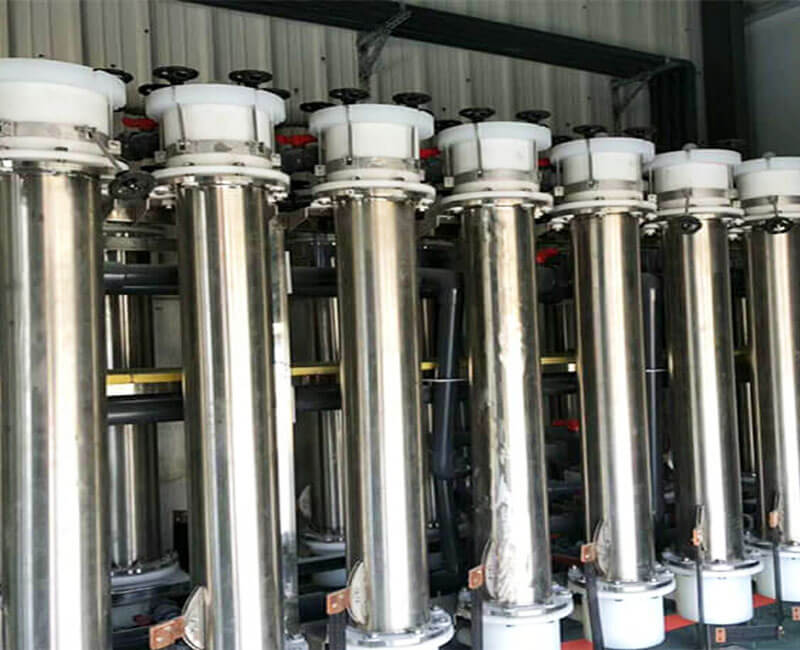
Swirl electrolytic copper recovery system
Swirl (cyclone) electrolytic copper recovery system is mainly used for copper metal refining. It is especially suitable for the metallurgical industry for selective electrolytic (electrowinning) separation and purification of low-content and complex solutions, as well as refining heavy metal ions from wastewater.
Swirl electrolytic copper recovery system
Swirl electrolytic copper recovery system is also called cyclone electrolytic copper recovery equipment. Cyclone electrolytic technology is a wet refining and purifying metal method. It mainly includes electrolyzer, solution distribution system, electric power and control system, and engineering supporting system. It is a new technology capable of selective electrolysis (electrowinning) of valuable metals and is widely used in copper smelters for metal extraction and recovery.
The copper electrolytic system can recover valuable metal elements directly from the leach solution of metal minerals in a simple way. Through the high-speed cyclone of the liquid, the solubility polarization in the electrolysis process is eliminated, avoiding the influence of many factors in the traditional electrolysis process, which preferentially precipitates metals with closer potentials, resulting in higher efficiency at low concentrations and high current densities. The cyclone electrolysis copper recovery system increases the uniformity of copper wastewater flow by swirling, which makes it possible to solve the problems of inconvenient electrolysis of copper wastewater and inconvenient collection of copper slag.
Process & Structure Of Swirl electrolytic copper recovery system
The two-time direct electrolysis method is adopted. The hydrogen peroxide in the waste liquid is firstly broken by electrolysis, and then enters the electrolytic cell or cyclone electrolytic tank. After the copper is electrolyzed, a small amount of reagent is added to effectively recover and recycle the micro-etching liquid.
Structure of cyclone electrolytic copper recovery equipment
Including a bottom cylinder, an electrolytic cylinder is provided at the top of the bottom cylinder, a cyclone assembly is provided in the bottom cylinder, a cover plate is provided at the top port of the electrolytic cylinder, an electrolytic mechanism is provided in the electrolytic cylinder, and a sliding assembly is provided on the cover plate.
- Cathode reaction: metal ions obtain electrons at the cathode to form metal.
- Swirl (cyclone) electrolysis: through high flow rate and high solution concentration difference, metal is efficiently refined.
- Swirl (cyclone) electrolysis device: including a hollow cylindrical main body, the main body has an inlet and an outlet for the micro-etching liquid to enter, a cathode and an anode are provided in the cylinder of the main body, and the cathode and the anode are both connected to the external electrode.
