Did you know that 30% of the diamonds mined worldwide each year come from alluvial deposits? These diamonds, buried in riverbeds, beaches, or ancient sedimentary layers, are favored by mining companies because of their easy mining and high quality. However, unlike primary mines (such as kimberlite), the dispersion and complexity of the sedimentary environment of alluvial diamonds make efficient recovery a huge challenge. If the equipment is not properly selected, it will not only waste resources but also may result in tens of millions of dollars in lost profits.
Among them, alluvial diamonds are hidden in riverbeds and weathered sediments, but mining them requires specialized tools. The right equipment is the difference between success and failure. With 40 years of experience in mining machinery, we will share 3 key tools that determine the success or failure of alluvial diamond processing and recovery.
The top 3 equipment for alluvial diamond processing are:
- 1) Trommel scrubbers to clean sticky clay.
- 2) Vibrating screens for gravel sorting.
- 3) Jig separators capture heavy minerals.
4 Equipment For Alluvial Diamond Processing
1. Trommel Scrubber For Alluvial Diamond Washing
In alluvial diamond processing, the trommel scrubber is the preferred equipment for processing diamond ore containing clay. Through the combined action of strong scrubbing, crushing and screening, it can remove more than 90% of the iron oxide film and clay wrapping on the surface of the diamond, and increase the subsequent X-ray sorting efficiency by 40%-60%. Its unique design can increase the processing capacity to 300 tons per hour while maintaining the integrity of the diamond crystal, becoming the core washing equipment for alluvial deposits in Africa, South America and other places.
Working principle of trommel scrubber
The drum ore washer achieves three-stage cleaning of diamond ore through the synergistic effect of the rotating drum (diameter 1.5-3m) and the internal spiral guide plate:
- Crushing stage: high-pressure spray (20-30bar) with wear-resistant steel stirring rods to strongly decompose cemented ore blocks
- Scrubbing stage: drum speed 5-8r/min, ore friction strips impurities on the surface of diamonds
- Screening stage: 8-12mm screen is configured at the end to complete the coarse particle classification simultaneously
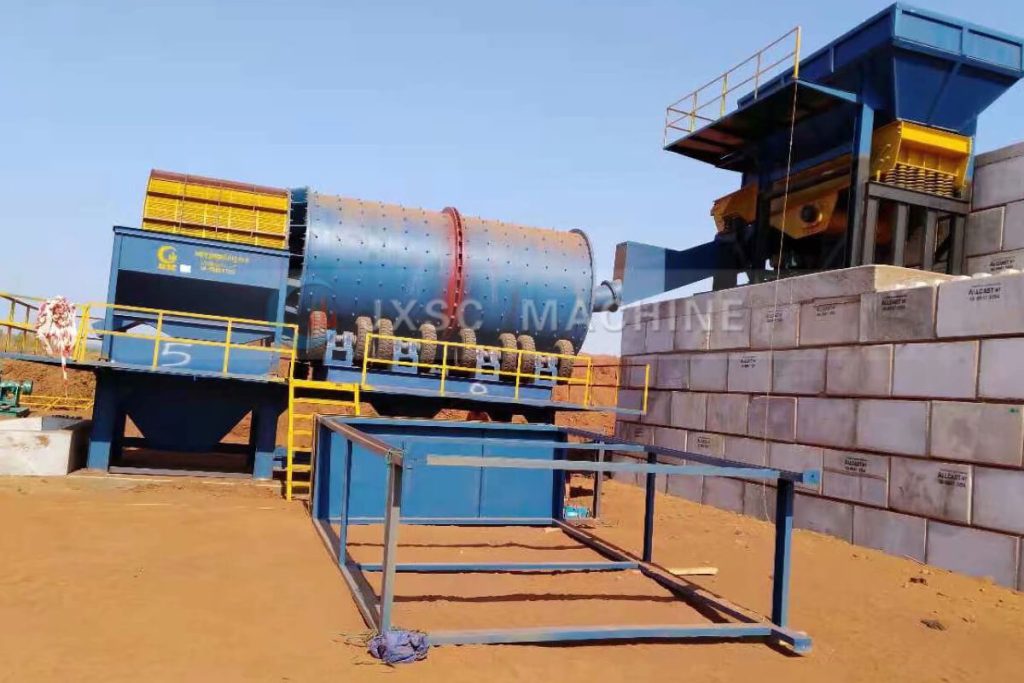
The diamond recovery rate increased by 23% with our drum ore washer. The equipment can process 50 tons per hour and remove 95% of clay. Key factors: adjustable speed (8-15 rpm) and replaceable screen plates. Without proper scrubbing, downstream equipment is prone to blockage, thereby reducing diamond recovery.
