With the continuous mining of high-grade iron ore, the characteristics of the ore have become increasingly poor and miscellaneous. The average iron grade of iron ore is only 33%, and the associated relationships are complex and changeable, making it challenging to select high-grade iron concentrates. Iron ore is an essential raw material for ironmaking and steelmaking. It mainly comprises iron-rich minerals (hematite, magnetite, siderite, etc.) and gangue minerals (such as quartz and silicate).
Silicon is a typical impurity in iron ore. Because the silicon content of steel is too high (more than 0.5%), its elongation, shrinkage, and impact toughness will be significantly reduced. Therefore, ferrosilicon beneficiation to reduce its gangue mineral content and increase its iron content before it can be used as raw material for blast furnace smelting.
About silicon-iron minerals
Silicon-containing iron ores, also known as ferruginous silicon ores, are gaining attention in the steel industry due to their unique properties. Silicon-iron minerals are typical magnet-poor ores. Silicon is a specific harmful impurity in iron ore. Reducing the silicon content in iron ore concentrate has always been the focus of iron ore sorting. This ore has the characteristics of low grade, very fine particle size, high silica content, and complex composition. It is a relatively difficult ore to select among magnet ores.
The ore structure mainly includes fine-grained structure, other-shaped crystal structure, euhedral crystal structure, etc. The relationship between the iron minerals in the ore is complex. There are many types of iron minerals in ores; the most valuable iron mineral is magnetite, followed by hematite and limonite. Gangue minerals are mainly quartz, calcite, chlorite, actinolite, feldspar, clay minerals, etc.
Silicon-iron ore beneficiation
Silicon is found mainly in the form of quartz in iron ore. One of the critical characteristics of these ores is their high silicon content, which gives them exceptional strength and durability when used in steel production. Additionally, the silicon content in these ores helps reduce energy consumption during the smelting process, resulting in cost savings and environmental benefits.
Among them, the ferrosilicon ore beneficiation process involves purifying and increasing the silicon content in the iron ore, ultimately improving the quality and performance of the steel. Generally speaking, beneficiation ensures the production of high-grade ferrosilicon alloys critical in various industrial applications by effectively removing phosphorus, sulfur, and other contaminants from raw materials.
- For low-grade iron ore with fine particle size, flotation and magnetic separation–flotation combined beneficiation processes are often used to improve iron and reduce silicon.
- Iron ore and silicon-containing minerals have noticeable magnetic differences. After the two monomers are dissociated, silicon can be effectively removed through weak magnetic separation.
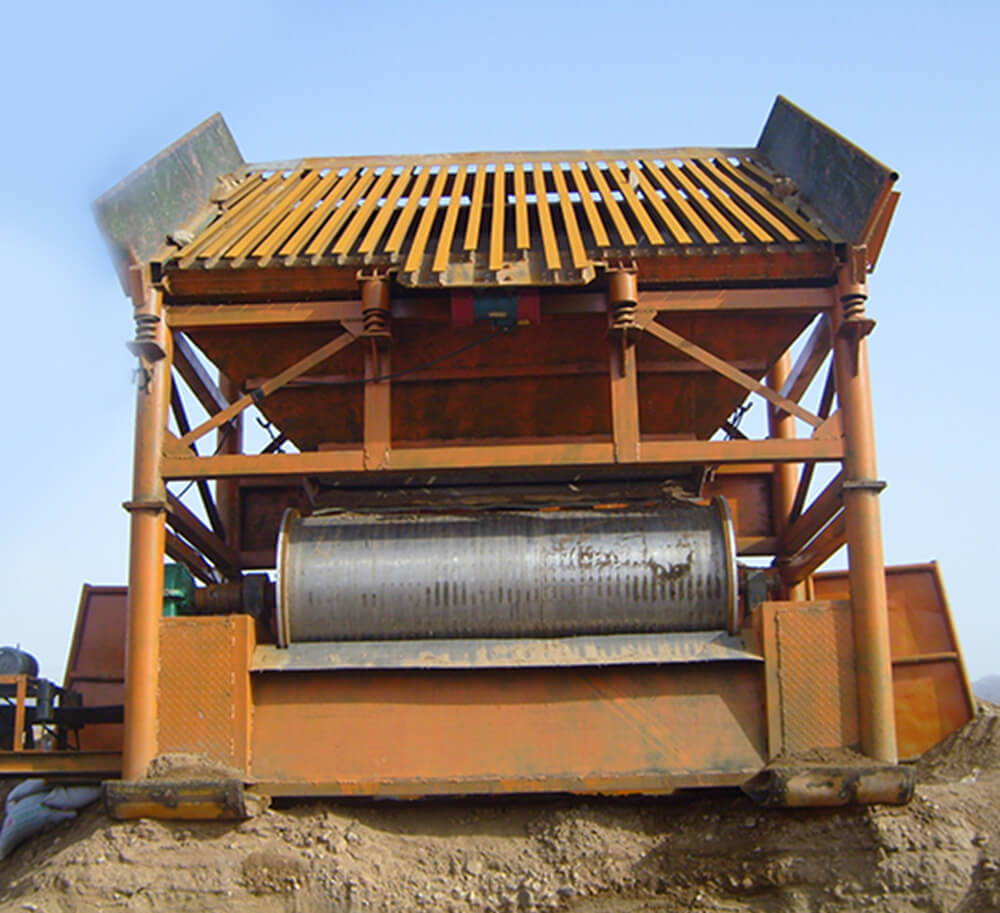
Silicon-iron ore beneficiation equipment
From gravity separators to magnetic separators to flotation machines, the latest equipment is designed to remove impurities and improve the purity of iron ore, ultimately increasing its quality and availability for various industrial applications.
- Silicon-iron ore gravity separation equipment
