Gold mining is a lucrative industry that has flourished for centuries but also leaves behind a huge amount of waste known as tailings. Its gold tailings are a by-product of the mining process and consist of finely divided rock and mineral residues. These tailings often present significant environmental and safety risks if not managed properly due to their high water content and the potential for toxic pollutants to leach into nearby ecosystems. To mitigate these hazards, it is critical to have effective dewatering equipment that can effectively remove excess water from tailings before disposal or recycling.
Due to environmental protection and other reasons, most gold mine tailings require dehydration and dry discharge. On the one hand, it is to reduce the pressure of the tailings pond and reduce the safety hazard of the tailings pond, and on the other hand, it is to control the pollution of the tailings to the environment. Common gold tailings dewatering equipment includes hydrocyclone, thickener, dewatering screen and filter press. With our in-depth analysis, mining operators can decide which dewatering equipment best suits their specific needs, while minimizing environmental impact and maximizing operational efficiency.
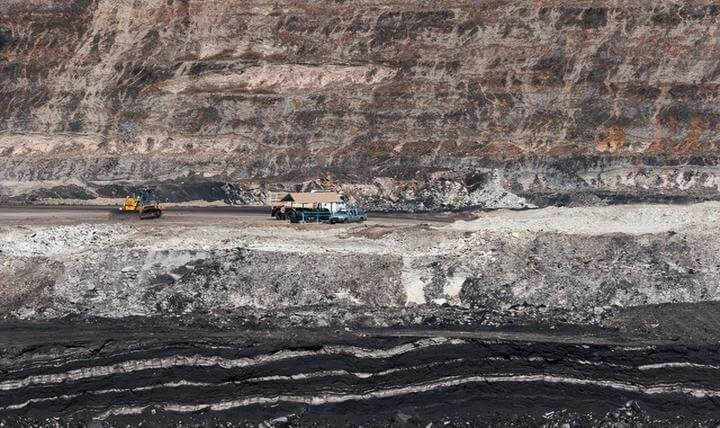
Gold Tailings Dewatering Equipment
1. Hydrocyclone
Hydrocyclones are generally used for pre-concentration of tailings, which greatly reduces the water content of gold tailings, improves the dehydration efficiency of subsequent operations, and eases the operating burden of concentration and filtration equipment. It has the advantages of high efficiency, a simple process and a small footprint.
Work Principle
It usually consists of a cylindrical container, an inlet pipe, a swirl chamber, a discharge port, etc. When working, the mixture enters the cyclone chamber through the inlet pipe. The inlet pipe is designed so that the fluid enters the swirl chamber in a helical shape, forming a vortex in the swirl chamber. After the vortex is formed, the solid particles are pushed to the outer wall of the cyclone chamber, forming a solid deposition layer due to the centrifugal force. The liquid forms a vortex cavity in the center of the vortex and is discharged from the discharge port. Due to the action of centrifugal force, solid particles are forced to deposit on the outer wall of the cyclone chamber, forming a solid deposition layer. The thicker the solid deposition layer, the better the solid-liquid separation effect. The solid deposition layer must be dehydrated when it reaches a certain thickness. Dehydration is carried out through a discharge port at the bottom of the cyclone chamber. After the liquid flows out of the vortex cavity, it is discharged through the discharge port, while the solid particles remain on the outer wall of the vortex chamber.
