Kaolin is a white clay mineral widely used in various industrial applications, including papermaking, ceramics, rubber production and cosmetics. However, extracting high-quality kaolin from the ore can be challenging due to its complex and variable composition.
To improve the purity and value of kaolin products, it is very necessary to use beneficiation methods. Mainly divided into kaolin dry and wet beneficiation methods, it has revolutionized the extraction process by improving product quality while minimizing environmental impact.
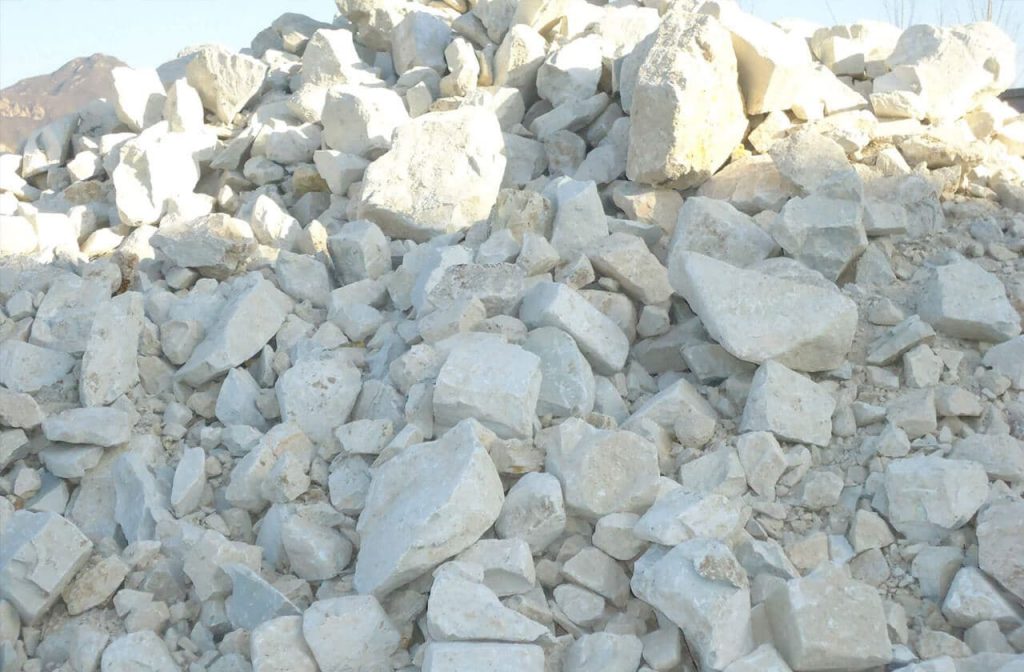
Kaolin dry beneficiation Method
Dry beneficiation is a commonly used kaolin ore separation method, which mainly realizes the separation of ores through the difference in physical properties. It involves crushing, screening, grinding, sorting, etc. of kaolin ore using mechanical equipment to obtain the desired products. Dry beneficiation is usually suitable for some fields with less strict product requirements, such as building materials, fillers, etc. The following are the steps and main advantages of the dry beneficiation method:
1. Ore crushing and grinding: Kaolin ore first needs to go through the process of crushing and grinding to reduce the ore particle size for subsequent separation operations.
2. Screening: The ore after grinding will be sent to the screening equipment and classified through different sieve hole sizes to separate the ore particles with different particle sizes.
3. Gravity separation: After sieving, gravity separation can be carried out according to the density difference of ore particles. Commonly used gravity separation equipment includes centrifuges, gravity concentrators, etc., which separate particles of different densities through centrifugal force or gravity.
4. Winning: Kaolin usually contains some impurities, such as quartz, iron, etc. Air separation separates impurities and kaolin in the airflow using the difference in particle size and density. This can be achieved with equipment such as air classifiers, cyclones, etc.
5. Magnetic separation: It can be used if the kaolin ore contains magnetic impurities, such as iron minerals. Magnetic separation uses the adsorption of magnetic materials on magnetic particles to separate them.
