The mining ball mill is the most important equipment in mineral processing and is widely used. Mining ball mills can convert raw minerals into valuable commodities by impacting rocks and ores with steel balls. This powerful machine is responsible for grinding raw materials into fine powder. From excessive vibration to uneven grinding performance, our expert analysis will uncover the root causes behind these issues and provide effective solutions to have your mining ball mill running like a well-lubricated machine in no time. Next, let’s look at five common failures and their solutions.
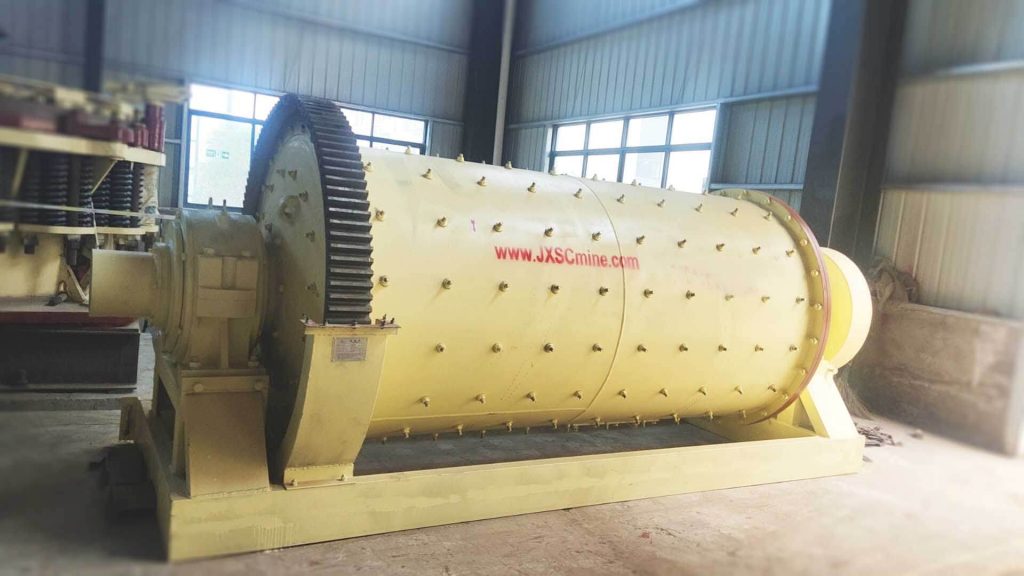
Fault 1: The mining ball mill makes loud noise
Reason: One of the reasons for loud operating noise may be unbalanced load distribution in the mill. Uneven distribution of material may cause uneven grinding media wear or excessive vibration, resulting in additional noise. Another possible cause could be worn or damaged bearings, which can cause excessive friction and increase noise levels during operation.
Solution: A thorough inspection of the grinding media distribution can help identify imbalances and make appropriate adjustments. In addition, regular lubrication of bearings cannot be ignored as it can minimize friction noise while reducing wear and tear on moving parts. Users can significantly reduce unnecessary noise in the work environment by carefully checking and ensuring that bearings are well lubricated and maintaining proper load distribution within the mill.
Fault 2: Mining ball mill reducer bearing heats up
Reason: One of the possible reasons for the ball mill reducer bearing heating is insufficient lubrication. Insufficient lubrication can cause bearings to operate at high temperatures, resulting in overheating.
Another cause could be excessive load or improper installation. When equipment is subjected to heavier loads than it can handle, it stresses the bearings, causing overheating. Likewise, if the bearings are installed incorrectly or misaligned between the shafts, this can lead to increased friction and heat generation.
Solution: To solve this problem, regularly checking and replenishing the lubricating oil in the reducer is necessary. A high-quality and suitable lubricant can also help reduce friction and heat generation. Proper load management and accurate installation procedures also need to be ensured.
Fault 3: Mining ball mill has an insufficient grinding capacity
Reason: This is a common problem mining ball mills face, resulting in low productivity and low ore processing efficiency. One reason may be the improper design of the grinding chamber, which affects the flow of materials and reduces grinding efficiency. Additionally, worn or damaged liners can hinder the grinding process by reducing the effective impact between the ball and the material.
Solution: Optimizing the design of the grinding chamber by increasing its length or diameter can improve flow patterns and increase grinding efficiency. Renewing worn linings with high-quality materials can restore normal functionality and optimize wear resistance. Additionally, implementing an advanced control system allows operators to adjust variables such as feed rate and ball loading in real time to maximize mill throughput.
Fault 4: High-frequency vibration occurs in the mining ball mill
Reasons: On the one hand, the cause may be excessive wear or imbalance of rotating parts. On the other hand, some external factors, such as improper foundation design or inadequate maintenance practices, can also cause vibration problems.
Solutions: This may involve regular inspection and maintenance procedures to ensure proper lubrication and alignment of all components. Additionally, implementing dynamic balancing technology can help significantly reduce vibration levels. Another promising solution is using advanced monitoring systems that provide real-time data on plant performance. Operators can quickly detect abnormal behavior and take timely corrective measures by tracking essential parameters such as power consumption or bearing temperature.
Fault 5: Mining ball mill motor bearing temperature rises
If not handled properly, heat buildup within a mining ball mill can result in shortened equipment life and possible failure.
Reasons: One of the culprits is insufficient lubrication, which can lead to increased friction and heating. It may occur if the lubricant used in the bearing is unsuitable for the operating conditions or if there are problems with lubricant flow. Another cause could be an improper or misaligned ball mill generator shaft. Misalignment can put excessive stress on the bearing, causing it to overheat. Overheating can occur due to insufficient cooling mechanisms, excessive friction caused by dry running conditions, or inadequate lubrication.
Solutions: To avoid excessive heat generation, it is vital to have an effective cooling system and always ensure proper lubrication. Periodic inspections should be performed to monitor lubricant flow and ensure no blockages or leaks could prevent appropriate function.
The mining ball mill is the key equipment in the ore grinding stage of the mineral processing plant. Regular maintenance and inspection of your mill, along with proper lubrication and alignment, can go a long way toward preventing failures such as excessive wear, leaks, and vibration. By implementing these solutions, mining operations can ensure that their ball mills run smoothly and efficiently, ultimately increasing productivity and reducing downtime. JXSC will choose the best grinding equipment according to your mineral situation!