Chrome ore refers to natural deposits containing chromium in its original form. A hard, shiny, and corrosion-resistant metal, chrome ore is usually found in the earth’s crust in the form of chromite. Chromite is composed of chromium, iron, and oxygen. Chromium is usually extracted from the ore through various mineral processing processes. In the field of chrome ore processing, the plant is like a complex ecosystem that transforms raw mineral deposits into valuable resources. The purpose is to extract the chromium element from the chrome ore and obtain high-grade chrome concentrate. Whether it is alluvial or rock mineral, the chrome ore processing process generally includes a combination of washing, crushing, grinding, classification, gravity separation, magnetic separation, etc., to recover chrome concentrate with high efficiency.
Characteristics of chrome ore processing flow
These differences processing of alluvial chrome ore and rock chrome ore, mainly due to the different physical and chemical properties of the two ores and their different occurrence states in nature, and the preferred beneficiation methods are different.
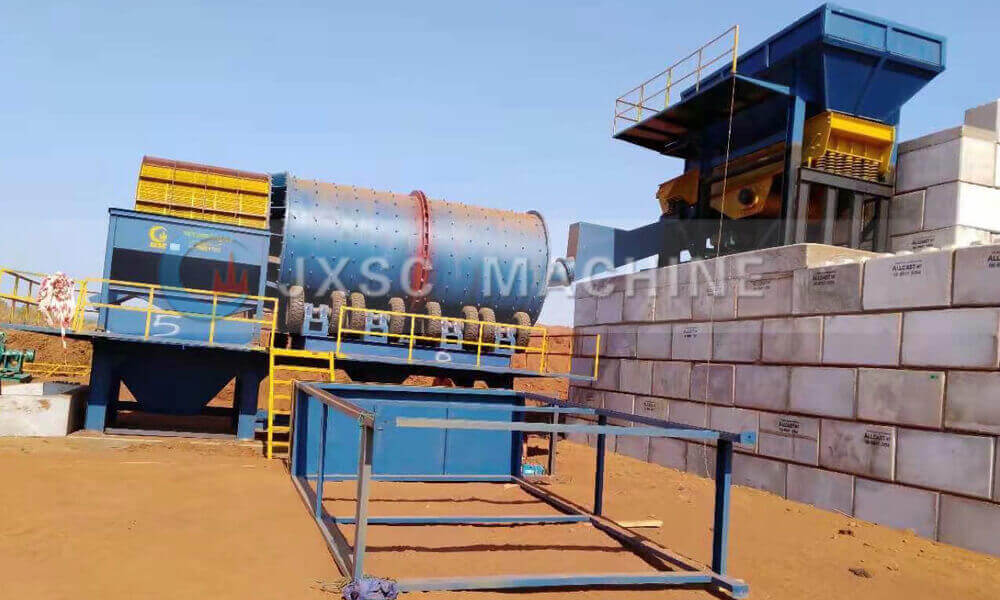
Characteristics of alluvial chrome ore process
Mining method: Sand chrome ore usually exists in sandy or alluvial deposits. The mining process is relatively simple and does not require deep excavation or blasting.
Main process: Due to its fine particle size and high density, sand chrome ore mainly uses gravity separation methods, such as shaking tables, jigs, spiral processes and other equipment to achieve the separation of chromite from gangue minerals.
- Dependence on beneficiation methods: It usually contains more slime impurities and needs to be deslimed and cleaned through the ore washing process. More reliance on physical methods to separate and enrich chromite, because the chromite in sand chrome ore is small in particle size and easy to be separated by gravity separation.
- Particle size control: During the processing process, the particle size control requirements are high to ensure sorting efficiency and product quality.
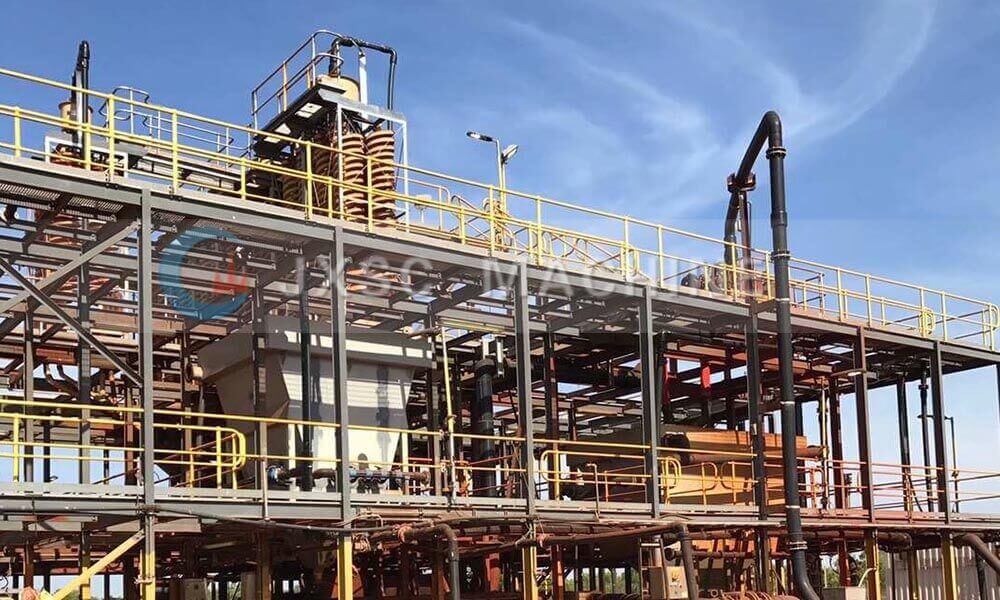
Characteristics of rock chrome ore process
Mining method: Rock chrome ore is usually embedded in solid rock, and the mining process may involve deeper excavation, blasting, and crushing operations.
