What is dolomite
The main components of dolomite ore are calcium carbonate and magnesium carbonate. They are carbonate minerals, including ankerite and manganese dolomite. Dolomite has surface adsorption, can provide a source of magnesium and calcium, has high refractoriness, a large specific surface area, and good heat insulation and heat preservation effects. It is widely used in building materials, ceramics, glass and refractory materials, chemical industry, agriculture, environmental protection, energy saving and other fields. It is mainly used as a flux for alkaline refractory materials and blast furnace ironmaking; for the production of calcium magnesium phosphate fertilizer and magnesium sulfate; and as an ingredient for the production of glass and ceramics.
Dolomite belongs to the trigonal crystal system. The crystals are curved saddle-shaped rhombohedrons. The aggregates are crystalline granular and dense blocks. It is often symbiotic with calcite, clay, chert and magnesite. In addition, there are impurities such as mica, quartz, talc, iron-containing minerals, etc. At this time, mineral processing and purification must be carried out. After beneficiation, high-grade dolomite can be produced with improved properties, making it more suitable for a wide range of applications and increasing its market value.
Dolomite beneficiation and purification methods
Dolomite is an important mineral used in a variety of industries, including construction and agriculture, and needs to be refined and purified to improve its quality and properties. Generally, dolomite can meet the needs only after crushing and screening. Some ores need to be washed to remove clay impurities. Only a few dolomite mines in the world are beneficiated. Ore dressing and purification is mainly a process of removing harmful impurities in dolomite ore. There are mainly gravity separation, flotation and magnetic separation, which not only improve the purity of dolomite, but also reduce the impact on the environment by minimizing the generation of waste materials.
- Gravity separation:
That is, dolomite ore is separated from impurities based on its density difference. This method can effectively remove contaminants such as silica and iron oxide, improving the overall quality of dolomite products.
- Flotation:
By adjusting the pH and using suitable reagents, dolomite can be selectively separated from other impurities, such as silicate minerals. Flotation is a versatile method for improving the purity of dolomite through selective recovery of valuable components.
- Magnetic separation
Magnetic separation mainly removes iron-containing impurities from dolomite ore. By applying a magnetic field, iron particles can be effectively extracted, thereby improving the overall quality of the dolomite product.
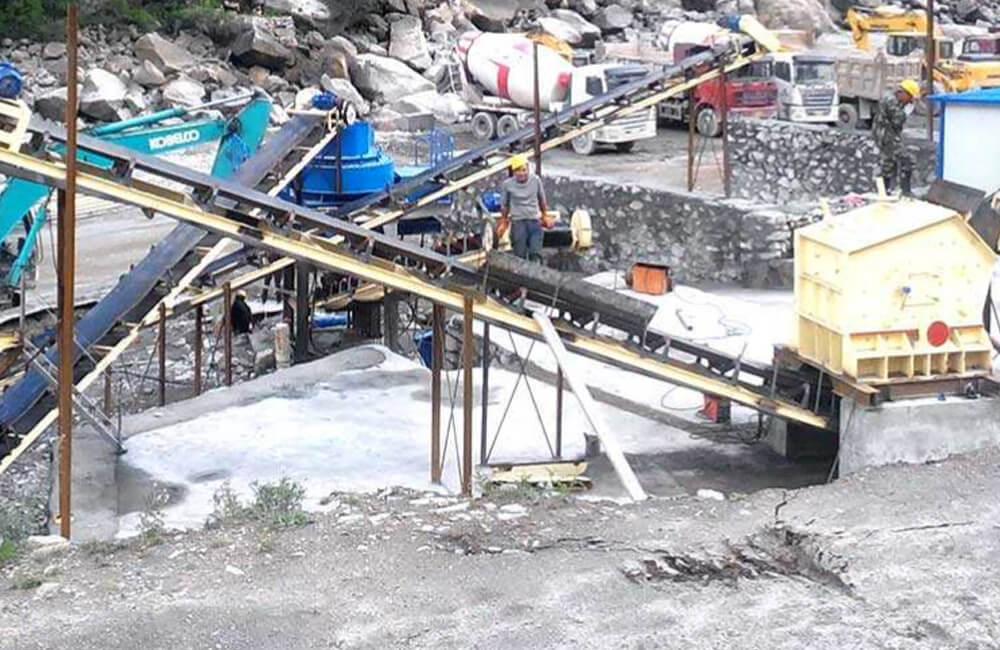
Dolomite beneficiation and purification plant
First, the raw dolomite is crushed and screened to remove any impurities. It then goes through a calcination process, which heats the dolomite to high temperatures to remove carbon dioxide and other volatile elements.
