Limonite, a common iron oxide mineral, has long been known for its challenging processing characteristics due to its complex composition and difficulty in processing. Its high moisture content, fine particle size distribution and low iron grade make it a difficult material to process and beneficiate effectively. However, recent advances in beneficiation methods have shown promising results in overcoming these difficulties and unlocking the potential of limonite as an important iron source. We will delve into limonite beneficiation methods to maximize iron recovery from limonite while minimizing energy consumption and environmental impact. The JXSC beneficiation method will provide a more efficient and environmentally friendly solution for extracting valuable iron from limonite deposits.
Limonite Processing Difficult
Limonite is a common iron ore mineral that forms due to the weathering and oxidation of iron-rich rocks and minerals. It is commonly found in areas with high rainfall and acidic soils. The composition of this brownish-yellow mineral varies but usually contains hydrated iron oxide and varying amounts of goethite and hematite. Limonite is an important source of iron ore, but its processing faces some challenges. One of the main challenges in processing limonite is its complex mineralogy. Limonite usually occurs as a mixture or association with other minerals such as quartz, clay minerals, and manganese oxides. This makes it challenging to separate limonite from these impurities during beneficiation. In addition, the presence of different hydrated iron oxide phases in limonite can affect its magnetic properties, further complicating its separation. However, our limonite beneficiation methods mainly include gravity separation, magnetic separation, flotation and combined separation process.
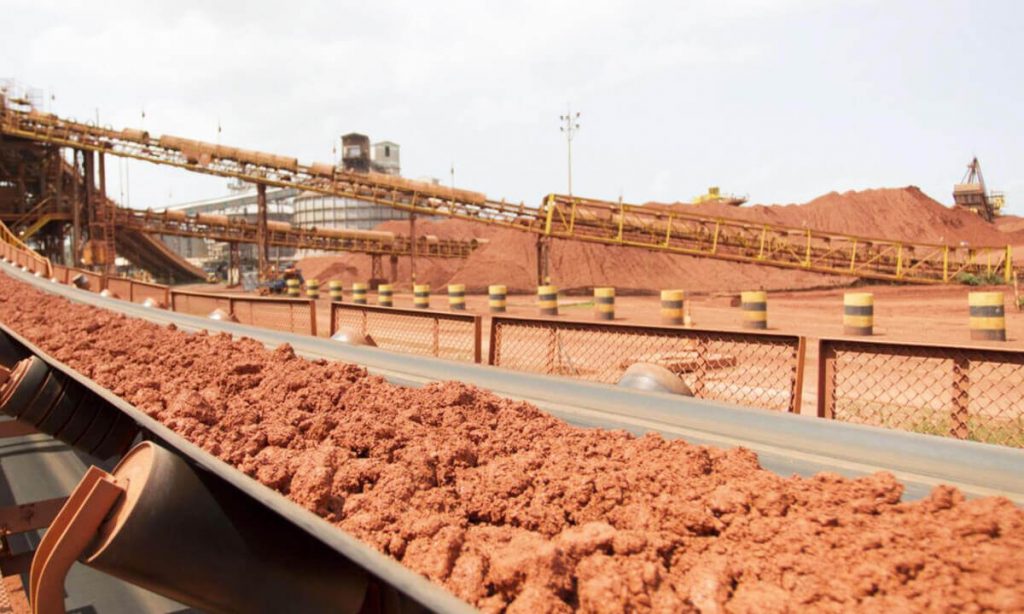
Limonite Beneficiation Methods
1. Limonite gravity separation
Limonite gravity separation has become a revolutionary technology for extracting valuable minerals from complex deposits in mineral processing. It mainly uses the density difference between various ore components to separate them by gravity. The limonite gravity separation method involves several steps that play a critical role in maximizing efficiency and yield.
- The ore is broken into smaller particles to facilitate the subsequent separation process. The crushed ore is screened to remove any large particles or impurities.
- Classify according to particle size through jigs, shakers or spiral chutes. These devices use gravity and centrifugal force to separate the heavier iron-rich particles from the lighter gangue material.
- Dehydration and drying of concentrated products can be used in various applications, such as steel production or pigment manufacturing.
The gravity separation method is mainly suitable for processing limonite ore with coarse particle size. The process is simple, the cost is low, and it is mainly used in small mineral processing plant. But there are also the disadvantages of small processing capacity and low recovery rate
2. Limonite Magnetic Separation
Limonite is a common iron ore known for its complex composition and low iron content. A magnetic separation is usually used to extract valuable iron from limonite efficiently. Commonly used equipment is high gradient strong magnetic separator. The method uses a magnet to separate magnetic and non-magnetic particles, isolating pure iron.