Main process: Rock chrome ore processing often requires crushing and grinding to reduce the ore’s particle size. Since chromite may be enclosed in other minerals, magnetic separation, flotation, or other chemical treatment methods may be required for further separation.
Dependence on beneficiation methods: Rock chrome ore processing may rely more on physical and chemical processes such as magnetic separation and flotation, mainly when chromite is closely associated with other minerals.
Particle size control and fine grinding: Since rock chrome ore is usually found in harder rocks, more complex grinding processes may be required in the processing process to achieve sufficient dissociation, which is beneficial to the subsequent beneficiation steps.
chrome ore processing flow
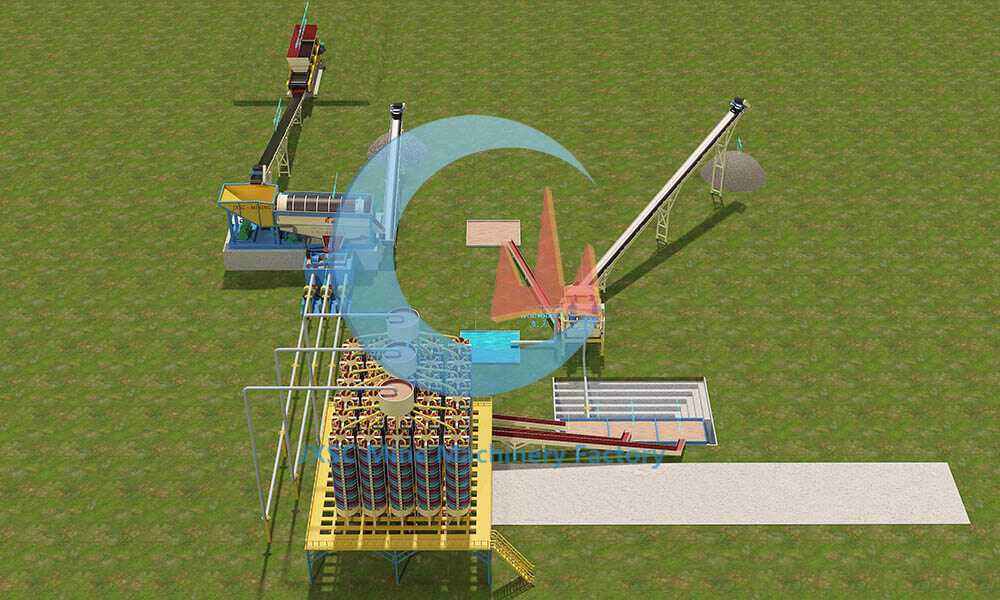
100TPH alluvial chrome ore processing plant
This complete system is a 100 tph alluvial chrome ore processing plant, configured with a hopper+belt feeder, trommel screen, belt conveyor, slurry pump, spiral chute, and dewatering screen. The whole process is as below:
(1) Excavator or truck sends raw ore into the raw material hopper, through a belt feeder evenly fed trommel screen by belt conveyor.
(2) Trommel screen for sieving out 0-2 mm and 2-70mm. 2-70mm are sent to the waste stockpile via belt conveyor. 0-2mm go to slurry tank.
(3) Use a slurry pump to send 0-2mm to the first stage spiral chute group for separating out chrome concentrate, middling, and tailing. (tailing go to tailing pool)
(4) Middling from the first stage spiral chute group to the second stage spiral chute group by slurry pump for further processing, the middling from the second stage spiral chute will pump to the third stage spiral chute, this can recovery more chrome concentrate.
(5) Chrome concentrate from three stages of spiral chute groups go to the concentrated pool, middling go to the middling pool, tailing will go the the tailing pool
(6) Dewatering screen for dewatering the tailing to get the clean water as the feeding water for the trommel screen.