Next, the calcined dolomite is ground into a fine powder and then further processed through various techniques such as flotation or magnetic separation to separate the dolomite from other minerals.
1. Crushing process
The first step in the process involves primary crushing, using heavy machinery to break large chunks of dolomite into smaller pieces. This initial crushing stage plays a crucial role in determining the final size and quality of the dolomite aggregate produced. After primary crushing, the dolomite undergoes secondary and tertiary crushing processes to obtain the desired particle size distribution. These subsequent stages involve further reduction of the dolomite particles through multiple crushers to ensure a consistent quality and particle size distribution in the final product.
2. Calcination
Then, it goes through a calcination process, where the dolomite is heated to high temperatures to remove carbon dioxide and other volatile elements.
3. Grinding process
Next, the calcined dolomite is ground into a fine powder, which is then further processed and purified through various techniques such as flotation or magnetic separation.
4. Flotation process
Condition the slurry with reagents to promote the separation of dolomite from other minerals. Then it enters the flotation machine, using bubbles to selectively adhere and separate the required dolomite particles. Generally speaking, by adjusting the pH using alkaline or acidic reagents, operators can optimize dolomite recovery conditions while minimizing interference from other minerals.
5. Magnetic separation process
Dolomite sometimes contains iron impurities, in which an electromagnetic coil generates a strong magnetic field that separates the iron-containing impurities from the dolomite. Reducing the iron impurity content, the magnetic separator can precisely separate the impurities, ensuring that only pure dolomite is collected at the end of the process.
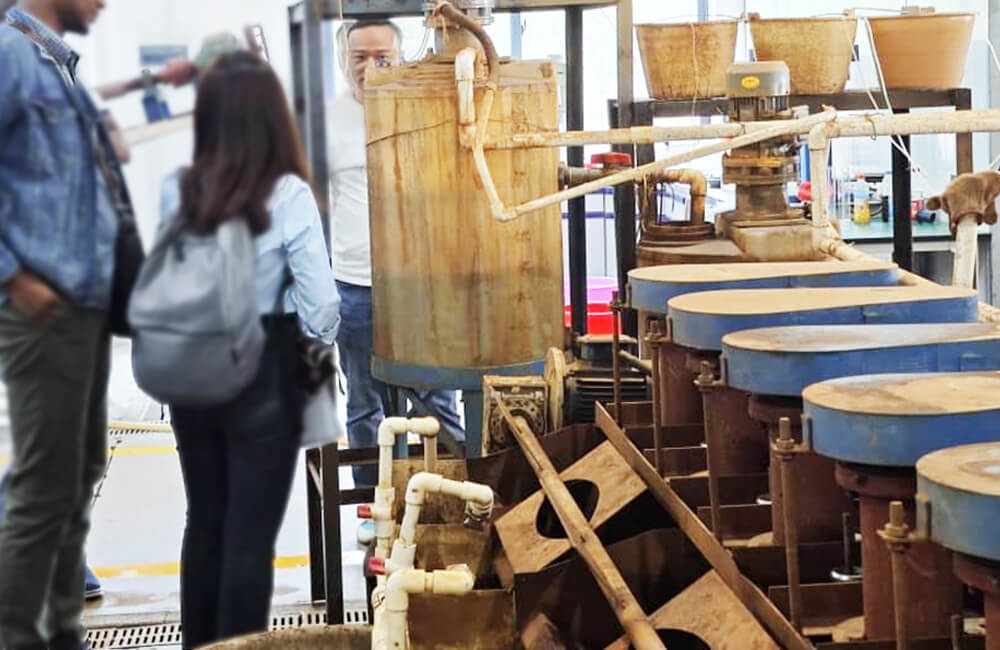
Dolomite beneficiation and purification can convert dolomite raw materials into valuable minerals. Finally, purified dolomite can be used in a wide range of applications including building materials, agriculture, and pharmaceuticals. By carefully following each step in the process, manufacturers can ensure they produce a high-quality dolomite product that meets their customers’ specific needs while minimizing waste and maximizing efficiency. For specific processes, please contact JXSC. We support customized mienral processing solutions and equipment, contact us for more details!