Flotation separation is an important process in the mining industry to separate valuable minerals from waste. The process involves adding chemicals to the crushed pulp, which causes certain minerals to float to the top of the mix and be collected. However, this process often faces obstacles and challenges that hinder its efficiency and effectiveness. In it, we will discuss the top 8 common problems encountered in the flotation process and their solutions. So, whether you are an experienced miner or just entering the industry, you can optimize your flotation operation to extract minerals more efficiently.
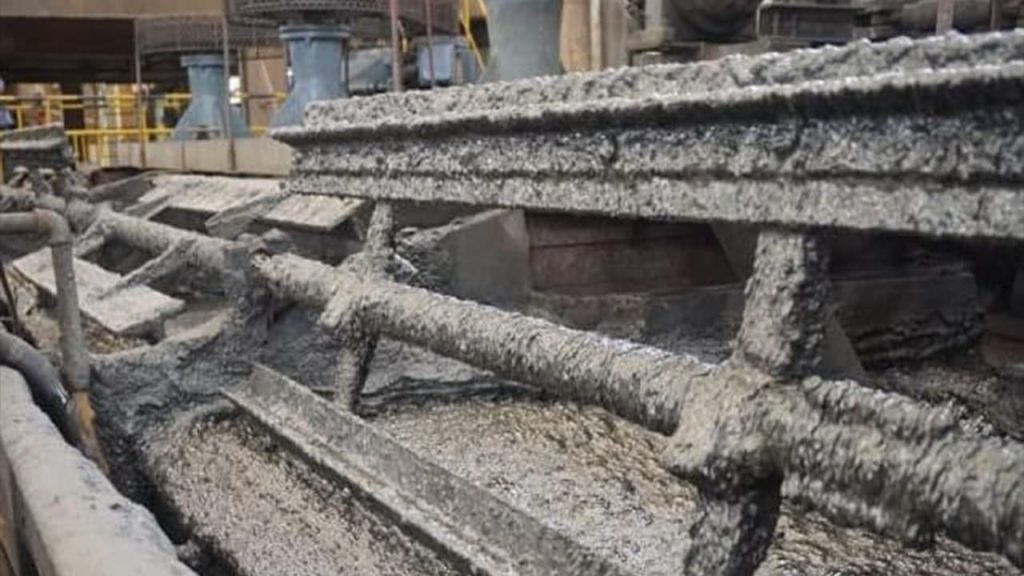
1. What is the effect of grinding particle size on flotation?
During flotation, too coarse ore particles (greater than 0.1mm) and very fine ore particles (less than 0.006mm) do not float well, and the recovery rate is low.
In the flotation of coarse particles, due to the larger weight, the shedding force of the ore particles increases. Then you need:
(1) Use a sufficient amount of the most effective collector;
(2) Increase the aeration of the pulp, cause larger bubbles, and increase the amount of microbubbles precipitated in the water;
(3) The stirring intensity of the pulp should be appropriate;
(4) Properly increase the pulp concentration;
(5) The scraper should be quick and steady when scraping the bubbles.
In the flotation of very fine particles (usually refers to the slime less than 5 ~ 10μm):
- Due to the small quality of the slime, it is easy to adhere to the surface of the coarse particles, which reduces the floatability of the coarse particles and deteriorates the selectivity;
- Due to the large specific surface of the sludge, they will absorb a large number of flotation reagents in the pulp, which reduces the concentration of the reagent in the pulp, destroys the normal flotation process and reduces the flotation index;
- Because the slime is very fine and has a large surface area, the surface activity is increased, it is easy to act with various chemicals, it is not easy to be sorted and it has strong hydration. Hence, the foam is too stable, and it will cause trapping during selection. Accuracy reduces concentrate quality and the fluidity and concentration efficiency of foam products.
2. How to prevent and reduce excessive sludge in refining?
Common methods to prevent and reduce sludge are:
(1) Multi-stage grinding and classification processes can be used. It is necessary to correctly select the grinding and classifying equipment to improve the efficiency of the classifier;
(2) Add medicaments to eliminate the harmful effects of ore slime: water glass, soda ash, caustic soda, etc., are commonly used; to reduce the flocculation and covering effect of ore slime.
