Lithium is a new energy mineral, commonly used in new energy vehicles, battery manufacturing and other fields. The presence of lithium enables batteries to store more electrical energy, providing cars with strong and lasting power and range. Therefore, the lithium content in the battery of an ordinary electric car directly affects its performance and cost. However, spodumene has a high lithium content and is the main source of metallic lithium extraction. Therefore, spodumene beneficiation solutions are diverse, which can directly determine the recovery rate of lithium and the quality of concentrate. According to the properties of the ore, spodumene beneficiation methods mainly include gravity separation, flotation, and magnetic separation; each has suitable scenarios and characteristics.
Properties of Spodumene beneficiation
Spodumene is a chain-structured silicate belonging to the monoclinic pyroxene family of minerals. It is mainly produced in pegmatite granites, and its origins include the United States, Brazil, Australia, Canada, and Xinjiang, China. It is mostly grayish white, green, dark green, or yellow, with a glassy luster. The crystals are short columnar or plate-shaped, and the vertical crystal faces have crystal face stripes. There are often trace amounts of sodium, calcium, and magnesium, and occasionally chromium, rare earths, helium, and cesium.
In terms of hardness, its Mohs hardness is about 6.5-7, which is relatively high. This determines that it is necessary to select appropriate crushing and grinding equipment before mineral processing to dissociate spodumene from gangue minerals effectively. The density is about 3.03-3.22g/cm³, different from some gangue minerals. At this time, gravity separation is often used to achieve initial enrichment of spodumene through density difference. At the same time, its hardness and density also affect the control of grinding fineness during flotation. If the grinding is too fine, it may lead to over-crushing and affect the flotation effect; if the grinding is too coarse, the mineral dissociation is insufficient, reducing the lithium recovery rate.
spodumene beneficiation solutions
1. Gravity separation
Gravity separation is a mineral separation method based on the density difference between spodumene and gangue minerals to achieve spodumene separation and enrichment. The density of spodumene is about 3.03 – 3.22g/cm³. Compared with some gangue minerals, this density difference provides feasibility for this method. The gravity separation flow includes crushing, screening, and gravity separation processes.
Spodumene beneficiation – gravity separation Process
The mined spodumene ore is first crushed by a crusher for coarse, medium, and fine crushing to reduce its particle size to a suitable range, creating conditions for subsequent separation. Subsequently, the crushed material is screened by a vibrating screen and classified by particle size to ensure that the particle size of the selected material is uniform, providing qualified selected materials for subsequent gravity separation operations. Shaking tables and spiral concentrators are commonly used equipment in gravity separation.
- When the shaking table is working, the asymmetric reciprocating motion of the bed surface and the action of the lateral water flow cause minerals of different densities to produce different motion trajectories on the bed surface, thereby achieving the separation of spodumene and gangue minerals.
- The spiral concentrator uses the water flow in the spiral trough and the centrifugal force to move the denser spodumene particles to the bottom of the trough. Then, along the spiral line at the bottom of the trough, the denser spodumene particles move to the concentrate end for discharge, while the less dense gangue minerals are discharged from the tailings end with the water flow.
Gravity separation is usually suitable for coarse-grained spodumene beneficiation and when the density difference between spodumene and gangue is large. Its advantages are that the equipment structure is relatively simple, easy to operate, low cost, and has less impact on the environment. For fine-grained spodumene ore, gravity separation needs to be used in combination with flotation to improve the recovery rate of spodumene and the concentrate grade.
