Limonite is primarily composed of hydrated iron oxide minerals and typically exhibits earthy colors ranging from yellow to brown. An indicator of its formation through the weathering process of primary iron-bearing minerals such as pyrite or hematite. Its amorphous nature means that limonite has no well-defined crystal structure and exists as a powdery substance, which can complicate extraction methods while providing fertile ground for metallurgical innovations. The properties of limonite vary depending on the geographic location and surrounding environmental conditions. For example, deposits found in tropical regions tend to be rich in manganese, which makes it uniquely commercially valuable beyond just iron ore mining. To extract valuable metals from limonite, gravity separation, magnetic separation, and flotation are the most widely used limonite ore dressing methods.
limonite ore dressing process
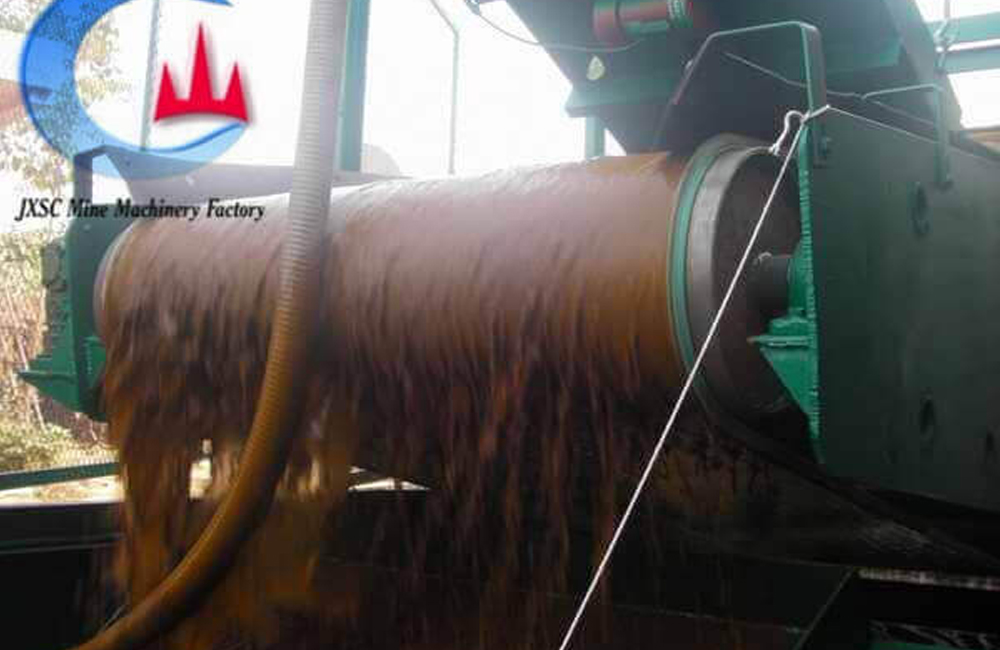
1. Limonite Gravity Separation
Gravity separation is based on the density differences between different minerals. The method relies on water and gravity to separate particles based on their weight. It can effectively separate heavy minerals from light minerals and can be used to concentrate limonite ore.
The limonite gravity separation process is a highly efficient method of separating limonite and other minerals from gangue materials. The process uses the differences in the physical and chemical properties of limonite and gangue minerals to achieve separation. By utilizing gravity, this separation process does not require the use of chemicals or complex equipment, making it cost-effective and environmentally friendly.
2. Limonite Magnetic Separation
Magnetic separation exploits the magnetic properties of certain minerals in limonite. By using magnets or magnetic fields, the technology separates iron-rich particles from the other components of the ore. Magnetic separation is very effective for removing impurities that may affect downstream processes.
An important consideration in limonite magnetic separation is optimizing operating parameters for maximum recovery and purity. Factors such as particle size, initial concentration, and pH can affect process efficiency. Understanding these variables allows conditions to be fine-tuned to achieve the desired results.
3. Limonite Flotation process
Limonite has a complex structure consisting of hydrated iron oxides. The flotation method is unique in its ability to selectively separate the desired minerals from the unwanted gangue material using surfactants, thereby improving the overall efficiency of ore processing. Flotation involves the addition of reagents to render certain minerals hydrophobic while making others hydrophilic. The froth brings the hydrophobic minerals to the surface while leaving the hydrophilic materials in the pulp phase. Flotation selectively concentrates the valuable components such as iron oxide while minimizing impurities.