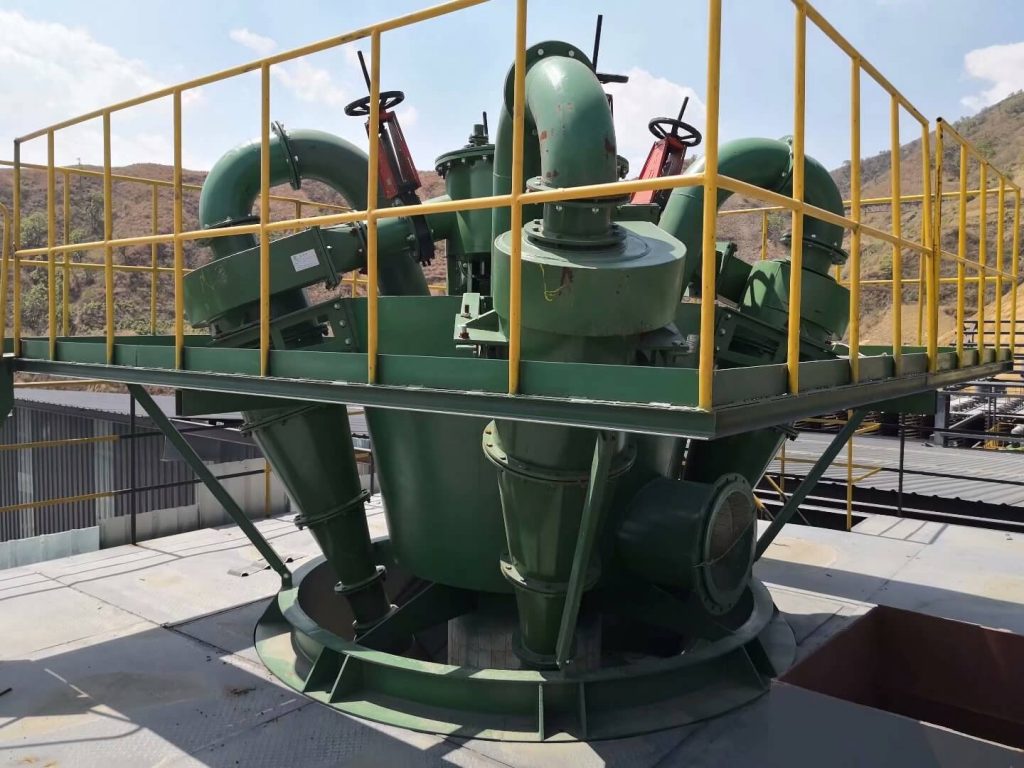
The dehydration effect can be adjusted by controlling the opening degree of the outlet and the pressure in the cyclone chamber. The hydrocyclone has a better separation effect on fine particles dewatering, but it may not be effective for larger particles, and it needs to be combined with other equipment for processing.
2. Cone Thickener
The cone thickener is commonly used for gold mine tailings dehydration. The deep cone design greatly increases the area of the thickening zone and improves the underflow concentration. It mainly uses gravity to separate solid particles from liquid to achieve dehydration effect. Larger solid particles settle to the bottom of the deep cone thickener, while lighter liquid is discharged.
Work Principle:
The feed mixture, the suspension containing solid particles and liquid, is injected into the center of the deep cone thickener through the feed pipe, then forms a mixing pool at the bottom of the deep cone thickener. The solid particles and the liquid are mixed in the mixing tank, and the settling process begins. Due to the density of solid particles, they will gradually settle to the bottom of the mixing tank—a liquid outlet at the bottom discharges the settled cleaning liquid. The cleaning liquid flows through the discharge port, leaving the drier solid particles in the deep cone thickener. A stable layer is formed at the bottom of the deep cone thickener, and these solid particles can be collected and discharged through the collector or discharger at the bottom.
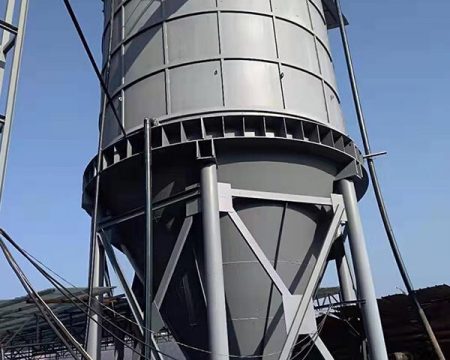
By controlling the feeding speed, stirring intensity and the concentration of the mixture, the dehydration effect of the deep cone thickener can be adjusted. Even when the concentration of tailings is low and the particle size is fine, it can achieve good concentration effect, and it has a small footprint, large processing capacity and low infrastructure costs.