(3) Desliming is carried out on the grinding ore before flotation and discarded as tailings. If the content of valuable components in the slime is high, the detached mud can also be treated by flotation or sent to water for smelting.
Common desliming methods by spiral classifier and hydrocyclone. In special cases, a small amount of foaming agent can be added before flotation to remove easily floatable sludge by flotation.
3. What should I do if the coarse particles are not easy to float?
There is a tendency to reduce the coarse grinding fineness to ensure the recovery rate of the coarse grinding in the flotation plant that deals with embedded heterogeneous ores. Because coarse particles are relatively heavy, they are not easy to suspend in the flotation machine, reducing the chance of colliding with air bubbles. In addition, after the coarse particles are attached to the air pockets, they are easily removed from the air pockets due to their high separation force. Therefore, the flotation effect of coarse particles could be better under general process conditions. To improve the rough flotation effect, the following technological measures can be taken:
(1) Use a collector with strong collecting power, or add auxiliary collectors such as kerosene and diesel oil.
(2) Under the premise of ensuring the stability of the foam layer, proper stirring is required. It promotes the suspension of coarse particles and increases the chance of air bubble attachment.
(3) Appropriately increase the air volume of the flotation machine to make the bubbles bigger and form the “buoyancy” created by large and small bubbles.
(4) Shallow trough flotation machines shorten the floating distance of mineralized bubbles and reduce the falling of ore particles from the bubbles.
(5) A fast and stable foam scraping device is used to scrape off the floating mineralized foam in time to reduce the re-falling off of mineral particles.
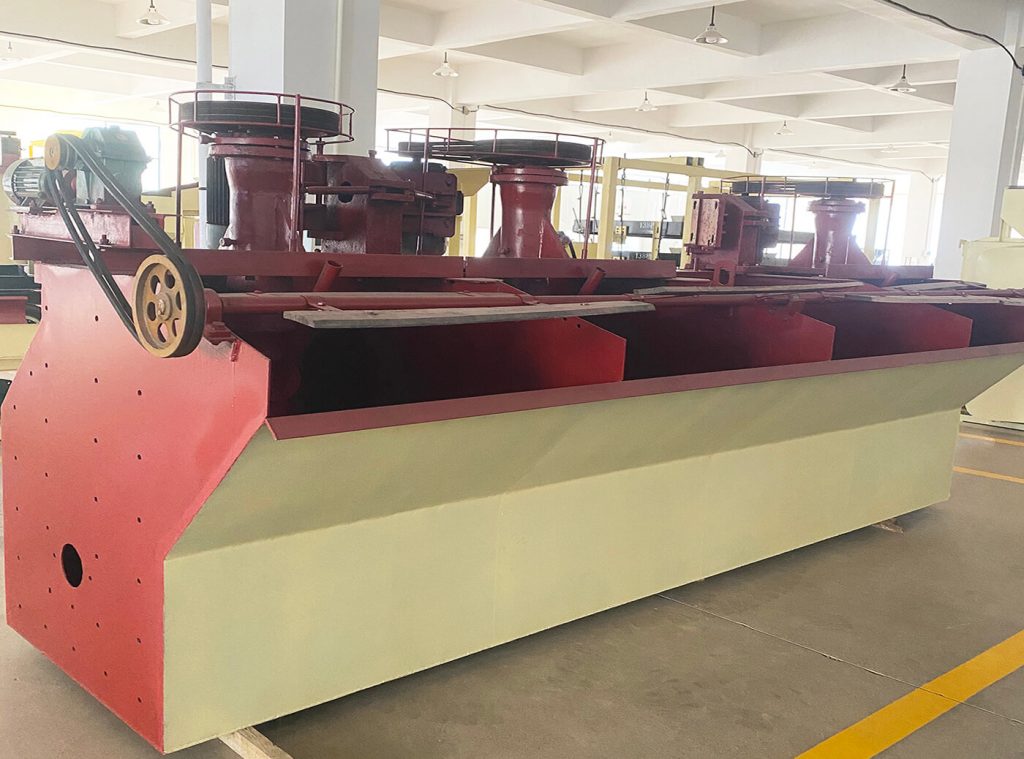
4. What are the reasons and measures for the difficulty of fine particle flotation?
Flotation separation of fine-grained materials is difficult for the following reasons:
(1) The specific surface area of fine particles is large, and the surface energy is significantly improved.
