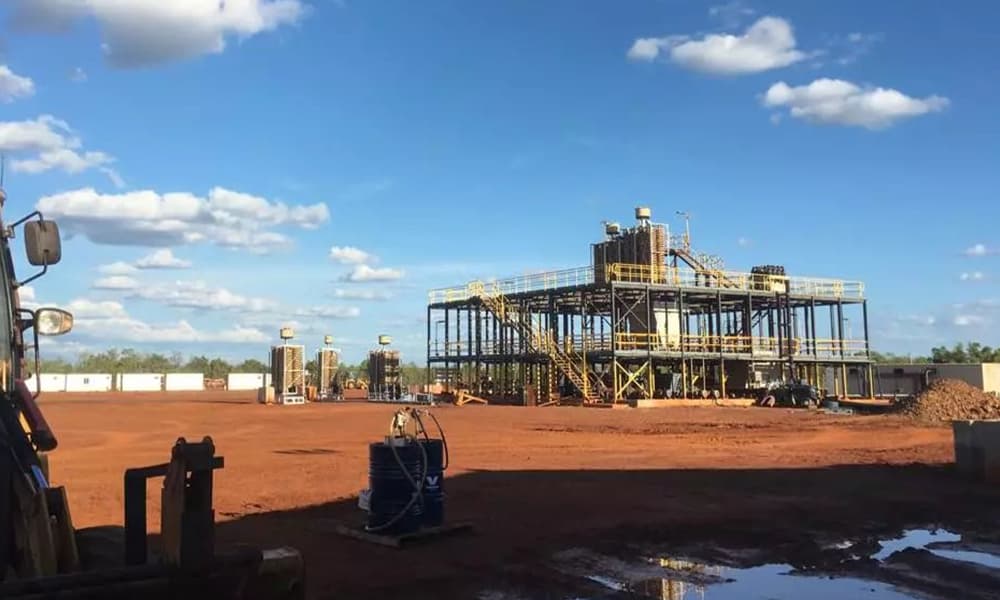
Gravity beneficiation process is a method to achieve separation based on differences in particle density and sedimentation speeds under gravity. Compared with other separation methods, such as flotation or magnetic separation, gravity separation can effectively concentrate heavy minerals such as zircon, rutile, and ilmenite by taking advantage of the difference in specific gravity between particles. It mainly selects and optimizes feed volume, particle size distribution, and slurry concentration parameters. Operators can achieve high recovery rates and product quality by carefully controlling these variables. Provides a cost-effective and environmentally friendly process for separating valuable minerals from waste materials.
Heavy minerals usually include ilmenite, zircon, rutile, garnet, mica, and tourmaline. Their density is greater than that of light minerals. To extract these heavy minerals efficiently, we need to use a gravity separation equipment process.
Heavy mineral gravity separation process
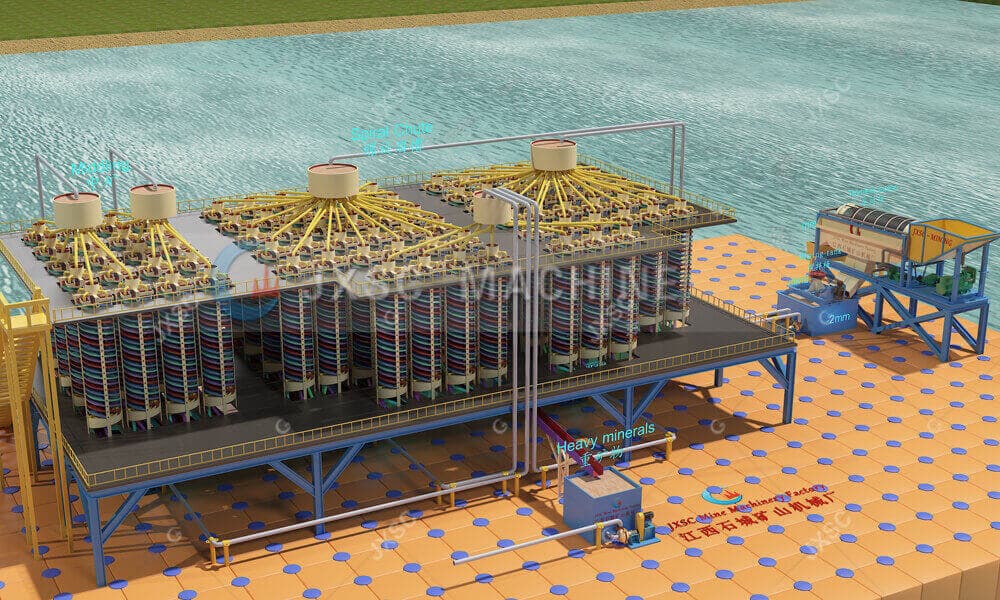
180TPH heavy mineral concentrate (HMC) process plant
Mineral information:
Raw materials: Mainly sand, with extremely low heavy mineral content, about 1% HMC (heavy mineral concentrate). Its breakdown is as follows: 68% ilmenite, 15% zircon, 2.5% rutile, 1.5% leukodiene; feed size range is 0.3 to 0.03 mm.