3. Dewatering Screen
High-efficiency high-frequency dewatering screen and special screen design make it difficult for the materials in the pulp to pass through the screen holes, and the loss of useful materials is small.
Working Principle
It mainly comprises a vibrating motor, screen frame, screen mesh and base. The vibration motor generates high-frequency vibration force through the exciter to vibrate the screen frame. The material enters the screen frame through the feed port, and the influence of high-frequency vibration will accelerate its moisture. Due to the small adhesion force between water molecules, they are easily separated under vibration. During the working process of the high-frequency dehydration screen, the solid material will be vibrated onto the screen, and the water will be discharged through the screen holes, thereby realizing solid-liquid separation. Larger solid particles will stay on the screen, forming a dewatered layer of solid material. As the vibration proceeds, the dewatered layer will continue to thicken until the desired solid moisture content is reached.
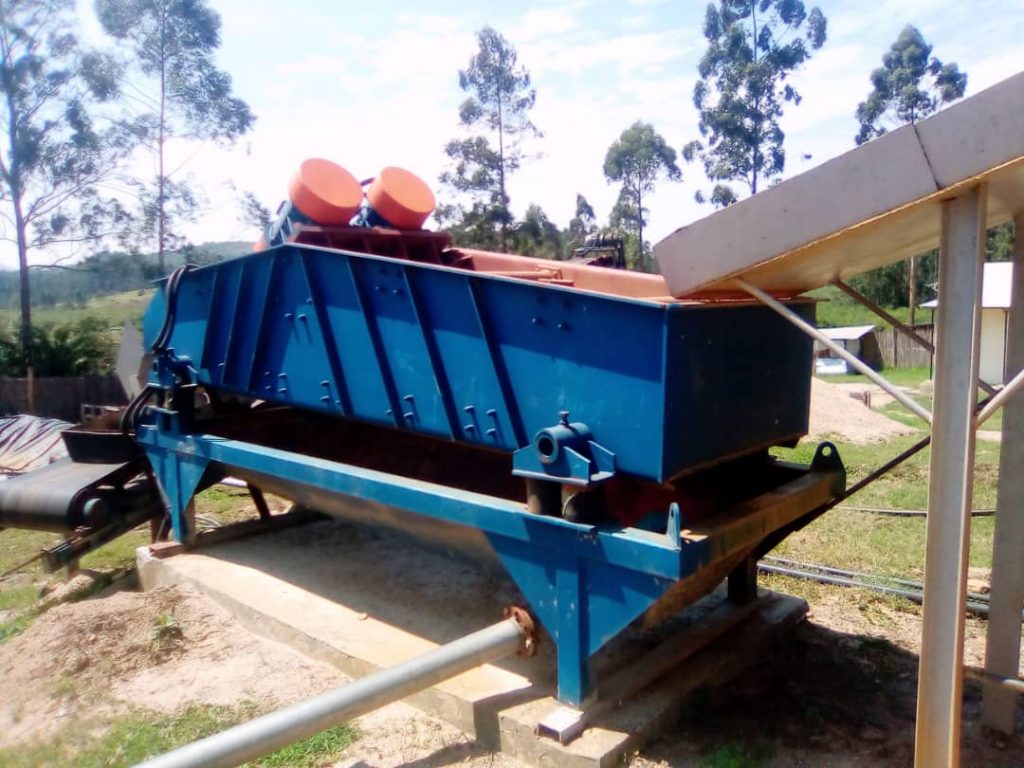
The high-frequency dehydration screen separates the moisture in the solid material through high-frequency vibration and the screen and realizes an efficient dehydration process. Moreover, the structure is simple, the operation is convenient, the processing capacity is large, and it is durable. The moisture content of the tailings can finally reach about 15%.
