Is your mineral processing production line plagued by inefficiency due to the wrong selection of grading equipment? In mineral processing, chemical or mineral processing production, when materials need to be graded, spiral classifiers and hydrocyclones have similar functions. The main functions include graded dehydration, high-precision classification, and concentration. This seemingly simple equipment selection problem is directly related to the efficiency, cost, and even stability of the subsequent process. Choosing the wrong equipment may lead to insufficient grading accuracy, soaring energy consumption, or frequent downtime for maintenance, which will make production plans passive. We will disassemble practical selection techniques, from essential differences, particle size, to cost analysis, etc., to help you sort out your ideas and find the “optimal solution” in the most practical way.
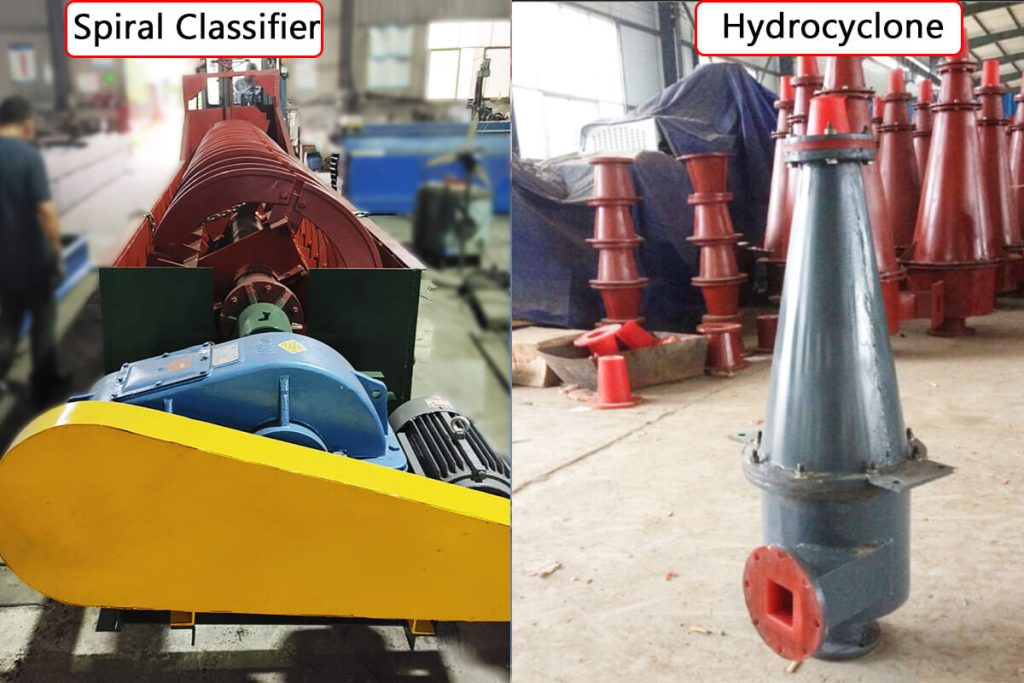
Are you having trouble choosing between spiral classifier or hydrocyclone? We have practical tips and tricks to help you make an efficient decision! Compares the core differences between the two in terms of working principle, particle size processing capacity, energy cost, and maintenance requirements. Avoid the loss of fine particles or soaring energy consumption due to choosing the wrong equipment, and help you quickly choose and find the optimal solution for the classifying equipment that is suitable for your production line.
Spiral classifier or hydrocyclone: essential difference
In the mineral processing process, spiral classifiers and hydrocyclones are both mineral processing classifiers. The purpose is to effectively separate coarse and fine particles, avoid over-crushing of fine minerals, reduce unnecessary energy consumption, and make coarse minerals return to the mill as return sand for effective crushing again.
Working principle of spiral classifier
“Gravity sedimentation + mechanical conveying”
The spiral classifier uses low-speed rotating spiral blades to settle and separate the coarse particles (>0.15mm) in the slurry, and at the same time, the blades convey qualified fine particles upward to achieve solid-liquid classification. Its core relies on gravity sedimentation, which is suitable for coarse-grained classification of high-concentration slurries (such as iron ore and tungsten ore), and can integrate washing functions (such as desludging and desulfurization).
Applicable scenarios of spiral classifier: classification of ores with large processing capacity, coarse particles (0.1-3mm), and high requirements for cleanliness, such as quartz sand and coal washing.
Working principle of hydrocyclone
“Efficient classification by centrifugal force”
Hydrocyclone uses the centrifugal force field generated by high-speed tangential feeding to separate solid particles according to particle size. Fine particles (5-300μm) are discharged from the overflow port, and coarse particles (>100μm) settle to the underflow port to complete the sorting. No rotating parts are required, energy-saving and adaptable to high production needs.
Applicable scenarios of hydrocyclone: fine powder classification (such as titanium dioxide, calcium carbonate), concentration and dehydration or closed-circuit grinding system, especially suitable for production lines with limited space but high-precision classification requirements.