According to the mineral information provided by the customer and the requirement of reaching 180t/h, the entire device is also required to be installed on a steel structure floating working platform (the platform is prepared and built by the customer). Finally, based on the customer’s specific requirements and information, JXSC specially designed a set of heavy mineral separation plant, flow and equipment for this purpose. It mainly includes trommel screen, spiral chute, slurry pump, slurry tank and distribution tank.
The specific process is as follows:
1. First, use a dredging pump to transport the slurryto the trommel screen hopper. The slurrydensity should be about 25-30%. The slurry pressure (flow rate) should be a manageable size.
2. The drum screen, with its 2mm mesh screen, plays a crucial role in removing waste sand larger than 2mm and discharging it directly to the nearby area. However, 0-2mm slurryfirst enters the mixing tank (2000*1500mm). Because the slurryflow rate of the trommel screen is large, the slurry needs to be stirred before being sent to the first-stage spiral group. This understanding of the equipment’s parameters empowers you to ensure efficient operation. After this, the solid materials in the slurry are evenly distributed on the spiral.
3. The slurry from the mixing tank is sent to the first-stage spiral chute group by two slurry pumps (8/6E-AH). The first-stage spiral chute has two groups (each group has 30 sets of spirals), so one group of spirals has one pump, and each group has a large distribution tank (1800*2000mm).
4. The medium slurry discharged from the first-stage spiral chute enters two slurry tanks, and then two slurry pumps (6/4D-AH) are used to transport the medium slurry to the second-stage spiral chute. The chute also has two spiral groups (10 spirals in each group), 20 groups in total), and each group has a large distribution trough (1500*1500mm)
5. The concentrate discharged from the first-stage spiral chute enters two slurry tanks, and then is sent to the third-stage spiral for final concentration using two slurry pumps (4/3C-AH). The discharged tailings enter two tailings tanks and are then sent to the tailings pile 200 meters away using two slurry pumps (6/4D-AH).
6. The concentrate discharged from the second-stage spiral chute enters a slurry tank and then uses a slurry pump (3/2C-AH) to send the concentrate to the third-stage spiral large distribution tank (1000*1200mm). The discharged tailings enter a slurrytank and are then sent to tailings pile 200 meters away using a slurrypump (6/4D-AH).
7. The final heavy mineral concentrate product discharged from the third-stage spiral chute enters a slurry tank. Then, a slurry pump (1.5/1C-HH) delivers the concentrate to a ground concentrate pile 300 meters away.
8. We have designed the process to be adaptable. We will consider installing some water supply pipes to add extra water to each spiral. When the slurry separation effect is not good and the slurry density is too high, we have the flexibility to add a little extra water to the spiral. Whether to add additional water depends on the actual separation effect of the spiral and the ore conditions, and is mainly used as a backup. This flexibility in the process should give you confidence in handling variations in the operation.
Main Equipment
Trommel screen
Trommel screens effectively sort and classify materials according to size and shape, mainly washing and screening raw sand ore. Trommel screens are also used for density separation, where heavier minerals settle to the bottom while lighter materials are carried away. Because there are not many large gravels in this heavy mineral placer, but mostly fine sand, a simple drum screen and flushing water are used to wash and screen the ore.
