Types of Mineral Use Jig Machines
Jig machines for mining is one of the common gravity separation equipment. The working principle is separating the materials with different densities in the vertical lifting medium. According to the separation medium, the structure of equipment, the movement and other aspects, the jig machine can be divided into several types. In this article, we will let you know about the different types of jig machines for mining and their application.
According to the structure, the jig machine can be divided into piston jig, diaphragm jig, air pulsating jig, movable sieve jig and so on. Among them, the piston jig is an old type, which is basically not in use.
1.Diaphragm Jig machine
Diaphragm Jig machine is driving by the eccentric connecting rod, CAM lever or hydraulic equipment. According to the installation position of the diaphragm, it can be divided into up-motion(side-motion) diaphragm jig, down-motion cone diaphragm jig, side-moving diaphragm jig, which is the most useful type for gravity separation plant.
(1)Up-motion(side-motion) diaphragm jig
Up-motion(side-motion) diaphragm jig is most the equipment for roughing and concentrating. It is wildly used in the separation of tungsten, tin, gold and other metal minerals with large density. The separation particle size is from 0.2mm to 18-12mm. The characteristics are high enrichment and large stroke coefficient. There is only one type of up-moving diaphragm jig of 300mmx450mm, with double jigging Chambers in series. After the material is sorted by the first chamber, it enters the second chamber, and the two compartments reciprocate alternately to separate the material in the chamber.
(2)Down-motion cone diaphragm jig
The diaphragm of down-motion cone diaphragm jig is between the jigging chamber cone and movable cone. It is common as the roughing equipment for minerals with practical size under 6mm. The advantages are energy-saving and easy to pull out large density product, while the disadvantages are loose bed and worse effect in recovering coarse minerals under a large practical size.
(3)Side-moving diaphragm jig
This kind of mining jig machine has a trapezoidal face. The configuration is flexible. It has a short feeding part and a wide tailing part, which is an advantage for recovering fine ores. It is suitable for sorting minerals and gangue minerals with large mineral density and uneven mineral distribution. Sometimes, it is applied as the concentrating equipment for hematite and limonite.
2.Air pulsating jig
Air pulsation jig is also known as piston-free jig, which is characterized by air compression for sorting, according to different air chamber locations can be divided into sieve side air chamber (side drum) jig and air chamber jig under the screen. Air pulsation jig is mainly used as a coal sorting equipment.
3.Movable sieve jig
It can be divided into mechanical sieve jig and manual sieve jig according to the driving system. Manual sieve jig has been basically eliminated. Mechanical sieve jigger through hydraulic or mechanical force to drive the sieve plate to do reciprocating motion, to make the sieve plate on the material loose purpose. The moving sieve jig is mainly used as coal preparation equipment in large coal preparation or high cold water shortage areas.
Above are some types of jig machines for mining and their applications. Some key issues should be paid attention to when designing and selecting jig machines:
1. Conduct ore dressing test to understand the size range of materials and the dissociation of the monomer of useful minerals, and determine the size and density of artificial bed stone.
2. When the jigging chamber has a large area and the stroke coefficient is relatively small, if the hydrodynamic force is insufficient or uneven, the bed may be “consolidated”, this problem should be considered at the beginning of the design;
3. If there is a large amount of heavy sand in the mineral, it will be more difficult for jigging, which may lead to a decrease in the jigging operation rate. Check whether the sieve bed layer has deposited multiple sands in time, if this phenomenon should be promptly stopped to remove the material accumulated on the sieve.
4. When the material contains more primary ore mud or secondary ore mud, the mud removal operation should be increased in the design stage to obtain better separation effect.
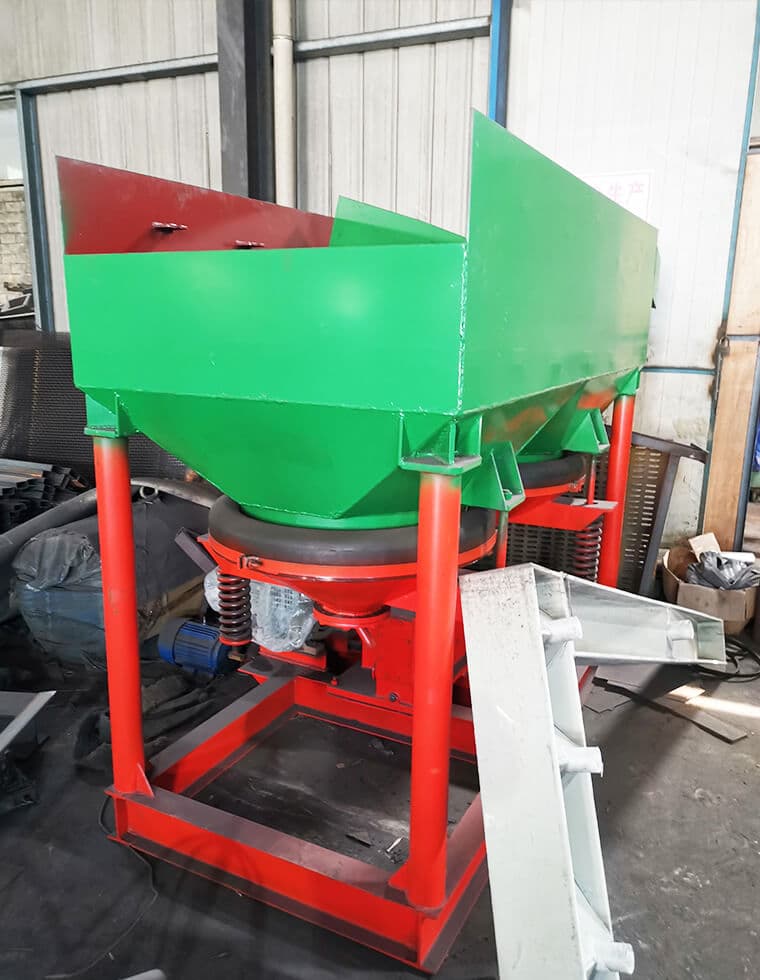
From this point of view, from the understanding of the type of jig to the actual application need to consider a comprehensive consideration of various factors, here it is recommended that the mine owner carry out ore dressing test and design in advance, by the construction of JXSC manufacturers with the qualification of customized equipment, selection and application to reach the expected level.
Products
Send Us A Message
More Posts
related solutions
- Placer Gold Process Plant
- Diamond Mining Process
- Silver Flotation Process
- Gold Flotation Process
- Gold CIL Processing Plant
- Gold CIP Processing Plant
- Dense Media Separation(DMS) Process
- Copper Processing Plant
- Lead Zinc Ore Processing
- Tungsten Ore Processing
- Magnetite Separation Plant
- Manganese Ore Processing
- Chrome Processing Plant
- Quartz Beneficiation Plant
- Phosphate Rock Processing
- Fluorite Ore Processing
- Tantalum Niobium Ore Processing
- Tin Ore Processing Plant
- Titanium Beneficiation Plant
- Graphite Ore Processing
- Hematite Separation Process
- Iron Ore Beneficiation Plant
- Kaolin Processing Plant
- Limonite Ore Dressing
- Lithium Processing Plant
- Magnetite Separation Plant
- Molybdenum Flotation Process
- Cobalt Ore Processing
- Nickel Ore Beneficiation
- Antimony Ore Processing
- Barite Ore Beneficiation
- Feldspar Processing Plant
- Coal Washing Process
- Beach Sand Beneficiation Plant
- Tailings Processing
- Chrome Wash Plant