Why does the seemingly routine tin(cassiterite) ore beneficiation process always put mining engineers in the double dilemma of “difficult to improve efficiency and difficult to reduce costs”? As the core raw material of electronic components solder, and the key additive metal of high-end alloys, tin is a very necessary material in modern industry. However, the characteristics of “low grade, many impurities, and difficult to sort” make the beneficiation link an “efficiency bottleneck”. The grade of global tin ore resources has declined, and the tin beneficiation efficiency directly affects enterprises’ costs and resource utilization.
Tin ore beneficiation mainly includes washing, crushing, grinding, separating(gravity separation/flotation/magnetic separation, etc.), and concentrate dehydration. Mining practitioners/engineers often encounter challenges such as fine cassiterite loss, multi-metal impurity interference, high energy consumption, and environmental pressure. JXSC will dismantle these four challenges and provide expert solutions to help you improve your beneficiation efficiency.
Tin ore beneficiation process
Every step of the tin ore beneficiation process from raw ore to concentrate is like a precision gear meshing, which directly determines the final resource income and corporate profits. The whole process can be summarized as “pretreatment (crushing, cleaning), grinding, sorting, dehydration” four major links.
Tin Ore Process Flow
1. Pretreatment:
- Washing: If the surface of the raw material contains slime or other impurities, it is necessary to use a trommel scrubber or other ore washing machine to clean it to prevent clogging in the crushing chamber.
- Crushing: The raw ore is processed layer by layer by jaw, cone and other crushers, from several meters of large pieces to 5-10mm particles, reducing the subsequent load.
2. Grinding:
The ball mill/rod mill grinds the ore to less than 0.074mm (about 200 meshes) to separate the cassiterite and gangue monomers (usually requiring -0.074mm to account for more than 60%).
3. Tin Ore Sorting:
According to the characteristics of the ore, gravity separation (jigging machine, shaking table to recover coarse particles), flotation (flotation machine + phosphonic acid collector to capture fine particles), and magnetic separation (magnetic separator to remove iron impurities) are combined to enrich the raw tin into high-grade concentrate.
4. Dehydration:
The thickener initially reduces the water content to 30%, and the filter press finally dehydrates to ≤10%, meeting the requirements of transportation and smelting.
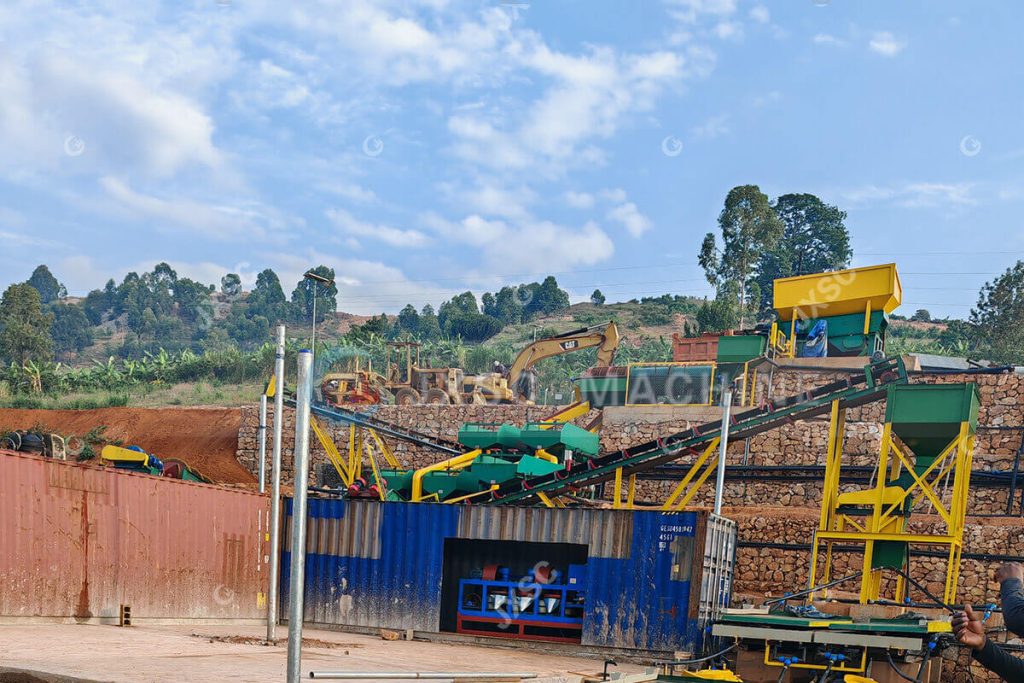
Preview of key challenges in tin ore Beneficiation
1. Loss of fine-grained cassiterite:
Tin is brittle and easily becomes muddy. It is easy to generate ultra-fine particles of -0.037mm during grinding. Traditional gravity separation equipment (such as a shaking table) is difficult to capture due to the slow sedimentation of ore particles. →→Solutions
2. Interference of multi-metal impurities: tin ore often coexists with tungsten, lead, zinc, sulfur, etc., and impurities are easily mixed into the concentrate during sorting. →→Solutions
3. High energy consumption pressure: Grinding accounts for more than 60% of the total energy consumption, and the continuous operation of the flotation machine has caused a sharp increase in electricity bills.→→Solutions
4. Environmental protection is difficult to comply with: Ore dressing wastewater contains heavy metals such as lead and arsenic and residual reagents, and direct discharge faces fines. The large area of the tailings pond makes “production expansion” even more difficult.→→Solutions
4 Common Challenges + Expert Solutions
1. Low recovery rate of fine Tin(cassiterite)
Problem manifestation: Tin is brittle and easy to be muddy, and the proportion of -0.037mm fine particles (400 mesh) is high. Although this type of fine particles has a high density, the particle size is too small, and it is difficult to capture by traditional gravity separation/flotation, resulting in excessive tin content in tailings, and a high probability that 25% of the tin concentrate will be lost.
