What is a jig separator?
Jigs are common mineral gravity separation equipment with above-screen and below-screen discharge machines. They are mainly used to separate various metal and non-metallic minerals, especially for the recovery of fine-grained minerals. They are widely used in tantalum, niobium, tin, gold, diamond, coltan, manganese, copper, iron ore, barite, and other ore dressing plants and have a wide range of applications. Jigs mainly use water as a medium to separate minerals according to the specific gravity difference between minerals and gangue. They have large processing capacity, high recovery efficiency, and can be continuously sorted. They are also the most efficient, energy-saving, and environmentally friendly re-selection machines for mineral processing.
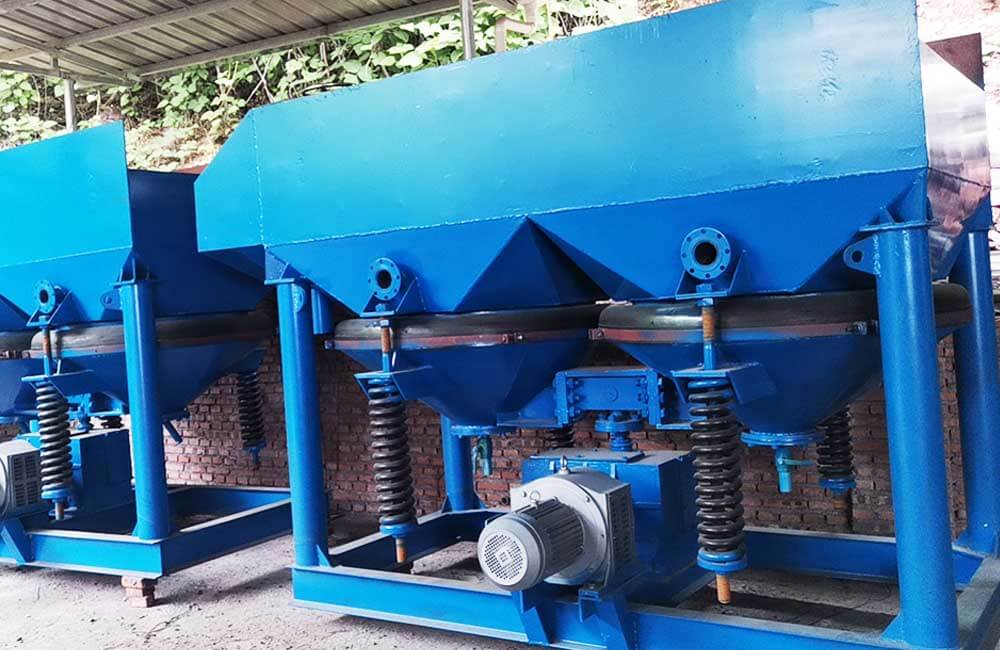
working principle
In the vertical rising water flow of the jig, light, heavy, and different-sized mineral particles have different movement speeds. The heavy minerals fall behind the light minerals when they rise and are under the light mineral particles at the end of the rise. When the mineral particles move in the opposite direction, the heavier mineral particles will fall faster in the static or descending water flow. According to the difference in density, it is difficult for the material with low density to pass through the material layer with high density to enter the lower space, so the material entering the jig is roughly divided into two material layers. The heavy minerals pass through the screen into the concentrate tank, and the light minerals enter the tailing tank for discharge. The materials are continuously fed into the jig, sorted, and discharged separately, forming a continuous jig beneficiation process.
Factors Affecting Jig Gravity Separation
The effect of the jig gravity separation process is affected by many factors, and six common factors are listed as follows:
1. Structure Of jig separators:
The jig is mainly composed of the main parts, such as the body, transmission device, water separator, diaphragm, and valve. The structure has a greater impact on the selection index. The jig has two sections, each of which is divided into a jig chamber and a diaphragm chamber by a partition. For example, increasing the screen area of the jig chamber can increase productivity.
2. Stroke and stroke frequency
The stroke refers to the distance the jig moves in each cycle, while the stroke frequency indicates the number of cycles per minute. These two factors play an essential role in determining the size and density of the particles separated by the jig. The higher the stroke length, the more intense the movement inside the jig, resulting in better particle stratification and higher separation efficiency. On the other hand, adjusting the stroke frequency can help control the residence time of the particles inside the jig, thereby better controlling the separation process. Finding the best balance between stroke length and frequency is the key to achieving the desired results of the jig separation process. By carefully adjusting these parameters, operators can adjust their processes to achieve the highest efficiency and recovery rate.