2. Vibrating Screens For Sort Diamond-Bearing Material
In alluvial diamond mining, efficient separation of diamond-bearing materials from gravel, sand and debris is essential to maximize production and reduce operating costs. As the core sorting equipment, the vibrating screen undertakes the key task of accurately separating diamond-bearing ore from complex materials such as gravel and soil. Through the combined design of high-frequency vibration and multi-layer screens, it can achieve efficient sorting of hundreds of tons of raw materials per hour, while increasing the recovery rate of diamond particles to more than 95%.
Sorting principle of vibrating screen:
The vibrating screen drives the eccentric block through the motor to produce regular three-dimensional vibration, so that the screen surface material is graded in a jumping motion. In view of the fact that diamonds in alluvial deposits are often associated with gravels with a particle size of 5-30mm, the equipment adopts a multi-layer screen structure (usually 3-5 layers) to filter materials of different sizes layer by layer.
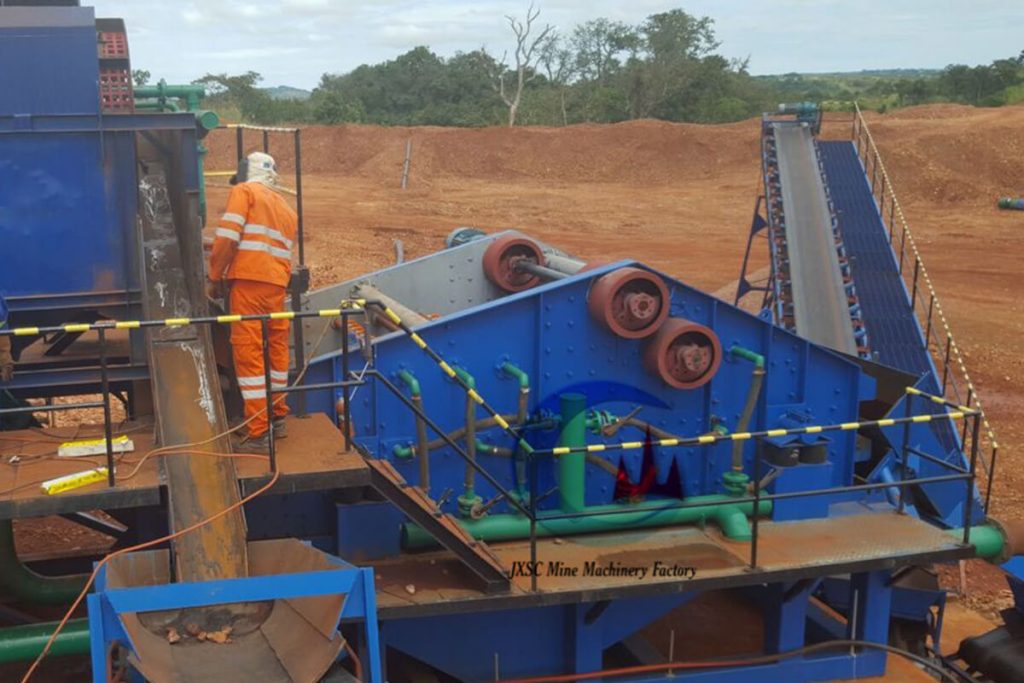
Vibrating screens use high-frequency vibrations to screen excavated alluvial deposits, separating oversized rocks, fine sediments, and other worthless materials from diamond-rich gravel. This step minimizes the amount of material sent to the washing plant or X-ray sorter, thereby reducing energy consumption and processing time.