(2) Fine particles are small in size and less likely to collide with air bubbles.
The technical measures to solve fine particle flotation are as follows:
(1) Selectively flocculate target mineral particles or gangue fine mud with flocculants and then separate by flotation;
(2) With the ore particles of general flotation size as the carrier, the fine particles of the target minerals are covered on the carrier and floated. The carrier may use the same mineral or different minerals. For example, fine-grained gold can be floated using pyrite as a carrier. Calcite is used as the carrier to float out fine iron and titanium impurities in kaolin.
5. How does sludge impact flotation and how can it be solved?
If the flotation pulp contains more sludge, it will bring a series of adverse effects to the flotation.
The main impacts are as follows:
- It is easy to mix into foam products and reduce the grade of concentrate;
- It is easy to cover the surface of coarse grains and affect the flotation of coarse grains;
- Adsorb a large number of drugs, increasing drug consumption;
- Make the pulp sticky and make the aeration condition worse.
The technical measures to solve this problem are:
- The use of thinner pulp can reduce the viscosity of pulp, thereby reducing the inclusion of mineral mud in foam products;
- Add dispersant to disperse the mucus and eliminate the harmful effect of mucus covering the surface of other minerals;
- Dosing in sections to reduce the consumption of sludge for chemicals;
- Desliming of flotation materials before flotation. The commonly used desliming method is cyclone classification desliming.
6.What is the main effect of air on flotation?
In addition to oxygen, nitrogen and inert gases, there are carbon dioxide gas and water vapor in the air.
Air has a certain effect on the buoyancy of minerals:
(1) After the mineral is crushed, the new surface is exposed, and it will be hydrated when it meets water, showing hydrophilicity. However, when the gas is adsorbed to the mineral surface, hydration is weakened, resulting in an initially hydrophobic surface;
(2) The use of gas and mineral surfaces is selective. Among them, oxygen has a greater influence on the mineral surface;
(3) The role of oxygen is beneficial to the hydrophobicity of sulfide ore. But if left on for too long, the mineral surface becomes hydrophilic. When the gas adsorption conditions are suitable, the surface of the mineral is hydrophobic, and it can be floated even without adding a flotation agent (such as dry coal powder).
7. What is the function of slurry stirring?
The stirring of the slurry can promote the suspension and uniform dispersion of the ore particles in the tank.
- It can promote good dispersion of air and make it evenly distributed in the tank.
- It can promote the enhanced dissolution of air in the high-pressure area of the tank and the enhanced precipitation in the low-pressure area to generate a large number of active microbubbles.
- Strengthening aeration and agitation is beneficial to flotation, but it should not be excessive, because excessive aeration and agitation will cause the following disadvantages:
(1) Facilitated the consolidation of bubbles;
(2) The quality of the concentrate is reduced;
(3) Increased power consumption;
(4) Increase the wear and tear of each part of the flotation machine;
(5) The volume of the slurry in the tank decreases (this is due to the increase in the volume of the tank occupied by the air bubbles);
(6) Excessive stirring may also cause the mineral particles attached to the air bubbles to fall off.
The optimal amount of aeration and stirring in production should be determined through experiments according to the type and structural characteristics of the flotation machine.
8. What is the relationship between the flotation conditions and the properties of the pulp concentration?
Determining the most suitable pulp concentration during flotation is related to ore properties and flotation conditions. The general rules are:
(1) Concentrated pulp is used for the flotation of minerals with high density, while the dilute pulp is the opposite;
(2) Coarse pulp is used for flotation of coarse-grained materials, and finer pulp is used for flotation of fine-grained and muddy materials;
(3) Using thicker pulp for roughing and sweeping can reduce the consumption of chemicals and the number of flotation machines. And using finer pulp for beneficiation can obtain higher quality concentrate.
The flotation process is a key technology in the mining industry, but it is not without its challenges. The top 8 common problems and solutions discussed above can help operators improve processes, reduce costs and increase efficiency. By implementing these solutions and continuously monitoring the performance of your flotation circuits, you can optimize recovery and maximize profitability. So it’s time to start implementing these JXSC flotation solutions and take your plant to new heights!