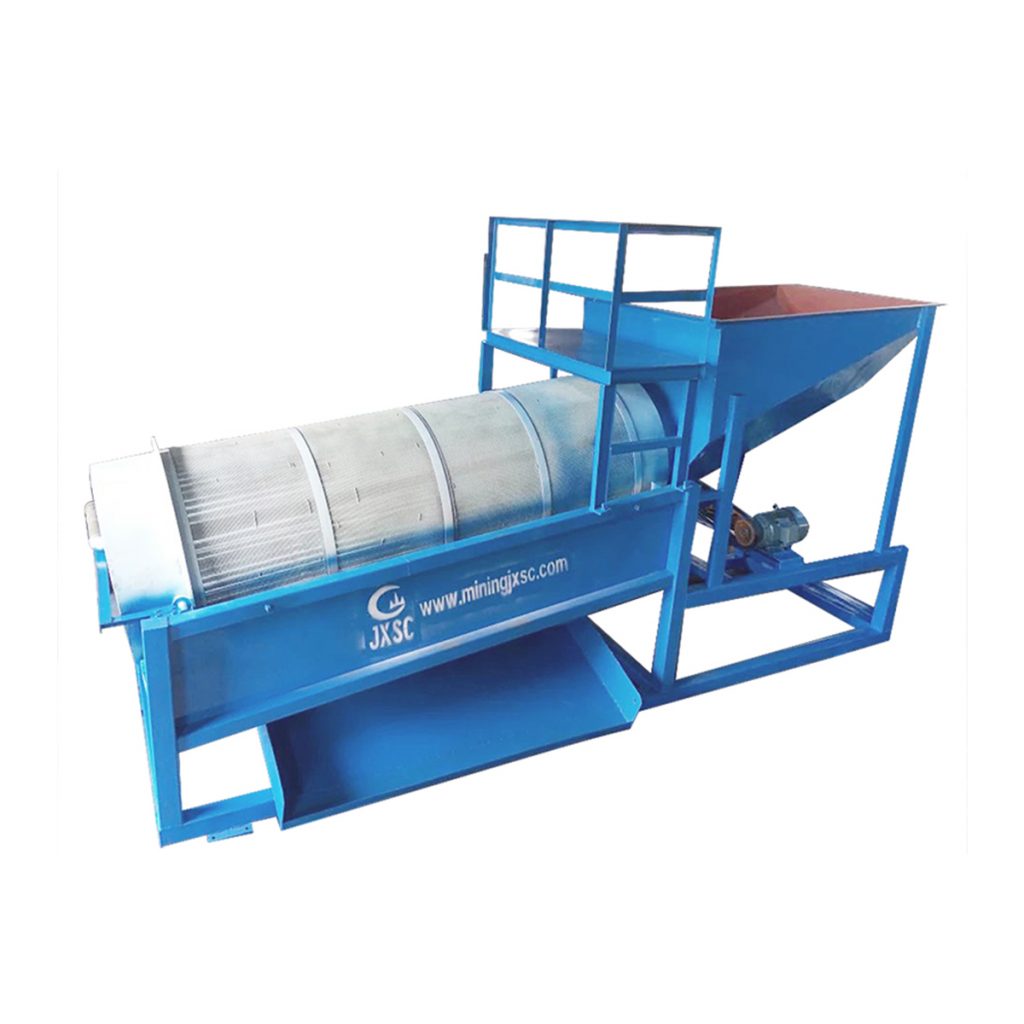
spiral chute
The spiral chute is a gravity separation equipment that uses the continuous centrifugal force generated by the mortar in the rotary spiral motion to separate light and heavy minerals. It can effectively process coarse, medium-grained ores with large differences in specific gravity and low slurry content. It has the advantages of a simple equipment structure, low production cost, and less environmental pollution. The chute uses gravity to separate materials of different densities, allowing heavier particles to settle to the bottom while lighter particles are carried upward. This simple yet effective mechanism contributes to the high purity of the final isolated product. It takes up less floor space and consumes less water and electricity. In heavy mineral sorting, it is the most critical equipment.
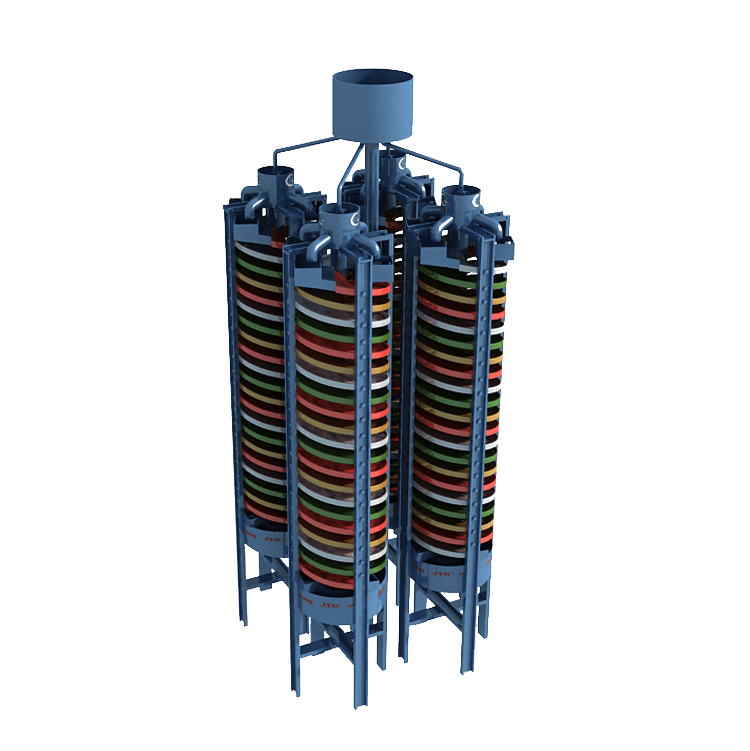
The gravity separation method uses multiple processes for extraction to ensure the quality of the valuable mineral concentrate. The process flow is relatively simple, easy to master and operate, does not require overly complex equipment and technology, and reduces production costs. Based on the characteristics of heavy minerals, we(JXSC) will develop suitable heavy mineral separation methods and equipment for you to extract concentrates with high efficiency. Contact us for more details!