6. Dry Flotation: Dry flotation is a sorting method based on particle surface properties and is suitable for kaolin-containing moisture-sensitive impurities. The moisture-sensitive particles can be separated by hydrophilicity at the gas-solid interface through specific flotation agents and sorting conditions.
7. Sintering: In the final stage of the dry beneficiation process, the sorted kaolin particles can be sintered to improve their physical properties and chemical stability.
Advantages of the kaolin dry beneficiation method:
- Wide range of applications: Dry beneficiation is suitable for kaolin ore with larger particles and can process coarser ore.
- No need for water source: Dry beneficiation only requires a few water resources, so ore treatment can be effectively carried out in areas where water resources are scarce, reducing the dependence on water resources.
- Lower energy consumption: The dry beneficiation process does not require energy consumption for wet grinding, so it can sometimes have lower energy costs.
- Simplified process: Compared with wet beneficiation, dry beneficiation is relatively simple, reducing some equipment and steps, which may reduce investment costs.
In actual operation, it is necessary to select the appropriate dry beneficiation method according to the characteristics of ore and production requirements.
Kaolin Wet Beneficiation Method
Wet beneficiation of kaolin is another method of processing kaolin; compared to dry processing, it involves using water as a processing medium to separate, purify and process kaolin through steps such as suspension, sedimentation and separation. Water separates impurities from the clay during this process by forming a slurry mixture. The clay is then dispersed in water and stirred to break up any large particles or aggregates. Subsequently, flocculation and centrifugation are used to separate unwanted minerals and organics from the kaolin. Wet beneficiation is usually suitable for fields with strict product purity and particle distribution requirements, such as ceramics, enamel, advanced ceramic materials, etc. The following are the steps and main advantages of kaolin wet beneficiation:
1. Ore Crushing and Grinding: Like dry processing, the first step in wet processing is to crush the raw kaolin ore into properly sized particles and perform the necessary grinding to refine particle size and increase surface area.
2. Flotation or agitation: Suspend the crushed and ground kaolin particles in water, and suspend the particles by stirring or injecting air bubbles to realize the particles’ dispersion.
3. Classification and Sorting: Particles are separated by settling and classification by taking advantage of the weight and size differences of the particles. Usually, equipment such as settling tanks or centrifuges are used to separate particles of different sizes.
4. Sedimentation and Separation: After agitation and classification, particles settle in water according to size and weight. The particles can be further separated depending on the settling rate to obtain the desired particle size.
5. Washing: Precipitated particles may also have some impurities, so a washing step is required to remove impurities and contaminants attached to the surface of the particles.
6. Filtration and Drying: Washed kaolin granules can be filtered to remove excess moisture and then dried to reduce the moisture content of the granules for future processing and applications.
7. Subdivision and packaging: After the above processing steps, kaolin particles can be subdivided to obtain products within a specific particle size range. The final product can be packaged for future sale and use.
Wet beneficiation can better control particles’ dispersion, separation and purification process and is suitable for applications that require highly pure and uniform particles, such as ceramics, enamel, and preparation of advanced ceramic materials. Processing parameters must be strictly controlled during processing to obtain a final product that meets the requirements.
Advantages of the kaolin wet beneficiation method
- High-quality concentrate: Wet beneficiation can more thoroughly separate the impurities in the ore to obtain higher-quality concentrate. It is suitable for beneficiation of kaolin with more impurities.
- Strong adaptability: wet beneficiation is suitable for ores of different particle sizes and can also adapt to different types of kaolin ores or powdered ores.
- High environmental protection: wet beneficiation uses water as the medium and relatively less chemical waste is generated, which is conducive to environmental protection.
Finding an efficient and cost-effective method of beneficiating kaolin is critical to maximizing its value in various industries. It is mainly divided into dry and wet beneficiation methods, and each has its advantages. The dry or wet beneficiation method choice depends on product requirements, equipment, energy costs and environmental factors. Dry beneficiation is more suitable for some fields with relatively loose product requirements, while wet beneficiation is more suitable for areas with higher standards for product quality. Using JXSC beneficiation methods, you can obtain performance-enhanced kaolin for various applications such as ceramics, paper and cosmetics.