Tungsten is known for its exceptional strength and high melting point. It is a vital metal in various industries, from aerospace engineering to electronic manufacturing, where it plays a vital role in the production of numerous important products. However, this versatile metal does not occur naturally in its pure form; it is found in almost every type of rock and must be extracted from its ores through a complex process.
As the demand for this versatile metal continues to increase, so does the need for efficient extraction methods from its ores. Extracting tungsten from its ore involves separating it from other minerals and impurities before it can be transformed into a useful product. Therefore, we use a highly efficient beneficiation process for tungsten ore, mainly includes gravity separation and flotaion process.
Types of Tungsten Ore
Tungsten ore, a crucial metal ore, plays a significant role in the production of tungsten and other related products. Here, we’ll explore several common types of tungsten ores.
- Scheelite: Scheelite is one of the most common types of tungsten ore, with a chemical formula of CaWO4. It usually appears yellow, brown, or light blue and has a glassy luster. Scheelite is a vital tungsten ore and widely used to manufacture alloys and other products.
- Wolframite: Scheelite is another common tungsten ore. It is usually black or brown-black in color and crystallizes in block or plate form. It is also an important ore, widely used to manufacture tungsten alloys.
- Aside from scheelite and wolframite, there is a diverse range of tungsten ores. These include tungsten tin ore in cassiterite, tungsten phosphate ore in apatite, and more.
Scheelite and wolframite, however, hold higher mining value and serve as the primary sources of tungsten ore resources. The extraction of tungsten ore requires the use of different beneficiation processss, depending on the specific type of ore.
Tungsten ore beneficiation process
It mainly includes physical methods such as flotation, gravity, and magnetic separation. Chemical beneficiation is preferred for difficult-to-select middlings and low-grade concentrates.
Gravity separation: Gravity separation is a method of sorting tungsten minerals and impurity minerals based on the difference in specific gravity. Commonly used gravity separation equipment includes spiral chutes, shaking tables, etc. This method is suitable for ores with finer particle sizes and more non-sulfide tungsten minerals.
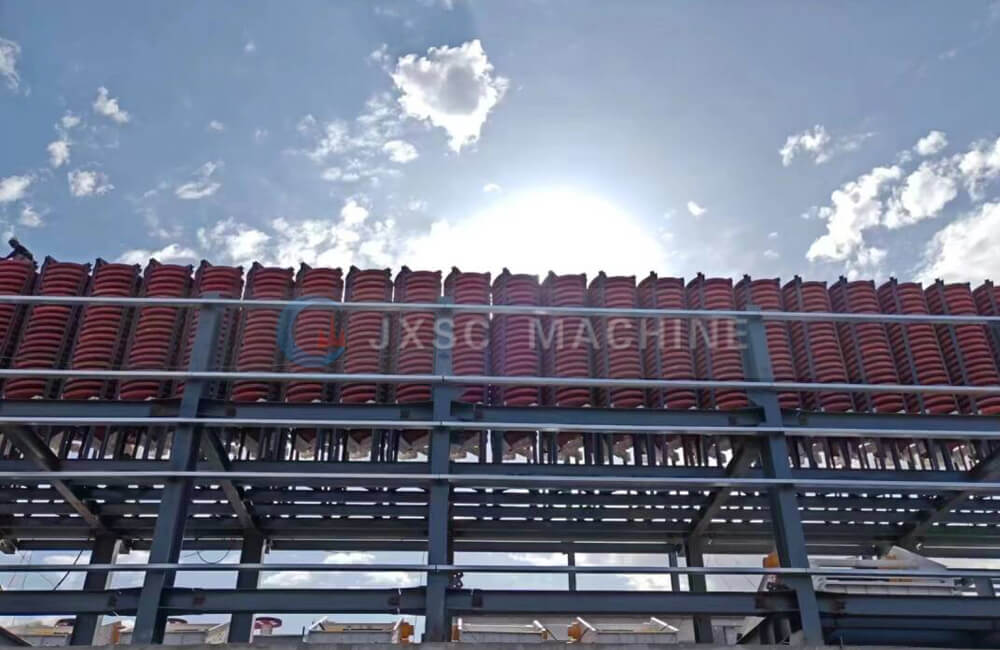
Flotation: a commonly used method for extracting tungsten ore, operates on the principle of density difference between tungsten minerals and other minerals. It using flotation agents and bubbles into flotation machines to intricately separate tungsten minerals from ores, particularly those with higher sulfide tungsten minerals.
