The flotation process is widely used in the mining industry to separate valuable minerals from ore, and the process relies on using specific types of ore. Usually used to concentrate various sulfide minerals, phosphates, and oxide minerals also need to be concentrated by flotation machines. For example, gold ore, silver ore, copper ore, lead-zinc ore, tin ore, molybdenum ore, nickel ore, antimony ore, chalcopyrite, sphalerite, galena and pyrite, fluorite ore, etc. Below, we list some common ores that need to be concentrated through the flotation process.
What is Flotation Process
Flotation refers to separating mineral particles by utilizing the differences in physical and chemical properties of mineral surfaces. It is the most widely used method in mineral processing applications. However, the flotation machine is the most critical equipment. It mainly involves using chemicals to create foam on the surface of the slurry, thereby selectively separating valuable minerals from the gangue material. By controlling factors like pH and particle size, flotation machines can effectively concentrate these ores for further processing. Flotation is mainly used to concentrate non-ferrous metal minerals and rough and select ferrous metals and non-metals.
working principle
After the ore undergoes wet grinding, the minerals that have been basically dissociated into monomers are adjusted into a slurry of a specific concentration, and an appropriate amount of chemicals is added. The agent’s function is to chemically react with the ore and change its hydrophilicity, making it easier for helpful mineral particles to be adhered to by air bubbles after thoroughly blending with flotation reagents in the stirring tank. The valuable mineral particles float together with the ore bubbles, while the waste rock particles sink to the bottom of the slurry, achieving flotation separation of valuable minerals. (Because minerals have a high affinity with water and are easily wetted by water, they are challenging to adhere to air bubbles and float. Minerals with a low affinity to water and are not easily wetted by water tend to float.)
The flotation foam forms a scum layer on the upper part of the flotation machine tank. The valuable mineral particles are concentrated on the scum layer and collected through the concentrator, while the waste rock is discharged through the waste slag port. This completes the flotation separation process.
Common ores by flotation process
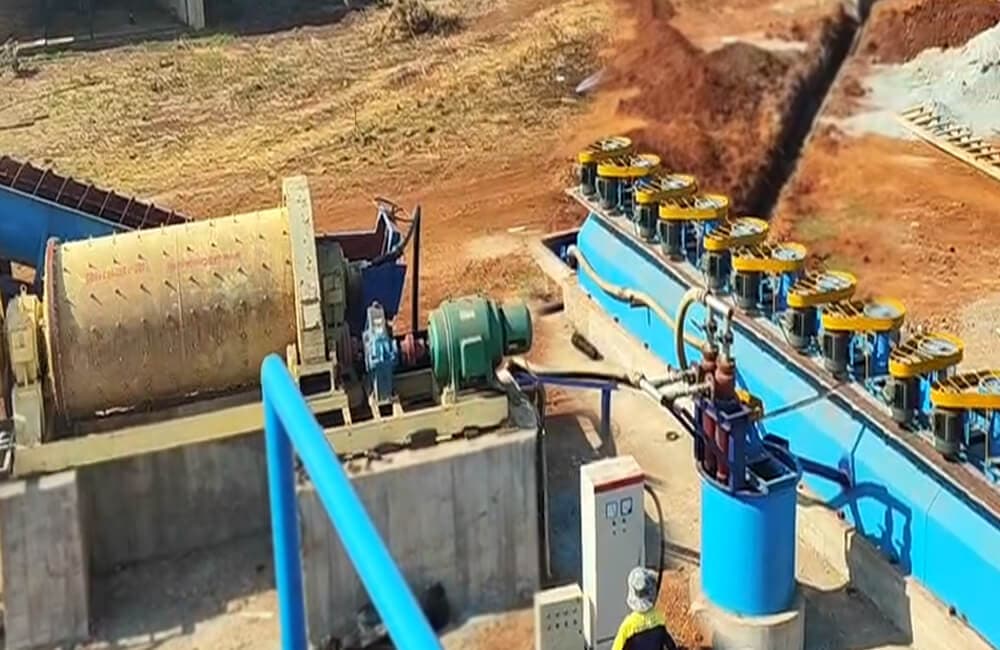
Gold Ore flotation
Flotation is a key process in extracting gold from certain types of ore. It is very suitable for processing gold-containing sulfide ores with fine gold particles and good floatability. These deposits contain gold that is difficult to extract through traditional methods because it is associated with other minerals such as pyrite or arsenopyrite. However, flotation can separate these minerals from the gold, making them easier to extract and process.
Gold deposits in sedimentary rocks also often require flotation to be effectively extracted. These deposits are formed by the accumulation of mineral-rich sediments over time, resulting in complex ore compositions that require separation processes such as flotation. By using froth flotation technology to selectively separate valuable components from ore, miners can increase overall recovery rates and maximize production of precious metals such as gold.
