Having trouble effectively processing alluvial gold with high clay content? Losing precious gold nuggets in oversized waste? Ores with high clay content can clog equipment and reduce efficiency, and exploring proven solutions to solve common challenges and improve recovery is an important part of successful purification. If you are struggling with gold ores with high clay content, this proven African alluvial gold processing plant solution can reduce your losses. Ready to optimize your gold recovery? Let us break down the FAQs and solutions for a customized Ghana 250TPH alluvial gold plant to quickly answer your questions.
The alluvial gold plant uses specialized equipment such as dual washing screening machines and centrifugal concentrators to achieve a more than 90% gold recovery rate.
250TPH Alluvial Gold Plant Project Info.
This is a 250TPH alluvial gold plant designed by JXSC for a Ghanaian customer. It mainly solves the sticky clay problem by using a water jet feeder, a 4-motor trommel scrubber, and a separation system.
- Mine location: Ghana
- Ore condition: The plant is designed to produce 250TPH;
- The ore contains a lot of sticky clay;
- Maximum feed size: Consider 0-300mm;
- Gold concentrate size: 0-6mm and 6-20mm.
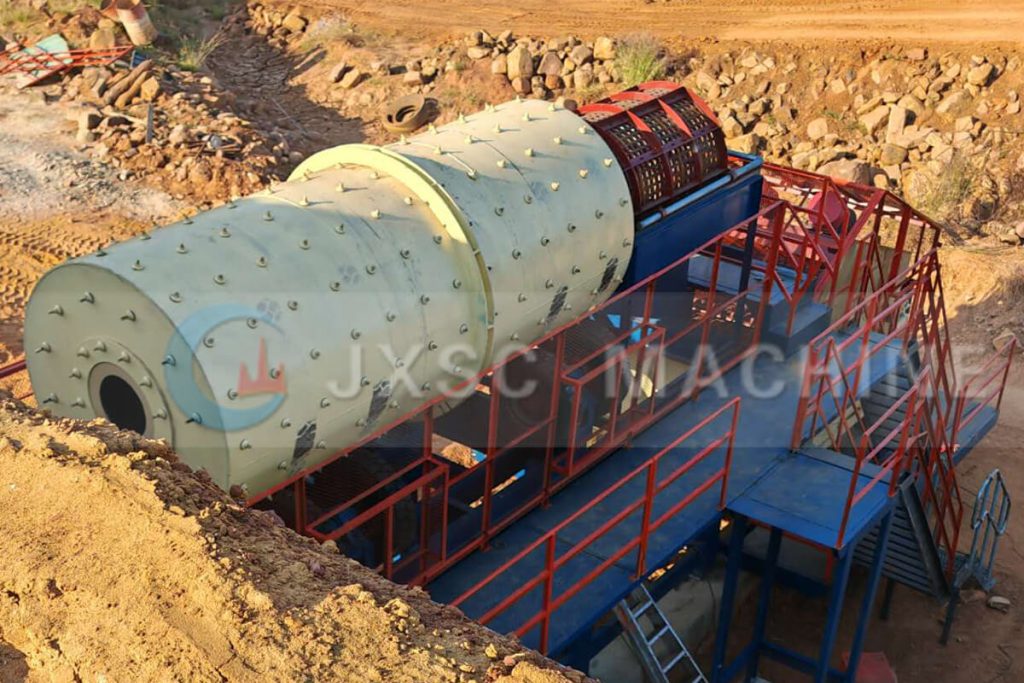
250TPH Alluvial Gold Plant FAQ
Before the 250TPH alluvial gold plant project was officially put into operation, we were often asked how to deal with Ghana’s processing clay-rich gold mines when communicating with customers. Let’s examine the process design options through real customer problems and proven gold placer plant solutions. These answers come from JXSC’s nearly four decades of African mine project experience and feedback from most customers.
Alluvial Gold Plant Quick Q&A
- Question 1: The raw ore contains a lot of sticky clay, do we need to spray water when feeding?
- Answer: Yes, no problem. Sticky clay will form clumps, which will reduce processing efficiency. We can solve this problem by adding two high-pressure water spray guns on the vibrating feeder silo. This can quickly break up the surface clay and rinse the material before it enters the rotary scrubber.
- Question 2: According to the quoted model JXSC2500 drum scrubber, the scrubber length is 5000mm and the screen part is 2000mm. How many motors are there?
- Answer: It will be a combination of 4 motors and 4 reducers. This setup ensures stable rotation for washing and screening tasks. Some customers worry about motor failure, but redundancy prevents complete downtime. Sometimes, however, a single-motor system stalls under heavy load. Adding three extra motors here guarantees continued operation even if one motor fails. Clay decomposition is 30% faster with a 4-motor system.
- Question 3: Do we only use the rotary screener for screening partly, i.e. two-layer screening?
- Answer: According to your ore situation, there is more sticky clay and the production capacity is not small. If the clay content is high and the processing capacity is large, the rotary screen alone is not enough. We recommend that you use a high-frequency vibrating screen for further cleaning and screening. This screen will do additional cleaning and separate the material into 0-6 mm and 6-20 mm sizes. In this way, the material will be cleaner before entering the separation system.
- Question 4: Should the shaking table be placed in the gold room, and is the collection bucket under the shaking table locked with a transparent glass window panel?
- Answer: Yes, most customers place the shaking table in the room, or the collection bucket is placed under a transparent glass panel with a lock on it. Regarding the transparent glass window panel, the operator monitors them through the window and prevents theft at the same time. It needs to be designed in advance when installing this equipment. But please consider that you also need to collect the concentrate manually, and you'd better let a reliable person operate it.
- Question 5: Are all oversized materials transported to one side to facilitate subsequent truck operations?