Spiral Classifier or Hydrocyclone: Key Tips for Selection
1. Particle size range
If the material is mainly coarse particles (>50μm) or the slurry concentration is high (>40%), the spiral classifier is more suitable. The mechanical push of its spiral blades can stably handle large particles and avoid blockage.
If the material is fine particles (<50μm) or low-concentration slurry (<20%), the centrifugal field of the hydrocyclone can quickly separate fine particles, and the efficiency is more than 30% higher than that of the spiral classifier.
Tips: Do a screening experiment first. If >50% of the particles are above 0.15mm, choose a spiral classifier; if <0.1mm, the cyclone is more economical.
2. Processing capacity requirements
- The processing capacity of the spiral classifier is 21-1785 t/24h (over flow); 145-23300t/24h (returned sand); up to 150% spiral submergence. It is more suitable for a high-capacity roughing stage.
- The processing capacity of the hydrocyclone is 0.1-900 m³ /h, which is suitable for large-scale production of fine particles.
Tips:
Small/medium-scale production line (<200t/h): such as small ore dressing plant or laboratory pilot line, it is more cost-effective to choose a spiral classifier, and the initial equipment cost is low.
Large-scale continuous production (>500t/h): such as the main production line of a large mining group, a cyclone must be used, and its single unit processing capacity can reach 10 times that of a spiral classifier, avoiding multiple devices in parallel to increase energy consumption.
3. Functional requirements
- Cleaning function: The spiral machine can integrate high-pressure flushing water (de-sludge and desulfurization), which cannot be achieved by the cyclone.
- Concentration function: The underflow concentration of the cyclone is as high as 70%, which directly enters the filter press to save the investment of the thickener.
Tips: Choose the spiral sporal classifier for dehydration needs and the cyclone for concentration needs.
4. Maintenance complexity
Components | Spiral classifier | Hydrocyclone |
Replacement cycle | Blades 5 years/Bearings 2 years | Rubber lining 2 years/Nozzles 6 months |
Tips: For high wear conditions, cyclone with quick-release structure is preferred, such as processing silica sand. For sticky materials, spiral machine is selected, which has anti-blocking design.
5. Comparison of investment budget
In terms of equipment investment, the equipment price of hydrocyclone is lower than that of spiral classifier. However, in addition to the equipment itself, hydrocyclone requires a series of necessary auxiliary equipment in the classification process, such as distributors, valves, pumps, etc., which increases part of the equipment investment. The lining rubber of the hydrocyclone wears quickly, and the blades of the spiral machine have a longer life. The spiral classifier relies on motor drive, but there is no pumping energy consumption. The hydrocyclone needs to be equipped with a pump, which consumes 30% more energy, but the classification efficiency is increased by 50%.
Tips: If the budget is sufficient, you can choose a spiral classifier; the hydrocyclone requires high pumping energy consumption but has high efficiency. From the perspective of long-term benefits, it is more “economical” to choose a hydrocyclone for large production capacity scenarios.
6. Site and installation conditions
- The spiral classifier needs to be installed at an angle (angle of 12°-18°), and the overall structure is long. The length of a single machine is generally 5-12 meters (large equipment can reach 15 meters), and the height needs to be reserved for 2-4 meters (including spiral lifting space), and a 1-2 meter maintenance passage needs to be reserved in front and behind. The length and floor height of the plant are required to be high. The installation requires pouring a concrete foundation, and the inclination needs to be strictly calibrated. At the same time, it needs to be equipped with auxiliary structures such as the motor base and the transmission belt bracket, which is relatively complicated.
- The diameter of a single hydrocyclone is mostly 100-600mm (large hydrocyclone groups are connected in parallel by multiple units), and the height is only 1-3 meters. It can be installed vertically or tilted, and can even be arranged in the corners or high-altitude spaces of the plant. It is particularly suitable for the renovation of old plants with narrow sites and limited floor heights, or production lines that need to be closely connected with other equipment. It is suitable for scenes with limited plant buildings. It only needs simple brackets for fixing, and no complex foundation is required, so the installation is relatively simple.
Tips: The spiral classifier occupies a large area. If there is enough space on the mineral processing site, it can be selected. No matter which one you choose, be sure to measure the length, width and height of the site (accurate to centimeters) before installation, and confirm the “minimum installation space” with the equipment manufacturer to avoid the equipment being unable to enter the site due to insufficient space reservation, or frequent adjustments later affecting production progress.
The main features of spiral classifiers are coarse material classification, low budget, and easy maintenance. The main features of hydrocyclones are fine material classification, high efficiency, and automation.
In general, spiral classifiers are suitable for coarse particles/small production capacity, and hydrocyclones are suitable for fine particles/large production capacity.To make the best choice between spiral classifiers and hydrocyclones, it is necessary to consider various factors such as particle size, production capacity, energy consumption, maintenance, budget, and site. Only by replacing blindly following trends with adaptability can the classification equipment truly become a production tool for increasing production capacity and reducing costs in mineral processing solutions. Contact us for details and equipment quotes!