Ball mills and wet pan mills are usually the most critical grinding equipment after crushing. When grinding gold, the main purpose is to crush the material into finer materials to prepare for the subsequent steps. It is often combined with a grading device to form a closed-loop grinding device, which grinds and grades the material at the same time to achieve the best effect. The choice of these two equipment depends largely on your operation’s specific requirements and the ore’s characteristics. Next, we will introduce these two types of grinding equipment: ball mills and wet pan mills.
What Is Ball Mill?
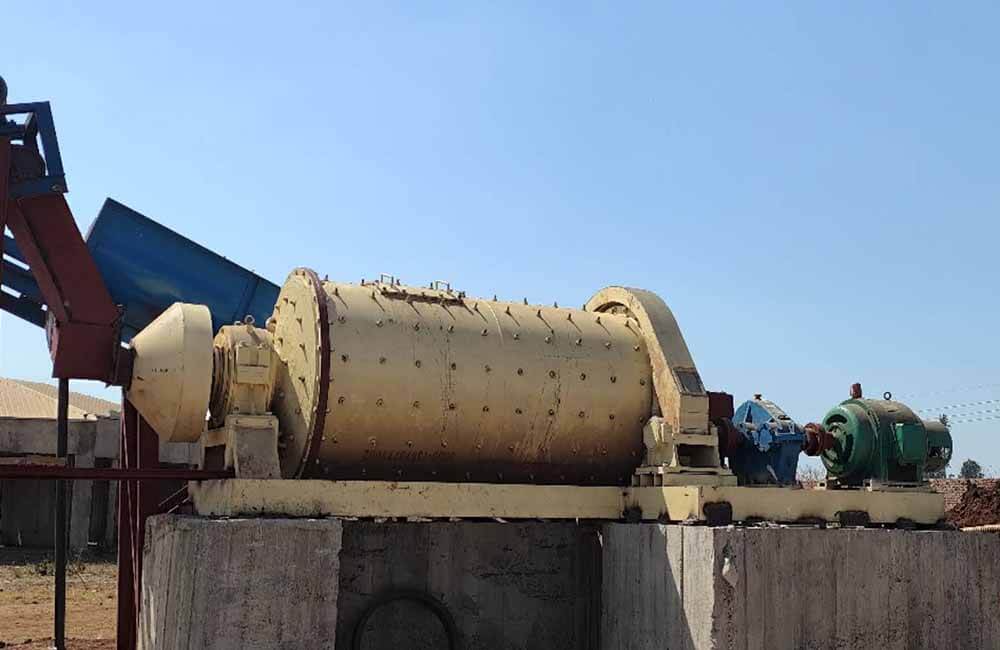
Ball mills are generally used in the mineral processing industry. It’s also widely used in cement, silicate products, new building materials, refractory materials, fertilizers, black and non-ferrous metal beneficiation, glass and ceramics, and other production industries. Dry or wet grinding of various ores and other grindable materials. The processed materials include gold, iron ore, copper ore, molybdenum ore, manganese, lithium ore, antimony ore, and other minerals, with a wide range of applications. Its core function is to grind materials. Ball mills are key grinding equipment for processing materials after crushed. According to different ore discharge methods, they can be divided into two types: grid type and overflow type. They are generally used as core equipment in gold mineral processing production lines.
working principle
Materials are fed into the barrel of the ball mill through the hollow shaft. A motor drives the barrel of the ball mill to rotate. The materials and media in the barrel spin and move at a certain speed, including gravity, centrifugal force, and friction. When the grinding medium and the cylinder reach a certain height and its weight is greater than the centrifugal force, it will break away from the inner wall of the cylinder and fall or roll down. Since the gravitational potential energy is converted into kinetic energy when falling, the steel ball will eventually collide with the ore at a certain speed, and the impact force will break the ore. The crushed qualified materials are discharged through the ore discharge port.
Features
- Famous for its ability to process large amounts of material, it is good at producing fine particles and is often an ideal choice for large-scale capacity gold processing plants.
- The sturdy design also enables it to handle different ore hardnesses while adjusting the grinding time accordingly, thereby maximizing gold recovery.
- JXSC ball mill uses metal wheels and new wear-resistant materials to make the friction rolling between the processing wheels for transmission, with extremely low noise and good applicable environment;
- High degree of automation, good grinding effect, strong adaptability, stable operating performance and long service life.

