Why has copper ore dressing technology become the “decisive factor” in the global mining industry? Copper, as an important basic material in the industrial field, plays an irreplaceable role in many industries such as power transmission, electronic equipment manufacturing, and transportation. Copper ore dressing is the process of separating copper minerals in ore from other impurities through a series of technologies. However, in the face of low-grade, complex and “difficult to chew” ores, how to efficiently extract copper metal requires more precise technology. For miners, facing different processes such as gravity separation, flotation, leaching-electrolysis, etc., how to choose an adaptation plan based on the properties of the ore (particle size, grade, symbiotic relationship), cost budget and environmental protection requirements is often the key to determining whether the project is profitable or not. This article will focus on these three mainstream processes, dismantling them one by one from principles, applicable scenarios to advantages and disadvantages, to help you quickly sort out the technical logic and provide the best reference for actual production decisions.
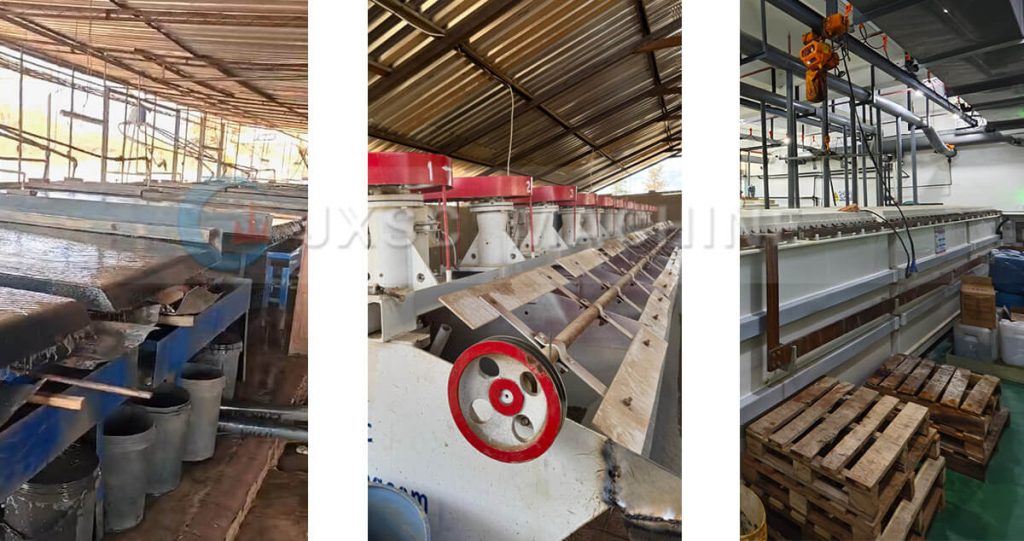
Copper ore dressing technology can improve the grade and recovery rate of copper concentrate, reduce the difficulty and cost of subsequent smelting, and achieve efficient utilization of resources. The three major processes of gravity separation, flotation, and leaching-electrolysis each have their strengths. Gravity separation is mainly used to process coarse-grained high-grade ores with low costs. Flotation is used for fine-grained complex ores with higher recovery rates. Leaching-electrolysis is used to process low-grade/oxidized ores with high resource utilization.
1. Copper Ore Dressing: Gravity Separation Process
Copper gravity separation is a classic mineral separation method based on physical separation. Its principle is to use the density difference between copper minerals and gangue to achieve effective separation of the two in a gravity field (usually with the help of water or air as a medium). It is especially suitable for processing coarse-grained oxidized copper ores or sulfide ores (such as malachite and chalcopyrite). When a mixture containing copper minerals and gangue enters a specific gravity separation environment, the copper minerals with higher density will settle at a faster rate under the action of gravity, while the gangue with lower density will settle relatively slowly, thus achieving the purpose of preliminary separation.
Key equipment of copper gravity separation:
- Jig concentrator: Through the reciprocating water flow, pulsation is generated to achieve the “layering-separation” cycle (suitable for 0.5-10mm coarse-grained ores). The processing capacity of a single unit can reach 50t/h, but the water pressure fluctuation needs to be strictly controlled.
- Shaking table: With the help of asymmetric reciprocating motion of the bed surface, the difference in mineral motion trajectory is used for sorting (0.02-2mm medium and fine particles), and the recovery rate of fine particles (-0.074mm) drops sharply to below 40%.