3. Feed Ore properties
The physical and chemical properties of the ore have a significant impact on the jig gravity separation process. The density composition of the ore determines the selectivity of the material. The greater the density difference between light and heavy minerals, the higher the separation efficiency. The effective processing particle size range of gravity separation is the medium and fine particle size. Under the condition that the valuable minerals and gangue minerals can achieve monomer dissociation, the coarser the crushing particle size, the better. There is a greater choice of gravity separation equipment at this time, and better separation indicators can be obtained.
4. Underscreen water and feed water
Water is an essential medium for the jig. A higher under-screen water flow rate tends to result in a finer particle size distribution in the feed, thereby improving the separation efficiency due to better stratification and separation. On the other hand, the quality and quantity of feed water provided to the jig directly affect its effectiveness in separating valuable minerals from gangue materials. Clean and evenly distributed feed water helps maintain a stable bed density, thereby achieving better sedimentation and stratification during separation. In addition, monitoring and adjusting the under-screen water flow rate and feed water quality can optimize jig performance and maximize mineral processing plant recovery.
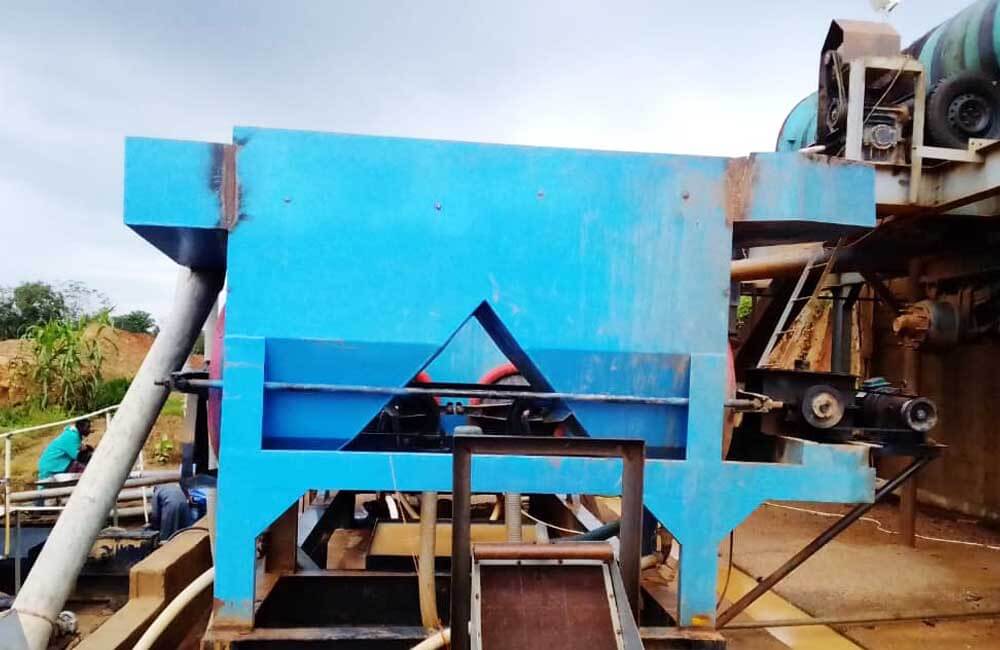
5. Selection Of Jig Separator
When choosing the right jig gravity separation equipment, factors such as particle size, density, and shape must be carefully considered to achieve the best results. By using energy-saving machinery and incorporating recovery strategies into the beneficiation process, the efficiency of the separation process can be significantly improved, thereby increasing productivity and saving costs.
6. Maintenance Of Jig Separator
Refrain from maintaining maintenance after using the jig may lead to increased downtime, reduced productivity, and increased operating costs. Regular inspection and maintenance of the machine are required to reduce the possibility of failure during operation and ensure that the gravity separation process operates at optimal capacity. It not only saves time but also prevents potential safety hazards in operation and extends the life of the equipment.
In short, the effectiveness of jig gravity separation is affected by many factors, such as machine design, pulsation frequency, ore density, stroke length, amplitude, and slope, which may affect the sorting effect. More detailed control and adjustment are required for the best mineral processing performance. JXSC has an experienced team of engineers who support the customization of equipment that suits your mineral situation. Contact us for more details!