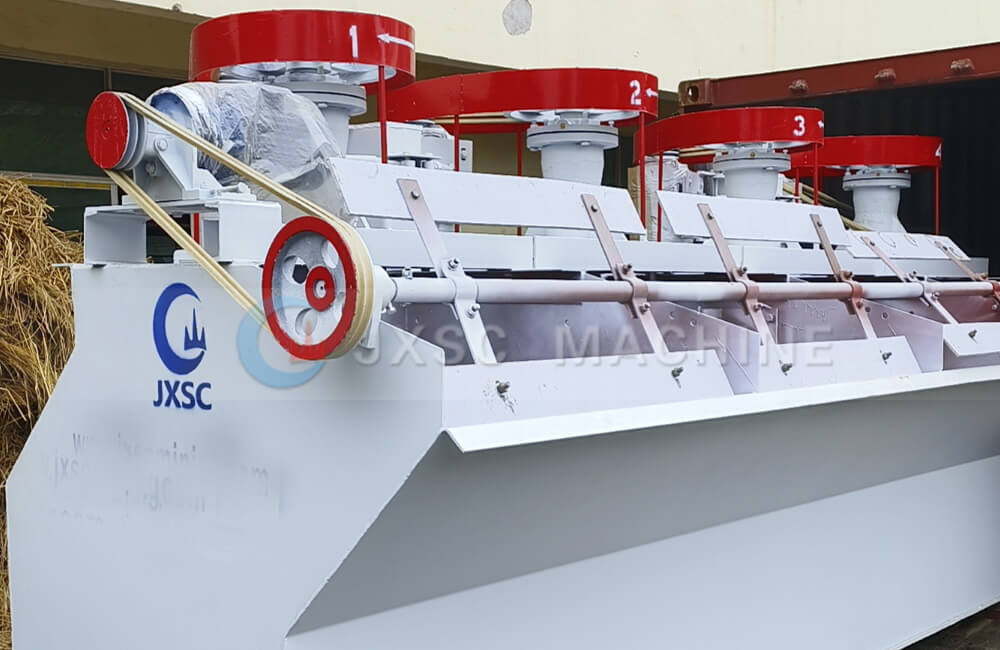
Magnetic separation: Magnetic separator is used to process ores containing magnetic tungsten minerals. Through a magnetic field, magnetic tungsten minerals are separated from ores. This method is often used for ores containing magnetic tungstenite.
These methods are mainly used in combination according to the characteristics of the ore and the requirements of the beneficiation process to obtain higher tungsten extraction rates and purity. At the same time, in practical applications, pre-treatment, ore crushing, grinding, and other steps may also be involved in optimizing the tungsten ore beneficiation solutions.
Tungsten ore beneficiation processing
Wolframite Processing
The tungsten in wolframite is mostly quartz vein type, with high dilution rate, low grade, coarse particle size, high density, low hardness, easy to dissolve mud, and dark color. The beneficiation method of wolframite is mainly gravity separation, including pre-selection, gravity separation, flotation, concentration and recovery. Among them, the flotation process is usually used to process ultra-fine black tungsten sludge
Scheelite processing
According to the symbiotic relationship between scheelite and different types of gangue ores, scheelite can be divided into different types, and the beneficiation methods of different types of scheelite are also different. For coarse-grained scheelite processing, gravity separation is generally used, which has the advantages of low cost, less environmental pollution, and high recovery rate. For fine-grained scheelite processing, flotation separation is used for separation.
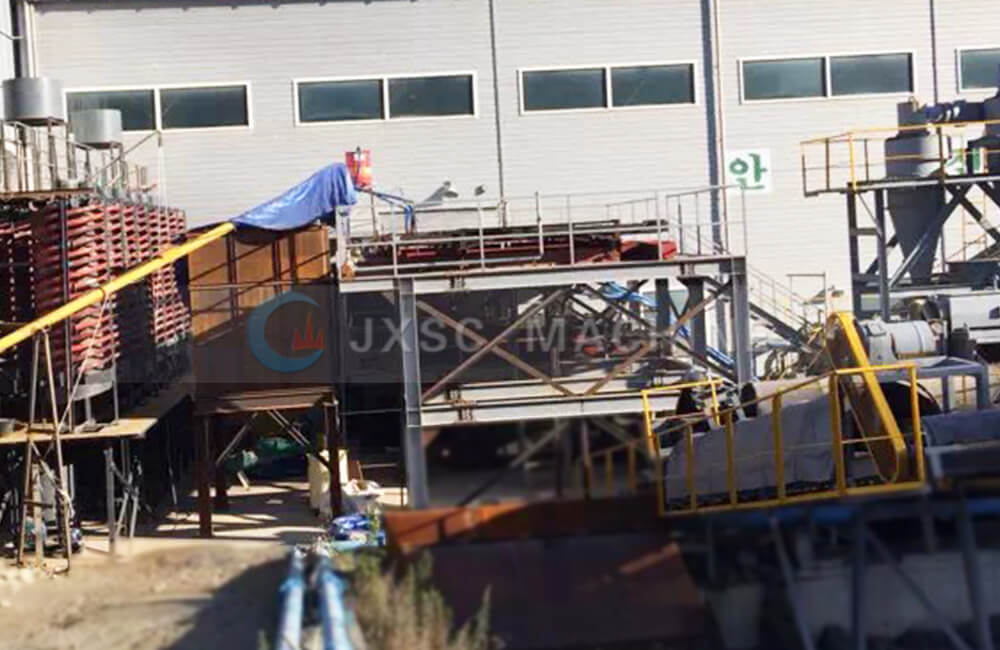
Tungsten mineral processing mainly includes gravity separation, flotation, and magnetic separation are essential in optimizing tungsten ore recovery rate. To determine the ore composition to the first factory degree of the tungsten mineral for the beneficiation of tungsten ore. JXSC provides mineral beneficiation tests and customizes the process flow according to the report and actual conditions to maximize the concentrate recovery rate and economic benefits. We support customized ore beneficiation processes and equipment; contact us for more details!