This whole setup is suitable for large processing capacity and is cost-effective with a good recovery effect.
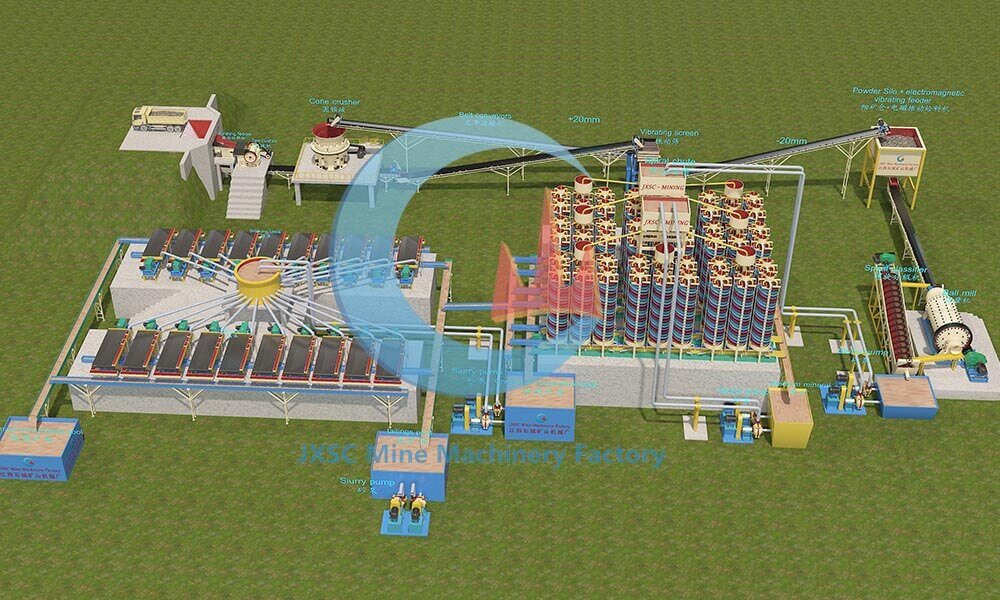
rock chrome ore processing plant flow
This Setup is a rock chrome ore processing plant, it is configured with raw material feeding, primary crushing, fine crushing, screening, ball mill grinding, and gravity separation to separate out and upgrade Chrome concentrate.
The chrome ore raw material stone is fed to the primary jaw crusher by a vibration feeder, so can feed rock chrome ore smoothly and evenly. The vibration feeder is with the grizzly bar to grizzly oversize to a primary jaw crusher, under grizzly bar small size material go to the fine crusher by conveyor. So as can increase the crushing effect of the primary jaw crusher.
The primary jaw crusher is for crushing big rock chrome ore to a smaller size, output material to go next fine crushing machine cone crusher. Cone crusher is crushed rock chrome to below 20mm that suitable feed to ball mill but firstly will go to a vibration screen for screening out oversize+20mm send back to cone crush crushing again. Under screen 0-20mm go to storage bin before ball mill. If a small capacity plant, the cone crusher can be replaced by another type of fine crusher, such as a fine jaw crusher or hammer crusher or impact fine crusher, etc.
The 0-20mm powder material will be sent to the ball mill smoothly by an electromagnetic vibration feeder and belt conveyor. The ball mill is for grinding 0-20mm to small powder, it works together with the spiral classifier, so overflow slurry from the classifier is about 80% 200mesh powder, the oversize particle from classifier will go back to ball mill grinding again, to form a closed-loop.
The 200mesh slurry will be pumped to a gravity separation machine, spiral chute, and shaking table, the spiral chute is for primary concentration. In order to increase the chrome recovery ratio to maximum, we use a 2-stage spiral chute separation. The middling material from the 1st stage spiral chute group will be pumped to the 2nd stage spiral group, so as can recover as much chrome as possible.
All the heavy concentrate ore that is discharged from two stages spiral separators group will go to shaking table for concentrate again, to get higher grade chrome concentrate.
This setup plant design can be customized according to the customer’s chrome ore conditions, if need much higher grade chrome concentrate, can consider adding a high-intensity magnetic separator at the final stage. The plant capacity also can be as per request, such as 2tph,5tph,10tph,15tph,20tph, etc.
The processing of alluvial chrome ore and rock chrome ore includes a series of physical and chemical treatment steps to extract commercially valuable chromium from sand and rock. Due to its natural state and particle size characteristics, alluvial chrome ore processing is relatively simple and focuses on physical separation methods. Rock chrome ore processing is more complicated and may require a combination of physical and chemical methods to achieve effective separation, especially when the mineral interpenetration relationship is complex. The specific process needs to be adjusted according to factors such as ore deposit characteristics, technical conditions, and market requirements. JXSC supports the customization of various mineral processing solutions and equipment. Contact us for more details and machine prices!