Have you ever wondered how to achieve a stable supply of high-grade manganese ore in today’s booming global steel industry and continuous innovation in battery technology? Manganese is an indispensable element in many key industries such as steel manufacturing, battery production, and chemical industry, the quality of its ore directly affects the performance and quality of downstream products. However, manganese ores mined in nature are often mixed with many impurities such as gangue, which cannot directly meet the high standards of industrial production, making manganese ore beneficiation crucial. But extracting them efficiently challenges many miners. Choosing the wrong method leads to low recovery rates, wasted energy, and higher costs. For 40 years, we’ve helped mines in 40+ countries solve this high-value manganese beneficiation methods. Let me simplify your decision between gravity and magnetic separation.
Manganese beneficiation: Gravity separation works best for coarse manganese particles with clear density differences from waste materials. Magnetic separation targets fine particles with magnetic properties. The optimal choice depends on the ore type, particle size, and processing budget.
What is manganese beneficiation?
Manganese ore beneficiation refers to the process of using physical, chemical and other methods to separate manganese minerals from gangue and other impurities in manganese ore to increase the manganese content and purity in manganese ore. It mainly includes gravity separation and magnetic separation.
Ore characteristics affecting beneficiation
- Particle size: During the gravity separation process, coarse-grained ore can better utilize gravity to separate from impurities due to its fast sedimentation rate; while fine-grained ore is prone to incomplete separation during gravity separation, and may be more suitable for methods such as magnetic separation that are not so demanding on particle size.
- Density: The greater the difference in density between manganese ore and gangue, the better the gravity separation effect. In terms of magnetism, if the manganese ore in manganese ore has strong magnetism, magnetic separation can efficiently separate it from non-magnetic impurities.
- Mineral composition: Different mineral components have different chemical properties. Some may need to be treated by specific chemical beneficiation methods, while others can be separated by simple gravity or magnetic separation.
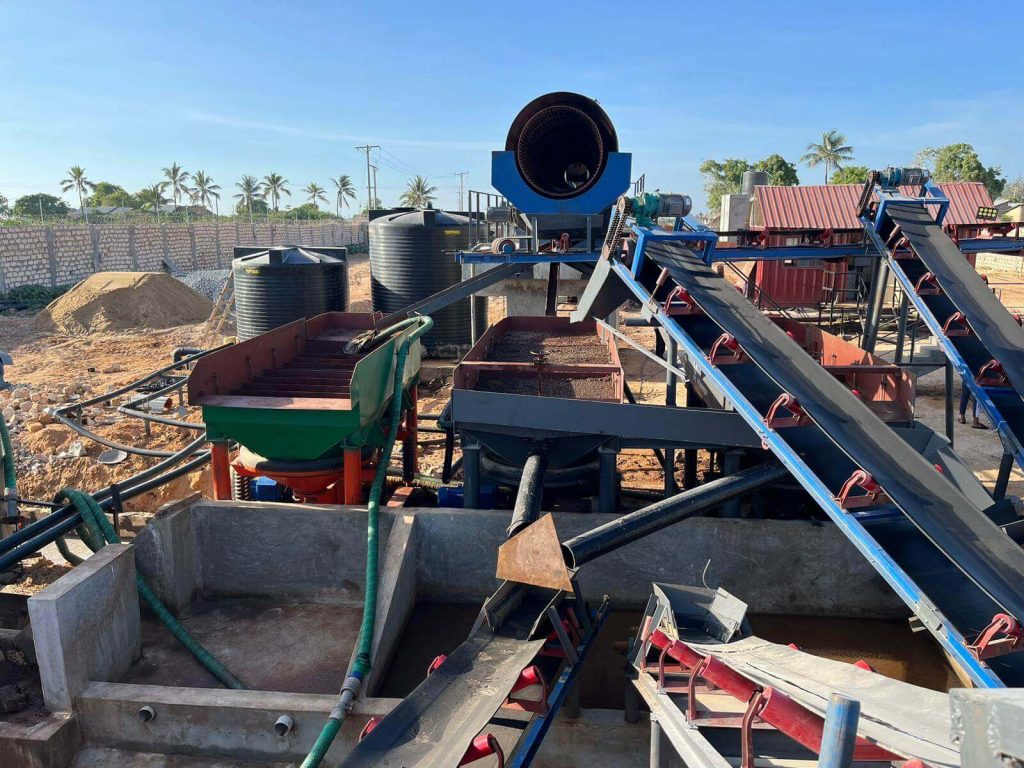
Manganese ore gravity separation method
1. Gravity separation principle
The core principle of gravity separation is to use the significant density difference between manganese ore and gangue minerals to achieve separation. During the gravity separation process, manganese ore is placed in a specific medium (usually water). Due to the different densities of different minerals, their sedimentation rates in the medium will also be different. Manganese ore with higher density settles faster, while gangue minerals with lower density settle relatively slowly. By controlling the speed and direction of the water flow and the movement state of the medium, manganese ore and gangue minerals can be enriched in different areas, respectively, thereby achieving the purpose of separation.