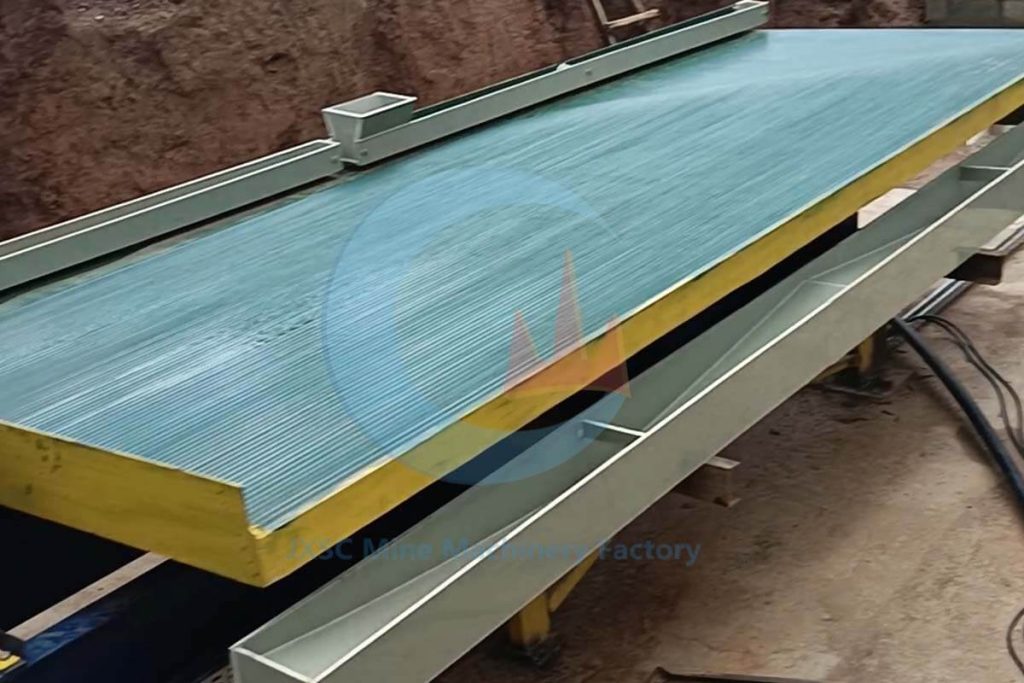
2. Flotation separation
Flotation is a common and efficient method for spodumene beneficiation. Flotation agents are added to achieve separation based on the difference in the physical and chemical properties of the surface of spodumene and gangue minerals.
Spodumene beneficiation – flotation Process
In the flotation process, the spodumene ore is first ground to dissociate the spodumene and gangue fully. The grinding fineness depends on the characteristics of the ore to ensure the degree of dissociation and prevent over-grinding. Then, the slurry is adjusted, and specific flotation agents are added. Collectors are one of the key agents. They can selectively adsorb on the surface of spodumene, enhance its hydrophobicity, and make it easy to attach to bubbles. Commonly used collectors include fatty acids, amines, etc. Frothing agents are used to generate a large number of stable bubbles to carry the spodumene particles that have been adsorbed with collectors. In addition, adjusters are added to adjust the pH value and other ion concentrations of the slurry, improve the flotation environment, and improve the selectivity of flotation. Flotation is suitable for fine-grained spodumene ores beneficiation, has good sorting effects, and can obtain high-grade and high-recovery concentrates.
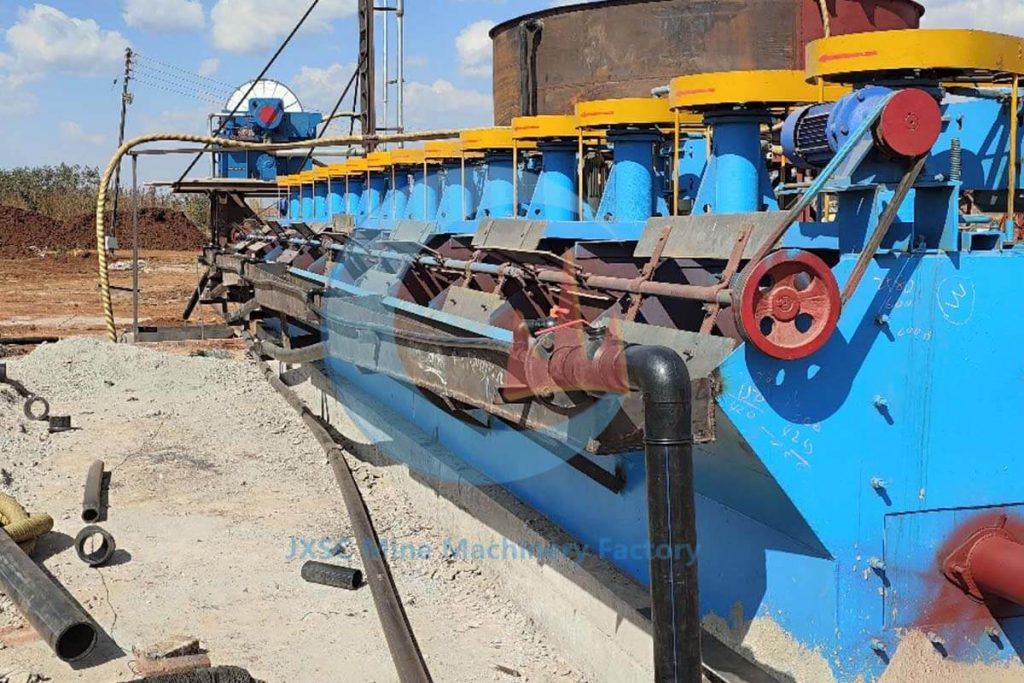
3. mangetic separation
Some associated minerals are magnetic in spodumene beneficiation, while spodumene itself is usually non-magnetic or extremely weakly magnetic. Therefore, magnetic separation is required to separate spodumene and associated magnetic minerals based on their magnetic difference.