- Answer: Yes, that is no problem. This simplifies clean-up and avoids mixing waste with valuable output. We can design it to your requirements.
250TPH Alluvial Gold Plant Solutions
This 250TPH alluvial gold process plant solution is designed according to the customer’s mine conditions and requirements. The following is a detailed description of the flow chart:
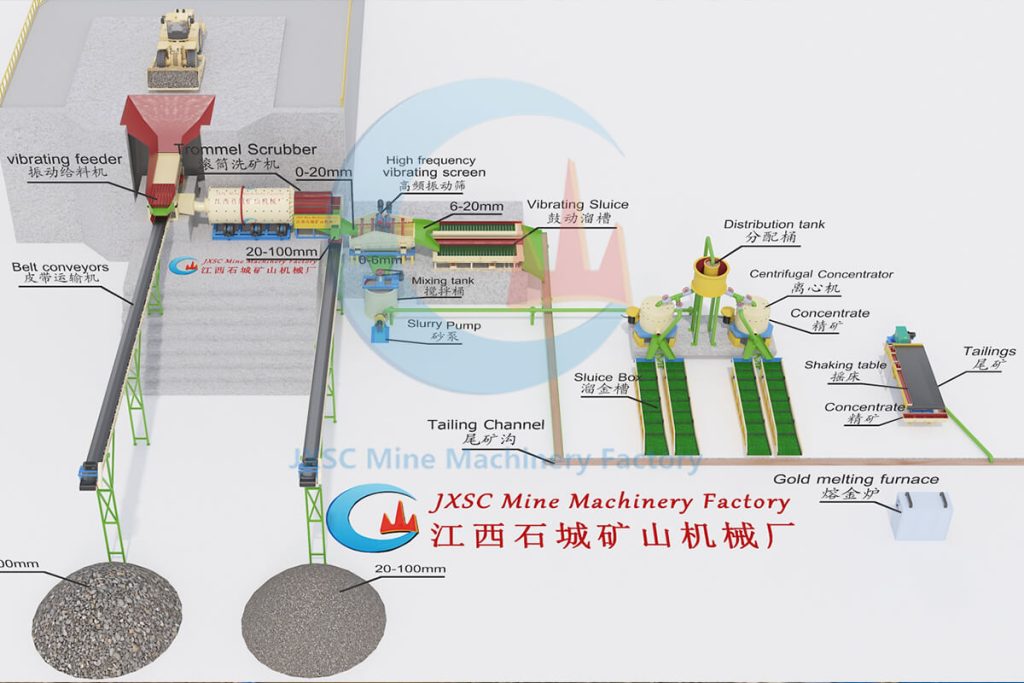
Full 250TPH Alluvial Process Plant Flow Details
1. First Stage: Feeding System
The raw materials will be sent to one hopper first, then dropped to the vibrating feeder, evenly feeding raw materials to the next machine. The vibrating feeder design with a grizzly bar, and the gap bar is 100 mm, so above 100 mm big waste stones can be easily removed here, and will be sent to the waste stockpile by one belt conveyor. Less than 100 mm of materials will go to the trommel scrubber.
2. Second Stage: Washing Screening System
0-100 mm raw materials will be evenly sent to the trommel scrubber by a vibrating feeder. The function of a trommel scrubber is to effectively remove mud/clay from raw materials, so as to separate free gold from mud/ clay. The raw materials are washed more cleanly, the gold recovery effect will be better.
After the raw materials are washed by the trommel scrubber.The trommel scrubber designed with 1 layer screen equipped with 20mm aperture. The gravel stone+20mm -100mm will be transported to the stocky pile by belt conveyor. 0-20mm part will go to a vibrating screen for further washing and sieving out different particle sizes: 0-6 mm and 6-20mm. 6-20mm matetails parts will go to a vibrating sluice box separately. 0-6mm parts will go to a mixing tank for well mixed.Then use a slurry pump to pump the slurry to next gold separators.
Our Solutions & Machine | Screen Size | Function |
Trommel scrubber | 20mm | Remove clay |
High-frequency screen | 6-20mm | Clean fine gold |
Vibrating sluice | 6mm sieve | Capture nuggets |
Centrifugal concentrator | 0-6mm | Recover fine gold particles |
Shaking table | <0.02mm | Final high-grade separation |
3. Third Stage: Gold Separator System
0-6 mm materials go to two sets of gold centrifugal concentrators for first concentrates enrichment. The tailings of the centrifugal concentrator will go to sluice boxes to recover gold again.
All the 0-6 mm gold concentrate from the 4 sets sluice boxes after concentrator and the centrifugal concentrator will go through one handmade sieve to sieve out 0-2 mm gold concentrate, 0-2mm concentrates will be sent to a shaking table for further separation of gold and to improve gold content. 6-20mm materials from the vibrating screen will go to vibrating sluice box to catch the big gold particles/ nuggets separately.
4. Fourth Stage: Gold Purification System
All gold concentrate from sluice boxes and shaking tables is sent to a gold smelting furnace,distiller and gold amalgamation machine for the refinery so that you can get a high-purity gold bar.
We have sold many of these alluvial gold plants to Africa and have received favorable comments from customers in Tanzania, South Africa, Nigeria, Angola, Uganda and many other countries cases. According to customers who have used this plant, the recovery effect is excellent. This 250TPH alluvial gold processing plant combines customized washing, multi-stage screening and safe processing to maximize the mineral recovery rate of more than 90% in clay-rich Ghanaian deposits. Since 1985, JXSC has helped miners in more than 60 countries to establish reliable gold placer processing plants. From equipment supply to complete EPC services, my team provides effective solutions. Need a gold placer equipment that can handle sticky clay? Contact us to quickly provide you with customized mineral processing solutions and equipment quotes.