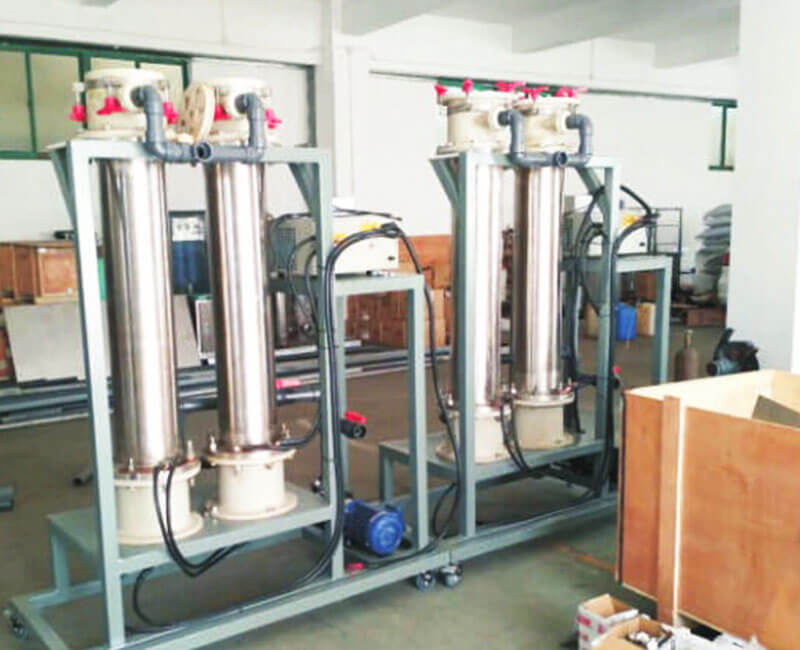
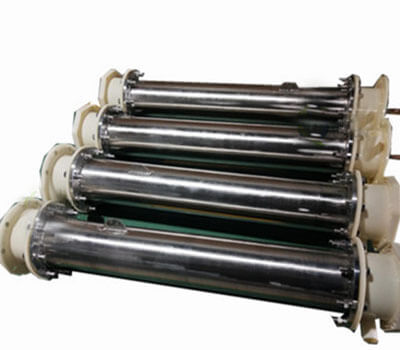
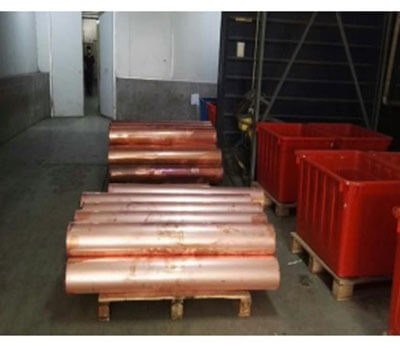
Working principle
The working principle is mainly based on electrochemical theory, relying on each metal ion’s difference in theoretical precipitation potential. That is, as long as the metal to be extracted has a large potential difference from other metal ions in the solution system, the metal with a more positive potential is easily precipitated preferentially at the cathode.
Its electrolysis process technology involves placing the anode and cathode in a plate-type tank. Under the action of the electric field, the anions move toward the anode, and the cations move toward the cathode. The plate electrolytic cell has a slow flow rate, and the solution concentration difference does not change much. The obtained metal cations are electronically deposited and precipitated by supplementing the solution concentration at the cathode, thereby obtaining electrolysis products.
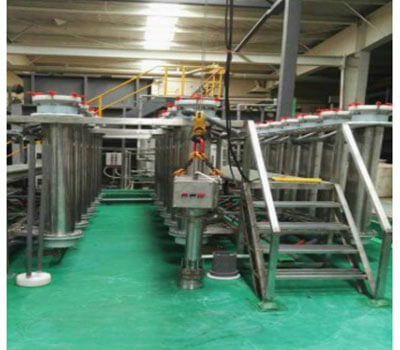
process features
1. This system can avoid the limitations of the traditional electrolysis process affected by various factors (ion concentration, precipitation potential, concentration polarization, overpotential, pH value, etc.);
2. The metal recovery rate can reach the ppm level with efficient and high-purity electrolytic extraction of low-concentration solutions. Cathode copper can reach 99.99%;
3. The solution is circulated in a closed loop, effectively preventing the electrolytic waste gas from precipitating and polluting the environment;
4. This entire electrolysis process is carried out in a closed space, no harmful gas is discharged, and the operating environment is good;
5. Higher production efficiency than traditional electrolysis technology, enriching valuable metals in a larger range;
6. This system has unparalleled technical advantages in copper-nickel or copper-silver separation, improving the appearance of recycled copper products;
7. Modular and portable assembly equipment, relatively simple operation;
8. Infrastructure investment and small footprint, easy installation or maintenance.
Technical Parameters
Model | Wastewater treatment capacity(Ton/ month) | Electricity load | Copper production capacity(Ton/ month) | Occupied area |
YZ-XLDJ50 | 50T | 20-30KW | 1.0T | 30-40M2 |
YZ-XLDJ100 | 100T | 40-50KW | 2.0T | 50-60M2 |
YZ-XLDJ200 | 200T | 70-80KW | 4.0T | 80-100M2 |
Contact Us Now
Ask us about mineral processing configuration and equipment quote! (No job, No investment)
Notice:
- We only provide mineral processing equipment and solutions; not buy and sell minerals/ ores/ materials.
- We do not recruit, don’t offer jobs, and are not interested in investments or partnerships.
- We value your privacy and keep your information safe.