3.Jig Separators For Capturing Microscopic Diamonds
In alluvial diamond processing, the jig has become the core equipment for recovering 0.2-2mm micro-diamonds with its unique gravity sorting principle. Through precisely controlled water flow pulsation, the jig separator can increase the diamond concentration to more than 1,000 times that of the raw material within 10-30 minutes, and the recovery rate of micro-diamonds reaches 85%-92%, which is especially suitable for fine-grained alluvial deposits in South Africa, Canada and other places.
Working Principle of jig separator
The jig achieves micro-diamond sorting through the 200-400 times/minute pulsating water flow generated by the diaphragm. The high-pressure water flow (0.2-0.5MPa) first suspends the ore particles, and uses the density difference between diamonds (3.5g/cm³) and quartz sand (2.65g/cm³) to penetrate the steel ball medium bed at a speed 3 times faster during the sedimentation stage, forming a high-concentration concentrate layer. The intelligent discharge valve automatically opens and closes according to the amount of concentrate accumulated. Combined with the electromagnetic drive system’s 0.05mm amplitude accuracy, it can achieve precise capture of 0.1mm-level micro-diamonds. A single sorting can enrich diamonds by 800-1200 times.
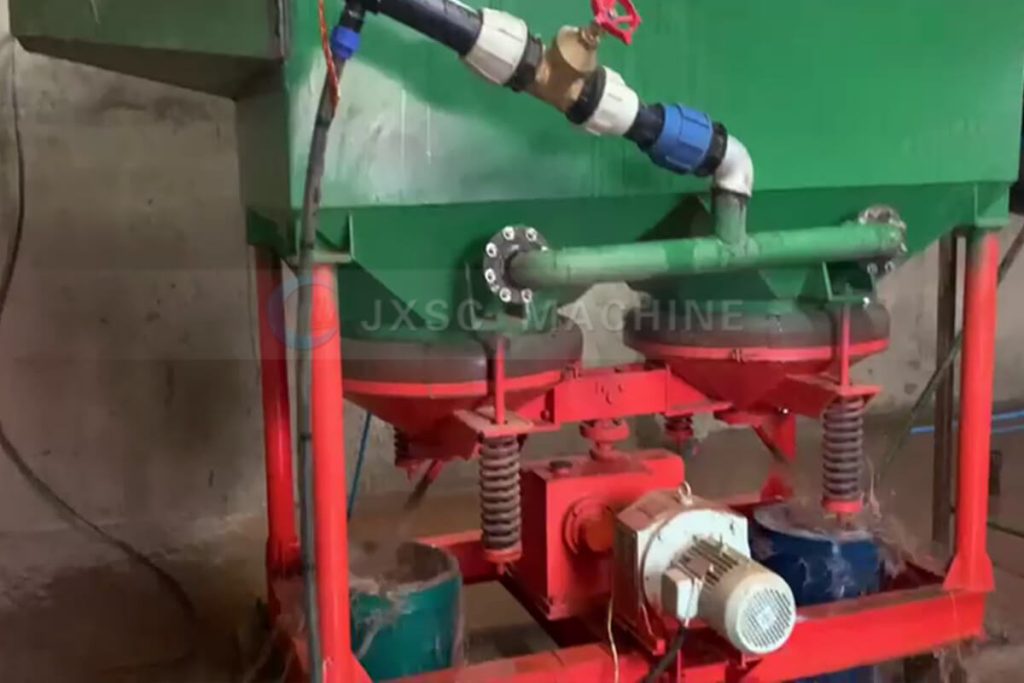
The core of alluvial diamond processing relies on three key equipment: vibrating screen, washing drum, and jig. The vibrating screen quickly separates sediments of different particle sizes through multiple layers of screens to improve the efficiency of subsequent sorting; the trommel scrubber is targeted at clay deposits and uses rotational friction to remove impurities on the surface of diamonds. The jig uses water pulsation to achieve density sorting of heavy minerals (such as diamonds) and light sand and gravel. They can quickly separate impurities, accurately extract tiny diamonds, and reduce environmental damage.
The specific equipment selection needs to take into account the type of ore deposit (such as the proportion of gravel, clay content), production scale (manual vs. industrialized) and budget. For example, small-scale mines may prefer low-cost manual jigs, while large enterprises need to invest in automated X-ray sorting lines to increase production capacity. JXSC supports customized diamond processing equipment and turnkey mineral processing solutions. Contact us for more details!