What Is Wet pan mill
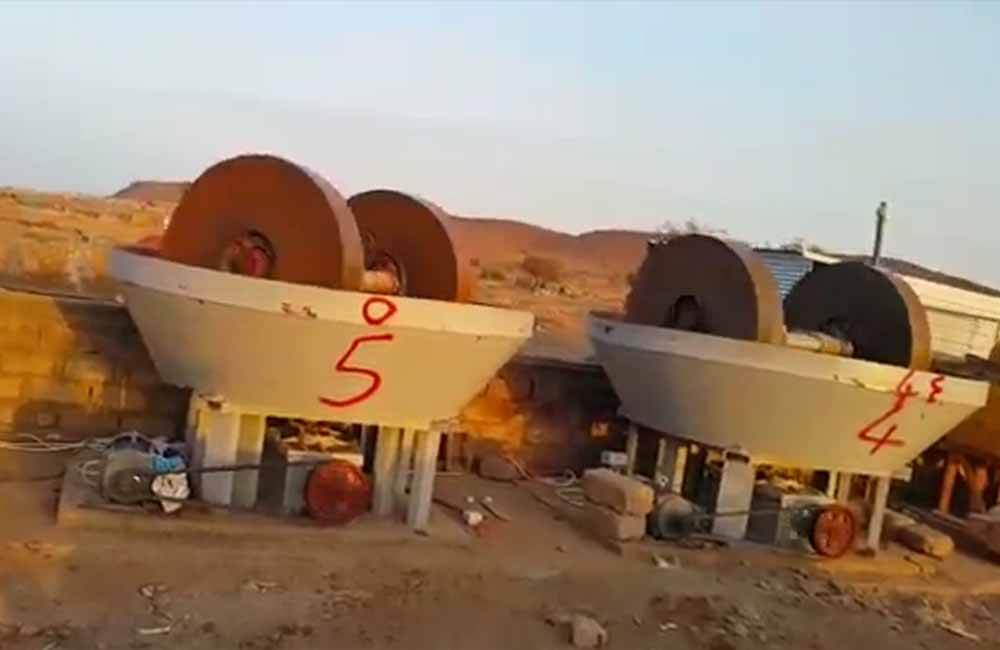
The wet pan mill realizes gold mineral recovery through its integrated amalgam process. It mainly adopts stirring, crushing and rolling of raw materials, and after repeated processes, the moisture balance and uniform slurry fineness are achieved, and then the materials are completely crushed. It is mainly composed of a frame, a water basin, a grinding wheel, a grinding plate, a motor, a reducer and other parts. The structure is relatively simple and is usually more common in small-scale rock gold processing solutions.
working principle
The electric motor transmits the power to the reducer. Under the drive of the reducer, the rolling wheel obtains the driving force and rotates counterclockwise along the horizontal direction of the horizontal axis.
When working, the grinding wheel can not only revolve around the large vertical shaft of the wet mill, but also rotate around the central axis of the grinding wheel, while the grinding plate is fixed. The added ore material is subjected to squeezing force from the weight of the wheel in the mill, and the huge friction force generated by the wheel during rotation and rotation of the wheel and the grinding pan is completely crushed after repeated extrusion, kneading and grinding.
Features
- Wet pan mills have unique advantages in small-scale mining settings or when processing softer ores;
Mercury is introduced during the grinding process to extract gold directly from the crushed material; - The equipment has a simple structure, is easy to install and maintain, is not affected by the site, and can be produced as soon as it is connected to the power supply;
- The cost of wet pan milll is low, and it has the advantages of good wet crushing performance, low investment, and high output;
- Single-unit beneficiation can be selected, or multiple-unit group beneficiation can be used, which is a good alternative to small and medium-sized grinding mill.
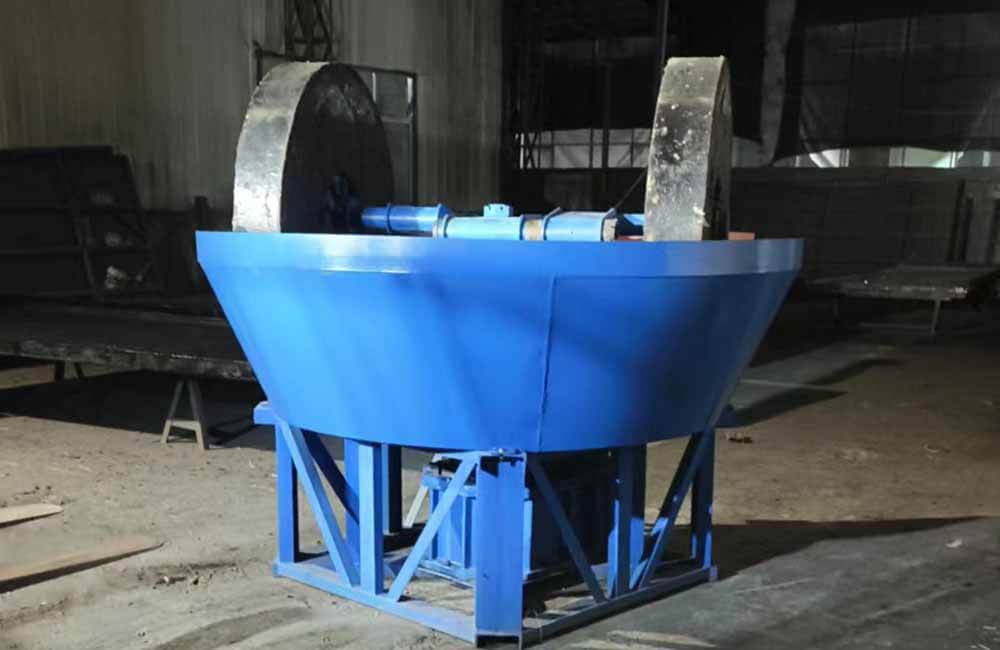
How to choose?
1. Particle size distribution
Ball mills typically produce a wide range of particle sizes because of their tumbling action, which is very beneficial for producing the finer particles required in the subsequent cyanidation process. In contrast, wet disc mills can more accurately control particle size and achieve narrow distributions, which enhance the flotation process, making them ideal when specific classification is critical.
2. Operational efficiency
This includes not only energy consumption, but also long-term maintenance requirements. Wet disc mills generally have simpler mechanical structures and fewer moving parts than traditional ball mills, which can mean lower downtime and operating costs.
3. Abrasiveness
Harder materials may wear out the ball mill more quickly than a sturdier designed wet disc mill, requiring more frequent grinding media changes.
In summary, the choice of ball mill and wet pan mill depends mainly on factors such as scale, ore characteristics and economic considerations. Understanding these nuances will help you choose the most effective grinding method and equipment for your gold extraction goals. JXSC supports customized ball mills and wet mills, contact us for more details and quotes!