Barite is a non-metallic mineral product with barium sulfate as the main component. It is the most common mineral of barium. It is produced in low-temperature hydrothermal veins and often coexists with galena, sphalerite, chalcopyrite, etc. It has the advantages of high density, being insoluble in water, being non-toxic, being easy to absorb radiation, and having good filling properties. It is widely used in petrochemicals, building materials, metallurgy, textiles, electronics, building materials, medicine, and other industries.
The proportion of barite commercial-grade rich ores with grades higher than 90% has declined. Salts and carbonate minerals coexist and must be beneficiated before use. Under normal circumstances, the grade or specific gravity of native barite ores cannot meet industrial production requirements due to the presence of impurities such as other gangues. Therefore, the specific gravity or grade must be increased through a barite beneficiation line to meet industrial requirements before selling. Impurities and undesirable components can be removed from barite ore through crushing, washing, gravity, magnetic, and flotation separation processes, thereby obtaining higher purity.
Barite ore beneficiation Process
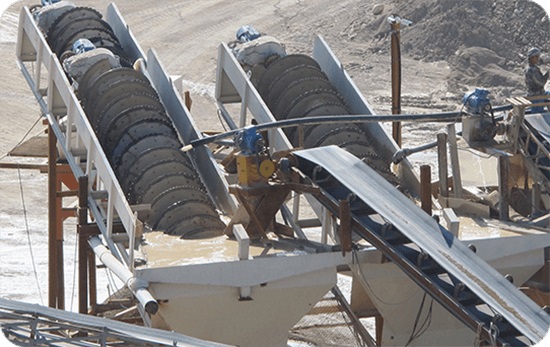
Barite ore crushing and washing
In the crushing and washing process of barite ore, efficiency is key. If the barite ore contains a large amount of mud, the ore washing machine needs to be added. Commonly used log washers and spiral sand washers use high-pressure water jets to remove the mud and clay attached to the barite ore, making it easier to separate and purify. The washing process ensures that only high quality barite is obtained for further processing.
The initial stage usually uses a jaw crusher or impact crusher to break large pieces of raw ore into smaller pieces so that they can be processed more easily in subsequent steps. The ore is crushed to remove impurities and ensure high quality of the final product.
Barite ore gravity separation process
The process involves exploiting the density differences between barite and gangue minerals to separate them using gravity-based techniques. By adjusting parameters such as particle size, water flow and tilt angle, miners can optimize the efficiency of the gravity separation process.
The raw ore is crushed and ground into a fine powder. Subsequently, the material is fed into a jig or shaking tables where the denser barite particles settle to the bottom and the lighter material is removed, forming a mineral ready for further processing. Purified concentrate. The separated material can also be further processed through a centrifugal concentrator to increase the concentration of barite. The gravity separation process does not involve harmful chemicals or pollutants commonly used in other mineral separation processes, and is relatively environmentally friendly.
Barite magnetic separation process
When barite coexists with magnetic minerals such as siderite, magnetite, and hematite, magnetic separation is an effective separation method that can obtain high-grade concentrate products that can be used as raw materials for the production of barium-based pharmaceuticals.
For ferromagnetic minerals with finer particle sizes in barite, dry magnetic separators or wet high gradient magnetic separators are usually used. Attract and separate barite particles based on their magnetic properties. An important aspect of the barite ore magnetic separator is the optimization of operating parameters such as magnetic intensity, feed rate and particle size distribution. By carefully controlling these factors, operators can increase the efficiency of the separation process and improve the quality of the final product.
Barite Flotation Separation Process
If barite ore contains a high barium sulfate (BaSO4) content, it is associated with gangue minerals such as quartz, calcite and fluorite. Flotation machine is often required to separate the valuable barite from other minerals present in the ore. The flotation process involves adding reagents to create froth that selectively attaches to barite particles, thereby separating them from the gangue minerals. Crushed and ground barite ore is mixed with water and various reagents to form a slurry. The slurry is then aerated, causing air bubbles to attach to the barite particles and cause them to float to the surface. Next, the foam containing floating barite particles is skimmed off and collected. The collected material is further processed to remove impurities and improve the grade of the final product. Under conventional flotation conditions, the recovery rate of barite can reach more than 80%, and the collector used also has good foaming properties. Flotation is also particularly effective for processing low-grade or complex barite ores.
By extracting and processing valuable minerals from low-grade ores through beneficiation technology, we can reduce waste generation and enhance the sustainability of mining operations. Based on the density, floatability, specific magnetic susceptibility and other physical and chemical properties of quartz, fluorite, magnetite, lead-zinc ore, pyrite, hematite, goethite, calcite and other minerals associated with barite Depending on the difference, you can choose reasonable barite beneficiation processes such as gravity separation, magnetic separation, and flotation, which can effectively separate one or more concentrated mineral products. Contact us online to find out more!