4. Filter press
The commonly used filter press types for gold tailings dewatering include belt and box filters. The belt filter press uses heavy action to remove free water, then removes the remaining water by strongly pressing the pair of rollers. The processing time is longer, and the final water content of the filter cake can be controlled at about 20%. The box filter press uses high pressure to dehydrate and has a strong dehydration ability. The final water content of the filter cake can reach less than 8%, and it is easy to operate and low in energy consumption.
Working Principle
The dehydration principle of the filter press is mainly based on the action of filtration and compression. It usually consists of a filter plate, filter cloth, filter juice tank, pressing device and drainage system. The filter press gradually removes the moisture in the solid material by applying pressure, while the filter cloth separates solid and liquid. With the continuous application of pressure by the compacting device and filtrate discharge, solid materials’ moisture content will gradually decrease to achieve the desired dehydration effect.
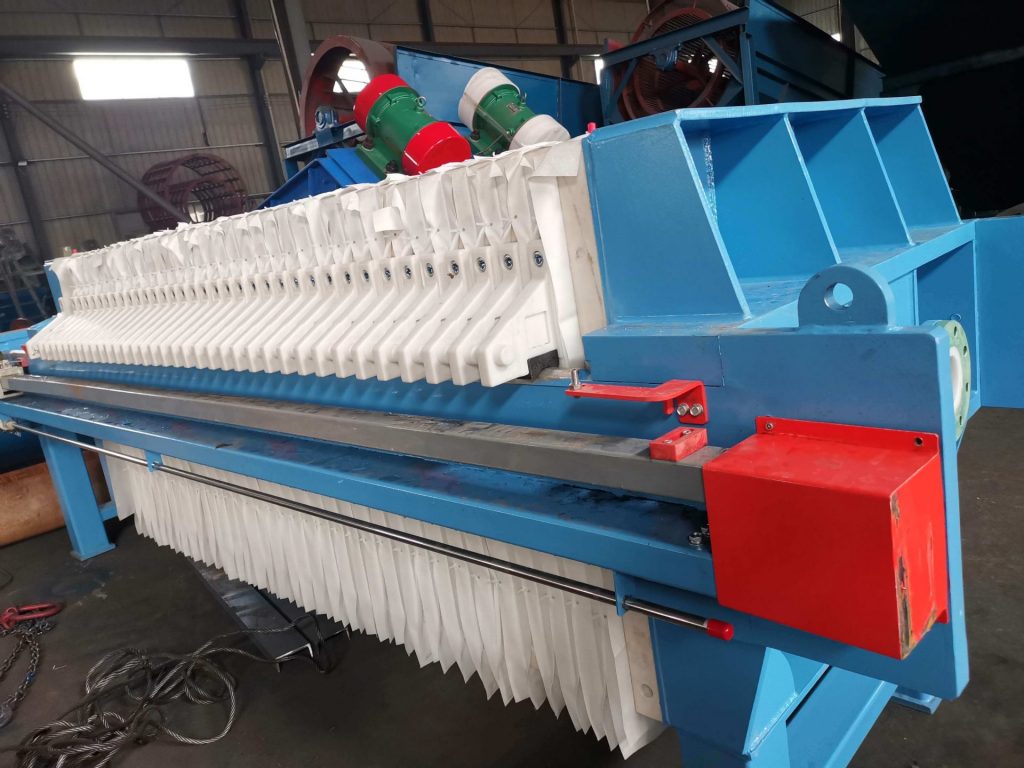
Filter presses are often used in various industries, such as chemical industry, food processing, environmental protection and other fields, and can efficiently carry out large-scale solid-liquid separation operations.
The above four gold tailings dewatering equipment can help mining companies effectively manage waste and protect the environment while maximizing profits. Whether you are a small miner or an established mining company, these options provide innovative ways to dewater gold tailings and convert them into valuable resources, ensuring sustainable operations in the gold mining industry. Gold tailings dewatering equipment is often combined to achieve better dehydration results. In actual production, selecting the appropriate equipment according to the ore properties, beneficiation conditions and other factors is necessary. Contact us online get the factory prices!