Solutions For Low Recovery:
- Process optimization: “stage grinding + classification separation” is used for coarse particles to enter gravity separation, and fine particles (-0.037mm) are treated separately with fine particle shaking tables, centrifugal concentrators or hydrocyclones.
- Reagent innovation: Use phosphonic acid collectors (such as styrenephosphonic acid) to selectively adsorb cassiterite and improve flotation recovery rate;
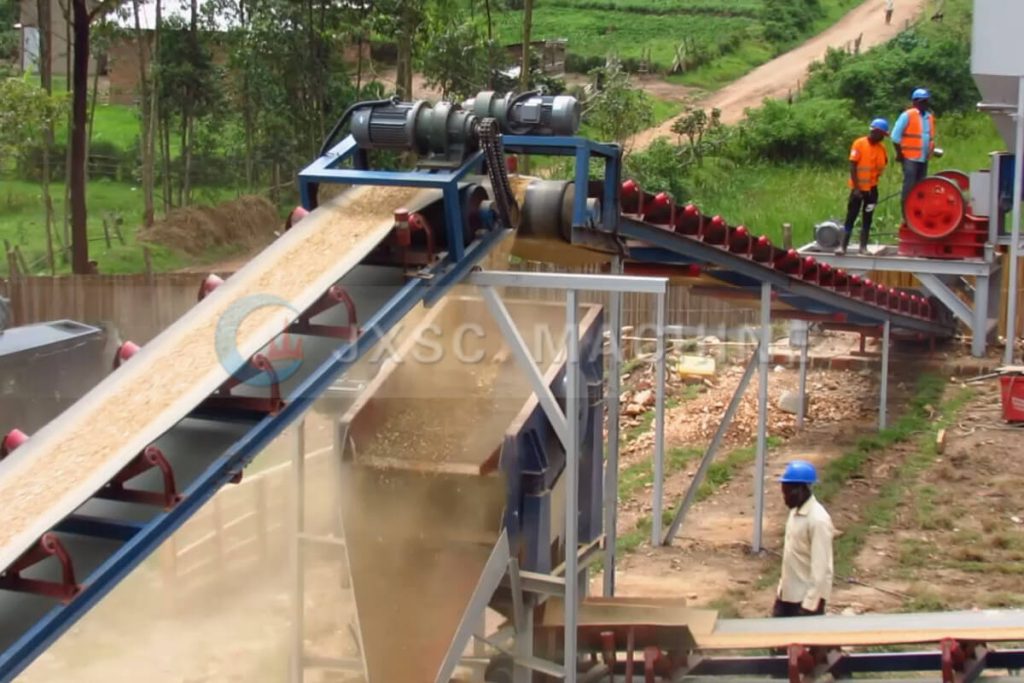
2. Interference of multi-metal impurities
Problem manifestation: Tin ore is often accompanied by tungsten, lead, zinc, sulfur, etc., and traditional processes easily lead to impurities in the concentrate (such as excessive sulfur affecting smelting). For example: the density of pyrite is close to that of cassiterite, and it is difficult to separate in gravity separation. Lead-zinc ore has high surface activity and “grabs collectors” with cassiterite in flotation. Therefore, this will cause the impurities such as sulfur and lead in the concentrate to exceed the standard, and the concentrate grade will be difficult to meet the standard.