- Spiral chute: Relying on the dual effects of centrifugal force and gravity, it can sort 0.03-1mm minerals. It does not consume power, but the slope needs to be precisely adjusted.
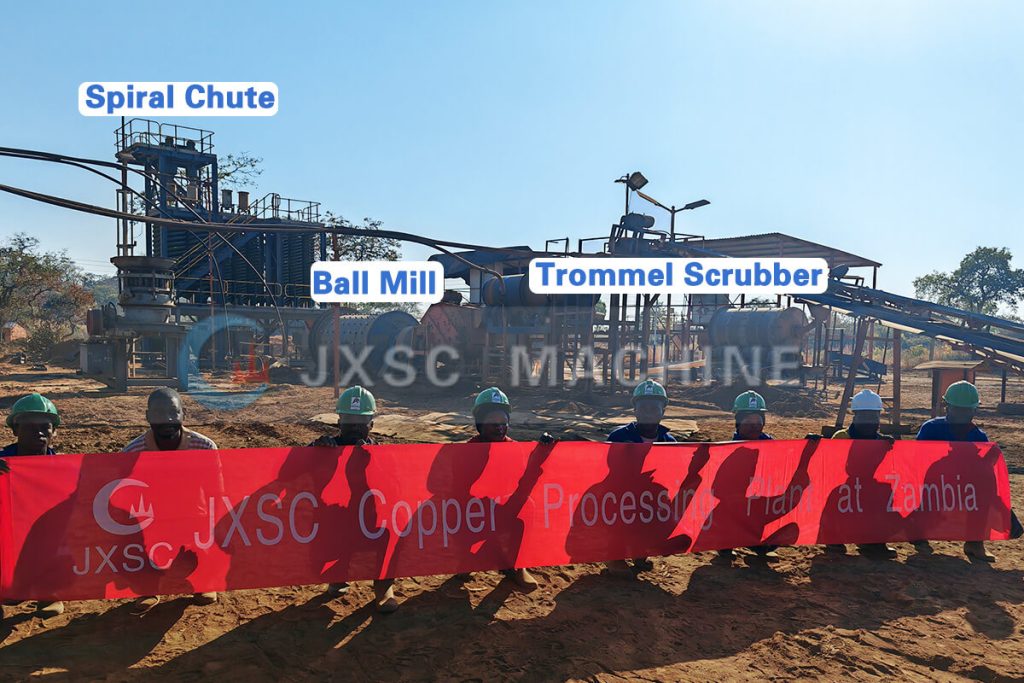
Technical features of gravity separation:
√ Advantages:
- Low cost: simple process, low energy consumption, and no need for cyanide and other reagents. The overall cost is 40% lower than flotation.
- Environmental protection: zero chemical additives throughout the process, and tailings can be directly discharged dry.
- Rapid production: The installation cycle is 30% shorter than flotation.
Χ Limitations:
Only suitable for coarse-grained copper ores. For fine-grained or complex copper ores, the recovery rate is low, generally less than 60%. In particular, it is almost ineffective for the beneficiation of complex paragenetic copper-lead-zinc ores.
2. Copper Ore Dressing: Flotation Process
The flotation process of copper ore is the core means to treat fine-grained and complex copper ores. Its core principle is to achieve separation through the difference in physical and chemical properties of the mineral surface. Specifically, the hydrophobic copper minerals are adsorbed on bubbles under the action of collectors (such as xanthate and chlorite), and rise with the foam layer to become concentrates; while the hydrophilic gangue minerals remain in the slurry to form tailings. It is mainly suitable for the beneficiation of copper sulfide ores (such as chalcopyrite and bornite), some low-oxidation mixed ores (oxidation rate <15%), and mixed copper ores.
Key steps Of copper Flotation
- Grinding: Dissociate copper mineral monomers (usually requiring -0.074mm to account for >80%), and the grinding fineness directly affects the recovery rate;
- Pulping: Adjust the pH value of the pulp (sulfide ores usually use pH 8-11, and oxide ores require pH 3-5), and add collectors + frothers + inhibitors (specific adjustments need to be made based on mineral information);
- Flotation: Mineralized foam separation is achieved through mechanical stirring or aerated flotation machines (such as XCF/KYF flotation machines), and the concentrate can be sent to the smelter after concentration-filtration and dehydration.