Spodumene beneficiation – mangetic separation Process
After the raw ore is crushed and ground, spodumene and associated magnetic minerals are separated into monomers. Subsequently, the slurry is sent to magnetic separation equipment, such as a wet magnetic separator. Under the action of the magnetic field, the magnetic minerals are adsorbed on the magnetic poles of the magnetic separator. As the equipment runs, the adsorbed magnetic minerals are taken to a certain position, separated from the magnetic field, and discharged as magnetic products. Spodumene, due to its weak or non-magnetic magnetism, flows out with the slurry and becomes a non-magnetic product, thereby separating spodumene from magnetic-associated minerals. Magnetic separation is mainly used to treat spodumene ores with associated magnetic minerals, which can effectively remove magnetic impurities and improve the purity of spodumene concentrate.
Flotation, magnetic separation, gravity separation, and other methods are usually combined to achieve efficient spodumene beneficiation.
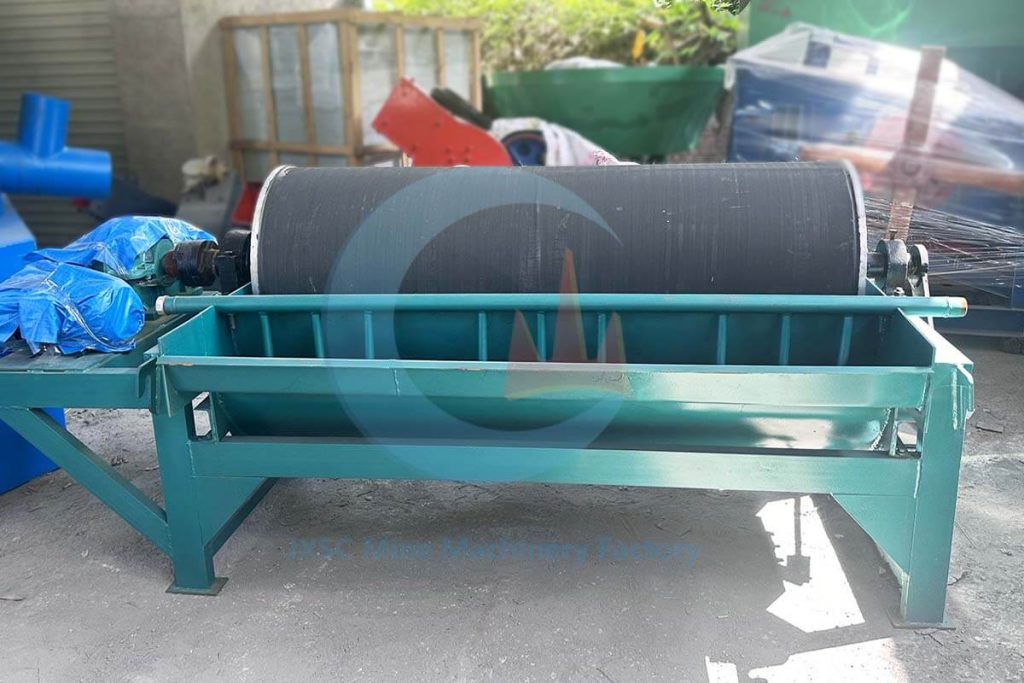
In summary, there are various solutions for spodumene beneficiation. The gravity separation method is based on density difference and is suitable for ores with coarse-grained distribution and significant density difference. The flotation method is based on the surface properties of the mineral and can process ores with various particle sizes, especially for fine-grained ores, but it has high requirements for reagents and operations. The magnetic separation method uses magnetic differences to mainly remove magnetic impurities. It is easy to operate but has limited application scenarios. When choosing a solution, it is necessary to comprehensively consider factors such as ore properties, production scale, product quality requirements, cost and environmental protection. Contact us to fully weigh your needs and select the most suitable spodumene beneficiation solution, including design processes and customized equipment.