The presence of organic carbon and other impurities can sometimes affect the flotation process, resulting in lower recovery rates. In some cases, pretreatment methods such as roasting or biological oxidation are required to improve the floatability of gold ore. For “refractory gold ores” that cannot be directly treated by mercury amalgamation or cyanide, a combined process including flotation is also required. The use of flotation machines in gold mining ensures high recovery rates and allows the processing of low-grade ore, which is more economical.
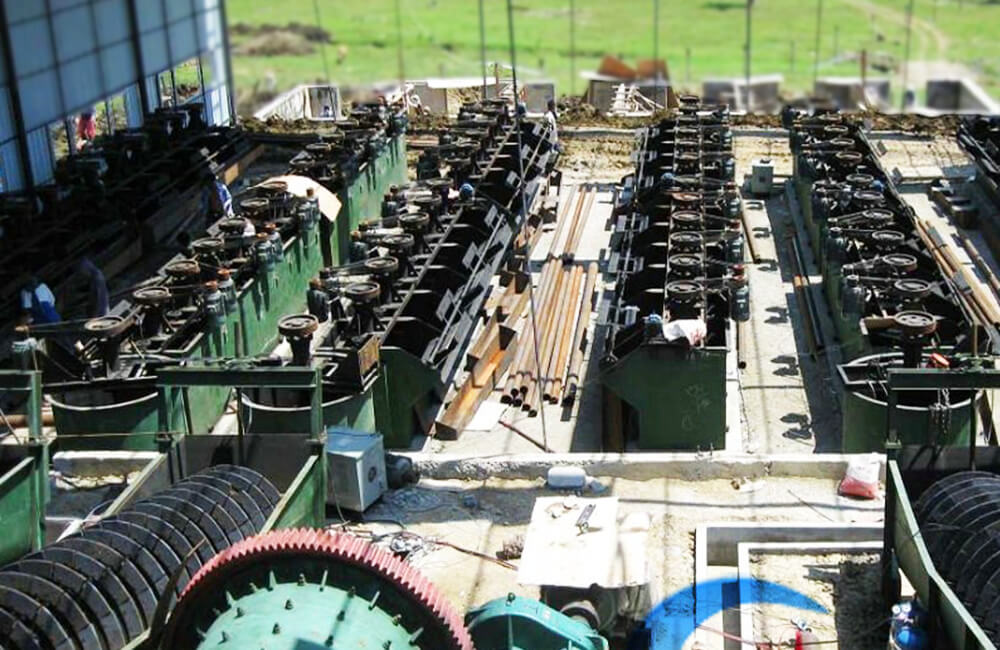
Copper- lead-zinc ore flotation
Often contain complex mineral compositions that require separation processes to effectively extract valuable metals. These ores typically contain a mixture of sulfide minerals such as chalcopyrite, galena and sphalerite, each requiring a different flotation strategy for optimal recovery. These ores may have valuable minerals finely distributed in the gangue matrix and require finer grinding to release them for efficient recovery by flotation.
Compared with other mineral processing methods, using flotation in copper, lead-zinc ore processing can achieve higher yields and concentrate grades.

iron-containing mineral flotation
Iron ore often has a complex mineral composition containing various impurities, making its separation challenging. For example, hematite ore typically contains silica and alumina as gangue minerals. Additionally, the presence of phosphorus in iron ore can make it difficult to obtain high-grade concentrates, as phosphorus is a harmful element that reduces the quality of the final product. Oxide ores like iron ore typically undergo a flotation process to separate the desired iron minerals from silica and other gangue materials.
In addition, the particle size distribution of iron ore has a key influence on its flotation behavior. Fine particles tend to be more difficult to recover by flotation because of their lower settling rate and increased surface area, which can result in higher reagent consumption and lower recoveries. Therefore, it is necessary to strictly control the grinding fineness during ore processing to ensure the smooth progress of the flotation process.
In addition to some of the minerals listed above, there are many ferrous metals and non-metallic minerals that often use combined processes including flotation. For example: molybdenum, nickel, manganese ore, lithium ore, feldspar ore, graphite ore, rutile and other mineral processing line.
The use of flotation machine technology provides a cost-effective and sustainable solution for mineral processing operations in different industries. Especially the beneficiation of ores containing valuable minerals such as gold, copper, lead and zinc. Our flotation machines due to their efficiency and versatility, ores with complex mineralogy or fine particle sizes are often best suited for flotation concentration. JXSC supports customized flotation machines and mineral flotation solutions, contact us online for details!