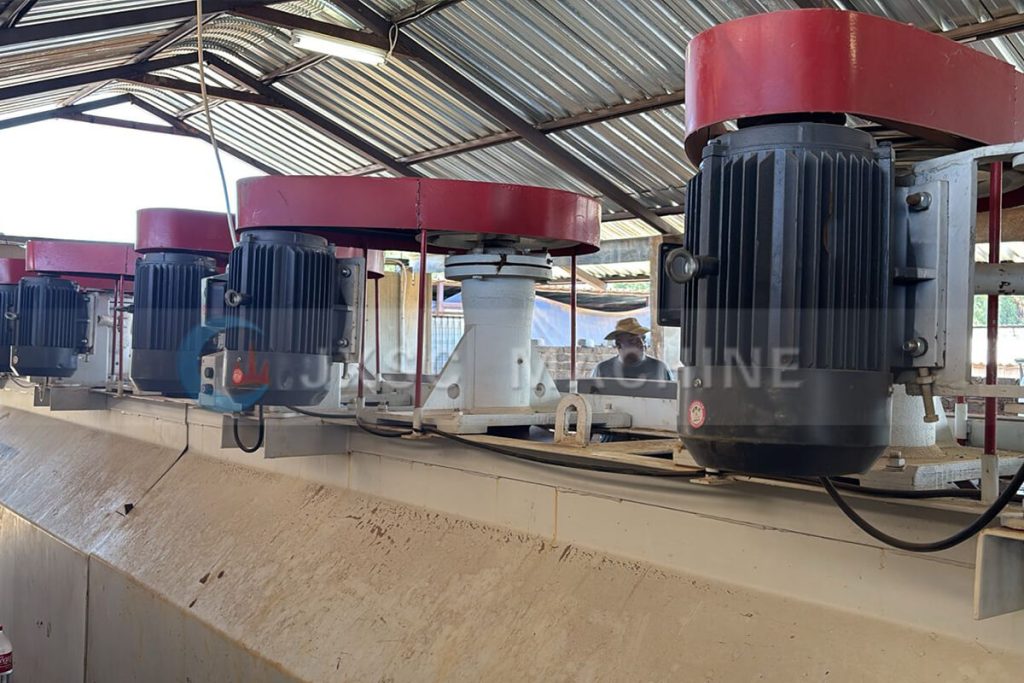
Technical features of copper flotation
√ Advantages: The “dominant advantage” of the flotation process lies in its efficient recovery of fine-grained and complex copper ores:
- Strong adaptability: It can process sulfide ores (chalcopyrite), oxide ores (malachite) and even ores with high mud content, and the copper recovery rate is usually 85%-95%.
- Multi-metal separation: Through preferential flotation or mixed flotation, different metals can be enriched from copper-lead-zinc-sulfur symbiotic ores.
Χ Limitations:
-High cost: The cost of reagents can reach 30%, resulting in high overall costs. Grinding consumes a lot of energy, which also accounts for 40% of the cost;
-Environmental pressure: A large amount of chemical reagents will be used in the flotation process, which may produce drug-containing wastewater. If it is not treated, it will pollute the environment. If a tailings pond is built, the cost will account for 20%.
3. Copper ore leaching-extraction-electrolysis
The copper ore leaching-electrolysis process is an efficient extraction solution for low-grade (Cu≤0.5%) and difficult-to-select oxidized copper ores (such as malachite and chrysocolla). Due to the low copper content and complex intercalation of such ores, large-scale grinding and high reagent consumption are required for copper beneficiation (gravity separation or flotation), and the cost far exceeds the benefits. While the leaching process does not require deep grinding (only simple crushing is required), and copper is directly extracted through solution reaction, which increases resource utilization by 20%-30% compared with traditional processes, and can even recover residual copper in mine waste rock and tailings. This method can directly obtain electrolytic copper products. Although the cost is high, the product purity is relatively high. Through acid leaching, the oxidized copper ore is converted into soluble copper salts, and then copper is obtained through extraction and electrolysis.
Key steps of copper leaching & electrolysis
- Leaching: Heap leaching involves piling the ore in a special site and spraying it with a leaching agent to dissolve the copper; it is suitable for open-pit low-grade mines with good permeability. Stirred leaching is carried out in a stirred tank, which can speed up the reaction rate; it is suitable for high-grade or fine-grained ores.
- Extraction: The copper in the leachate is selectively enriched and extracted using an extractant to increase the copper concentration and remove impurities such as iron.