Solutions for multi-metal tin ore process:
Process optimization: Use lime (to adjust pH) + copper sulfate (to activate pyrite) as a combination reagent, first flotation to remove pyrite, and then separate tin. A combined process of magnetic separation for iron removal → flotation desulfurization → gravity enrichment of tin can be used.
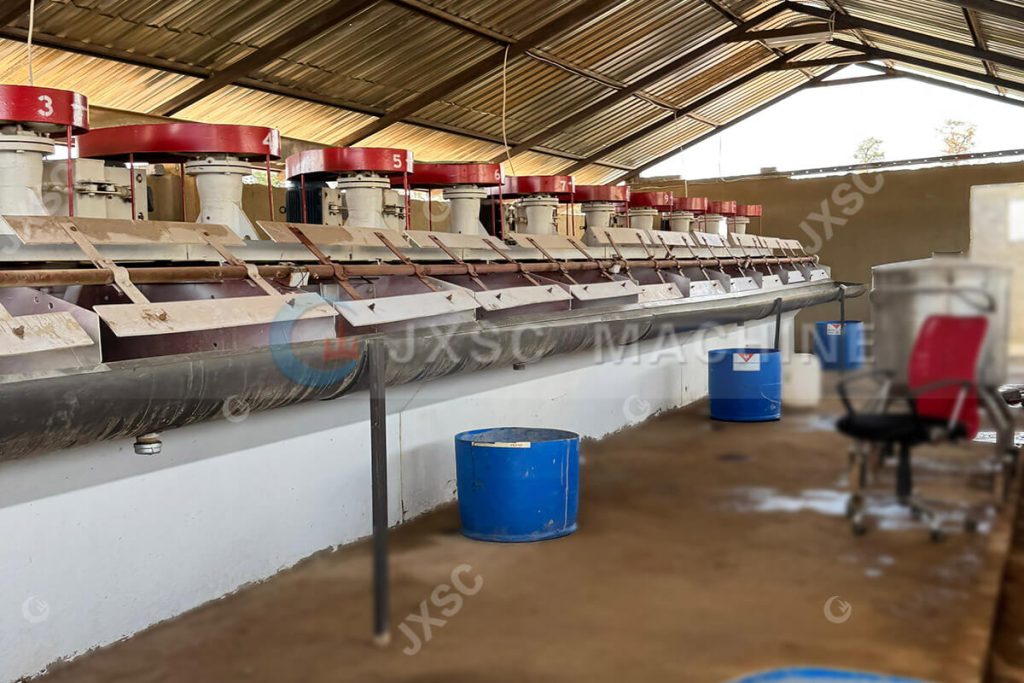
3. High energy consumption and cost pressure
Problem manifestation: Grinding accounts for 60% of the total energy consumption, and the flotation machine consumes a lot of electricity when running 24 hours a day. The overall electricity cost is likely to exceed the concentrate selling price, and the economic benefits of mineral processing will decline. If low-grade ore is processed, it is more likely to lose money.
Solutions for the cost challenge:
Process optimization:
- Energy-saving grinding: Adopting the “semi-autogenous grinding machine + ball mill” combined process, semi-autogenous grinding uses ore self-grinding to reduce steel ball consumption, which can reduce power consumption by 20%.
- Efficient sorting: Prioritize gravity separation, the energy consumption is only one-third of flotation, and coarse cassiterite is recovered. If it is a difficult-to-select fine ore, a flotation process can be added;
4. Tailings treatment, environmental protection is difficult to comply with
Problem manifestation: Ore dressing wastewater contains heavy metal from tin ore beneficiation such as lead and arsenic, and residual reagents. Direct discharge will cause environmental pollution. Tailings ponds often cover more than 100 acres, and there is a cost for expansion. If there is too much storage, it is easy to cause the risk of dam collapse on rainy days.
Solutions for tailings treatment:
- Wastewater circulation: “Clarification tank sedimentation + membrane filtration” achieves 90% return water utilization (reduces new water consumption);
- Tailing dry discharge: filter press reduces the moisture content of tailings to less than 20% (dry stack), replacing the traditional wet tailings pond;
The above challenges of tin ore beneficiation: fine particle loss, impurity interference, high energy consumption, environmental pressure, these problems are closely linked. The key to solving them is to coordinate the operation of “process + equipment + management“, focusing on the three core aspects of fine particle recovery, impurity separation, and energy saving and consumption reduction to optimize the solution. JXSC will disassemble one by one from process optimization to equipment upgrade, from impurity control to energy consumption management, and provide a feasible turnkey solution for tin ore dressing. Contact us now to customize the beneficiation solutions or equipment to achieve the triple goals of “efficient resource utilization + cost control + environmental compliance”.