Fluorspar, also known as fluorite, is a valuable mineral used in a variety of industries including metallurgy, chemical manufacturing, glass production, and more. The mining and processing of fluorspar involves several steps to extract the mineral from the earth and purify it for commercial use. One of the main challenges in fluorspar beneficiation is obtaining a high-quality concentrate with high purity.
The main methods of fluorspar beneficiation include crushing, grinding, flotation and gravity separation. Each step in the process plays a vital role in separating fluorspar from impurities such as quartz, calcite and barite. Next, we mainly introduce four common types of fluorspar mineral processing methods, including quartz-type fluorspar ore, calcite-fluorspar type ore, sulfide fluorspar type, and barite fluorspar type.
Fluorspar mineral processing methods
Fluorspar mineral processing is a complex field that requires a variety of methods to extract and refine this valuable mineral.
- One common type is gravity separation, which involves separating fluorspar from other minerals based on differences in density. This method is cost-effective and environmentally friendly, making it a popular choice in fluorspar processing.
- Another common method is flotation, which uses chemicals to separate fluorspar from gangue minerals. This process is very effective for recovering high-grade fluorspar concentrate for further refining.
- Magnetic separation is also used in fluorspar processing to remove magnetic impurities from the ore, resulting in a purer end product suitable for industrial use.
Finally, flotation is a widely used technique that exploits the hydrophobicity of fluorspar to separate it from gangue minerals. This method enables the efficient recovery of high-grade fluorspar concentrate by creating air bubbles that selectively attach to fluorspar particles.
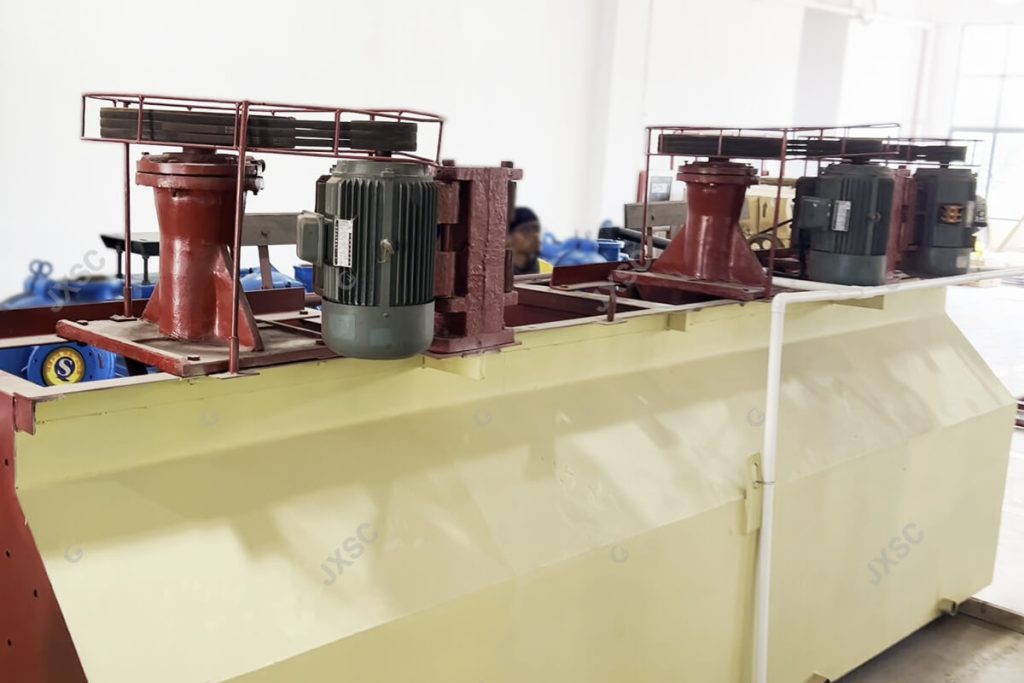
Four common types of fluorspar mineral processing
Quartz-fluorspar mineral processing
Reducing the silicon in the concentrate is the focus of this type of ore separation. Depending on the use requirements, the requirements for silicon content are also different. Since most quartz-type fluorspar ores contain conjoined bodies of quartz and fluorspar, too fine grinding particles will cause over-crushing of fluorspar and affect the recovery rate. Therefore, a staged grinding process is generally adopted, which not only reduces the silicon content of the concentrate product after fluorspar flotation, but also increases the recovery rate of the fluorspar concentrate.
The process begins by crushing and grinding the ore into a fine powder, which is then mixed with water and collector chemicals. The mixture is then aerated, causing the quartz particles to float to the surface and the fluorspar to sink, allowing for easy separation. Another is the need for selective flotation agents specific to each mineral. By controlling pH and selecting the right combination of chemicals, operators can obtain high-purity concentrates of quartz and fluorspar.
Calcite-fluorspar mineral processing
When processing calcite-fluorspar minerals, a widely used method is grinding-flotation. This process helps crushed down the ore into smaller particles, making it easier to separate valuable minerals from the waste. Flotation involves using water and various chemicals to create a froth that brings the desired minerals to the surface for collection, thereby separating the minerals from the ore. This method can efficiently and effectively separate calcite and fluorspar from other impurities in the ore.
Gravity separation can also be used as a method for processing calcite-fluorspar minerals. Gravity separation relies on density differences between different minerals to separate them from each other. The technology is particularly useful when dealing with high-density materials such as fluorspar, allowing efficient separation without relying on chemical reagents.
Sulfide fluorspar mineral processing
Flotation is the most effective method when processing sulfide fluorspar minerals. The flotation process involves using chemicals to separate valuable minerals from waste materials, taking advantage of differences in their surface properties. By creating a foam that attaches to the desired mineral particles, they can be selectively recycled while leaving behind impurities. In addition, gravity separation can be used as a complementary method to further refine the concentration of fluorspar sulfide.
A key consideration in sulfide fluorspar processing is the varying composition and complexity of different deposits. Advanced techniques such as magnetic separation can also be used in specific situations where additional purification is required.
Barite-fluorspar mineral processing methods
The main minerals of barite-type fluorspar ore are barite and fluorspar. The barite content is generally 10%-40%, often accompanied by sulfide minerals such as pyrite, galena, and sphalerite.
A common method is gravity separation, where the density difference between barite and fluorspar allows them to be easily separated using a shaker or centrifugal concentrator. Another method involves froth flotation, a widely used technique that selectively separates minerals based on their hydrophobicity by adding collectors and frothers to create a froth that attracts one mineral while repelling another mineral. This process is very effective for obtaining high-purity barite and fluorspar concentrates simultaneously.
In addition, magnetic separation can effectively remove magnetic impurities in barite, fluorspar ore, further improving the overall efficiency of the mineral processing operation.
The above four types of fluorspar mineral processing involve various methods to extract this valuable mineral from the ore, mainly including gravity separation, flotation, and magnetic separation. Each method has unique advantages and challenges in the extraction of fluorspar. JXSC will use a combination of these methods based on the characteristics of each deposit to ensure the successful extraction and beneficiation of fluorspar minerals.