In recent years, monometallic and polymetallic magnetite beneficiation has attracted extensive attention due to its high economic value and wide range of applications. Magnetite is a naturally occurring iron oxide mineral known for its magnetic properties. It is commonly used as a key raw material in various industries, including steelmaking, ceramic production and electronics manufacturing. Magnetite in its pure form contains a high proportion of iron (Fe), making it an attractive option for iron ore extraction. Single magnetite beneficiation focuses on separating magnetite from other minerals present in the ore through processes such as crushing, grinding, magnetic separation and flotation. This method concentrates the valuable iron content while minimizing impurities. Polymetallic magnetite beneficiation has attracted much attention as an alternative source of rare earth elements, iron and other precious metals; the heart of beneficiation involves multiple complex processes aimed at separating and concentrating valuable metals.
Single magnetite beneficiation
Refers to pure magnetite without any impurities or additional minerals. Also known as lodestone or magnetic iron ore, is a naturally occurring iron oxide mineral. It has unique magnetic properties and has been widely used in various industries such as manufacturing, construction, and environmental restoration. The composition of the ore is simple, and the weak magnetic separation process is often used:
- When the grinding particle size is more than 0.2mm, most iron ore magnetic separation plants often adopt the primary grinding-magnetic separation process;
- When the grinding particle size is less than 0.2mm, a two-stage grinding-magnetic separation process is adopted;
- For arid and water-scarce areas, magnetite concentrators may consider adopting dry grinding-dry magnetic separation process;
- For poor-rich magnetite or rich magnetite, dry magnetic separator can generally remove gangue. Obtain massive rich ore, then obtain concentrated ore through grinding-magnetic separation.
Flow:
The raw ore is first crushed into small particles. These particles are then fed into a ball mill for grinding. The ground ore is then subjected to various stages of magnetic separation to separate magnetic minerals from non-magnetic minerals. This involves passing finely ground ore through magnets to attract and remove magnetite particles. The separated magnetite concentrate is further processed through flotation and dehydration to obtain iron-rich products with low impurity content.
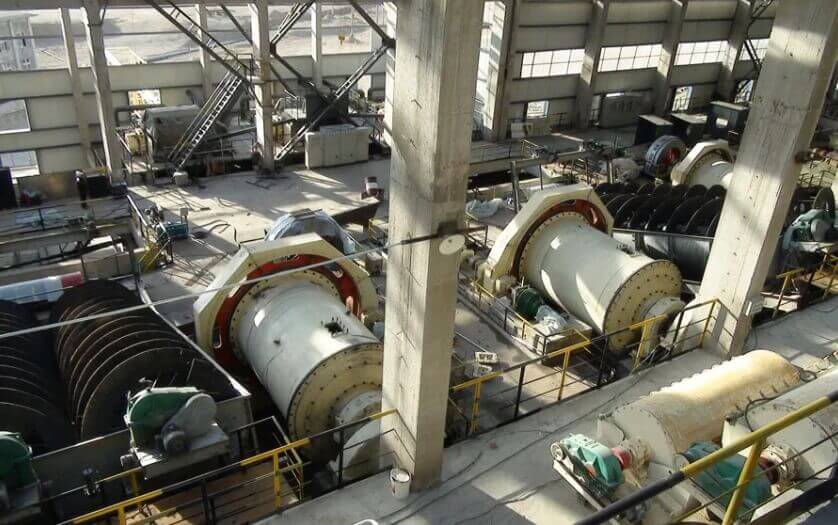
Polymetallic magnetite beneficiation
Besides iron, multi-metal magnetite also contains nickel, cobalt, copper, vanadium and other metal elements. The presence of these additional metals gives polymetallic magnetites unique properties and makes them highly sought after for specific applications. For example, the high vanadium content in some polymetallic magnetites makes them a valuable resource for producing vanadium-steel alloys with excellent strength and hardness. Generally, the combined process of weak magnetic separation and flotation is adopted; iron ore is recovered by weak magnetic separation, and sulfide or apatite is recovered by flotation.
- For the weak magnetic separation-flotation process, the continuum mainly enters the iron concentrate;
- For the flotation-weak magnetic separation process, the continuum mainly enters the sulfide concentrate.
The magnetite concentrate can be subjected to flotation or impact fine screening to obtain high-grade concentrate.
Flow:
The first step in the beneficiation process involves crushing and grinding the raw ore to reduce its size for further processing. Next comes magnetic separation, which uses magnetism to separate magnetite from other minerals. The extracted magnetite is further ground to achieve the optimum particle size to ensure higher efficiency of subsequent processes. The magnetite concentrate can be subjected to flotation or impact fine screening to obtain high-grade concentrate. Adding reagents helps enhance this stage’s selectivity and improve mineral grades. To improve the recovery rate, tailings reprocessing and other processes can be considered for further recovery.
magnetite processing plant
1. Crushing and screening: a vibrating feeder is installed in front of the crusher, and the raw ore is evenly fed into the jaw crusher. Then the raw ore that meets the particle size is screened out by a vibrating screen for crushing.
- For high-grade magnetite, a closed-circuit method is usually used to obtain magnetite with qualified particle size;
- For low-grade magnetite, three-stage open-circuit or three-stage closed-circuit operation is used to complete ore crushing.
2. Grinding and classifying: the ore has high hardness and extremely fine size. The closed-circuit ring grinding process combines ball mill and spiral classifier to achieve the required grinding fineness.
3. Magnetic separation: permanent magnet drum-type magnetic separator is generally used for separation.
Most magnetite concentrators often use coarse-grained dry magnetic separation tailings. The ultra-lean magnetite with a grade below 20.00%, the ultra-fine crushing-wet magnetic separation tailings process can be used before grinding. The ore is finely crushed to below 5mm-3mm, and then wet magnetic separation and tailings are carried out with a permanent magnetic field magnetic separator.
4. Tailings treatment: After obtaining the magnetite concentrate, the tailings must be concentrated and dehydrated. After passing through the dryer, the dried mineral products can be obtained.
The actual processing flow will vary according to the ore composition, product requirements, and the equipment and technical level of the factory. However, the process of polymetallic magnetite processing plants is usually a complex and comprehensive project. Before processing, you should conduct a beneficiation test to formulate a reasonable magnetite beneficiation solution. If necessary, you are welcome to contact online!