Gravity separation equipment has revolutionized the mining industry by providing an efficient and cost-effective method to separate valuable minerals from gangue material. This equipment uses advanced technologies such as centrifugal force and pulsating water flow to separate silicon and iron ore particles effectively based on specific gravity.
- Silicon-Iron Ore Magnetic Separation Equipment
It revolutionized the mining industry with its efficient and cost-effective method of separating valuable minerals. The device can effectively extract iron ore from silicon-rich ores by using strong magnetic fields, allowing for a more precise and profitable extraction process. The use of advanced gravity and magnetic separation equipment and technology can improve the final product’s quality, process efficiency, energy consumption, and environmental impact.
- Silicon-iron ore flotation equipment
Flotation equipment is pivotal in the ferrosilicon ore beneficiation industry, effectively separating valuable minerals from gangue. Using novel reagents has shown promising results in improving siderite flotation selectivity, better separations, and higher purity end products. Additionally, advances in automation and control systems have revolutionized the operation of flotation equipment, optimizing performance while minimizing human error.
Silicon-iron ore beneficiation methods
- The ore is crushed and ground into fine particles, which increases its surface area for better interaction with other reagents during the beneficiation process. This step is crucial as it directly affects the efficiency of subsequent processes such as magnetic separation and flotation.
- The use of advanced magnetic separation technology greatly improves the beneficiation efficiency of ferrosilicon ore. By applying a strong magnetic field, valuable iron-rich components can be separated from unwanted gangue minerals. The process is vital in obtaining high-purity iron concentrates while minimizing environmental impact through efficient resource utilization.
- Flotation: Iron ore undergoes froth flotation. This process uses differences in surface wettability to separate hydrophobic iron particles from hydrophilic gangue materials. The selective separation of different mineral phases based on surface properties further enriches iron content. This step further refines the iron concentrate, maximizing its purity and value for downstream applications such as steel production.
- Use gravity separation technology combined with magnetic separation. This method effectively removes impurities such as aluminum, phosphorus, and sulfur, producing a higher-grade, purer ferrosilicon ore product.
This ferrosilicon ore concentrator improves product quality and contributes to sustainable mining practices by minimizing waste generation and optimizing resource utilization.
The beneficiation of ferrosilicon ore is a complex process that requires careful consideration of various factors such as ore grade, mineralogy, and market demand. Using advanced equipment and technology can significantly improve the efficiency and effectiveness of the mineral processing process, resulting in higher-quality end products and reduced environmental impact. JXSC provides customized mineral processes plant and equipment to maximize recycling rates while achieving environmentally friendly production lines.