2. Gravity separation equipment
- When the jig is working, the speed and direction of the water flow are periodically changed to make the ore particles stratified according to density in the vertical alternating water flow. Manganese ore with high density will sink to the lower layer, while gangue with low density will remain in the upper layer, and then be discharged separately to achieve separation. It is suitable for processing coarse and medium-sized manganese ore.
- The shaking table uses the asymmetric reciprocating motion of the bed surface and the effect of the lateral water flow to make the ore particles fan-shaped on the bed surface, and separate them according to the density and particle size differences. It is often used for the selection of fine-grained manganese ore.
- The spiral chute uses the rotary motion of the slurry in the spiral trough to make the ore particles of different densities move along different trajectories under the combined action of centrifugal force, gravity, and friction, thereby achieving separation. It can beneficiate finer manganese ore, and the equipment has a simple structure and is easy to operate.
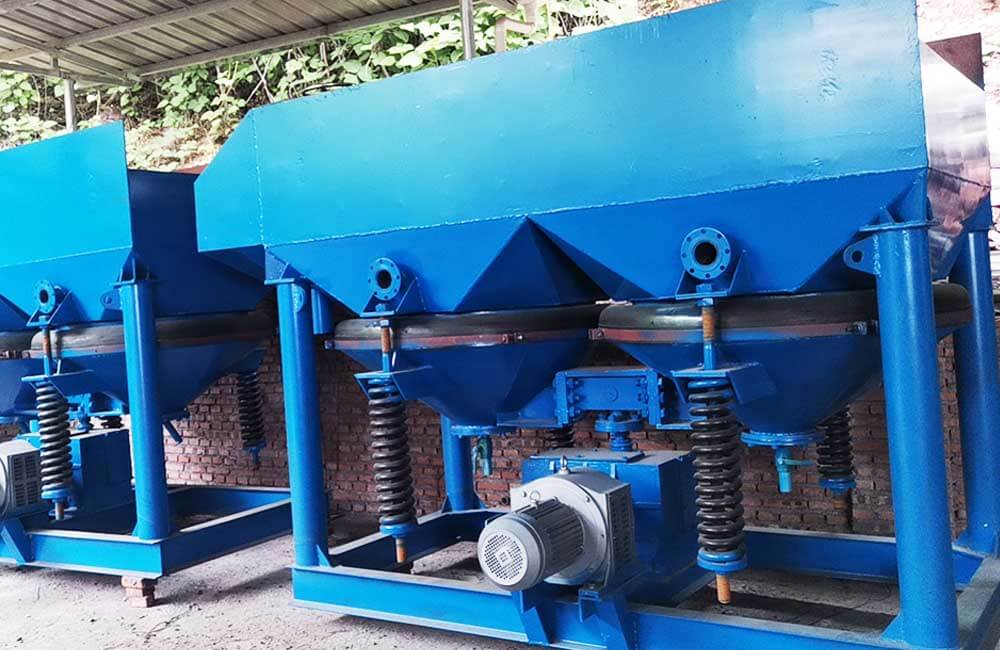
3. Advantages of gravity separation:
- It has high separation efficiency and can quickly and effectively separate manganese ore from gangue to obtain high-grade manganese concentrate.
- The operation is relatively simple and does not require complex process flow and professional technicians.
- The equipment cost is also low, and chemical agents are usually not required, which avoids the pollution of the environment caused by chemical agents and conforms to the development concept of green environmental protection.
4. Limitations of gravity separation
Χ For fine-grained ores or ores with small density differences, the separation effect of gravity separation is often poor.
Χ For complex ores, the recovery rate of gravity separation is limited. Complex ores may contain a variety of minerals, and their embedded relationships are complex. It is difficult for gravity separation to effectively recover all manganese minerals, which will cause a certain waste of resources and affect the economic benefits of mineral processing.
Manganese ore magnetic separation method
1. Principle of magnetic separation
The basic principle of magnetic separation is to separate manganese ore from non-magnetic gangue based on the magnetic properties of manganese ore. During the magnetic separation process, manganese ore is placed in a magnetic field environment. Because manganese ore is magnetic, it will be attracted by the magnetic force and deviate from its original motion trajectory under the action of the magnetic field force; the non-magnetic gangue is not affected by the magnetic field force and continues to move in the original direction. In this way, by reasonably setting the strength, direction and structure of the magnetic field, magnetic manganese ore and non-magnetic gangue can be collected in different areas respectively, so as to achieve the purpose of separation.
2. Types of magnetic separation equipment
- The magnetic field intensity generated by the low-intensity magnetic separator is relatively low, and it is generally suitable for sorting strongly magnetic manganese ores, such as some manganese ores containing strongly magnetic minerals such as magnetite.