- Electrolytic deposition: It is carried out in an electrolytic cell to deposit copper ions on the cathode.
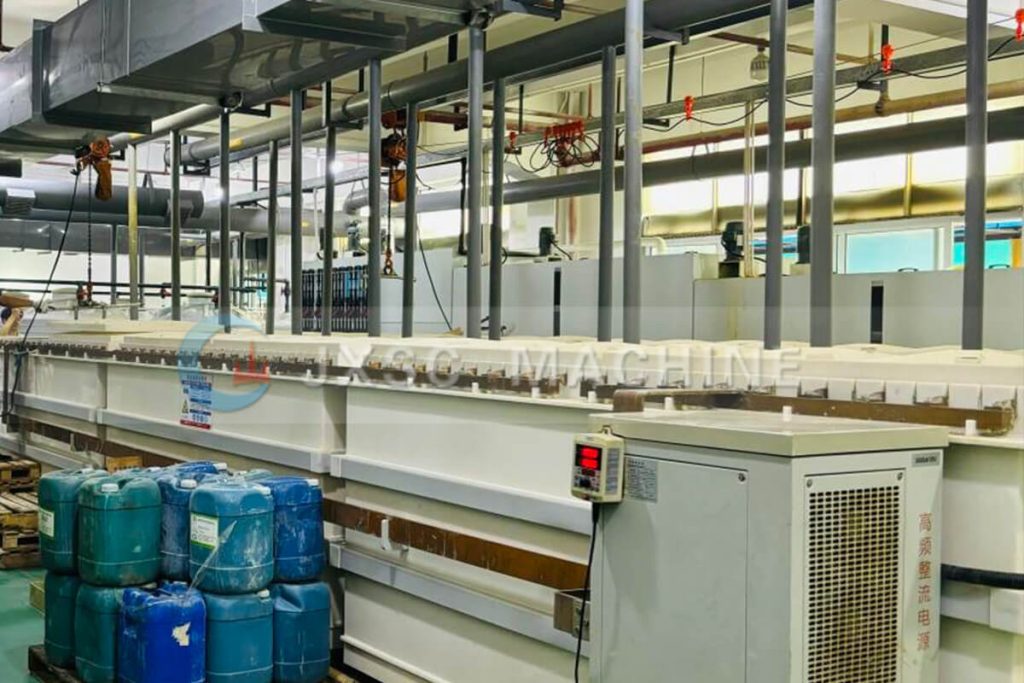
Technical features of leaching-extraction-electrolysis
√Advantages
- Handle extremely low-grade ores: It can economically handle oxide ores with a grade as low as 0.2%, clay-type copper ores with high mud content, and even residual copper in tailings ponds.
- Green and low-carbon: Compared with pyrometallurgy, waste rock piles can be repaired in situ, and bioleaching does not emit sulfur dioxide.
- High purity: The purity of the finished product is as high as 99.99%, which can directly meet the steel material standards.
Χ Limitations:
-Long time: Heap leaching takes several months to complete copper dissolution, which is much slower than the hourly processing of flotation.
-High particle size requirements: If there are few cracks in the ore, it is difficult for the leaching agent to contact the mineral, and the leaching rate may be less than 50%.
High cost: The energy consumption in the electrolytic deposition process is extremely high, accounting for more than 40% of the total cost.
Comparison of the three major mainstream processes: How to choose?
Indicator/ Process | Gravity Separation | Flotation | Leaching-Electrowinning |
Applicable Ore Types | Coarse-grained sulfide ore/primary ore | Fine-grained sulfide ore/polymetallic ore | Low-grade oxidized ore/waste rock |
Recovery Rate | 60%-80% | 85%-95% | 70%-85% (depending on leaching conditions) |
Environmental Friendliness | No chemical pollution | Need to treat wastewater with reagents | May generate acidic wastewater |
There are three mainstream processes for copper ore dressing: gravity separation has become the preferred choice for coarse-grained high-grade ores due to its simple process and low cost; flotation is the “mainstream solution” for fine-grained complex ores with its high recovery rate and strong adaptability; leaching-electrolysis has opened up a new path for resource recycling for low-grade ores and difficult-to-select oxidized ores with its ability to “turn waste into treasure”. When selecting a process, it is necessary to comprehensively consider core factors such as ore particle size, grade, symbiotic relationship, cost budget, and environmental protection requirements. JXSC supports customized ore dressing solutions and equipment. Contact our experts for direct answers!