The limonite flotation process separates the limonite mineral from other impurities through a series of flotation stages. The success of the process depends on a variety of factors, including pH control, reagent selection, and particle size distribution.
Limonite Ore Dressing Plant
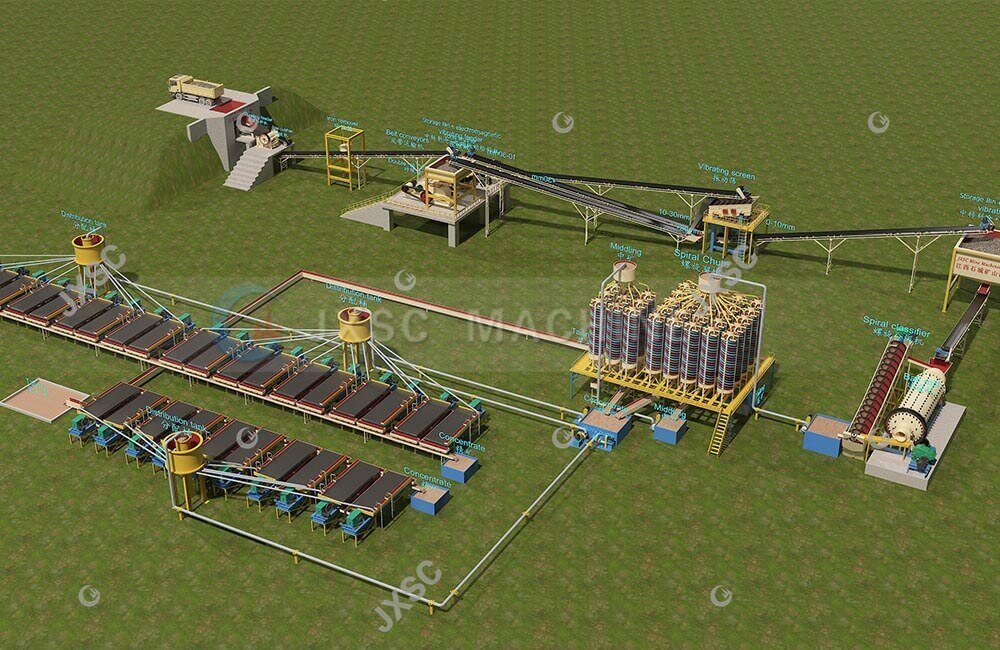
Rock Limonite Ore Dressing process plant
This setup is a rock limonite ore dressing plant, it is configured with raw material feeding, primary crushing, fine crushing, screening, ball mill grinding, and gravity separation to separate out and upgrade limonite concentrate.
- The Limonite ore raw material stone is fed to the primary jaw crusher by a vibration feeder, so can feed rock chrome ore smoothly and evenly. The vibration feeder is with the grizzly bar to grizzly oversize to a primary jaw crusher, under the grizzly bar small size material goes to the fine crusher by conveyor. So as can increase the crushing effect of the primary jaw crusher.
- The primary jaw crusher is for crushing big rock chrome ore to a smaller size, and the output material goes to the next cone crusher for fine crushing. The cone crusher crushed rock Limonite to below 30 mm is suitable to feed to the ball mill but firstly will go to a vibration screen for screening out oversize larger than 30mm and sent back to cone crusher crushing again. 5 to 30mm will go to the double roller crusher crushing again. Under screens 0 to 5mm go to the storage bin before the ball mill.
- The 0 to 5mm powder material will be sent to the ball mill smoothly by an electromagnetic vibration feeder and belt conveyor. The ball mill is for grinding 0 to 5 mm to small powder, it works together with the spiral classifier, so the overflow slurry from the classifier is about 80% 200 mesh powder, the oversize particle from the classifier will go back to the ball mill grinding again, to form a closed-loop.
- The 200 mesh slurry will be pumped to spiral chutes, and shaking tables. The spiral chute is for primary concentration. In order to increase the concentrate recovery ratio to the maximum, we use a 2-stage spiral chute separation. The middling material from the 1st stage spiral chute group will be pumped to the 2nd stage spiral group, so as to recover as much Limonite as possible.
- All the heavy concentrate ore that is discharged from the two stages spiral group will go to the shaking table to concentrate again, to get higher-grade Limonite to concentrate.
The main purpose of limonite ore dressing is to effectively extract iron. Technologies such as magnetic separation, flotation and gravity concentration can improve ore grade and recovery rate. Choose the appropriate method based on the characteristics of the ore and the desired final product. JXSC supports customized ore dressing processes and equipment, contact us for more details!