1. The first step involves crushing and grinding the raw ore to separate it from the gangue minerals.
2. A wet high-strength magnetic separator separates magnetic and non-magnetic particles. It generates a high-strength magnetic field that attracts and traps paramagnetic particles while allowing non-magnetic minerals to pass through unaffected.
3. The limonite pulp after magnetic separation contains a certain amount of water and needs to be dehydrated to increase the solid content of the ore after magnetic separation.
4. The magnetic separation after dehydration treatment is further selected. The purpose is to improve the grade of the concentrate and reduce the iron content in the tailings.
5. Carry out further concentration treatment on the selected limonite to obtain higher-grade limonite concentrate.
Limonite strong magnetic separation method is a simple and economical mineral processing method. Simple and stable, it can improve the grade of products, an efficient and environmentally friendly method to obtain high-quality iron ore.
3. Limonite Flotation Separation
Limonite may also contain non-magnetic impurities such as silicates, which flotation can separate. The following are the basic steps of the limonite flotation process:
1. Crushing: The raw ore is broken into a suitable particle size through the crushing process, making it ideal for flotation treatment.
2. Grinding: The crushed ore is subjected to a grinding process to refine the particles and increase the contact area between the mineral and the flotation agent, thereby increasing the flotation efficiency.
3. Flotation agent addition: After grinding, the limonite slurry is mixed with a specific flotation agent. Flotation agent is a chemical agent that can make limonite particles absorb air bubbles and float. Commonly used flotation agents are pyruvic acid, petroleum sulfonic acid, sodium dioctanoate, etc.
4. Bubble generation: The flotation agent forms bubbles in the pulp by feeding in air or nitrogen. These air bubbles attach to the limonite particles, causing them to float.
5. Flotation: Due to the action of the flotation agent, limonite particles are attached and floated by air bubbles, forming flotation foam. Froth flotation concentrates the limonite mineral to separate it from other impurity minerals. The froth and flotation agent in the flotation product is removed from the bottom or top, and the limonite flotation froth and tailings are further separated.
6. Concentration: The limonite flotation foam is concentrated in multiple stages to improve the grade of limonite.
7. Concentrate dehydration: Dehydrate the concentrated limonite slurry by filtration or centrifugation to obtain concentrate.
The flotation method has a good effect on the recovery of fine-grained limonite. It is best to wash and deslim the limonite before flotation, otherwise, the ore mud will seriously affect the flotation effect. For limonite with single nature, the recovery rate of the flotation method is higher, but the cost is also higher.
Combined Beneficiation process of limonite
(1) Gravity separation – strong magnetic separation: Coarse-grained limonite is separated by gravity separation. Different types of magnetic separators are used for magnetic separation of intermediate and fine grades according to the nature of the ore. Re-selection ore and tailings can also be re-grinded and re-selected to increase the recovery rate.
(2) Selective flocculation flotation method: When the limonite is ground to a certain fineness, sodium carbonate and water glass are added to make the slurry well dispersed. The limonite is selectively flocculated to obtain the concentrate. The flotation method can be used on this basis to improve the grade of the concentrate further.
(3) Flocculation-strong magnetic method: suitable for separating low-grade and fine-grained limonite. The particle size of fine-grained iron minerals increases due to flocculation and can be separated by magnetic force in strong magnetic selection.
The composition of limonite itself changes greatly, and the particle size is uneven. In the actual beneficiation production of limonite, it is best to use the beneficiation test to determine the best beneficiation process. The limonite combined beneficiation method is a multi-stage and multi-process process. Through step-by-step processing, the valuable minerals in limonite are extracted, and the content of ore-containing impurities is reduced simultaneously to obtain high-grade limonite products. Specific process and equipment choices may vary depending on the specific composition and characteristics of the ore.
Limonite ore is effectively separated from impurities by combining gravity separation, magnetic separation and flotation techniques, resulting in a high-quality final product. The application of these beneficiation methods reduces the impact on the environment by minimizing waste and pollution. Therefore, industries facing limonite beneficiation challenges are strongly advised to consider implementing JXSC‘s state-of-the-art equipment and beneficiation methods to overcome these difficulties and achieve the best results. The quality and purity of the limonite concentrate are improved, and the overall production efficiency is significantly improved.