- High-intensity magnetic separators can generate higher magnetic field intensity, which is suitable for sorting weakly magnetic manganese ores, such as rhodochrosite.
Manganese ore magnetic separation equipment includes drum magnetic separators, three-disc magnetic separators or high-intensity magnetic separators. Different types of magnetic separation equipment play their respective advantages in processing manganese ores with different magnetic properties according to the characteristics of their magnetic field strength.
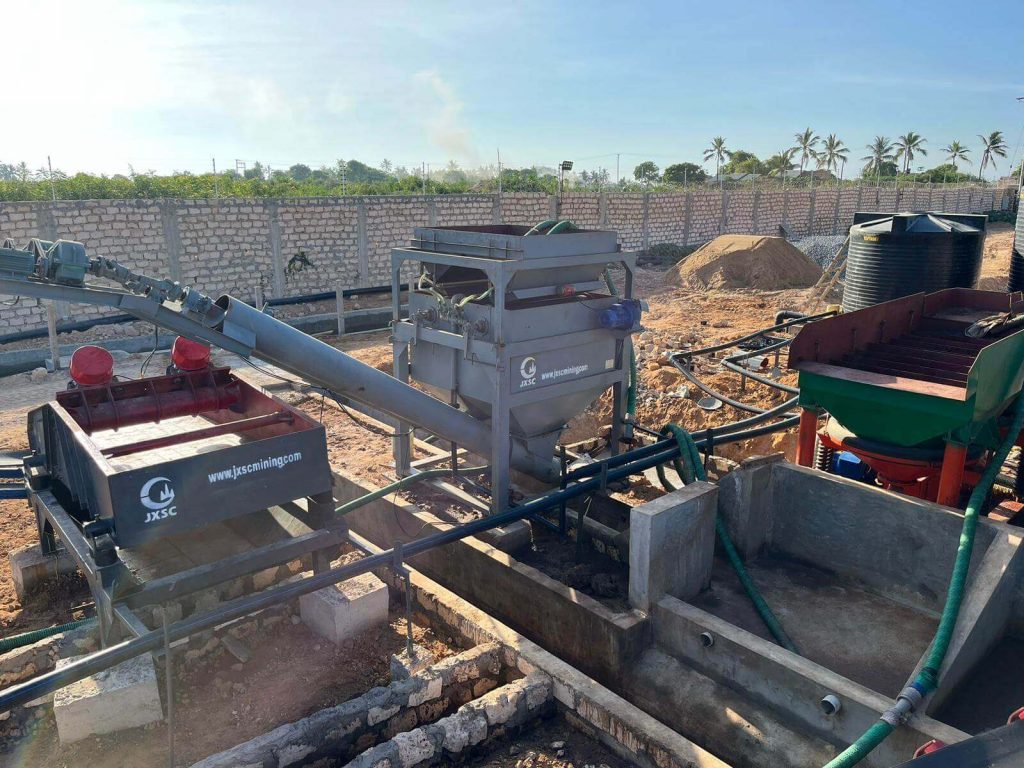
3. Advantages of magnetic separation
- It has high selectivity for magnetic manganese ore. It can accurately identify and separate magnetic manganese ore, while excluding non-magnetic impurities such as gangue, greatly improving the purity of manganese concentrate.
- It can effectively process fine-grained ore. For fine-grained manganese ore, other beneficiation methods may be difficult to achieve efficient separation, but magnetic separation is not too restricted by particle size and can use magnetic properties to separate fine-grained manganese ore.
- High-grade concentrate can be obtained by magnetic separation. Due to its high selectivity and effective processing capacity for fine-grained ore, manganese ore can be enriched as much as possible, thereby obtaining high-grade manganese concentrate to meet the demand for high-quality manganese ore in industrial production.
4. Limitations of magnetic separation
Χ High energy consumption is a more prominent problem, especially for high-intensity magnetic separators. Long-term high-energy consumption operation is also not conducive to energy conservation and emission reduction.
Χ It has limited applicability to non-magnetic or weakly magnetic manganese ores. Magnetic separation cannot work for almost non-magnetic manganese ores.
Gravity separation is based on the density difference between manganese ore and gangue. It is simple to operate, low-cost and environmentally friendly. It has high separation efficiency for coarse-grained ores with obvious density differences, but it is not effective for fine-grained ores with small density differences, and the recovery rate of complex ores is limited. Magnetic separation utilizes the magnetic properties of manganese ore and has high selectivity for magnetic manganese ore. It can effectively process fine-grained ores and obtain high-grade concentrates. However, it has high energy consumption and limited applicability to non-magnetic or weakly magnetic ores. When choosing a beneficiation method, it is necessary to comprehensively consider the ore characteristics and project requirements. Sometimes, crushing, grinding, washing, or screening processes are used in combination with beneficiation.
Whether you need a simple manganese beneficiation plant or a full EPC solution, we adapt to your ore’s unique personality. The right technology choice can boost your recovery by 20-40%. Contact our engineers with your ore specifics.